Is it rock, or is it concrete?
Rock-themed landscapes are showing up more and more in commercial and residential settings — and many of them look like the real thing.
But as most decorative concrete contractors know, many of the rocks that are seen in museums, theme parks, resorts, shopping malls, golf courses and even people’s backyards are fake — or faux, as they’re often called. They’re made of concrete, and for good reasons: cost, weight, versatility and concerns about the environment are some that come to mind.
Of the many techniques used to create faux rocks from concrete, shotcrete is one of the best.
For big jobs, shotcrete solves a lot of potential problems, observes David Long, president of Lakeland Co. Inc., a firm with a wide variety of large-scale projects to its credit. “Shotcrete is the best option for work that requires a transition of different finishes into one application,” he says, “or for areas where there is not access for equipment to hang rock panels or other prefabricated theme structures.”
Long also notes shotcrete is good for areas that need to be stabilized before the finish work can be done, and when a budget doesn’t have room for replica panels. And applying shotcrete allows you to cover a large surface area in a short amount of time.
Shotcrete is good for smaller projects, too. Michael Dahl, president of Michael Dahl Concrete Designs Inc., almost always uses shotcrete. “It goes on a lot faster and you get a stronger concrete because of minimal air pockets,” he says.
Because of its quality and strength, Dahl especially likes using shotcrete on vertical surfaces. “Because of the lower water/cement ratio, it’s really strong for retaining walls,” he says.
Coming to terms with shotcrete
Shotcrete is pneumatically applied concrete or mortar. The term “shotcrete” was originally used as a substitute for the proprietary word “Gunite,” and can refer to both the wet-mix and dry-mix process. For our discussion, shotcrete will mean the wet-mix process. Gunite refers only to the dry-mix process.
With shotcrete, the wet concrete mix is pumped through a hose to a nozzle, at which point high-pressure air is introduced to shoot the concrete onto the receiving surface.
With Gunite, high-pressure air is used to blow a dry cement mix through a hose to the nozzle, where water is injected into the mix immediately prior to application.
Each process has pros and cons.
One of the major advantages of wet-process shotcrete is that you do not have to hand-mix the material on site. This aspect of the job can be outsourced and the material brought to the site in ready-mix trucks. However, if you go this route, you have a certain window within which you must apply the shotcrete. Depending on the size of your crew, this may also limit the amount of time available for carving and detailing your faux rocks.
If you use Gunite, careful application is critical to ensure that the dry cement mix and the water combine successfully on the receiving surface. As a safety factor, it is important to remember the psi of the compressed air required for Gunite is much greater than that required by shotcrete. This also results in greater overspray and rebound. On the other hand, because Gunite is a dry mix, you can apply it in sections, set the equipment aside and take more time to carve the rockwork.
Pumping concerns
Depending on the scale of the project, you may have varied needs with regard to pumping equipment. Pumps come in portable, tow-behind sizes as well as large-scale behemoths.
If you need to pump shotcrete great distances, hydraulic swing tube piston pumps might fit your bill. “These pumps can be engineered so that they are capable of pumping wet shotcrete mixes extreme distances due to the amount of piston face pressure (up to 2,200 psi),” explains Tripp Farrell, sales manager of Blastcrete Equipment Co. Volume in these pumps can range from 3 cubic yards per hour up to 50 cubic yards per hour, he adds. An important characteristic of hydraulic swing tube pumps is that they will reverse, he says, “which is extremely important when pumping low-slump mixes.”
Ball seat pumps are another option and can be used quite successfully. But because these machines are not designed to reverse, they can be dangerous if a plug occurs. If there is a plug, the discharge line or a valve on the machine must be opened to release the line pressure.
Peristaltic pumps — also called hydraulic squeeze pumps — use rollers against flexible tubing to create pressurized flow through the pumping tube. Farrell notes these kinds of pumps have forward and reverse capabilities, and they are easy to maintain.
“Most contractors prefer to have a mixer/pump combination unit,” Farrell observes. This gives contractors the option to mix, pump and spray material for smaller jobs, and for large jobs to bypass the mixer, instead having the ready mix delivery of shotcrete dispensed directly into the receiving hopper.
Equipment prices vary and some equipment can be very costly. Equipment may also be rented, but may not be cost effective if you do a lot of this type of work.
Stan Pace, president of FossilCrete Inc., advises that contractors buy equipment appropriately sized for the scale of their usual projects. But he cautions also to keep in mind the size of the air compressor support you’ll need to accommodate the pump, and the design of the mix you’ll expect the pump to handle.
But even if you do mostly large-scale work, Pace says having a smaller pump in your equipment line up may be a good idea because it will allow you to work with a smaller amount of mix, which can be used for detailing and texturing after the structure coat is applied.
Doctoring the mix
The shotcrete mix used in any given application will vary pending the requirements of the project application, and then some.
“Knowing which aggregates are provided from the concrete company would determine the mix ratio for the shotcrete being applied,” Long explains. “For example, some concrete providers have round 3/8-inch aggregate and others might carry crushed 3/8-inch shale, depending on the part of the country where your project is located.”
