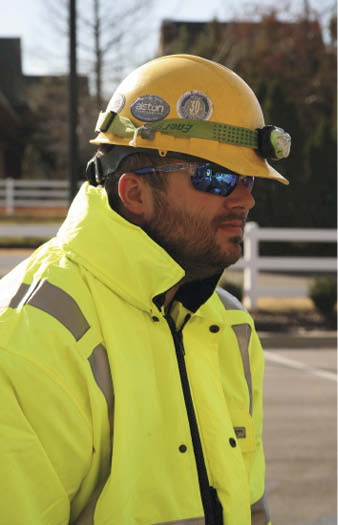
In recent months, most of the safety emphasis in the industry has been on crystalline silica and new regulations designed to keep it out of concrete workers’ lungs.
Both equipment manufacturers and contractors have worked hard to come up with new products and processes to keep their workers safe.
Unfortunately, dust generated by polishing and grinding is hardly the only danger concrete employees face on the job. Eyes and ears, hands and feet, heads and more are all at risk on the job site, and that will likely continue as long as people head off to work each morning.
However, just as with silica dust, there are ways to mitigate the problem. There are plenty of experts out there, available to companies large and small, who can help ensure people leave work in much the same condition as they arrived.
PPE provisions
Pres. Ronald Reagan generated plenty of laughs over the years with his contention that some of the most-frightening words ever spoken were, “We’re from the government and we’re here to help you.”
However, for many people their first line of defense with job site safety is the federal Occupational Safety and Health Administration (OSHA) or — in states that have chosen to write their own, stricter standards— a similar state agency.
In an industry that sees as many as 28,000 injuries a year, according to Chris Smith, director of marketing and inside sales for MCR Safety based in Collierville, Tennessee, personalized protective equipment (PPE) doesn’t just include lung protection. For concrete workers, it also largely includes eye and skin protection.
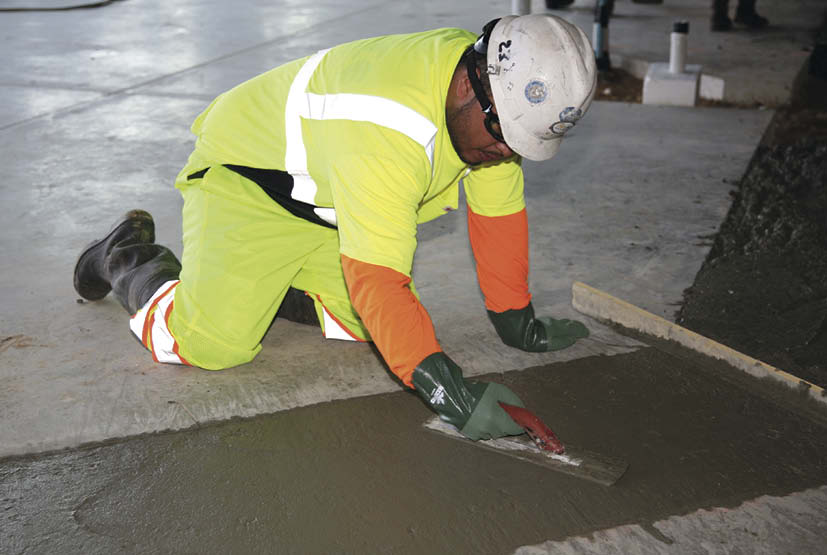
Finding out exactly what’s required isn’t always an easy matter. A simple search of “concrete” in the OSHA website turns up more than 200 different entries.
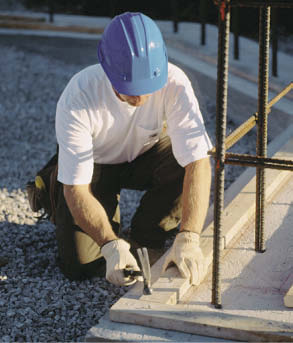
And all this must be done “at no cost to the employees with limited exceptions.”
For employees whose companies are working on large job sites, there are a couple of other advantages as well. Michael Katz, category director for safety at H.D. Supply Construction & Industrial/White Cap in Norcross, Georgia, notes that large contractors are going to have a safety officer on-site and regular safety training is the order of the day.
His co-worker, Erica Meloney, the senior safety manager, adds, “If you’re walking onto a large job site, there will possibly even be a picture of a worker showing everything the worker is required to wear, and descriptions in both English and Spanish.”
The right stuff
If you’re a sole proprietor or own or work for a small company, Katz’s list is probably a good place to start, but it’s certainly not complete.
One item that isn’t always easy to see and is sometimes forgotten in the mix is hearing protection, according to both John Paesano, category director for concrete, restoration and waterproofing at H.D. Supply, and Stacey Simmons, product manager for Bullard in Cynthiana, Kentucky.
Simmons explains that workers must be protected if they’re continuously exposed to noise greater than 85 decibels (85 dBA), or the sound of city street traffic. The reason: once hearing is damaged, that loss is not reversible.
“It’s certainly recommended when you’re preparing a concrete substrate, whether it’s a parking garage or a sidewalk,” says Paesano. “Whether you’re using a grinder or a shot-blast machine, those are noisy and while we sometimes take that for granted, ear protection is definitely needed.”
How does the average person know they’re getting the best product for a specific need — even if they’re shopping at a big box store? Not surprisingly, OSHA outlines standards for approved products for use on the job site.
Simmons, who chairs the ANSI/ISEA (American National Standards Institute/Industrial Safety Equipment Association) committee on head protection, explains that the federal agency adopts the standards, which are updated every five years or so.
“We’re competitors sitting around the table,” she says. “But, at the end of the day, we want workers to go home in better condition than when they arrived at work that day.”
