The decorative industry grew up on the “one size fits all” high-gloss sealer which was the go-to coating for decades. While high gloss is still widely used, low-gloss and natural finishes in the decorative concrete industry have been gaining momentum as homeowners, architects and designers seek more ecofriendly, green and natural-looking sealing options.
In some cases, the demand has less to do with the sealer’s environmental impact and more to do with people wanting a “natural appearance” while the sealer still protected the substrate. The best way to achieve this look, while still providing protection, is to use a penetrating sealer.
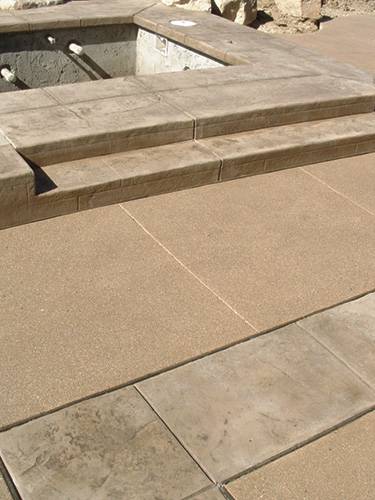
Penetrating sealer is a catch-all or umbrella term used to describe multiple chemistries and hundreds of products. What these various chemistries have in common is that they all penetrate the surface, provide some level of stain resistance and don’t leave a film. This lack of a film means there won’t be any gloss or shine, and the concrete, not a sealer film, will be the wear surface.
This last point of wear protection is especially important in the decorative world because there are color systems that require a sealer film to “lock in” the color and provide abrasion and wear protection. Stain and dye systems come to mind as the two big markets where this is important. It’s also important to note that some decorative systems look better with a high-gloss coating, like metallic epoxy coatings and certain stains and dyes. Overall, the decorative market has been more about gloss and color enhancement, and less about performance when it comes to sealers.
While relatively new to the decorative industry, penetrating sealers have been used successfully in other markets for decades. Originally developed for the stone, masonry and concrete flatwork industry, penetrating sealers primarily resist water and stains, while not changing the substrate’s appearance. Their primary functions have been salt and acid resistance, efflorescence control and water resistance.
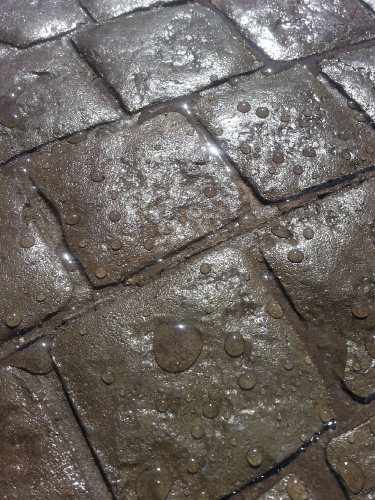
The characteristic of not changing the substrate is a drawback to using penetrating sealers in our industry, as many decorative finishes have historically relied on a sealer to enhance and darken the color, known as the “wet look.” The good news is there are now multiple penetrating sealers that provide some level of enhancement and darken the substrate without forming a film.
The other relatively new development is the use of certain penetrating sealers in conjunction with traditional thin film-forming sealers. In some cases, solvent-based penetrating sealers can be applied before or after an acrylic thin-film sealer is applied. This combines the surface darkening and protection of a film former with the internal stain resistance and deep protection of a penetrating sealer.
So, here’s our question:
How does a penetrating sealer work?
A penetrating sealer reduces a substrate’s ability to absorb water or stains at the molecular level. Imagine the concrete surface as a series of microscopic doors (pores) set end to end. Without any kind of sealer, those doors are wide open, allowing easy entry for water or stains. In physics and chemistry, this is referred to as having a high level of energy (surface tension for liquids). Every surface in the universe has one.
A penetrating sealer’s goal is to reduce the energy level of the substrate to below the energy level of the staining material. Basically, it’s a battle between substrate and stain, with the lowest level of energy winning.
