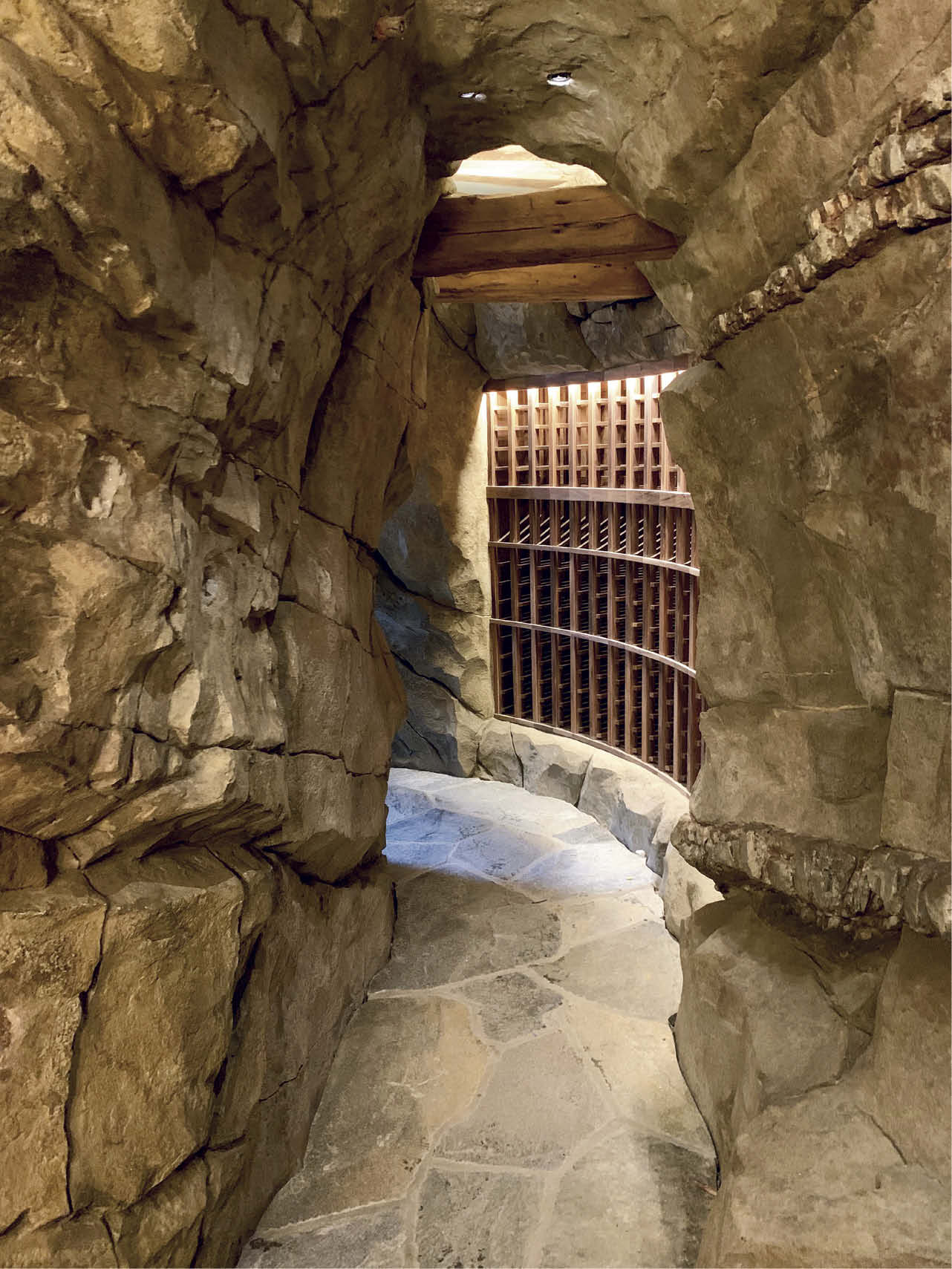
Looking for a way to expand your business’ offerings or add a little more creativity to your life? Either way, the vertical surfaces market may be for you.
While the idea of hand-carving and coloring concrete on vertical surfaces has been around for at least two decades, its popularity is on the rise, both with homeowners looking for something unique for a fireplace or outdoor kitchen, and for special applications.