In Canada, similar regulations are set by CSA Group, formerly the Canadian Standards Association.
And, Simmons doesn’t discount doing a little research at the nearest big box store.
“Big box retailers, including Home Depot and Lowe’s, have full safety bays, with safety vests, respiratory masks, hardhats and gloves. These retailers won’t direct you specifically on what to buy, but they do cater more to professional do-it-yourselfers.”
Other sources of information can be the technical data sheets and material safety data sheets that come with the products contractors are using, whether they’re stains, release agents, color hardeners or whatnot.
“The manufacturers provide that information but sometimes you have to ask for it,” says Dan Anna, Ph.D., CIH, CSP, the senior industrial hygienist at Johns Hopkins University Applied Physics Laboratory in Laurel, Maryland, and past president of the American Industrial Hygiene Association. “The safety data sheets will give you general information, but not always enough specific guidance, unfortunately.”
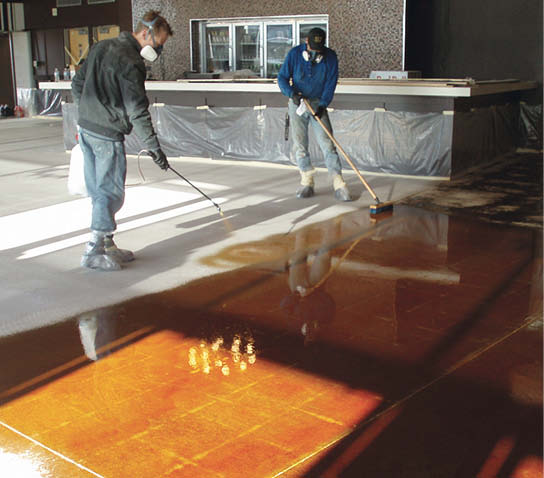
For those that do, however, the information may be specific enough to advise users to use chemical-resistant safety glasses, an organic respirator or a dust mask that’s approved by two other federal agencies, NIOSH (the National Institute of Occupational Safety and Administration) and MSHA (Mine Safety and Health Administration).
Saving someone’s skin
While respiration protection for anyone working around dry concrete or powdered chemicals is a must, along with lung protection, the biggest concerns for concrete workers are eye and skin protection.
When it comes to eye protection, the ANSI/ISEA standard for impact protection is Z87.1-2010. Glasses are supposed to protect eyes from flying particles, molten metal, liquid chemicals, acids or caustic liquids, chemical gases or vapors or potentially injurious light radiation.
Where eye protection isn’t enough, a face shield may be required. Even for employees who aren’t working directly with the concrete, its caustic nature requires that eye protection is needed anytime concrete dust is present, with goggles recommended, according to MCR Safety’s Smith.
But dust isn’t the only issue. Because wet concrete is highly alkaline and can burn in a matter of hours, long sleeves and pants are a must, as well as waterproof boots and gloves that are waterproof and alkali-resistant.
Anna says gloves can be a complicated issue, which helps explain the extensive selection of work gloves carried by some suppliers. While a typical work glove is mainly designed to protect from trauma, concrete workers need more.
“When you start getting into using chemicals and your hands are going to be in a powder or a liquid, then you have to look at that chemical and which gloves are appropriate to protect from exposure,” he says. “If you have the wrong glove material, it can permeate right through, almost like you have no glove on at all.”
Fortunately, Anna says, many manufacturers offer guidance tables on what work glove material should be used to protect against a given chemical, and if or how long it will take for the chemical to break through the glove material.
Fit for success
Along with the manufacturers’ websites and blogs, other sources of information on these products include the websites of OSHA, ANSI and NIOSH. And, even after a person has found the best product for his or her specific needs, there are a couple of other things to keep in mind.
One is that while some products — think safety vests — are a one-size-fits-all proposition, others are not, and fit can be critical to their successful use, says Dennis Capizzi, the industrial customer marketing manager for North America for head, eye, face and hearing for MSA Safety based in Cranberry Township, Pennsylvania.
“Properly fitting equipment helps to ensure that the equipment will perform as designed,” he says. For example, a respirator that hasn’t been fit tested prior to using on a job may have gaps on the sealing surface where the mask touches the face. These gaps may allow contaminants to enter.
“Size selection, fit testing and proper donning per the manufacturer’s instructions will help the user determine which mask size and style fit properly to ensure a secure fit and optimal protection,” Capizzi says.
These items also don’t last forever. Many products come with information on when they should be replaced, but a daily visual inspection is critical.
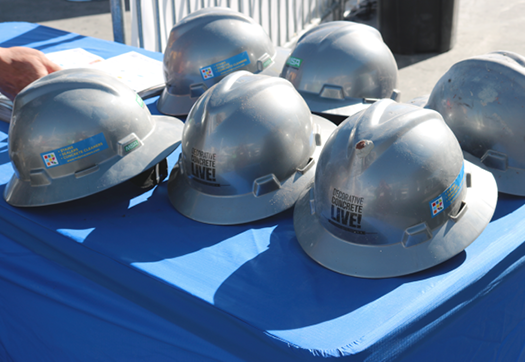
“The hardhat shell MSA produces can last up to five years, and the suspension can last up to one,” Capizzi says. Other factors, such as environmental conditions and use, can influence PPE’s life expectancy.
Users should follow the manufacturer’s instructions and inspect PPE before and after each use for signs of wear or damage. If any is found, “That item should be taken out of service, repaired or replaced per the manufacturer’s instructions,” Capizzi says.
www.aiha.org
www.bullard.com
www.hdsupply.com
www.mcrsafety.com
www.msasafety.com