Are you asking why green matters? To answer that question, this article takes a look at the benefits that are encouraging property owners and designers to choose finished concrete floors instead of other floor coverings.
Going green saves the green
According to the U.S. Green Building Council, the fastest growing sector in green building is schools and universities. The demand for green schools is being driven by the climate crisis and the high cost of energy. A green school is typically designed to produce an annual operational cost savings of $100,000, but the net construction cost of building a green school is most often comparable to conventional building, or very minimally higher. The Web site Buildgreenschools.org reports that in addition to saving facility management and maintenance costs, creating a healthy indoor environment has been proven to reduce respiratory illnesses and absenteeism for students, teachers and school workers.
When Sherwood School District in Oregon hired Dull Olson Weekes Architects Inc. to expand a high school by remodeling the old building and designing a modern addition, the architects specified polished and colored concrete throughout the facility: in the lobby, entries, classrooms, corridors, commons areas, cafeteria, media rooms and every other feasible location. “During refurbishment old vinyl and carpet were removed to eliminate materials that outgas,” says the firm’s president, Norm Dull, AIA. “Several reasons were considered. Industrial-strength carpet cleaners and the treatments used in stripping and refurbishing vinyl contain noxious materials harmful to construction workers as well as maintenance crews and building occupants. Floor coverings wear out and require replacement in time, but concrete will last for the life of the building and provide an excellent life cycle cost.
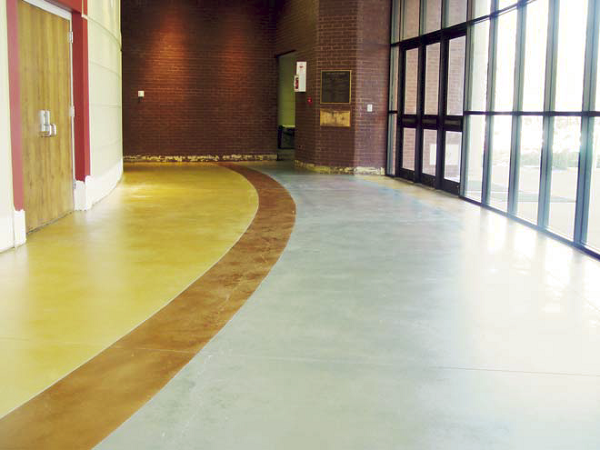
“Our firm specializes in LEED projects, and we enjoy the challenges of designing buildings that are cost- and energy-efficient to reduce the use of natural resources and provide a healthy learning environment,” he continues. “Indoor air quality is a very high priority for the Sherwood School District, and polished concrete is a good environmental choice. It also meets our criteria for appearance. We specified three colors in graphic block patterns, plus the light natural concrete color.”
Healthy buildings attract health-conscious tenants
The University of Calgary hired Kasian Architecture Interior Design and Planning to design a new four-story, 125,000-square-foot building with a child-care facility, clinic and offices for the Calgary Health Region. The design firm addressed LEED criteria by specifying light-colored polished concrete on the ground floor to increase reflectivity 30 percent in order to reduce lighting costs. They selected durable, abrasion-resistant RetroPlate to create high-performance floors with minimal maintenance for the Child Development Center and open-space public areas for events. This contributed to indoor environmental quality by eliminating the need for harsh chemicals and high-pH detergents, because the RetroPlate floor is easy to clean with only damp mopping. Appropriate for a facility dedicated to the well-being of children, the building achieved the highest LEED level of recognition, LEED Platinum, providing a high-profile symbol of the university’s commitment to sustainability.
Selling decorative concrete as a green alternative
A growing number of concrete contractors are addressing the demand for green building by developing their own educational programs to show architects and interior designers the ways concrete can be finished to provide a healthy building environment with good indoor air quality and low maintenance costs. Some contractors are promoting mixes that contain recycled materials, slag or fly ash that substitute for cement. Some have developed their own proprietary finishes for green building.
For example, Scott Truax of Middle Georgia Concrete Constructors Inc. and CSolutions says: “We do two to three lunchtime presentations per month promoting architectural concrete solutions, specifically surface-seeded concrete flooring. I have just recently been seeking out projects where terrazzo is specified and reached out to the designers to introduce them to our product line and educate them on the value it offers. We have taken it a step further and branded our finishes: Seascapes, Prism, Elements, and Reflections.”
The surface-seeded concrete flooring systems are 100 percent custom to each project. “We spend a considerable amount of time and money on sampling,” Truax says. “Our new office building that is currently under construction will include a 1,000-square-foot laboratory to accommodate the demand for samples.” Clients can see numerous examples of combinations of colored aggregates and glass on display in the CSolutions showroom. The company also produces samples specific to each job.
Why decorative concrete floors?
Concrete provides a healthy alternative to floor coverings because it contains no organic materials that can mold or mildew to contribute to sick building syndrome. Eliminating carpets that can harbor animal dander and dust mites is a good choice for people with asthma or allergies. Synthetic materials such as vinyl, carpet and composite woods outgas, even though low-emitting choices are available. The padding, adhesives and cleaning products associated with floor coverings are often noxious. Concrete has no harmful emissions and is produced from plentiful materials. Therefore, concrete offers an environmentally sound, safe, cost-competitive and durable flooring alternative for schools, universities, hospitals, recreation facilities, child-care centers and any place where healthy air quality is the top priority.
Versatility and durability
As an added attraction, decorative concrete offers a wide range of creative choices and colors. Using environmentally sound stains and sealers that have been introduced in the last few years, a skilled applicator can create an almost infinite number of looks, ranging from vivid, brightly colored graphics to earth-toned hues with subtle variations. Even stenciled graphics can be added. Grinding and polishing colored or uncolored concrete can produce a monochromatic appearance that can rival terrazzo and granite when enhanced with aggregates and glass during construction. The long-term durability of polished concrete has been tested and proven in shopping centers and big-box retail locations. Contractors can combine all of the above creatively to produce floors that meet the demands for green building beautifully.
Is green building a fad?
I asked Keith Parker, an architect who is studying to become a LEED Accredited Professional, whether green building is a fad or the direction of the future. “LEED certification is certainly not a fad,” he replied. “On the contrary, in the commercial sector, it is quickly becoming the norm. Most new commercial construction is LEED precertified, and by the end of the lease for most of our commercial interior clients, basic LEED certification will be commonplace and affordable. Additionally, several current requirements to obtain LEED certification are already transitioning to legislation. As additional LEED-certified requirements are implemented, the construction industry will see mandates become routine.”
At Acquilano Leslie Inc., Parker tells clients interested in following LEED criteria to expect a 2 percent to 3 percent increase in initial construction costs, including soft costs. “However, the gain from these upfront costs results in, among other things, lower operating expenses and improved indoor air quality, which directly affects increased productivity and decreased absenteeism,” he says.
“Ultimately, green building results in a better workplace which, in today’s environmentally conscious society, helps to attract employees who are aware of terms like ‘carbon footprint’ and ‘good corporate citizenship.’