As with other creative endeavors, there’s no one formula for getting it up and getting the color and appearance just right. Different methods and products have their own positives and negatives, but those who make a living with vertical concrete suggest it’s an area where classes and a willingness to experiment can pay off both in cash and satisfaction.
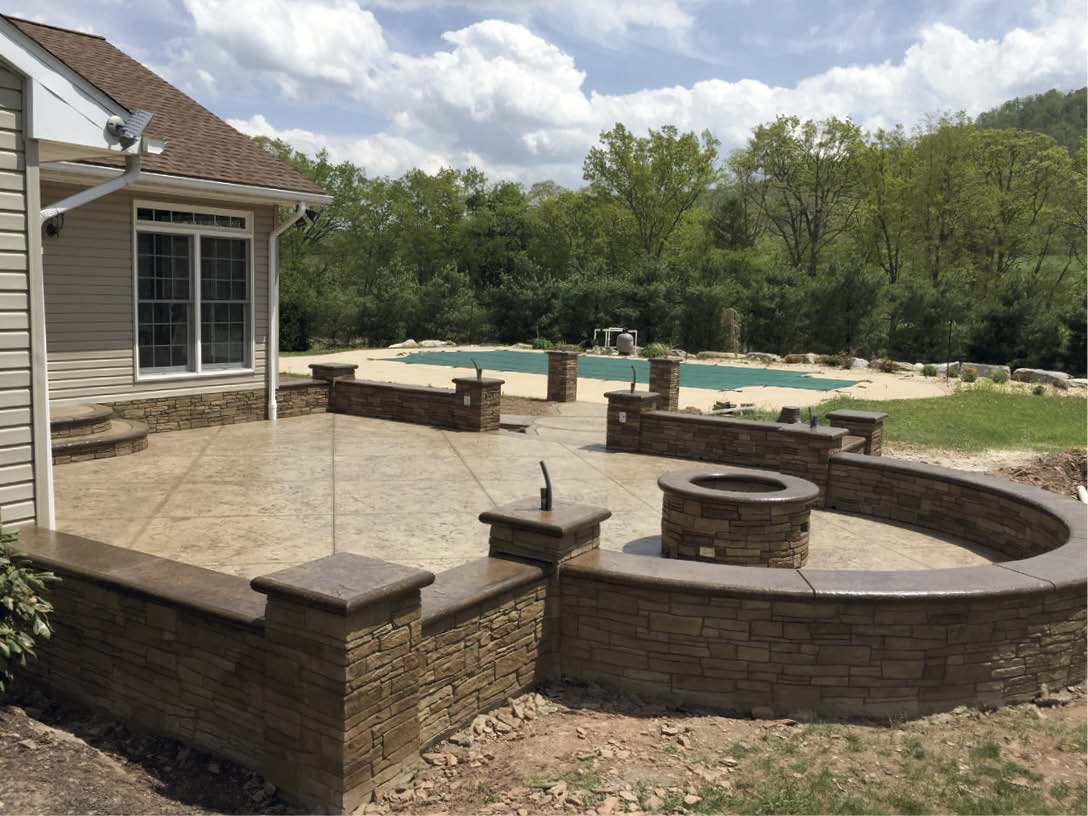
At home … everywhere
For a technique that was foreign to many people in the concrete industry until recent years, vertical wall carving is on a roll.
“It’s definitely gaining traction in the market,” says Jeremy Wilkerson, owner of distribution company DreamKrete in Midlothian, Virginia. “Vertical is one of those really unique types of finishes in decorative concrete that a lot of people are interested in.”
And, for such a custom product, it may come as a surprise that the biggest market for carved vertical concrete involves backyards of homes large and small.
“Outdoor is a huge area for growth,” says Nathan Giffin, owner of Vertical Artisans in Hickory Hills, Illinois. “The vertical area has expanded largely into outdoor spaces that would be a natural fit, such as artificial rocks for waterfalls and things of that nature (like) outcroppings, hardscapes. But we’ve also branched into seat walls, planters, outdoor fireplaces and outdoor kitchens.”
Emil Gera of Gera Concrete in Weatherly, Pennsylvania, agrees that currently he has a lot of residential customers who want exterior amenities like fire pits and seat walls in their backyards. But, he points out, today’s vertical carving projects don’t have to be outdoors or simulate rock.
