Building owners are asking contractors around the country to create decorative outdoor concrete features on areas not normally associated with concrete surfaces such as decks and roofs. The transformation from exposed wood surfaces to waterproof concrete decking is a factor in the growth of the whole deck and patio market. According to a November 2017 market analysis report prepared by IBISWorld, the demand for deck and patio construction will experience an annual growth of at least 5.5 percent.
There are several design trends supporting the forecasted growth of waterproofed concrete deck treatments. Architects use these systems to reduce a project’s initial cost. In many markets, it’s more economical to top off the building with waterproof concrete decking systems than purchasing more expensive ground-level acreage to provide outdoor amenities relished by prospective buyers and renters.
In the residential market, waterproofed durable decorative concrete surfaces offer a quality alternative to the joist-supported under-decking treatment on elevated decks. When protected from the weather elements, these under-utilized areas can be expanded to patios, outdoor cooking areas or additional secure storage.
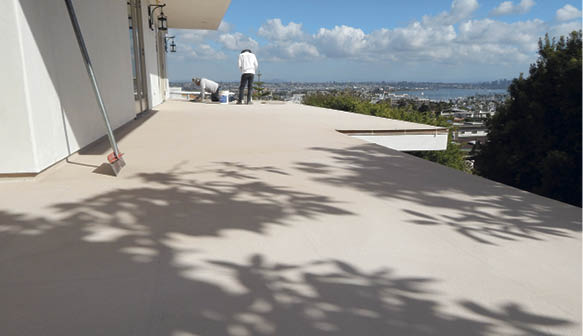
And since concrete overlay systems can now be placed on both interior and exterior floors, they offer a distinctive floor design on both sides of the patio door. Katy Tomasulo, the editor of Professional Builder, reported in the magazine’s 2018 hot trend surveys of the design industry that “Buyers increasingly want the same amenities on their decks and patios that they have inside.”
Business opportunity knocks
When Norman Clayton performed his first deck treatment project more than 30 years ago, little did the contractor in San Marcos, California, realize that waterproofed decorative concrete decks would become an important part of his business. Currently he estimates that waterproofing wooden decks accounts for nearly two-thirds of his company’s billings.
Christiaan Zaayer, owner of Quality Sealants in Escondido, California, also has seen an increased interest from her company’s core customers in using decorative concrete to waterproof wooden decks. Zaayer has opted to use this new service to organically grow with the company’s key accounts. Currently, waterproofing accounts for about 15 percent of the company’s total billings, but that number is growing.
Clayton, who owns Kaimana Coatings, and Zaayer are just two contractors who are expanding their decorative concrete businesses by adding waterproofing to their portfolio of services they offer to general contractors.
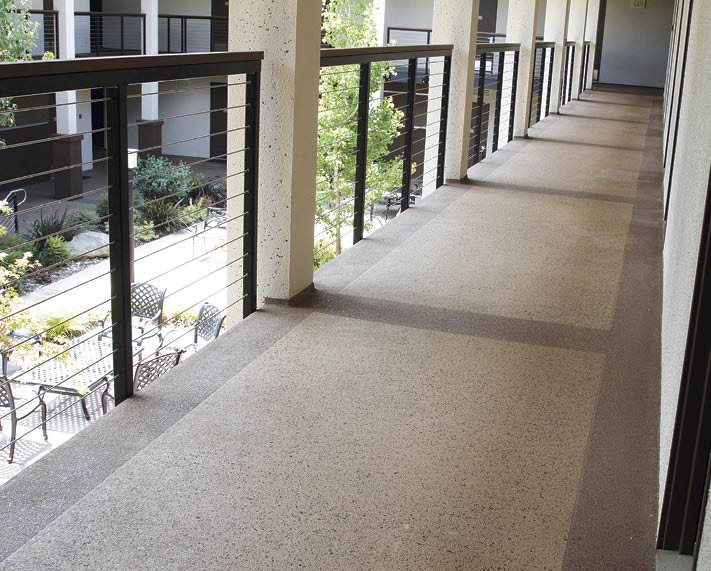
The combination of decorative and waterproofing skills may be the industry’s fastest-growing business opportunity. While the market potential seems inviting, transforming from a slab-on-grade focused business to waterproofing elevated wood decks requires careful planning and a commitment to details.
How to get started
Marc Di Zinno, architectural representative for Westcoat Specialty Coating Systems, has helped contractors around North America expand their portfolios into waterproofing. Di Zinno, who has witnessed the growth of Kaimana Coatings and Quality Sealants, offers contractors three important considerations as they extend their services to include waterproofing.
First, contractors should select a coating manufacturer with whom they feel comfortable. Many manufacturers offer training on their system followed by experienced field support through all phases of the project.
Product manufacturers direct their marketing efforts to architects, design-build owners and specifiers to promote their proprietary systems in job specs. To receive a full warranty, these manufacturers will insist that only authorized contractors or those who have received certified training on the application process be allowed to perform the work. It’s important to receive the general contractor’s approval before opting to use a nonspecified system.
