Being next door to the Artistry in Concrete competition at the World of Concrete 2015, Steven Ochs knew he had to bring his A game to the Smith Paint Products booth. Ochs, a decorative concrete artisan and chairman of the department of art and design for Southern Arkansas University, presented several designs to the Brunners, owners of the family-run business.
“They liked the idea of a family tree branching out in different directions,” Ochs says. “Plus they wanted me to do something standing up rather than being on my hands and knees all day.” The four main branches represent the four generations of the Brunner family involved with the business and the “Smith’s” logo carved into the massive trunk is the company’s original name.
He acknowledges there is a fifth hand in the sculpture that he added purely for aesthetics. “Odd numbers are better numbers to work with in an active composition,” he says. In hindsight, it also could signify a future generation of Brunners.
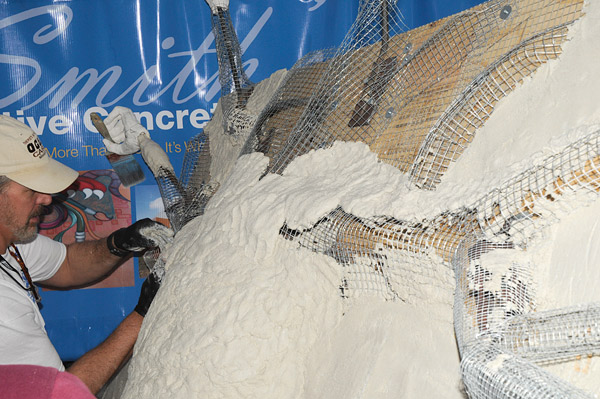
Give them a hand
To emphasize the company’s very hands-on approach to business and to draw attention to the fact that they make all their own products, Ochs outfitted the Smith’s family tree with subtly colored branches, five of which were equipped with their own porcelain hand made before the show. The hands, holding a paint brush or related tool, were made to look as if they were “creating and recreating” the piece of art at the show.
Ochs says even though he used the young and unwrinkled hands of his 16-year-old son as his model, he grossly exaggerated the scale, muscles and tendons. “I wanted to create strong, powerful hands. I thought about taking a mold from actual hands, but I didn’t want them to look realistic. I wanted them to look like chiseled wood.”
To make the exhibit ever more client-specific, Ochs modeled the tree after the eastern cottonwood, a species native to Harrisburg, Pennsylvania, where Smith Paint Products is headquartered. The backdrop depicts the Blue Ridge Mountains also in the vicinity. “I made the exhibit all about them — who they are, where they are and what they do.”
Addition versus subtraction
The technique Ochs used to build the tree involved an additive process rather than the “subtracting” method used by most carvers. “Most people do carving where they build up a product nice and thick and then carve it,” he says, but not him. To create the bark, he applied individual pieces of material, which resembled fat lengths of rope about 1 inch in diameter, with negative spaces between each.
“All I had to do was wet the surface, press on the coil and hold it for a few seconds and it bonded to the previous layer,” he says. When dry, he just shaved off the rounded tops so the flattish pieces better resembled cottonwood bark.
“There was very little mess and no wasted materials,” says Ochs. “I got a lot more random movement in twisting and turning (with this method) than what I would have gotten if I had carved the traditional way.” Plus, he adds, leaving the negative space between coils saved carving time.
4 In 1 formula
The tree bulges out about a foot to a foot and a half, which Ochs constructed on site with rebar and wire mesh. Once the armature was in place, he pressed “pancakes” made out of Smith’s 4 In 1 Overlay on top for his scratch coat. “Other people would have sprayed this on but I built it up to a 1/2 inch thick to give me a very strong structure. The 4 In 1 has a lot of polymer in it,” he says. “It’s really hard stuff — like 5,000 psi.”
It was the first time Ochs used the 4 In 1 product, a single-bag dry mix that only requires water to produce a permanent-bonding cement for interior and exterior installations. He troweled it on very thin and smooth for the mountain and sky background, made it thicker for the pancakes and stiffer yet for the bark. “The material can be used as a topical coating for vertical modeling and for stamping as well,” he says.
It’s such a versatile product, Ochs says, that he plans to introduce it to his sculpture class for a project involving making a sculpture over wire mesh. “It’s my way of introducing the young ones into the field of decorative concrete.”
Colorful touches
As for coloring the tree, Ochs thought about going natural but knew gray wouldn’t be the best color to represent a company that makes products in a wide array of colors. So, he first airbrushed five sections of the tree with dark red, blue, purple, green and blue again, with the colored sections starting at the bottom of the trunk. “As the colors come up the tree, each of the five hands becomes one of those colors,” he says.
Next, he used a 4-inch house paint brush to dry brush the top and outside edges of the bark gray and white. “But I left the colors deep inside the crevices so when you walked around the sculpture, the colors were revealed to you. You can’t see them all at the same time,” he says. The water-based concrete stains, he adds, are from Smith’s Color Floor Classic Series. Ironically, one of the only colors he didn’t use was Bark Brown.