One of his jobs this past winter involved building a fireplace/entertainment center in a living room. The massive unit equipped with a large TV looks like it was made from large timbers, with sliding barn doors on the front and a fireplace beneath the TV. “The barn doors open and close and give (the owners) extra storage,” Gera says.
Warren Ness, who offers both vertical concrete services and training through his Spokane, Washington-based business Rock Sculptor, says for him business is evenly divided between residential and commercial clients — and surprisingly they’re often looking for the same things, like pools and water features.
“Beyond that, you have fireplaces, facades and covering up unsightly foundations,” Ness says. And, while the rock finish is the most popular, simulated wood is gaining ground.
Joshua Russell is something of an outlier in this group of artists. The owner of Beyond Vertical Concrete in Byron, Michigan, says his split is probably 80% commercial and 20% residential, which is right in line with his business plan. Whereas he continues to work with families with lower budgets, he concentrates on larger projects. Recent projects have included exhibit spaces for zoos in Detroit, Toronto and Alabama, as well as water features for a new resort in Ludington, Michigan.
His work at the resort includes a carved feature that’s based on a boat theme, Russell says, after he convinced the owner to let him carve replicas of the famous ships that have sunk in lakes Michigan, Heron and Superior.
A tale of two foundations
Possibly fueling the rise of carved vertical concrete is a newer method for providing the foundations of these jobs: foam core construction.
Vertical Artisans’ Giffin, for one, attributes much of the current market’s diversity to foam core construction — particularly the speed at which it allows projects to be built and the lighter weight of the end product.
“We don’t see the same types of problems with foam core construction that we do with lath and mesh,” he says. “The lath is a galvanized product, but we still see cracking. There’s rusting of the metal. There’s exposure.”
Rock Sculptor’s Ness agrees that the pitfalls of rebar or lath construction are well-known. However, he says it’s also a time-tested method that has the advantage of providing structural integrity when needed.
“I look at foam as nothing more than a placeholder,” Ness says. “There are certain guidelines to follow when using foam, and one of them is to go extra thick with a specialized, fortified, fiber-rich mortar because then you aren’t relying on the foam. The shell of the mortar is providing the structural integrity.”
Beyond Vertical Concrete’s Russell admits foam core construction can be a touchy subject. For one thing, there’s not a lot of data on it and what information is available has mostly come from Europe. He says some people he was working with couldn’t get a building permit for a job in Florida involving foam core construction because of concerns about liability and insurance.
Currently, however, in Baton Rouge, Louisiana, he’s working on a water project where the grotto and the slide are rebar-engineered, and the mass of the fountain is foam. For the parts of the structure that need to structurally sound, he’s including rebar reinforcement.
Russell’s not the only one who’s doing a mix of both methods. DreamKrete’s Wilkerson estimates about 85% of the residential projects he supplies are done with foam, as well as some of the small commercial projects.
Gera estimates his split at 75%-25%, although he says part of the problem with foam is its availability.
“We’re doing mostly foam because it fits better for the fireplaces and seat walls,” he says. “I see rebar and steel more geared toward water features and things like that.”
The substrate the artisans put their work on isn’t always the same, but there’s a great deal of agreement that using premixed products is better than creating from scratch — although there’s a certain amount of tinkering with the products anyway.
Rock Sculptor’s Ness, for instance, uses a vertical carving admix called Car-VZ, which he co-developed with Trinic LLC, that’s aimed at solving common problems that plague vertical carved concrete. It’s one of several such admixes on the market.
“You source your portland cement and your sand,” he says. “Car-VZ takes the sand and cement and transforms it into a mortar that can be sculpted and has water-repelling properties, as well as anti-shrinking agents. One of the nice things about this admix is being able to adjust the sand quantity and type.”
