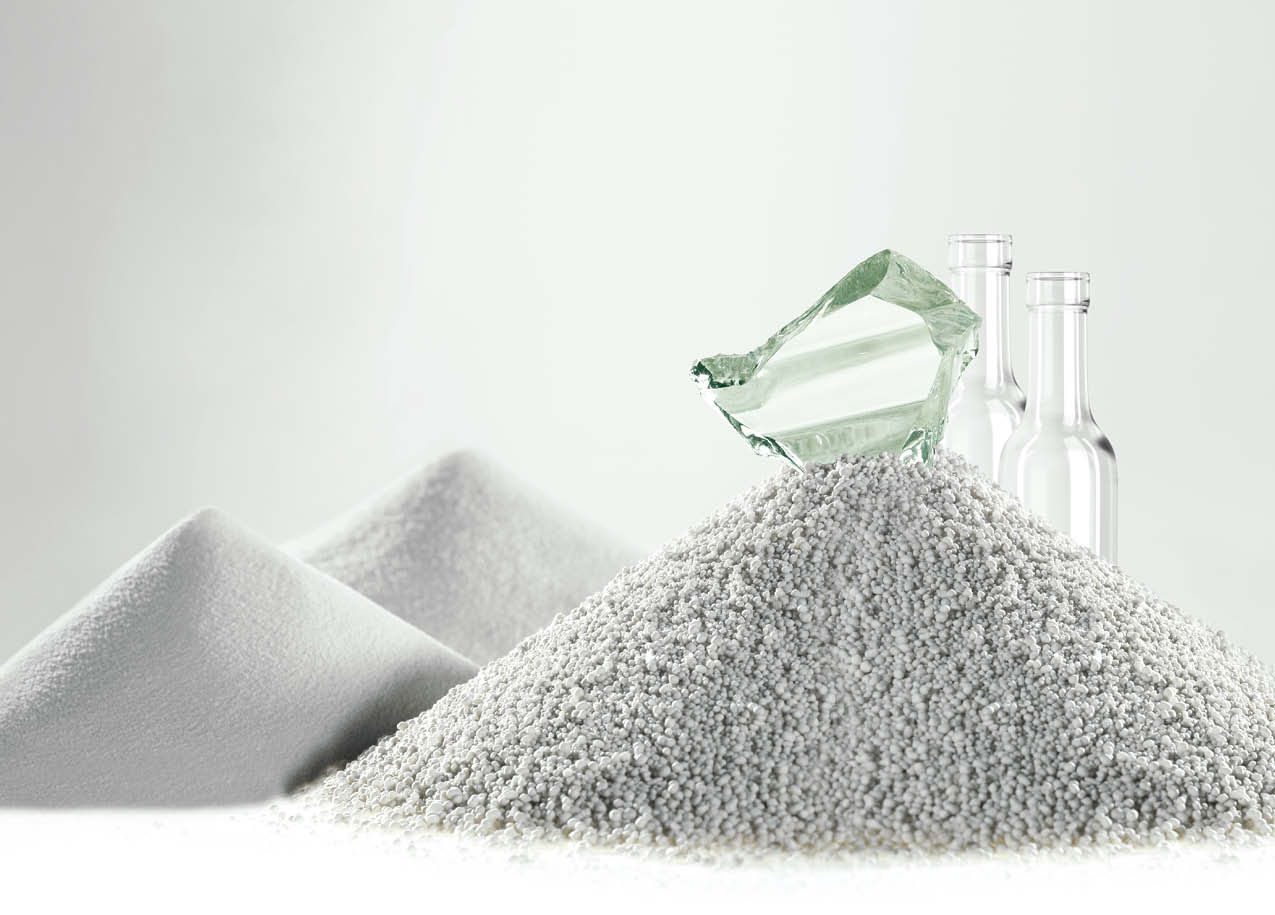
Historically, repurposing glass for use in concrete mixtures has simply involved crushing and grinding the glass to a smaller size. Resizing alone doesn’t bring glass processing far enough to create a functional raw material for the concrete industry. Rather than a re-engineered raw material you just end up with a resized material. Crushing is indeed the first step in the process of recycling glass… but, it can’t be the last step if you’re trying to create something new and innovative like turning waste glass into expanded glass.
A previous article on using crushed waste glass in concrete. It pointed out the problem associated with this is alkali-silica reaction (ASR). Alkalis, present in portland cement, that encounter “reactive aggregates” initiate a chemical reaction that forms a gel. Add in a little moisture intrusion and the result is a bad day at the beach for the concrete as the gel expands when hydrated.
Signs of ASR are only seen in compact concrete. With expanded glass (EG) as an admixture, you create porous concrete. In these enhanced concretes the swelling pressure caused by the ASR gels is dissipated through the pores. No hairline cracks, edge spalling, drops of gel or other peculiarities appear.
Expanding glass is a process where crushed glass cullet is upcycled on the particle size level and re-formed into spherical-aerated-granules that don’t contribute toward ASR. The material is stable and inert with a chemical composition containing around 71% silicon dioxide (SiO2). The process of converting waste glass into expanded glass also creates two additional raw materials.

