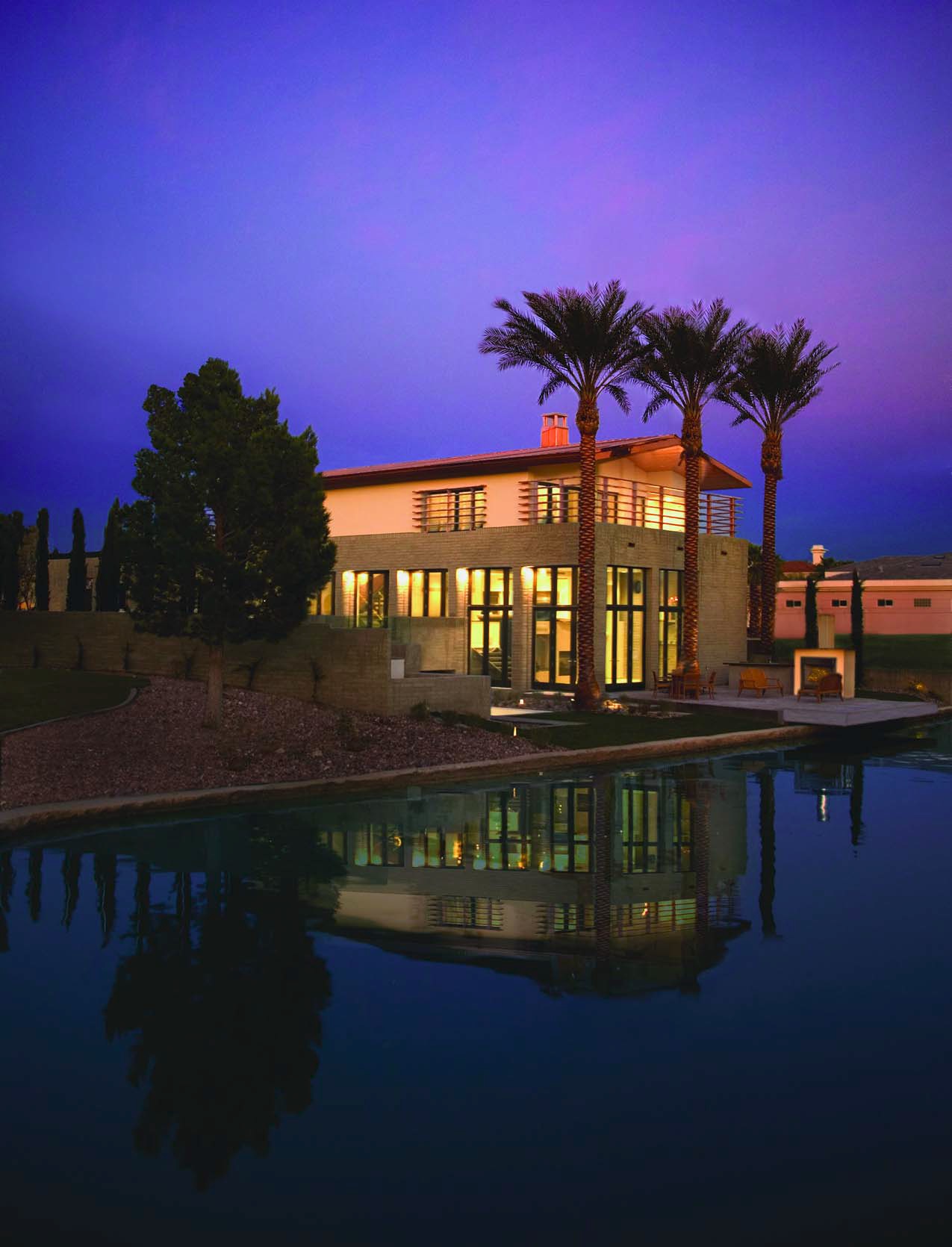
The ancient Romans had the right idea. If you want a structure to last for centuries (think Coliseum, aqueducts), shelve the sticks. Build it out of concrete.
And although most Europeans grasped onto this concept eons ago — their dwellings are built to be passed on from generation to generation — it’s taken the less frugal Americans awhile longer to literally bring the concept home.
But it’s here and finally catching on. According to the National Association of Home Builders, the market share of concrete homes has steadily increased in recent years, from 3 percent in 1993 to more than 14 percent in 2002. In 2002 alone, more than 150,000 single-family homes were built with a variety of exterior above-grade concrete wall systems, including masonry construction, which uses concrete blocks to form the basic structure of a home; cast-in-place forms, which are filled with concrete to create walls, then removed once the concrete is hardened; precast panels, which are cast in a factory and then assembled in large sections at the job site; and insulating concrete forms (ICFs), where concrete is pumped between two layers of foam insulation to form walls.
