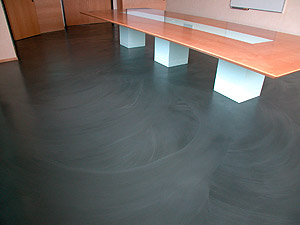
Be sure to match product attributes with the substrate and the desired outcome.
Overlays. Have you looked at how many there are for you to choose from these days?
As Ken Freestone, director of technical engineering at Elite Crete Systems Inc., aptly observes: “It seems like every year there are new overlay products released to the industry. Where splatter textures and plain gray restoration coats once dominated the concrete overlay industry, consumers now have virtually unlimited choices of color, texture, and thickness.”
There are self-leveling products, microtoppings, trowelable mortar toppings, epoxy mortar toppings, stampable products, stencil-grade products, splatter/ knock-down products, and more. How do you choose?
“The primary considerations will relate to the look the customer is trying to achieve and the substrate that the installer is working with,” says Ben Mack, manager of national accounts at Ardex Engineered Cements.
Parameters of the project will also help narrow the selection. For example, “Over large areas, a self-leveling topping may be used because the installer can cover a large area as each batch of material is poured,” Mack explains. In other situations a self-leveling product may not be appropriate, as on stairs.
Consider the substrate
The substrate over which you are applying an overlay is a critical component to your selection process.
If you are planning to overlay an interior on-grade slab, the options are wide open. As Scott Thome, director of product services for L.M. Scofield, explains, “If there is a normal amount of moisture, any overlays will work. That’s their intended use.” For exterior grade slab applications, stamp-grade, stencil-grade, and trowel and spray products will work, he says.
Be careful, however, when applying an overlay over an existing overlay. Lee Tizard, vice president of Floric Polytech Inc., says the problem with overlaying an overlay is that you rarely find an overlay that hasn’t been sealed. The issue then becomes the recoatability over sealers. You may find you are better off removing the base overlay and starting over.
Your choices also become more limited when applying an overlay system to substrates other than concrete, such as wood subflooring, terrazzo, tile, gypsum-based flooring and others.
Mack, of Ardex, explains, “It is difficult to install a product over wood without using some sort of system to help stabilize the wood from movement.” Also, he explains, any type of structure that has the potential to cause movement (such as the second level of a mall store), will cause the topping to crack.
You need to take a good look at the subfloor structure. Is it built solid? Is there a threshold joint? If there is flex in the deck, you have to figure that in. As Thome points out, “The thinner the overlay, the more deflection and vibration it can take, but it can’t take sheer, side-to-side movement.”
In some cases you may be able to use fracture-resistant or fracture-isolating membranes with microtoppings with high polymer content. But they are not a cure-all.
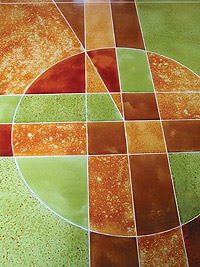
Decks and parking structures, also, have movement issues. In addition, you have to figure in slip coefficient and abrasion requirements. That may narrow your choices to coarser grade microtoppings or stencil-grade toppings.
How about traffic?
Most overlays can handle foot traffic. Vehicular traffic? Stencil- and stamp-grade are generally fine for vehicular traffic, Thome says, but not for forklift traffic. If that is a consideration, he says, you have to look at impact and point load. High compression strength does not necessarily mean an overlay can hold up to the crushing power of high density wheels.
Again, in this situation, you might turn to microtoppings. “Since microtoppings are very thin, you’re transferring the load through them, instead of having them absorb into the microtopping,” says Thome.
Of course, in any overlay situation, the cardinal rule of proper substrate preparation always applies.
As Mack observes, “There is no foolproof way to stop cracking, you can only minimize it. Remember, if there is a crack in the substrate, it will telegraph through the topping. That is why structural saw cuts are sometimes installed. The crack will have a tendency to crack within the saw cut and not be unsightly.”
Indoors or outdoors?
If you are familiar with overlay products, you should be aware that there are products that are designed to be installed indoors, outdoors or both.
In outdoor applications, rain, salt, dirt and other factors can all have an adverse effect on the topping if it is not protected. Crack repair and joint sealing are important to prevent water intrusion. “In a crack, moisture can get in and under the overlay,” Thome says. “Then, when traffic goes over it, you get a pumping action.” Ponding and excess water also can be problematic.