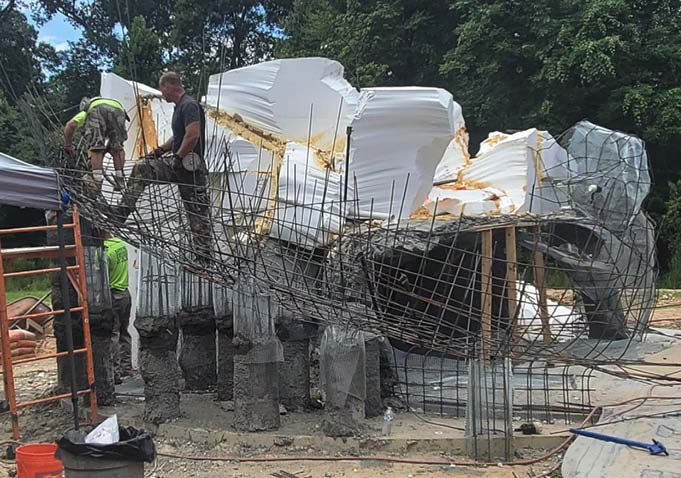
Ness adds that it’s not a one-size-fits-all when it comes to mixes, and that textural finishes from sandstone to decayed wood require slightly different formulations that greatly impact the final look.
Beyond Vertical Concrete’s Russell agrees there are several good mixes developed for the vertical market, often with good, long setting times that carve well, although some work better for certain applications than others. “They all have their place in the market,” he says.
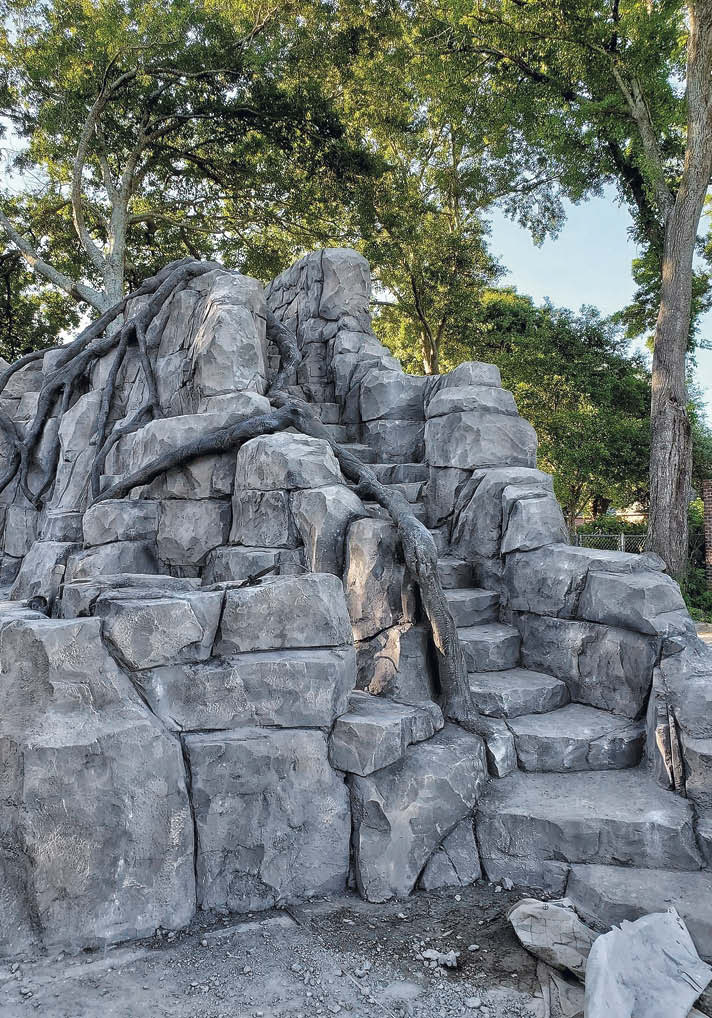
Color conundrum
When it comes to coloring — and sealing — their projects, these vertical concrete artists take a variety of approaches, often based on years of experience.
Vertical Artisans’ Giffin, for instances, says he’s going back to his concrete roots when working with color hardeners and color releases to create color outdoors.
“The industry at-large seems to be dealing with fading issues, leeching issues and a general weakening of color with time,” he says. “The first rock I ever did sits in my front yard. I did it with color hardeners more than 20 years ago, and it still has its colors.”
The only other option he sees for long-term color durability is acid stains. However, that isn’t everyone’s goal or preference.
