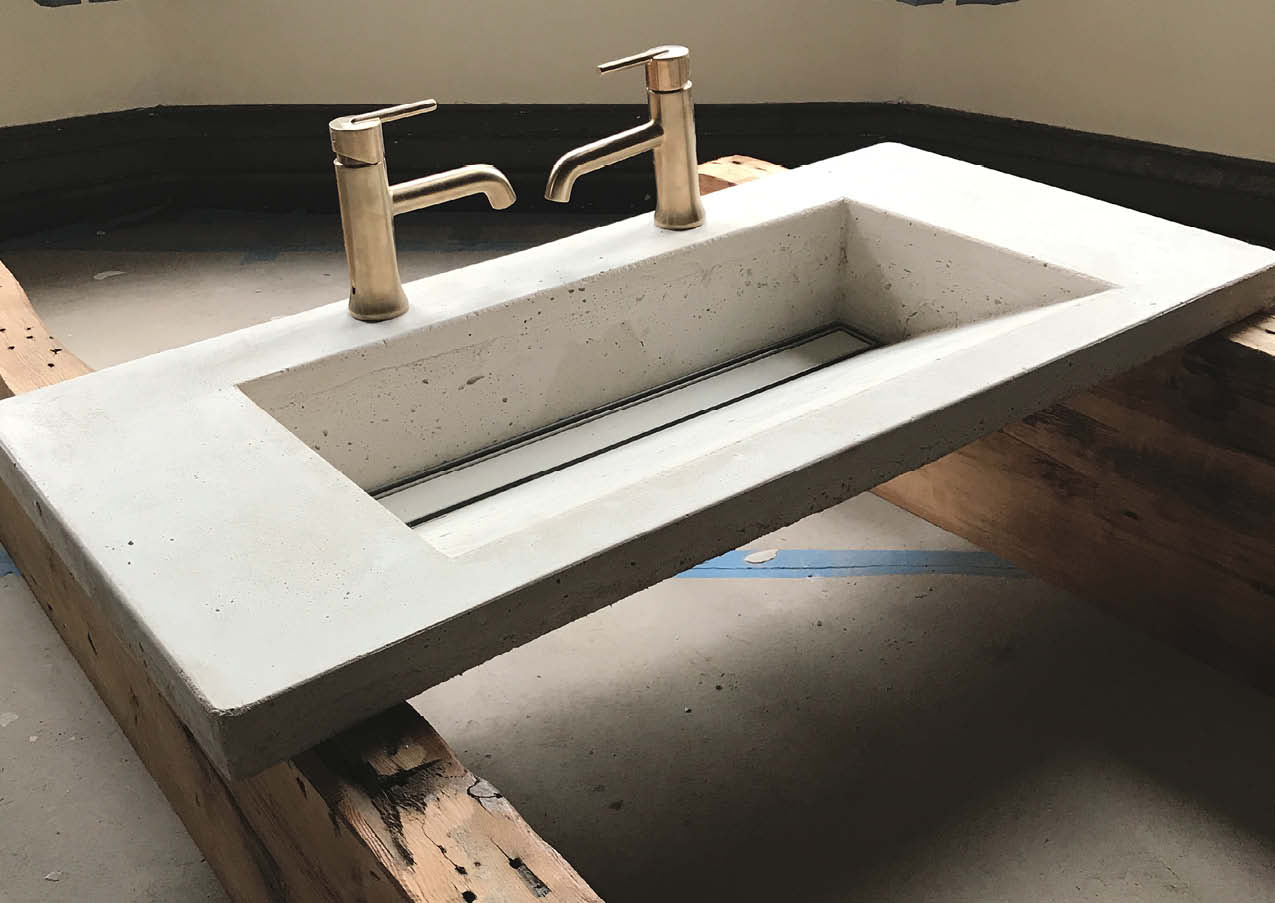
Aldo Buffone thinks of his avocation to be more artist than contractor. Either way, Buffone’s efforts are one of an innovator. 1025 Studio, the Philadelphia-based artisan’s company, has garnered a local reputation for its creative upgrades of the city’s historic downtown loft structures.
The majority of Buffone’s unique work is the transformation of drab historic warehouse spaces into modern living areas. The artisan integrates the traditional materials found on-site into the renovation. He’s adapted his skills of welding, woodworking and painting into his projects and recently embraced a new material — decorative, fiber-reinforced concrete.
Incorporating fibers in concrete to create durable elements is not new. The Romans first used horse hairs in many of their iconic structures. And in the last 20 years, fibers have become standard fare to reinforce high-performance floors and slabs.
