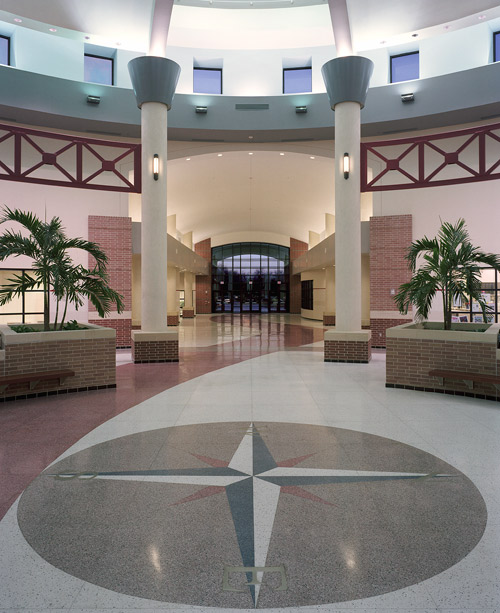
Industry experts predict that the demand for environmentally friendly, “green” building materials and methods will be the most significant driver in construction growth for the next five years and in the foreseeable future. According to the research, that’s good news for the concrete industry and decorative concrete contractors. Generally, concrete is now perceived as a sustainable and green building material. However, some of the reasons for the increased demand from property owners are a bit different from what contractors may think.
Both end users and contractors agree that the durability and aesthetic versatility of concrete are fundamentally important. However, according to recent industry surveys, other factors are stimulating demand even more.
The Green Matters Conference brought together industry experts in February to explore these factors and take a look at the role architectural and decorative concrete is playing in solving environmental problems. Speakers offered seminars and panel discussions on key issues in San Antonio, Texas, in conjunction with the 2012 Concrete Decor Show.
Some topics head the list of problems that architects, engineers and property owners strive to address: high operational costs in buildings, the heat island effect outdoors, environmental air quality inside and out, life-cycle cost reduction, and safety and resilience during natural disasters or security threats. Many of the speakers touched on these topics and the ways that decorative concrete professionals can promote concrete as a solution for these problems.
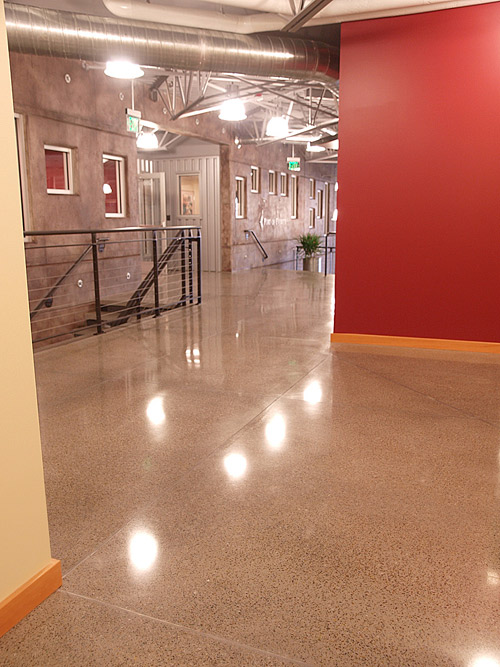
A growing demand for solutions
David D. Shepherd, director of sustainable development for the Portland Cement Association, shared some dramatic projections about the growing market for green building and important trends to watch during his opening address at the Green Matters Conference. He showed statistics demonstrating that green building demand increased between 2008 and 2010, while other types of construction declined. Contractor revenues from green building grew a startling 50 percent in that period according to McGraw-Hill’s independent research, he said, while at the same time total construction revenues declined 14.1 percent. During 2011 the U.S. Green Building Council reported 33,000 applications for LEED certification in the pipeline, plus 11,746 LEED-NC Certified Projects approved for new construction, with indications these numbers will continue to increase. At the same time, LEED has influenced perceptions beyond specified projects, he said, so that four to five times as many projects are adopting green building approaches as are actually pursuing the USGBC LEED certification.
On another front, the National Association of Home Builders reported a major shift into the area of green remodeling. A 2012 study of market opportunities produced by McGraw-Hill Construction, in conjunction with the NAHB and Waste Management Inc., predicted a five-fold increase in green construction in the residential sector and an even more impressive 150 percent increase in green remodeling in the next five years.
Shepherd also observed that in the commercial market, a building with green certification is worth much more than one without. One reason, he thinks, is the preference of tenants to lease within a green building, while another is the quantifiable reduction in operational costs. Concrete use can reduce energy expenses because its thermal properties and light reflectivity can deliver dramatic improvements in reduced energy use for interior and exterior lighting. Both concrete polishing and light-colored coatings can improve light reflectivity of floor surfaces by 60 to 70 percent, allowing the specification of fewer fixtures to achieve the necessary illumination while requiring less energy use in a commercial or retail environment. Big-box retail outlets have proven this value, and other commercial buildings are following their lead.