The No. 1 reason concrete homes are gaining in popularity depends on who you ask, and where. “There are five or six strong benefits associated with concrete,” says Dave R. Pfanmiller, managing partner of the Security Building Group, L.L.C., who built the first cast-in-place concrete home in Raleigh, N.C., and is currently building concrete condominiums in North Topsail Beach. “Depending on your geographical location, the list is reprioritized.
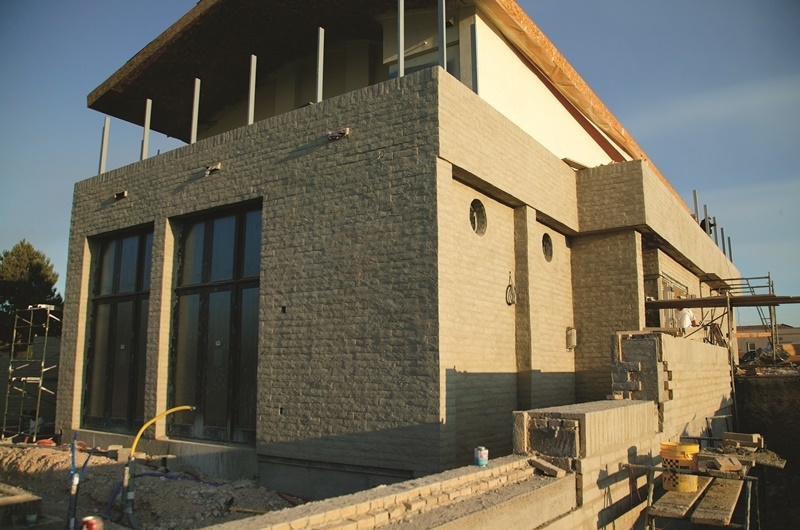
“At the beach, strength and safety are a big issue. In the Milwaukee area, it’s energy efficiency. In another part of the country, it’s durability [resistance to insects, mold or fire]. You just reshuffle the deck and you come up with the same benefits, just in a different order.”
But the list remains the same. Concrete walls make for a house that’s comfortable, solid, durable, resistant to natural disasters, quiet and incredibly energy efficient.
According to Reid T. Pocock Jr., president of Dominion Building Group in Virginia Beach, Va., who’s been building homes with PolySteel ICFs for more than 10 years and has twice won national awards for energy-efficient building, “My clients typically save between 50 percent and 70 percent of what it costs to heat and cool a stick-built house the same size.” As a matter of fact, he adds, he’s built a 2,200-square-foot house in neighboring Smithfield that has an average heating and cooling bill of $18 a month. And it gets these results with an HVAC system that’s half as powerful as the typical unit installed in a house that size. Other builders across the country report similar savings for their concrete homes.
Building a home with concrete usually costs 3 percent to 5 percent more than the conventional stick-built method. “There is a learning curve,” says Jim Niehoff, residential promotion manager for the Portland Cement Association, headquartered in Skokie, Ill. “That cost could be as high as 10 percent to 12 percent until the contractor gets the hang of it.”
But, Pocock quickly points out, the slightly higher initial cost will quickly be recouped by the homeowner through the reduced cost of heating and cooling alone.
Energy efficiency aside, Pocock concedes that in his neck of the woods homeowners want a concrete home because it can stand tough in hurricane-force winds (Isabel did visit the area last year), but he says you’ll be surprised by the main reason why his customers who outgrow their first concrete home choose to build another. “Although it seems like the most ambiguous of the reasons, most people build with concrete again because of how secure and comfortable they feel inside the house. They love the quiet.”
Insulating Concrete Forms
Of the many ways to build a concrete home, “Concrete block is the most popular method,” Niehoff says. “But ICFs are by far the fastest-growing segment.”
The Insulating Concrete Form Association in Glenview, Ill., reports there are more than 70 brands of ICFs in North America, each with some variations in design and materials. Basically, though, they are hollow blocks or panels made out of rigid foam insulation and welded steel. Once they are stacked in place, workers pour reinforced concrete into the center of the forms to produce a home’s walls. The forms are a permanent part of the wall assembly. The house can be built slab-on-grade or on a crawlspace.
“Houses built with ICFs aesthetically look like any other house on the block,” Niehoff says. They can be sided with most anything, including stucco, brick, fiber cement or vinyl.
And just like most other houses, the interior walls are covered with drywall. Pocock explains that the forms he uses have metal furring strips which are spaced about a foot apart and lie 3/8-inch below the foam. “You screw the wall board to that,” he says.