Other factors include whether your location is flat, vertical, sloped or inverted; the distance from the pump to job location; the weather at the time of application; and the concrete truck time spacing. The slump of the concrete needed to accomplish the required project application will be determined by the location and the design, Long adds.
Contractors use a variety of admixtures in shotcrete to make it work better. Different products help with flowability, plasticity and workability. But sometimes designing the mix is a calculation aimed at a fine line between a mix that is too dry or too soupy. Some contractors have turned to using a mix water conditioner.
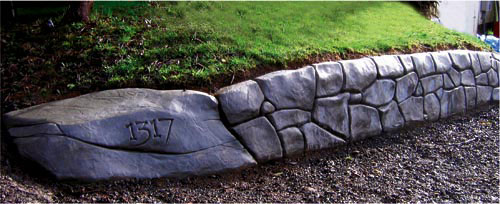
David Johnson, president of Applied Concrete Technology Inc., explains that a mix water conditioner is not an admixture. “The water is conditioned before it hits the portland cement,” he says. The product conditions the water to make it more efficient, causing it to bind with more particles. Some people liken the process to making the water wetter, but Johnson describes it as getting tighter into the concrete. This process is reported to also make the concrete stronger, more durable and less permeable.
The use of fiber reinforcement in shotcrete for faux rocks appears to be a personal choice. Some feel it adds strength. Others don’t. Some say the fibers can look like fuzz on the surface if they are disturbed during the detailing stage. Other contractors don’t seem to have this problem.
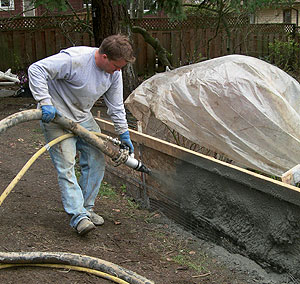
Making faux rocks
The method of creating faux rocks with shotcrete boils down to three steps, says Pace: frame, structure and texture.
The general shape and strength of the frame depends on the requirements of the finished rock structure. Sometimes the rock is designed for visual aesthetics only; other times the rock may be functional, such as forming stairs or a sitting ledge or functioning as a retaining wall. Typically, the shotcrete is applied to an appropriate framework of reinforcing bars covered by metal lathe.
The structure itself is created by applying the shotcrete to an adequate depth, and just about everyone will tell you the most important guy on the crew is the nozzle man.
“The hardest thing is placing the concrete,” Dahl says. “If you place it correctly the first time you don’t have a lot of extra work.” Having a nozzle man who has honed the techniques needed to do it right the first time is extremely valuable — especially when you are applying shotcrete on vertical surfaces.
The detailing and texturing may be part of step two or a separate step, depending on whether you apply a texture coat or directly carve a single application of shotcrete.
Pace recommends a separate texture coat. “You know your structure coat is strong enough, so when you apply a texture coat you are totally free to carve or stamp what you need in the texture coat.” So, for example, you could carve a crevice as deeply as you want in the texture coat without compromising the structure.
Texturing the original application of shotcrete is also an option, but you have to work quickly while being careful not to compromise the structure. You can’t begin carving and detailing too soon or the shotcrete will fall off, but the shotcrete can’t be too far along in setting up or you won’t be able to get the detail.
As Long explains, the texturing and detailing is where you need to be an artist. Carving and applying brush or stamped textures are all learned skills that take practice. Dahl uses trowels to sculpt the shotcrete and then uses custom-made texture mats.
Then there is the coloring. “We use a combination of acid stains and other techniques, such as acrylic washes and oxide washes, to achieve the effect we want,” Long says. Dahl likes to use acid stains. “They are earth-tone colors that suit natural-looking rocks. I’ll tint my sealer, too, to adjust or achieve a more true, pinpointed color,” he says.
Often, the viewing distance will impact the amount of detail required — as will the budget. If the faux rock is a backdrop to be viewed at a distance, the amount of detail doesn’t have to be so precise. The look desired may be accomplished by shape and general color, whereas if the faux rock will be close enough to touch, the texture and coloring must be as realistic as possible. That’s why really detailed work can cost $100 per square foot to $200 per square foot or more.
As for sealers, some prefer solvent-based sealers because they are more cost effective and others like water-based sealers because they are more environmentally friendly. Long recommends using a penetrating sealer for its protective qualities.
Reapplication of a sealer is not usually an issue. Long says most of his clients appreciate the weathered look that time and the elements produce.
Looking better with age
“Faux rocks allow you to accomplish what you couldn’t ever do with real stone,” Pace points out.
Dahl agrees. “The thing about making custom rocks is you can create the rock you need. You can problem-solve where a real rock is not practical or available,” he says.
But be careful not to oversell, cautions Long. And be sure to let the client know that the project will mature and look better with age. A recreation of a natural scenario never looks its best immediately when finished. But look at one a few years later, when the landscaping plants mature and fill in, and it looks like the real thing.
“The whole goal,” Long says, “is to help your client envision what you’re creating for their environment.”