Second, each waterproofing project is unique so closely examine the details, Di Zinno says. “Contractors should use the normal two- to three- week period following the contract award and start of work to do some serious checking.”
If contractors discover a challenging detail, they can seek support from the product manufacturer to determine the appropriate solution that maintains the system’s warranty. Also, Di Zinno continues, pay close attention to the terminology used in the bid documents. Many jurisdictions have enacted standards regarding waterproofing to their local building codes. Most manufacturers are aware of these requirements and can provide advice on product selection and installation.
Finally, perform a thorough review of the drawings, especially focusing on flashing details for the worksite’s perimeter and thresholds. Di Zinno advises contractors to confirm that the deck will have the appropriate slope, adequate drainage and flow features including cricket flashing. (Crickets are triangular shaped and are built up to direct water to the appropriate drains in the deck. This is most commonly done in the plywood substrate, Di Zinno says, but can also be installed with the Westcoat products.)
“Don’t forget to ask questions about the railing detail, including how and where it will be installed,” says Di Zinno.
Clayton agrees with Di Zinno’s suggestions but offers an additional important consideration before adding this service to your business: the initial investment.
Before offering waterproofing to clients, Clayton says he invested more than $10,000 for the right equipment. Equipping crews with the proper surface preparation equipment, product mixers and application tools are essential for quality installation. Along with these production tools, plan to invest in upgrades for proper safety equipment including fall protection and dust suppression/containment.
Many hands on deck
Prior to starting Kaimana Coatings in 2012, Clayton was first a technical trainer and problem-solver for a coating manufacturer before becoming a project director for several waterproofing contractors. He’s come to realize that while most decorative concrete contractors have a good working knowledge of how to install microtoppings and overlays on slabs, they need to recognize there are some important considerations when preparing a deck or wooden substrate.
The coating contractor is often the last sub on the job, warns Clayton, and a host of preceding contractors can compromise the quality of the install. So wise waterproofing contractors, he says, should ensure the built structure conforms to the construction plans. If any detail doesn’t match, they should document the deficiency’s specifics and alert the general contractor and client.
Clayton’s crews begin their inspections by checking the sturdiness of the framing and underlayment, and looking for any deflections caused by walking on the structure. The deck must be stiff, he says, and the supporting framing systems must be resistant to movement. Pay attention to vibrations caused by movement on adjoining stairs or decks.
Along with the structure’s soundness, the underlayment must be checked. “Most systems work well over properly engineered substrates,” says Di Zinno.
If you’re tasked to install a waterproofed concrete deck on a plywood substrate, make sure the framing crew installed a material rated for exterior applications. Exterior plywood carries an X stamp, which identifies it as suitable for use outdoors.
CDX is the most common exterior plywood grade. Marine-grade plywood is similar to standard exterior-grade plywood, but its core consists of knot-free sheets, eliminating the possibility of water pockets forming within the structure.
Down to the details
Zaayer insists that knowledge of how other aspects of construction may impact your waterproofing project can be the difference in profit or loss. Once you’re assured that the supporting structure is sound, she advises you to check out the building’s components that could cause moisture intrusion. Ensure that possible sources of water such as gutters, downspouts and trims don’t expose your soon-to-be installed decking to undue rainwater or snowfall.
Zaayer says her biggest concerns are with flashing and deck slope. Often there are repairs or adjustments to the original construction that didn’t include proper flashing. And unlike slabs on grade that are relatively static, elevated wooden decks are subject to post-installation movement. There could be settlement caused by freeze-thaw.
Zaayer’s passion for detail extends into product selection. Her crews only use decking systems that include primers for the wooden substrate, reinforcement such as metal lath or composite lath combined with a repair mortar or cement board, waterproofing coating and flashing materials, and a primer that prepares the system for the decorative topping and sealer.
When possible before starting applications, Clayton encourages contractors to prepare a small mock-up treatment area away from the potential highest visual exposure. It’s best to conduct the mock-up a week or so prior to the treatment date, he says, using the same equipment that will be on the project.
www.kaimanacoatings.com
www.qualitysealants.com
www.westcoat.com
Interested in Inspections?
For contractors who want to learn more about inspection procedures of residential elevated wooden decks, the International Association of Certified Home Inspectors offers the download of “Inspecting a Deck, Illustrated” on its website at www.nachi.org/deck-inspections.htm.
The document focuses on single-level residential and commercial wood decks and references both the InterNACHI’s Residential Standards of Practice and the International Standards of Practice for Inspecting Commercial Properties.
Learn from the Concrete Decor archives
Todd Fisher, who works on installs, research and development for Unique Concrete in West Milford, New Jersey, offers a great project profile on a wooden deck upgrade: https://bit.ly/2G3ot0w
Concrete Decor columnist Chris Sullivan examines a failed concrete overlay on a wood deck in “Why is My Concrete Deck Overlay Failing, But Only Where It’s Exposed to the Elements?”https://bit.ly/2ryj4tN