Allan R. Staker, a retired petroleum geologist turned developer who is currently building homes near Zion National Park in Utah, says when he first started his current project in Springdale he was using conventional 2-by-6s to create custom homes that look like national park structures built 75 years ago. But he was sending about a third of the wood back each shipment because it was substandard.
“That’s when we decided to make the switch to Arxx ICFs,” he says about the wall system that stacks up like LEGO building blocks. “We were skeptical at first. But we tried them and we liked them. They make an incredibly straight wall that is very sturdy. Everything we’re building now and in the future will be out of ICFs.”
Of all its fine qualities, Staker says, he likes concrete’s permanence. “Once you build with concrete, it’s there to stay. My homes will be around for 200 to 300 years.” In comparison, most builders agree today’s stick-built homes will last an average of 50 to 70 years without some kind of major renovation.
Cast-in-place has its place, too
Although ICF use is certainly on the rise, the building method isn’t for everybody. Pfanmiller says he saw ICFs nipping at the residential market, tried them and didn’t like them. “They didn’t fit our workforce,” he explains. He found a system made by Wall-Ties & Forms Inc., which basically consists of removable aluminum forms designed for above-grade applications, to be more in line with what his workers were used to.
Concrete houses constructed with these forms are built “one lift,” or a story, at a time on a slab-on-grade or an elevated slab. The forms are removed and then used again for the second lift, with the ceiling of the first lift also serving as the floor for the second. The exteriors are typically covered with brick, stucco or stone, and the interior walls are left a smooth concrete or plastered over for a textured look.
The forms are a major investment, Pfanmiller admits, costing a couple hundred thousand for the lot, but if you’re in the forming business much of the equipment and tools you already have can be adapted to this method of concrete home building. “There’s a difference between basement and housing forms,” he says, “but it’s the same technology.” And, like basement forms, the housing forms are designed to be used for many years to come. “I’ll wear out before the original set of forms wears out.”
The one thing that concrete home builders have to stay on top of more so than traditional home builders is planning, Pfanmiller warns. “We ask the homeowner the same questions, we just ask them earlier in the construction process” in matters concerning heating, electrical and plumbing components.
“One of the principal differences in our forming system as compared to ICFs is it allows us to pour walls and floors at the same time. This monolithic pour creates a tremendously strong structure with no joints or seams,” says Pfanmiller. “Its strength is second to none.”
Which is the driving factor for the concrete home demand along much of the East Coast. Pfanmiller says the six 3,060-square-foot concrete duplexes he built in North Topsail Beach each weigh more than 1 million pounds. “Imagine what kind of wind it would take to upset that structure,” he says. According to independent tests conducted by Texas Tech University, reinforced concrete homes can withstand 250 mph winds and projectiles traveling in excess of 100 mph. Thankfully, most hurricanes never reach that velocity.
Quality is the overriding factor
Jon S. Rufty of Rufty Homes Inc. in Cary, N.C., a builder who worked with Pfanmiller on his first concrete project three years ago, has since built a 10,000-square-foot cast-in-place beauty in Raleigh, among others. His reason for building concrete homes has little to do with the weather. “Storms are a minor reason,” says Rufty, who builds homes in the $1.5 to $4 million-plus range in the Research Triangle Park of North Carolina. “Our clients are looking for better quality and concrete homes are superior in construction. Whether you’re talking about energy efficiency, indoor air quality, safety or insurance rates, they’re just superior.”
David J. Davenport, AIA, of Davenport Architecture Design Inc. of Cary, who has worked with both Rufty and Pfanmiller on several occasions, agrees. “You cannot find a better, more durable material in the world than concrete,” he says. “It’s a wonderful liquid that can be made into any form that you want. From an architect’s perspective, I love concrete. It’s beautiful as an entity and limitless in what you can do with it. You can make it look like anything you want.”
From an environmental point of view, he says, “It’s a more energy-efficient way to build. The thermal performance of concrete homes surpasses anything you can build out of wood.”
As for its other attributes, Davenport says, “It’s an environmentally friendly, incredibly green material.” The elements made to create concrete are very plentiful and renewable. Concrete can be recycled. It contains no cellulose so it won’t support the growth of mold. There’s no off-gassing to affect indoor air quality and the product will practically last forever.
“That is a key element,” sums up Rich Warren, executive director of the Southern Nevada Concrete and Aggregates Association in Las Vegas. “Concrete’s sustainability. It not only lowers the life-cycle cost of the structure but it extends the life of a building, too. It’s a great concept to pass on to the generations to come. Let’s build better buildings.”
And now’s a good time to start.