Here are some facts and advice in the form of questions and answers that may help you maneuver the market if you’re interested in learning more about mixers and pumps, courtesy of Jim Farrell, CEO of Blastcrete Equipment Co.
What should contractors look for before purchasing a mixer? How does size and application play into the mix?
There are five types of mixers suitable for decorative concrete projects: pan or turbine, paddle, spiral, rotary drum and continuous. If liquid polymers are a part of the mix design, or if retention time in the mixer is required, this eliminates continuous mixers. If the mix design includes aggregate larger than 3/8 inch in diameter, this eliminates a spiral mixer. Determine the capacity of the mixer based on the largest anticipated batch size for the job.
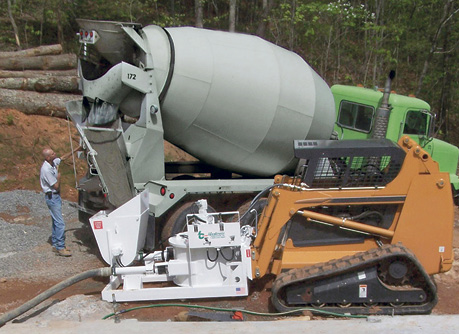
What are best practices for using a mixer in decorative concrete?
For decorative concrete, select the best type and size of mixer for the specific application. Always keep the mixer clean and well maintained to ensure the longest life and best return on investment. Additionally, know the mixer’s capacity and be sure to never overload it. Also, work to control respirable dust from the materials while working with a mixer.
Are you seeing any industry trends in concrete attachments?
We’ve seen the popularity of concrete pump attachments grow over the past 10 years because a pump attachment is the least expensive way to enter the pumping business. It gives contractors the ability to expand their service offerings with little expense and also opens the door to new contractors seeking a fast ROI. Mixer attachments have been available for a decade but have not gained the popularity of the pump attachments. Many decorative concrete material requirements have historically been too small to justify a mixer or pump attachment.
Pumps differ in this industry. What types of pumps do decorative concrete contractors use and what are the features/benefits?
The concrete material pumping industry is huge. That being said, pumps for decorative concrete projects would be considered the smallest capacity category of concrete pumps, with an output capacity up to 5 cubic yards per hour or less. These include squeeze pumps, which are also called peristaltic pumps and rotor stator pumps.
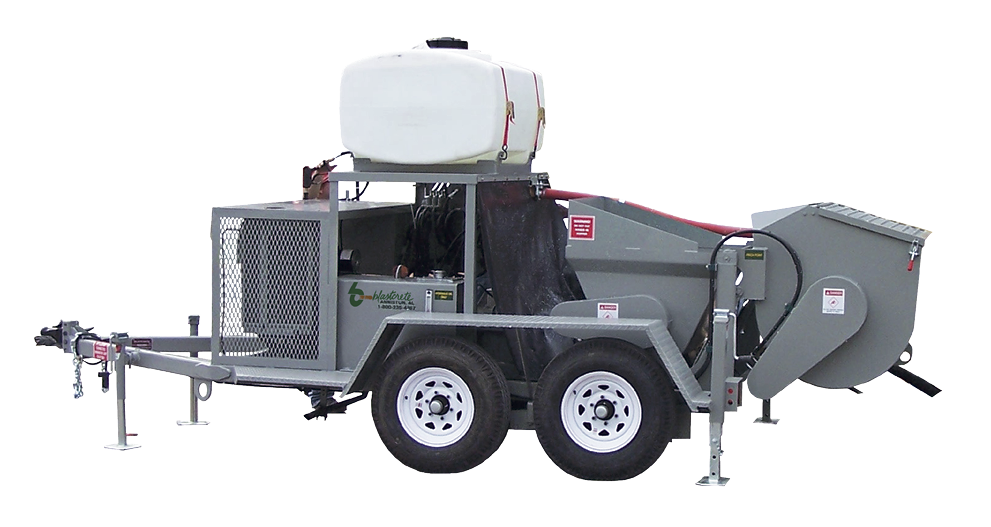
Squeeze pumps safely pump aggregate up to 3/8 inch in diameter and can even pump in reverse to remove blockages or obstructions without damaging the pump. Operators also clean them quickly by simply pushing a sponge ball through the pump. Rotor stator pumps typically wear fast when used for material with aggregate that’s larger than 1/8 inch. They cannot be run dry of material without causing damage to the stator. Rotor stator pumps offer about 30 percent more pumping pressure than a squeeze pump. When choosing a pump for an application, it’s more important to focus on sizing rather than pump speed.
What types of preventative maintenance and servicing should be done on pumping and mixing equipment, and how regularly should it be done?
Overall, it is very simple: Keep the pumps and mixer clean and maintained after each use.
When it comes to each type of pump, knowing a few guidelines goes a long way in getting the most out of your equipment for years to come.
Hydraulic peristaltic pumps only have one wear part: the rubber pumping tube, which makes for easy maintenance. Not only that, but rubber pumping tubes are nearly half the cost of rotors and stators. Try to keep a log of the amount of material pumped through each pumping tube to further reduce maintenance costs. Use the sponge ball technique for simple cleaning.
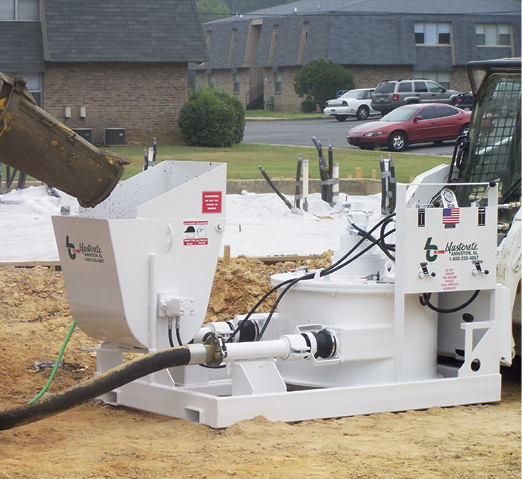
Look into the mechanical seal maintenance requirements manufacturers offer for rotor stator pumps. It’s important to select a model that gives operators the ability to perform mechanical seal maintenance without taking apart the rotor and stator. This drastically reduces labor expenses, keeping equipment where it’s profitable: on the job site. Rotor stator manufacturers recommend cleaning the machine by flushing the pump and delivery system with water.
Cleaning a continuous mixer is much faster than a batch mixer. Unlike a batch mixer, material is constantly entering a continuous mixer so operators avoid having to clean the mixer after each batch; operators simply clean the mixer once at the end of the day. It’s also important to regularly check and change out the blades to avoid any unwanted changes in the composition of the concrete produced.
What changes have you seen in this industry? Any predictions on what the future will bring in terms of types and sizes of jobs or new product developments?
The decorative concrete market has not had a history of using equipment requiring larger mixers and pumps. It’s obvious the market is growing, and typically if a market continues to mature, there will be more and more opportunities for higher production mixing and pumping equipment.
On the other hand, we’re seeing more specialty work in homes and hard-to-access areas. As a result, we’re developing small, wheeled squeeze pumps that will easily pass through a 28-inch-wide doorframe to give decorative concrete contractors an easy-to-maneuver solution for completing their jobs. Once it’s completed in 2017, it will be the most compact, lowest-volume pump that we have ever developed.
What is next in terms of product development for your company?
The small squeeze pump for the decorative concrete market is coming in 2017, and we are working on a new mixer/pump combination for the gypsum flooring and concrete overlay market, as well.