I firmly believe that the lifeblood of our industry is new and innovative products that continue to move the decorative market forward. A close second, the oxygen of our industry, is word-of-mouth advertising by satisfied clients who have had their expectations met.
Over the past several years as I’ve traveled from coast to coast promoting the decorative concrete industry, I’ve witnessed a growing tendency by an increasing number of contractors who exclude sealing decorative concrete as part of their scope of work. Some might describe this omission as an angst or even some sort of subconscious fear of failure. Those who still offer this service seem to take a “fingers crossed” or “roll the dice” approach.
What I’ve witnessed doesn’t come from lack of effort or from the industry not wanting to put out a quality product. Rather, it seems to come from not quite knowing how to keep up with or adapt to ever-changing rules and regulations that have necessitated formula changes away from “our daddy’s sealer.”
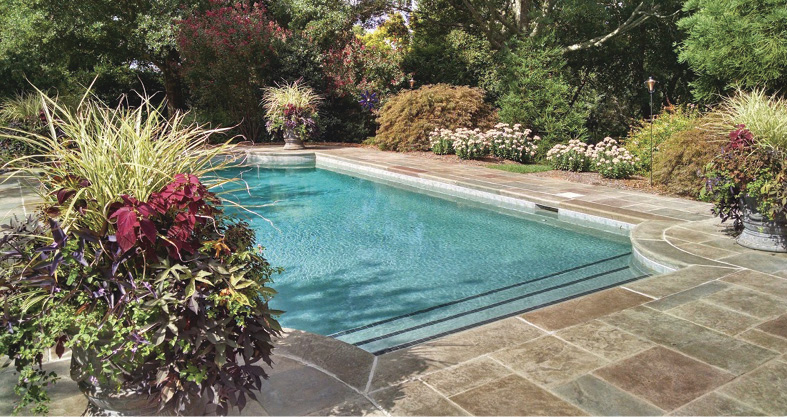
An early-on example
The first time I personally came across this sealer situation was several years ago in California. A friend of mine was having a very expensive backyard swimming pool built for his family. He asked me if I’d help his wife and him choose the dry shake hardener and release powder color combination that would best complement the surrounding rock, brick and other features of the backyard. Once the colors were chosen and with the contractor onboard with the selections and how and where they would be applied, it was full speed ahead. Or so my friend thought.
The pool deck was poured, the colors applied and the pool proceeded as designed to near completion. I asked my friend to let me know when everything was completed and sealed because I wanted to see the end result. That’s when he informed me that the general contractor, as well as the pool deck contractor, had excluded any type of sealer from the project.
I asked, “What do you mean excluded from the project?”
He said, “They do not and will not seal concrete.” My friend and I had discussed various color combinations with the clear understanding of how the pool deck would be enriched and enhanced by the type of sealer used. My friend was very frustrated to say the least.
I called a local contractor who in recent years has become somewhat of an expert on sealing concrete in California. He explained to me that most of his work comes by way of referral from contractors who no longer seal concrete.
When I asked how a contractor could complete only part of the project, he told me many contractors are afraid to apply sealer for various reasons including, but not limited to, issues associated with applying low-VOC sealers. Many states — California and parts of Utah being the most restrictive — require all concrete sealers to be 100<VOC grams/liter. There are many other states where the law is 350<VOC g/l.
Applying low-VOC sealers requires more than just a cursory knowledge of how these sealers perform under various conditions, such as time of day, heat, wind and direct sunlight, and how they are to be applied, such as sprayed or rolled, what type of spray equipment and proximity of spray tip to the surface. When one applies a low-VOC sealer outside of ideal conditions many things can happen, and none of them is good. Bubbling/blistering, flaking, lacking adhesion, applying too heavily or with too few applications can all cause problems.
Of course, even sealing concrete with a high-VOC sealer, where still permissible, can present problems if one is not knowledgeable and careful.
I wish I could say that my experience in California was an isolated incident, but it’s not. I’ve found that in nearly every state from coast to coast I’ve traveled, there’s a growing number of contractors who don’t want to seal concrete.
Knowledge is power
Most contractors in our industry continue to include sealing within their scope of work and do an admirable job. Yet, I find that this trend of not sealing a bit troubling and believe it will ultimately have a negative impact on our industry if not properly addressed.
The reasoning behind contractors not wanting to include sealing within their scope of work can’t be pinned down to one single thing. Yet, there are common threads. Some don’t understand how low-VOC sealers work. Others say they don’t want the liability/slip factor. Still others want to get in, get paid and get onto the next project. Some who understand the low-VOC sealers don’t feel that their crew has the “skill set” or they don’t have a specialized “detail crew” to cost effectively handle the sealing aspects.
It has been said that knowledge is power. Well, if this is true then I advocate for manufacturers to better disseminate information and help properly train our industry. Yes, low-VOC sealers are more difficult to apply than “our daddy’s sealer.” However, when properly applied, they are just as durable and will provide long-lasting protection.
I said earlier that the lifeblood of our industry is new and innovative products and that the oxygen of our industry is a satisfied client. The industry will continue to innovate and, in this case, provide new sealers that are durable regardless of how stringent VOC regulations become. Our satisfied clients will be like the old shampoo commercial of the 1980s — They will tell two friends, who will tell two friends, who will tell two friends ….