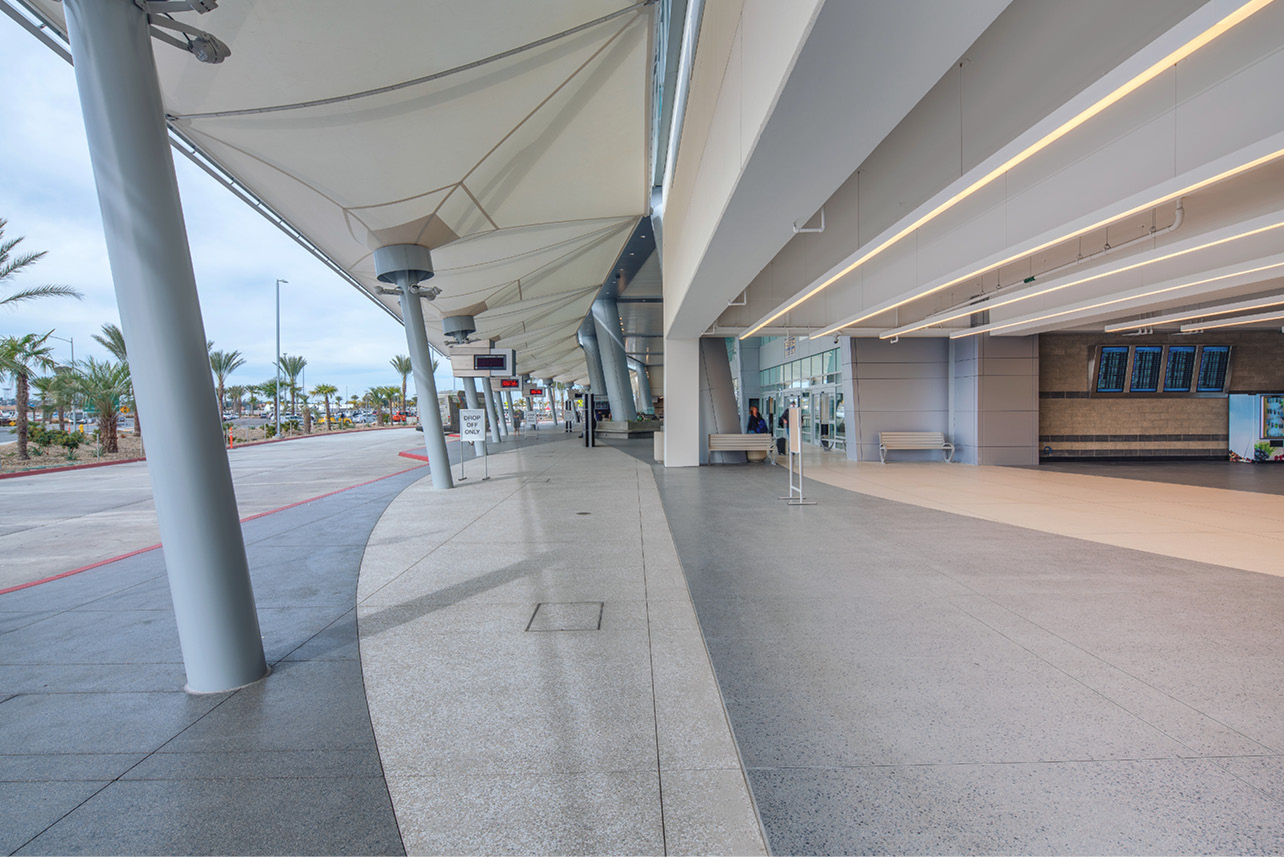
When weary travelers pull or carry their bags across the plaza and into one of the lobbies of the Consolidated Rental Car Center at Lindbergh Field at the airport in San Diego, they probably won’t give much thought to the decorative concrete and terrazzo beneath their feet.
However, those who worked on the project know it has something very much in common with many just-in-time travelers. The team at the locally based T.B. Penick & Sons Inc. worked right up to the center’s Jan. 20 opening when the owners made the decision to abandon the surface they had specified for those areas.
In the end, the surface was a mix of honed concrete and epoxy terrazzo. The two so closely resemble each other that most people have difficulty seeing the transition.
Back tracking to terrazzo
The Consolidated Rental Car Center is the culmination of more than a decade of work. Mark Pittman, registered architect in charge of construction with the San Francisco office of Demattei Wong Architecture, says when his company began working on the north side of the airport, it had not been master-planned.
“Tony Demattei was very instrumental in getting the north side projects squared away so this could proceed,” Pittman says. “That’s really the gist of it.”
The center moves all of the airport’s rental car companies to one location northeast of the airport near the Pacific Highway. The $316 million project provides space for up to 19 companies (although it opened with 14 brands), four levels of rental car parking and two customer lobbies. Access is via 16 25-passenger buses that travel between the facility and the airport’s terminals.