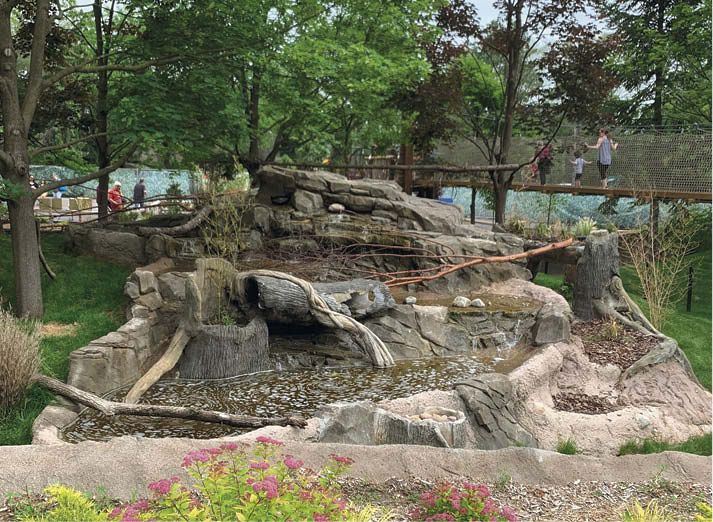
Gera Concrete’s Gera says he prefers water-based stains, which he applies with spray bottles, an airbrush or a high-volume, low-pressure spray gun. The reason: “It’s very easy for me to achieve realistic-looking colors with them, and they’re transparent.”
Rock Sculptor’s Ness prefers using integral color on anything that will be submerged in water, and a mix of acrylic colorant, glazes and transparent washes if it’s not.
“Each one is site-specific,” Ness says.
Whatever system is used — anything from exterior latex paints to water-based stains — the real secret to success is being patient, says Russell of Beyond Vertical Concrete.
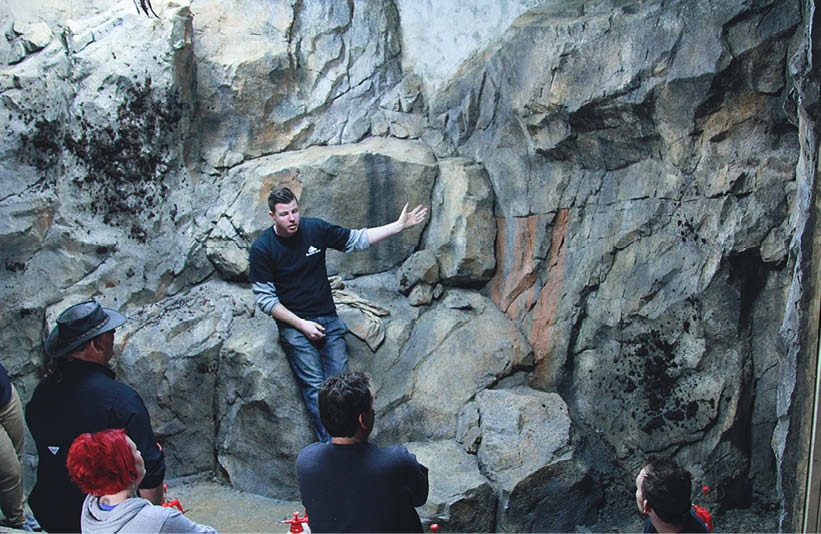
“It’s the end of the job and people want to rush through it and get paid, but you have to let each paint layer dry completely before you glaze and overlay,” he says. “It may look good when it’s first applied, but the next day it’s mottled into a monotone color without highlights.”
Russell further advises keeping the color palette simple. And, while he seals anything near water, he says he leaves much of his work unsealed.
“Typically, the pigment saturates so deep into the concrete that mechanical bonding has never been an issue,” he says. “I’ve been back to visit a few jobs after six or seven years, and I think they look better than the day I left because of nature putting down its patina.”
Regardless of the job, Rock Sculptor’s Ness says the best advice he can offer is to plan.
“Have the sequence of events mapped out in your brain before the mud goes up,” he says. “And, to make it as realistic looking as possible, do little sketch studies.” These can just be crude outlines that show the elements of form, color and texture to help achieve the hyper-realistic look people are seeking. Ness feels so strongly about this that he’s revising his approach in his training classes to stress planning.
DreamKrete’s Wilkerson, who used to work as a contractor before becoming a distributor, says the bottom line is people need to work with the mud and let their imaginations flow.
“Spend money on quality training courses,” he urges. “There are a lot of good trainers out there, and if you pick up one thing they do differently from the next guy, it can take your business to the next level.”
www.dreamkrete.com
www.geraconcrete.com
www.rocksculptor.com
www.verticalartisans.com