Fortunately, product manufacturers have technical installation guidelines on what products can be used outdoors and how to install them. Doing a little homework up front can prevent a lot of grief in the long run.
“There are protective sealers that increase or decrease various aspects of weather resistance, ranging from resistance to water, deicing salts, UV ray, freeze/thaw, acid rain and other factors,” Freestone says, “but the composition of the overlays themselves must be carefully looked at before applying just any old product.”
And technology is changing every day, so don’t be surprised if former “rules” might be broken in time. “For years most self-leveling overlays absolutely could not be used outside for fear of re-emulsifying,” Freestone says. “But there are manufacturers now that are making great improvements on the level of hydrophobicity among self-leveling cements.”
The mix design
If strength is important, one might tend to believe that the thicker the overlay, the stronger it is. Freestone is quick to point out that that just isn’t the case with overlays. The ultimate key to the strength of an overlay, he says, is in the mix design.
“Believe it or not, the aggregate size, shape, composition, volume and mix design is as equally as important as polymer-modifier content and composition. Most manufacturers are primarily concerned with either modifier-to-cement or modifier-to-water content. These ratios are important. However, most manufacturers will build in a safety percentage to make the overlay more ‘idiot-proof.’”
With mix design, he says, the composition and performance pitfalls of the modifier being used are critical; as is considering what the primary application the overlay system is going to be used to create, so you can better determine abrasion resistance, adhesion, exposure to the elements and tensile strength.
Then there is the aggregate. “It still depends on the specific application, but an ideal mix is one that has a larger aggregate content for abrasion resistance, medium aggregates to consistently fill the void between the large aggregate, and smaller aggregates to fill the void between the medium aggregates. Consistency in aggregate shape is critical and, therefore, angular or inconsistent aggregate shape simply won’t work well.”
Staining and sealing overlays
Not all overlays handle stains the same way. For example, most decorative concrete toppings and overlays can take a chemical stain, but high-resin-based materials don’t stain as well as those with high cement content. And acrylic stains can be used, too, but compatibility to the sealer you will use should be considered.
Compatibility between overlay and stain is essential. “That is why samples are almost always required by an architect or designer to determine how the look is going to turn out,” Mack says. “Some [overlay] manufacturers have done their own testing and provide their own stains.”
In choosing a sealer, Tizard advises that contractors make their choice based on multiple variables: compatibility, durability, cost-effectiveness, interior/exterior compatibility, breathability, chemical resistance, abrasion resistance, maintenance requirements, recoatability and sheen. You weigh your attributes and make a decision.
But Thome points out that in some areas your sealer options may be limited by law. “What’s key is, can you use solvent-based? That can eliminate half your sealers if you can’t.”
Repair and cost considerations
Some overlays are easier to repair than others.
Self-leveling products are the most difficult to repair, primarily because it is so hard to blend a repair in to the monolithic surface. Stampable and stencil-grade overlays can be patched back to a joint. And microtoppings and splatter/knock down overlays can be patched relatively easily.
It’s the color matching that’s the real challenge. Thome explains, “Repairing an overlay is really the work of an artist, especially if there were topical color treatments.”
As for the material cost for overlays, Freestone says he tends to view the material costs as immaterial. “I guess that is easy since we are the manufacturer, but really, the cost for any of our overlays runs in the range of 25 cents a square foot for broom-finish applications, 35 cents for micro-finish applications, 40 cents for splatter textures and knockdowns, 42 cents for skip trowel slate finishes, and $1.25 for elaborate thin stamped overlays. When you consider that these applications are being sold by the installer for $4 for basic finishes and upwards of $9 for the more detailed applications, you can see what I mean when I say the cost isn’t material.”
But some overlays, such as epoxy-based overlays, can have much higher material costs. On a basic scale, including material and installation, “Terrazzo is the most expensive overlay, followed by epoxy mortar,” Tizard says. “Self-levelers, one-quarter-inch mortar trowel-downs and stampable overlays are in the same ball park (in the middle). The least expensive are microtoppings.”
On the other hand, Mack says there may be more to consider in the higher-material-cost versus installation-cost equation. “Self-leveling products are more expensive because of how they are designed to work (ease of installation, fast track). Trowelable products are less expensive, but the cost of installation could be a factor since it may take more labor to trowel down a microtopping over a large area.”
So, which overlay product will you choose for your next job? Much of the information you need to make the decision is available from the manufacturers of the overlay products on your “options” list. If you understand each product’s limitations, you should easily understand which ones will be compatible with the specs of your project.