But what is new is the development of specialty fibers for the decorative concrete industry. These fibers are not the stiff, long fibers that strengthen concrete sidewalks or mitigate plastic shrinkage cracks. These engineered materials provide superior strength at lighter weights for thin panels and countertops.
This new technology of nontraditional reinforcing materials is now aiding Buffone and innovative artisans like him in their quest to create projects that seemingly defy gravity. These products not only help decrease the weight of the concrete element, but they can also enhance the element’s service life by increasing the concrete’s durability.
Strength with artistry
Decorative concrete contractors are benefiting from the research on ultra-high performance concrete (UHPC). These mixes combine an ultra-high performance mineral matrix with reinforcing fibers. UHPC is commonly used on architectural precast concrete elements such as rainscreens and facades.
UHPC is a useful material due to its special hardening properties. It yields exceptional strength, ductility and durability but, more important for decorative concrete work, UHPC has excellent forming qualities in its plastic state. Artisans can craft significantly thinner pieces that require little or no traditional reinforcement.
Several innovators are transferring UHPC technology into decorative elements. An excellent example is the UHPC-crafted landscape features placed on the campus of Simon Fraser University in Vancouver, British Columbia. Nolan Mayrhofer’s Vancouver-based concrete artistry firm, Szolyd Development, had the leadership role on this project. (http://concretedecor.net/decorativeconcretearticles/vol-17-no-2-february-march-2017/public-work-exemplifies-mingling-of-science-engineering-and-art/) Szolyd (pronounced solid) is among the businesses participating in Landscape Furnishings. This is a British Columbia-based group of designers, manufacturers and technologists whose goal is to make durable products that age gracefully and are suited to the environment.
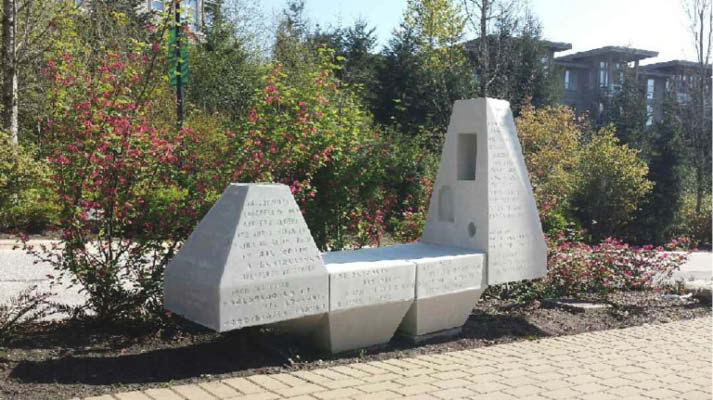
From flatwork to artistry
Greg Hryniewicz of Hyde Concrete in Pasadena, Maryland, started out as a traditional concrete contractor, but about 15 years ago he expanded into concrete surface treatments including staining, stamping and eventually polishing. Intrigued by the opportunity decorative concrete offered, Hryniewicz and his team became artisans when they cast their first concrete countertop.
Along with professional satisfaction came moderate commercial success. In a short time, Hyrniewicz’s interest in creating decorative structural elements took off.
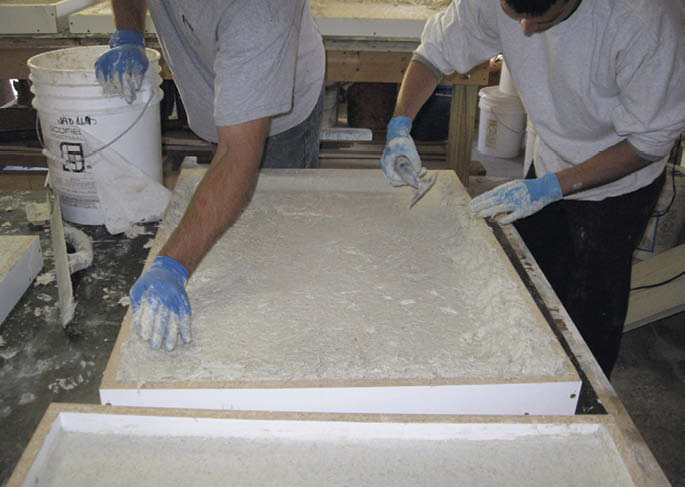
In 2016, the contractor launched Hyde Products, a division dedicated to the factory-like production of decorative concrete elements. Hyde Products’ portfolio includes unique architectural modern concrete sinks, countertops and other precast products marketed nationwide. He and his team are now expanding into a new production facility poised for growth.
Hryniewicz launched the venture because of his belief that general contractors and building owners are open to a new approach in construction, such as using decorative concrete elements made offsite.