Penick had already come in for its share of work on the project. Among other things, the company had supplied 70,000 square feet of site concrete, 1,300 linear feet of curbs and gutters, and large poured-in-place concrete bench planters.
However, when a last-minute issue arose over the finishing of approximately 54,000 square feet of mostly interior flooring and another 20,000 square feet of an exterior plaza, its experience convinced developers Penick had the people and the expertise needed to keep things on time and on budget.
Ironically, Pittman says, the project originally called for terrazzo in the beginning.
“It was value-engineered out so we could save money by replacing it with a fluid-applied flooring,” he says. “But, when airport management saw how the fluid-applied flooring stood up to traffic and dirt and dust, they back-tracked to the terrazzo because it’s so much better.”
Pittman explains that several mockups had been done to get the color of the fluid-applied flooring just right. When the final colors were determined, a 20-by-10-foot mockup was done that initially looked quite nice. After a couple days, though, the maintenance company weighed in on what kind of care it was going to require.
“Basically, they realized they couldn’t polish it because they’d go right through it,” says Pittman.
From there, both terrazzo and Penick were easy choices.
A short timeframe
“T.B. Penick had experience on the Terminal 2 expansion that had taken place at the airport the previous year, including the terrazzo,” Pittman says. “We knew we had somebody we could work with. The airport liked working with Penick and they suggested we contact them.”
While there was no question about the durability of terrazzo, the same efforts at color-matching that had gone into the fluid-applied flooring needed to be repeated — but “we had only 90 days to get it down and in,” says Pittman.
It was, says Chris Klemaske, the project developer for Penick, a short timeframe. Often her job starts at the very earliest stages of a project.
“I work with a lot of architects and owners and artists on the front-end of projects — often one to two years in advance,” she says. “We help them take a look at their drawings and figure out what finishes are going to function the best in the areas they’re putting them and help them budget and really help them figure out how best to use concrete or terrazzo on their projects.”
Klemaske had been the project developer for Penick with Terminal 2, which was fortunate because it was definitely “hair on fire” time for all of them, especially during the first 45 days or so when solutions were being developed and colors chosen.
“Initially, we talked about what could be done and what couldn’t be done,” she says. “We had concrete that had already been poured, so we had tolerance questions. Their first question was if we could do concrete with some sort of topping for the plaza that would really complement it.”
The answer: a surface-seeded, indelibly colored concrete that was then honed. And, to provide continuity with the interior terrazzo, the exterior concrete incorporates the same aggregates. However, getting the right mixes took some doing.
Team work was paramount
“We hit a home run at the very beginning when we came up with that solution,” says Klemaske. “Then, it was just fine-tuning colors. We were working with the architects, and it was fine-tuning the grays and the blacks and what kind of sealer we were going to use and the aggregate mixture.”
Pittman agrees that part of the reason for the success of the two closely matched surfaces is that they incorporate fairly muted colors. However, he says, the Penick crew did an excellent job of turning around mockups during a 45-day period.
“We had a new mockup coming every five days or so,” the architect says. “The minute those mockups hit our trailer we were on them.”
“Everybody pulled together,” says Klemaske. “We’d do these mockups and take them down to the airport on the backs of trucks, and everybody would look at them. From there, we went to even larger mockups. At the end of the day everybody loved them.”
Once everyone agreed on the look of the concrete and terrazzo, the job was fairly straightforward — except for a tight timeframe and the decision to take some of the terrazzo outside.
“It’s technically exterior, but it’s under the overhang,” says Andrew Weber, senior project manager for Penick. “You do have the fluctuation of temperature.”
“Terrazzo is typically an interior material, but we had designed this plaza area to be completely under cover and protected by a canopy,” says Pittman. “We ended up making the area directly under the footprint of the building terrazzo and all the areas outside that to the bus canopy are architectural concrete.”
All’s well that ends well
As for the timeframe, the architect cites challenges such as determining where to put the terrazzo’s zinc strips, grinding already poured areas to accommodate the depth of the terrazzo, and building a stationary coffee “cart” in the plaza while work was underway.
“There was a Penick crew at work in one corner of the building trying to get a problem solved during the opening ceremony,” says Pittman. Buff-washing and sealing up until the very end, they managed to finish up just before the facility officially opened, Klemaske adds.
Routine maintenance of the two surfaces is straightforward, Pittman says, in part because Penick worked with the third-party maintenance contractor on everything from proper cleaning procedures to using the right equipment and additives on them.
He adds that the surfaces — particularly the terrazzo — are very good for roller bags, with the most serious problem being a few black scuff marks.
“I’ve made probably four different trips to the rental car center since the opening,” Pittman concludes. “And, it looks cleaner and better every single time I go there.”
Project at a Glance
Client: San Diego Airport Authority
Decorative concrete contractor: T.B. Penick & Sons Inc., San Diego | www.tbpenick.com
Scope of project: Install 20,000 square feet of decorative honed concrete and 54,000 square feet of terrazzo.
Most challenging aspect: Match colors and complete the job within an approximately 90-day timeframe leading up to the grand opening.