Once the sealer is applied, those doors aren’t open as wide, which keeps the stain from getting into the surface. Note the doors don’t close completely, which allow vapor and gas to move through the substrate, but they don’t allow larger molecules with higher energy to pass through.
This is what differentiates a water-resistant, breathable penetrating sealer from an impermeable waterproof coating. Variables like the stain’s particle size and surface tension, the substrate’s finish and density, and environmental conditions such as temperature and humidity all play a part in this complex battle occurring at the molecular level.
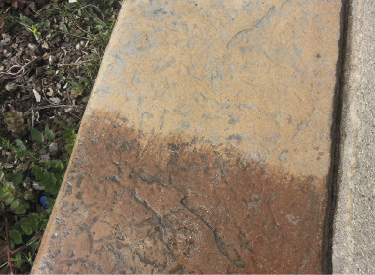
Wide range of choices
Here’s a quick overview of the common types of penetrating sealers and how they’re used in the decorative concrete industry. This list is based on the key active ingredients found in each type. It’s important to note that many penetrating sealers are blends of various ingredients. Read the technical data sheets and safety data sheets. And don’t be afraid to talk to the manufacturer if you have questions about a specific product and application.
Silicone – Depending on who you talk to, silicone-based sealers may be considered penetrating or film forming. In this instance, we’ll consider them penetrating, even though they are shallow penetrators. They offer excellent water and oil resistance, but often have a life span of a year or less due to poor UV stability. They can darken the substrate and are a good choice for colored concrete or exposed aggregate finishes where water, stain and graffiti resistance is required.
Silane – This type has the smallest particle size which allows for deep penetration into dense substrates. It bonds with cementitious material to reduce porosity and resists water and oil very well. To be fully effective, it must saturate the surface, which increases the cost per square foot. However, it has a life span of 5 to 8 years. Whereas it doesn’t enhance color much, it’s a good choice for stamped concrete, colored concrete, exposed aggregate finishes and overlays.
Siloxane – This type has the largest particle size which prohibits deep penetration. Its weak bond with cementitious material reduces porosity and it’s used most often to help porous substrates improve water resistance. Since most of the material is near the surface, it has a short life span of 1 to 3 years. It doesn’t enhance color and can be used on broom-finished colored concrete, stamped concrete, exposed aggregate finishes and concrete pavers.
Silicate – This one’s small particle size makes for good penetration. Silicate salts (lithium silicate, sodium silicate, potassium silicate) form calcium-silicate-hydrate crystals which densify the surface of the concrete. It provides some water and oil resistance, but is noted for its crystallization, long life span and hardening properties when used in conjunction with diamond polishing.
Siliconates – This sealer has medium-sized particles that form an internal cross-linked membrane which greatly reduces porosity. It provides excellent water and oil resistance, has a long life span and doesn’t enhance color. It performs best on porous substrates like broom-finished colored concrete, stamped concrete, exposed aggregate finishes and concrete pavers.
Hybrids – These sealers are combinations of penetrating sealers and/or other resins (acrylic) designed to provide a specific type of protection or substrate enhancement. A common hybrid would be a silane/siloxane blend to take advantage of the properties of both materials. Penetrating sealers that enhance color are usually blends of penetrating molecules and resins like acrylic.
Try them, you may like them
Where is this growth of penetrating sealers in decorative concrete coming from? Polished concrete has created a demand for natural-looking concrete with an aesthetic beauty without any type of film or coating. The other reason is 20+ years of decorative concrete sealer issues and complaints are finally taking their toll. Year after year, the biggest single source of complaints in the decorative concrete industry continues to be issues with film-forming sealers.
Where and when a penetrating sealer can be used in place of a traditional film-forming gloss sealer on a decorative project will come down to the client’s demands, the type of decorative finish and the installer’s comfort and experience applying these types of sealers.
If you’re not familiar with penetrating sealers, do some research and try them out. You may be surprised how easy they are to use, as well as the benefits you can achieve by not creating a film.