Elsewhere at the Conference, Larry Rowland, manager of marketing and technical services for Lehigh Cement Co., presented a seminar titled “A Concrete Solution to Green Building” that took a more detailed look at how concrete solves environmental problems. He stated that increasing reflectivity by using light-colored interior floors can potentially produce energy savings of 20 percent for the property owner. That amounts to significant operating-cost savings over the life of the building.
Rowland also shared data from a report titled “Attitudes and Perceptions: Decorative Concrete,” published by the Portland Cement Association in 2011. The research study showed that for decision makers, reducing the cost of materials is the number one factor they consider. Decorative concrete provides an opportunity to eliminate the cost of other floor coverings, such as carpeting, polyvinyl, laminates, wood and other wear surfaces that require replacement several times over the life of a building. This is most noticeable in high-traffic public, commercial and retail buildings, but homeowners increasingly recognize these benefits, also.
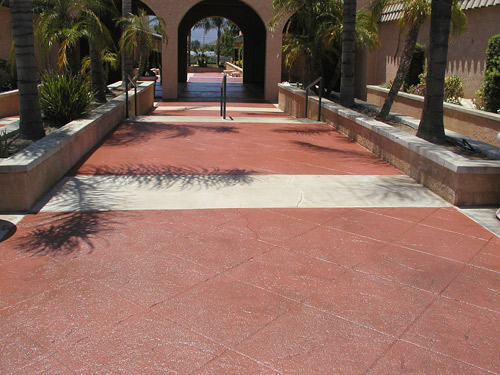
“Using IRR coatings for example, can greatly reduce surface temperatures by up to 50 degrees,” he said. “Experts say that we can solve global warming by painting everything white. We could gain up to 15 degrees Fahrenheit reduction if everything was white. But most of us are not ready for that white heaven yet. We still want colors. Great! No problem, just use an IRR coating that performs like white while still imparting color. Selecting ecofriendly products such as IRR coatings makes a contribution to the overall health of our planet and living environment. Oh, and by the way, it feels better to the touch and lasts longer.”
Heat islands are areas significantly hotter than their surroundings, and urban heat islands (UHI) have resulted from the use of building materials and dark colors that absorb and retain heat. As heat increases, VOCs and nitrous oxides in the air can trigger dangerous ozone buildup and smog as well as require even more energy consumption to cool buildings.
Substituting infrared reflective materials or treatments that reflect sunlight and absorb less heat can help to mitigate heat island effect in cities and qualify for LEED credits.
Trade-offs and misunderstandings
Undoubtedly there are many more issues to address. While there are many benefits to the increasing demand for green building solutions, some problems were also identified. One of the most challenging topics is producing acceptable concrete with a low carbon footprint when variables impacting performance are not properly accounted for in untested green mix designs.
Ward Malisch, technical director for the American Society of Concrete Contractors, presented a seminar called “Green Concrete Effects on Concrete Contractors” to help contractors talk sense about green mix design and long-term durability issues. He said: “One of the most prevalent misunderstandings is the belief that because some concrete producers can supply concrete with very low portland cement content (say, 200 pounds per cubic yard), acceptable setting times and early strength-gain characteristics, all concrete producers can do it. This is a fallacy. Concrete producer demographics affect the availability of supplementary cementitious materials and the environment in which the concrete will be placed.” The type of placement — foundation, wall, column, slab — also affects the setting time and early-strength gain needed, he noted.
Chris Sullivan, vice president of sales and marketing for ChemSystems Inc. presented a seminar on “The Vocabulary of LEED.” He discussed another common misperception with Concrete Decor. “Often the green movement has driven companies and agencies to force waste and recycled materials into a system that cannot or will not accept them,” he says. “Case in point is the ongoing debate on fly ash content in concrete. How much is enough, and to what final outcome?” The same goes for ecofriendly stains that utilize sustainable natural-based oils but have a high failure rate based on incompatibility to concrete or difficult application procedures, he says.
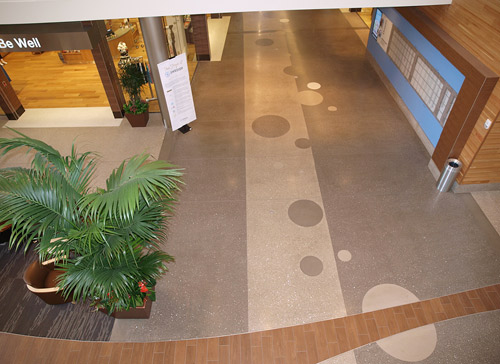