How would you define slump?
According to the Tennessee Ready Mix Concrete Association, slump is a measurement of concrete’s workability, or fluidity.
It’s an indirect measurement of concrete’s quality, states Gabriel Ojeda, president of Fritz-Pak Corp. in Dallas.
And Joe Daczko, group manager of concrete technology for Degussa Admixtures Inc. (formerly Master Builders) in Cleveland, maintains it’s a measurement for consistency, both from a quality-control perspective and to determine how fluid or stiff a material is.
However you define it, though, the bottom line remains the same: Slump is a test for the rigidity of uncured concrete. Lower slump concrete is very stiff, and higher slump concrete is more fluid.
Most people in the business agree that a typical slump for ordinary decorative concrete applications would be in the 4- to 5-inch range, but there’s no hard-and-fast rule. “The slump should match the application,” says Daczko. “It could be anywhere from 1 to 10 inches depending on what you’re doing. If you’re paving a road, you need a much stiffer material that can stand on its own. If you’re doing a wall, the flow needs to be much more fluid.” And if you’re pouring a patio, it needs to be somewhere in between.
Sizing it up
Bob Harris, an industry leader and president of the Decorative Concrete Institute in Temple, Ga., says that although most decorative concrete contractors don’t conduct formal slump tests on the job, that doesn’t make using the proper slump any less important. “They need to understand the correlation [of slump] and how it affects the overall finish and structure of concrete,” he says.
Harris, who teaches concrete techniques across the country and beyond, likes to explain it this way to his students who are just getting started in the business: If you make grape Kool-Aid and it’s too strong, you add water. The new mixture isn’t as sweet and it’s not as deep a shade of purple. The same holds true for integrally colored concrete: If you change the slump by the addition of excess water, you change the makeup of the entire mixture as well as the intensity of the color.
“If you use excessive amounts of water, sometimes referred to as ‘water of convenience,’ it makes the concrete a lot more permeable,” Harris says. “It won’t stand up to the test of time in aggressive environments and to things like de-icing salts and certain chemicals that could attack the concrete.”
Basically, if you add too much water to your mix, it dilutes the cement paste and weakens the concrete mixture. The materials segregate, with the heavier aggregates sinking to the bottom, the sand staying in the middle and the cement floating to the top. “You end up with a cement-poor bottom and a cement-rich surface,” says Ojeda, adding that a weaker surface is prone to cracking due to cement’s inherent
shrinking qualities.
There’s a huge difference in adjusting the slump with chemicals rather than with water, Harris continues. By using water-reducing admixtures, you can change the slump without affecting the integrity of the concrete mix.
High-range water reducers, sometimes referred to as superplasticizers, increase the mix’s flow, improve workability, disperse the cement more evenly and allow you to reduce the amount of water in your mix by a certain percentage, making for a more durable product in the long run. It must be kept in mind that they work for a limited amount of time.
The use of admixtures
There is a wide range of admixtures that can be used to “fix the mix,” says Ojeda, whose company is well known for its handy Fritz-Paks that can be tossed into the ready-mix truck at the job site, bag and all. Fritz-Pak Corp.’s admixtures are designed to restore loads of concrete that might otherwise be rejected and to improve the performance of problem concrete by modifying its characteristics and enhancing workability.
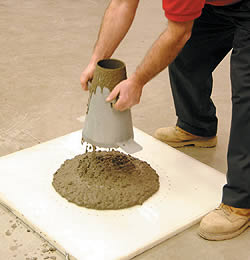
There are any number of reasons why you would use an admixture, all of which have to do with improving characteristics of the concrete. “To ensure the best finished project, contractors should work with their ready-mix supplier to develop a mix design before the concrete is delivered to the job site,” Daczko advises. “Besides adjusting slump, there are admixtures that can be used to slow down the set of concrete or accelerate it, improve the strength, control cracking, protect against freeze-thaw cycles and add coloring, just to name a few.” Some admixtures make the concrete temporarily more fluid, so colors added to the mix disperse much better.
Admixtures can often save the day, Ojeda points out, by increasing the slump without excessive water. They can fix concrete that is not quite what you ordered and they also can fill in when your crew is shorthanded or limited on the number of stamps.
Using a technique called step retardation, he says, you can discharge half the concrete and retard the other half. You can start stamping at one end and work from soft to medium to hard before getting to the next section that’s just starting to set. Again, you go from soft to medium to hard to get a consistent pattern.
Mike Costello, a regional manager with Dayton Superior, points out that admixtures have been around ever since they first started building concrete dams, but he marvels over the variety available today. “With the latest admixtures, you can have just about any slump you want. You just decide what you want your concrete to do and you can create a mix design to cause that to happen.”
Harris points out that not every job or application requires an admixture. But more contractors should be aware that help is there when they need it.