The process of expanding glass
After learning how to expand clay for his family’s precast concrete business in the Bavarian region of Germany in the ’60s and ’70s, Hans Veit Dennert upped his game in the early ’80s when he discovered how to expand glass. Subsequently, in 1983 he founded Poraver GmbH, the largest producer of expanded glass aggregates worldwide. He still presides over the company today.
Dennert’s process begins with a very fine gradation of post-consumer recycled glass called cullet. This unrefined soda-lime glass arrives at the plant simply pulverized to fit into a certain particle size range. The glass is then dried and quickly sent to the ball mill where the glass is ground down to very fine flour (< 36 microns). The glass flour is combined with a silicate binder and an expanding agent and blended into a viscous slurry.
Next they granulate the slurry. For larger grain sizes above 1 mm, they use a granulating dish. Additional glass powder is added to the slurry to form a semidry material which is applied to an inverted rotating dish. The slurry then rolls downhill like a snowball and forms into spherical-shaped grains. Changing the inversion angle or the rotational speed can alter the size of the grains.
Smaller sizes
For smaller sizes, the technology is not as simple. To make grain sizes below 1 mm, they use a spray dryer. It’s a different process from the granulating dish but nets the same result. They then spray the slurry into a drying chamber, which consists of a four-story conical tower that provides a controlled environment for the slurry to cool and form into spheres.
Along with kaolin clay that acts as a non binding agent, the spheres enter a linear rotary kiln heated to more than 1,400 degrees F. They then expand 200% and begin to cool. The process of sieving and packaging the grains into seven different grain sizes ranging from .04 mm to 4 mm happens at this stage.
During the heating process, the kaolin turns into metakaolin, a reactive pozzolan, also called a supplementary cementitious material (SCM), that can replace ordinary portland cement (OPC). A standard OPC replacement ratio is 15-20% by weight.
The three raw materials created in the glass expansion process are:
Expanded glass aggregate (EGA) – This material is an ultra-lightweight aggregate used to reduce density, insulate (R-2/inch) and absorb sound.
Glass flour – This material is processed to a particle size smaller than 36 microns. The flour becomes a reactive pozzolan and replaces portland cement.
Metakaolin – This material is an SCM. It, too, is a reactive pozzolan, the softest one on the scale.
How to use expanded glass in concrete
First match the particle size of your existing fine sand with the corresponding EG grain size. For face mixes, self-consolidating concrete and sprayable mixes, the EG grain size is typically .25-.5 mm. For gravity-cast mixes, architectural and structural precast, the EG grain size is typically .25-1 mm.
If there are larger aggregates in the mix, you can replace some (or all of them) with EG grain size 1-2.5 mm.
Finally, you must decide how much you’re going to replace. The concrete’s mechanical properties and performance requirements decides this ratio.
A key component of reformulating with expanded glass is to replace the sand in the mix by volume. This is because expanded glass has a specific gravity value less than 0.550. Most sands and aggregates have specific gravity values north of 2.5. Thus, replacement by volume is key as expanded glass is nearly five times lighter than silica sand.
Once you know your replacement ratio, you are ready to mix and cast. Expanded glass uptakes water at a rate of 20-30% mass. One hundred pounds of dry EG will absorb 20 to 30 pounds of water.
This is actually minimal absorption when you consider that 100 pounds of EG is 7 cubic feet, or ¼ yard, of material. The water that weeps into the expanded grains begrudgingly weeps back out of them. This water remains available, within the matrix, for cement hydration.
Expanded glass works as an internal curing agent extending the dehydration time of concrete and dry mortar. This is due to the initial water absorption followed by a slow return of the mix water to the matrix from within the expanded glass granules.
Mixing methods and uses
The first method is to take 20% of the calculated mix water and pre-hydrate, or quench, the expanded glass with it. Absorption takes only a few seconds. Blending the EG with other aggregates happens at this stage, and the mixing process proceeds as usual.
The second method is to run through the mixing process as usual and then introduce the pre-hydrated EG after the cement, sand, aggregates, water, and additives are all blended. This is the most common method in ready-mix and structural pre-cast concrete operations.
By turning waste glass into expanded glass using and using it as a sand and aggregate replacement, three distinct benefits can be obtained:
Performance benefits – Including extreme density reduction, improved thermal and acoustic absorption values, protection from ASR, and lowering the e-modulus which makes the concrete less brittle.
Health benefits – Including reducing crystalline silica content of the overall matrix since EG contains no crystalline silica. Using EG can help concrete product manufacturers conform to the new OSHA regulations regarding airborne crystalline silica.
Environmental benefits
Another benefit of turning waste glass into expanded glass is that expanded glass is 100% recycled content, a sustainable aggregate. Expanded glass helps products and projects earn LEED points.
It is also widely available throughout the United States and comes in various package sizes. Additionally, it is available in bulk for silo storage.