
The previous issue’s “Success With Concrete Countertops” article dealt with the role of water in your concrete. This issue’s column concerns the water produced during concrete countertop production.
Concrete-making uses water. Cleaning concrete-covered mixers, tools and buckets uses even more water. Add to that the sludge that’s rinsed out and you’re often left with a big mess. Everyone who makes concrete faces this dilemma: what to do with all that dirty water and gritty sludge. Managing this mess is essential to maintaining a safe, productive shop.
Most concrete countertop shops have mixers that can make between 200 pounds and 500 pounds of concrete. Cleaning these mixers uses about 15 to 30 gallons of dirty water and generates roughly 5 to 30 pounds of sludge, which is a mixture of sand, gravel, cement and pigment. Concrete wash water is a slurry of cement particles, pigments and admixtures.
Dealing with the wash water and sludge is a challenge for every concrete countertop maker. One can’t simply dump it. Not only does this make a big mess, it is irresponsible and environmentally unsound. Sludge aside, concrete wastewater is a cocktail of sediment, alkalinity and dissolved metals and minerals that can damage water supplies and pollute the environment.
Concrete wash water typically has a pH of over 12, making it almost as caustic as drain cleaner. The EPA limit for wash-water discharge is 9.0, much lower than the typical pH of concrete wash water.
If wash water is discharged onto grass or other vegetation, the high pH can damage or kill the plants and may alter the chemistry of the soil, affecting their ability to grow back. If discharged into a storm drain that leads directly to a stream, river or lake, such high alkalinity can cause death or serious harm to aquatic life.
Independent tests of conventional concrete wash water show that it is a highly alkaline soup of suspended solids, dissolved minerals and other contaminants. Some of the contaminants contained within concrete wash water include: hexavalent chromium (chromium 6), copper, magnesium, manganese, nickel, potassium, selenium, sodium, vanadium and zinc. The wash water may also contain trace elements of petroleum products, admixtures and other materials from processing or treating the material.
In-shop solutions
So how do you deal with your wash-water problem? One simple solution is to collect all the water and sludge in some form of waterproof container, where the water is left to evaporate. The container gets emptied or hauled away when it is full of sludge. Many companies sell concrete washout berms or metal bins that are designed for concrete truck washout. However, the metal bins are too expensive for use in a concrete countertop shop. Plastic berms are generally inexpensive, but they take up space, require time for evaporation and don’t allow for recycling.
Another solution would be to create a homemade water treatment system. It’s common for concrete countertop shop owners. Typically a floor trench drain is used as the collection point, and the murky water is then pumped into a series of barrels where the finer sediment settles out. Often two or three plastic 30- to 55-gallon barrels are plumbed together so that the water gradually flows from one barrel to the next. Dirty water is dumped or pumped into the first barrel, where the larger particles rapidly settle out. Water flows from the first barrel into the second through a piped overflow.
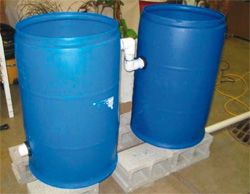
Each barrel is constructed so that water flows smoothly and gradually from one barrel to the next. Since the water in each barrel remains still and quiet, the fine particles settle out over time and collect at the bottom of the barrel. As the barrels fill up they are swapped out for empty ones. The full barrels are then emptied into a dumpster or landfilled directly.
The water that flows out of the last barrel often looks clear and is free of sediment. However, separation is not treatment, and the clear water that flows from the final barrel is far from clean and shouldn’t be dumped down the drain. It still is highly alkaline and contains dissolved contaminants.
True treatment involves not only separating the solids but also chemically treating the water to strip it of the contaminants and reduce the alkalinity. Only when the water is chemically treated can it be responsibly disposed of or reused.
Chemical treatment isn’t as easy as dumping a cup or so of acid into the water. Proper clarification and neutralization depend on the right products applied so they are most effective. Municipal drinking water and wastewater treatment plants use both sedimentation and tailored chemical treatment to clean and purify water.
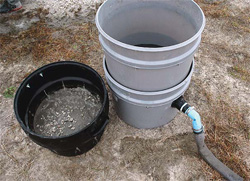
A new tool for the task
Recently, a simple and effective system called the Sludge Buster was developed that provides both particle separation and chemical treatment of the wash water. (Full disclosure: I was so excited when I found this product that I now sell it.)
The Sludge Buster is small, lightweight and portable, so it doesn’t take up valuable shop space. It’s easy to move it to where you need it, so your shop work area can remain flexible. And the Sludge Buster is easy to use and easy to clean.
The Sludge Buster uses three stackable chambers. The top chamber separates and cleans the coarse aggregates, and the middle chamber separates and cleans sand. The bottom chamber is where a chemical treatment lowers the pH and neutralizes and captures suspended solids and dissolved contaminants so they quickly settle out into an extra-fine sludge, also known as “flocs” in the water treatment industry.
The only part that must be disposed of in a dumpster or landfill is the extra-fine sludge. The aggregates (if there are any), sand and water can be recycled. Or, the water can safely be disposed of down the drain or outdoors. The water meets EPA standards for storm-water discharge.
By rapidly separating and treating wastewater from each project, the Sludge Buster amortizes the time needed to deal with sludge. You deal with a small amount of sludge project by project, rather than a large amount of sludge built up over multiple projects. The Buster also minimizes the amount of sludge you deal with. It separates out reusable aggregate and sand, resulting in only a small volume of extra-fine sludge to dispose of. Collection barrels do not separate out aggregate and sand, so they produce much larger volumes of waste that consists of mixed aggregate, sand and extra-fine sludge as well as untreated water.
The main disadvantage of the Sludge Buster is the initial cost: $548 for the unit. Occasional filter replacements are also required. Another disadvantage is that it does not make the extra-fine sludge disappear. You still have to scoop or dump the material out and dispose of it. However, no solution makes the extra-fine sludge just disappear. The Sludge Buster allows maximum recycling and minimum waste, shop space and time.