Attuned to improving profit margins, labor efficiency and project delivery expediency, many general contractors are adopting modular construction techniques and are discovering they are an effective resource.
Hyrniewicz believes the No. 1 reason for his firm’s successful expansion into modular decorative concrete fabrication has been the use of alkali-resistant glass fibers. First introduced into the European construction industry more than 40 years ago, alkali-resistant fibers are finding renewed interest in decorative concrete, with a new generation of mixes with these fibers permeating the industry. The unique concrete additive not only increases products’ durability for transport and installation, but it aids in their final appearance.
Alkali-resistant glass fibers are an engineered material with an affinity to cements. Contractors can use these fibers in their mix design to cast countertops that have high-tensile strength. Since these fibers have about the same density as the ingredients in a typical concrete mix, they quickly disperse with hand-held mixers with minimal clumping.
Many manufacturers use proprietary recipes that blend proportions of micro and macro fibers that ease mixing and maximize concrete’s hardening properties. These preblended mixes, many of which are sold in dissolvable bags, include powdered specialty additives that result in a “just add water” batching procedure. Ensured with proper mixtures, users can anticipate concrete products that consistently produce blemish-free textures without the risk of fibers showing.
Hyde Concrete’s success with creating architectural elements using alkali-resistant glass fibers continues. One of its countertops recently was awarded first place in the 2018 ASCC Decorative Concrete Awards program (https://concretedecor.net/decorativeconcretearticles/vol-18-no-2-febmarch-2018/ascc-names-2018-award-winners).
A lighter alternative
Buffone’s key to success is the sense of space with style he creates in nontraditional settings. Since many of his loft renovations have concrete floors, Buffone incorporates that same texture in vertical elements. He’s been able to accomplish this look by casting elements that are thin and stylish.
Along with concrete sinks and countertops, Buffone has been creating thin concrete planks that are used as shower wall surfaces and sink backsplashes. These water-resistant decorative surfaces share the same appearance as the main concrete fixtures.
Buffone credits much of his decorative concrete success to NForce-Pro, a fiber he’s been using in his mixes. Introduced during World of Concrete 2017, NForce-Pro is manufactured from industrial hemp, one of the world’s strongest and most durable natural fibers.
NForce-Pro is specifically designed for decorative concrete by its manufacturer, Canadian Greenfield Technologies Corp. It provides the same strength characteristics as glass fibers but at about half the weight.
The hemp fiber is the result of CGT founder Mike Pildysh’s keen interest in offering an effective concrete ingredient. Pildysh, who has been active in the concrete construction industry for more than 35 years, used his experience in structural design and concrete admixtures to come up with the concept of using natural fibers. Since the fibers are hydrophilic, their physical characteristics cause them to better disperse in fresh concrete during mixing and placing.
However, CGT faced a challenge when it came to commercially manufacturing the fibers. The company had to figure out a way to devise an effective processing method to properly create the size and nature of a suitable fiber.
Development went forward when CGT came up with a special processing machine that first focused on producing fiber segments suitable for concrete that didn’t damage the fiber’s structure. CGT’s research and development team engineered NForce-Pro to provide maximum mix stability and exceptional surface quality in decorative concrete applications.
There is an additional benefit to this natural fiber — it’s a sustainable product with a low carbon dioxide footprint. Buffone uses NForce-Pro to enhance concrete’s plastic and hardened properties, but many of his clients are simply intrigued that their decorative concrete was made with a sustainable material.
“They welcome being able to tout how green the concrete is by using hemp,” says Buffone.
www.canadiangreenfield.com
www.hydeconcrete.com
www.landscapefurnishings.com
www.szolyd.com
Micro-fibers to the rescue
Fibers are also improving the durability of concrete repair materials. At World of Concrete 2018, Euclid Chemical introduced a micro-fiber technology that creates a low-shrinkage, highly durable concrete repair mortar.
Decorative contractors attempting minor repairs are often frustrated by the look the replacement material leaves on the total project. If the traditional repair mortar is too rich, portland cement-based materials shrink when they dry and cause cracking. If the repair material is too wet, the bond between the repair and host concrete can be weak.
Euclid’s new micro-fiber technology has been specifically developed to help prepackaged concrete repair mortar avoid cracking when hardened. The tiny monofilament, polypropylene micro-fibers are distributed evenly throughout the repair mortar.
The micro-fibers enhance four hardened concrete properties that can reduce repair life. The fibers increase tensile strength, increase the modulus of elasticity, decrease tensile creep and reduce the material’s drying shrinkage rate.
www.euclidchemical.com