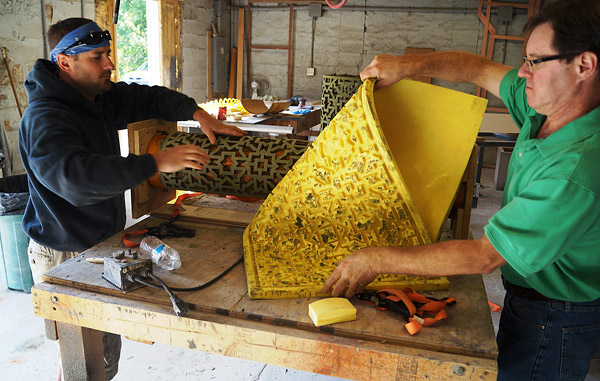
Most people don’t think of concrete as being bendable but it is, even in its hardened state. That said, bending and warping concrete is more manageable while it is still in its plastic state. Part of the appeal of warping concrete is the cool factor, and the other part is the time and labor savings. In the case of warping concrete versus casting in 3-D forms the appeal is big-time cost savings.
The forms
Polyurethane rubber forms are so useful they might have been invented for warping concrete. Rubber forms are easy to make, very flexible (depending on the durometer of rubber used) and very durable. I like Poly 74-45 rubber from Polytek Development Corp. for rubber molds with gradual bends and no undercuts, and the Poly 74-20 (which is a bit softer) for forms with very tight bends and lots of detail such as the lattice pieces shown in the photos.
I make my masters for casting the rubber molds out of medium-density fiberboard plywood. MDF lacks any grain structure, making it easy to machine or sand. Coat the raw MDF with lacquer to seal it. Then prior to casting the rubber, apply a couple of coats of Johnson’s paste wax and buff it out. Give the rubber a day to cure and you’re ready to cast. Your forms can last for hundreds of castings if you treat them carefully.
The mix
Let’s look at casting GFRC without a face coat and with no fiber showing. The majority of smaller fabricators and a growing number of larger GFRC manufacturers are using premix GFRC techniques. With a premix technique, a face coat with no fiber is sprayed on or sprayed onto the form, and a back coat with fiber is either hand-applied or sprayed onto the form. In spray-up techniques, a face coat with no fibers is sprayed on the form and the glass fiber is cut by a roving chopping gun and mixed with the mortar stream to form the back coat.
Both techniques use a face coat with no fibers, but we have taken premix techniques a step further and eliminated the face coat. Here’s an explanation of why and how it works:
Everything has a specific gravity. This measurement is how much a given volume of something weighs when compared to a given volume of water. Water has a specific gravity of 1, while steel, for instance, has a specific gravity of about 7.8 (depending on the grade). This means a given volume of steel weights 7.8 times as much as the same volume of water. When you drop a chunk of steel in water, the steel sinks.
When you blend items with different specific gravities, they are going to split up (segregate) into different layers if the mixing medium allows it to happen. Make your mix too fluid, with either too much water or too much plasticizer, and you’ll get separate layers. You can take advantage of this by allowing it to happen very slightly and under controlled conditions.
The materials in your mix have different specific gravities. Cement is 3.15, sands are generally around 2.62, water is the standard at 1 and most pozzolans are about 2.5. The good news is glass fiber has a specific gravity of 2.5. This means glass fiber won’t remain on the face of your casting if the conditions are right.
In a very fluid mix, the cement settles to the bottom, the sand settles on top of the cement, the glass fiber and pozzolans (about the same specific gravity) are next and the water layer is on top. Obviously we don’t want complete segregation in a mix or the resultant concrete would be very weak.
Your task is to allow the glass fiber to migrate off the face ever so slightly without the mix segregating. You can do this by adding Trinic Plasticizer to make the mix more fluid, vibrating the mix slightly or by using a combination of both. The glass fiber will still be visible if you grind the piece, but you’ll have a hard time seeing any fiber if you skip the polish.
This also is an excellent technique to use when casting concrete tile or wall panels. I call it ‘dump and done.’ The time-savings over a sprayed-up face coat and hand-laid back coat are considerable.
When Trinic had our admixture independently tested, we made the sample coupons using this technique. The results showed that the self-consolidating GFRC mix proportioned with Trinic’s GFRC Admix and Plasticizer have strengths equal to a premixed GFRC blend that’s hand-laid and rolled for compaction. This opens a whole new world of opportunities for GFRC manufacturers.
When to bend
When you bend concrete in the plastic state you are breaking the bonds of the initial set before it’s too late for them to heal. Bend too soon and the concrete will slump. Bend too late and it will crack. Bend at just the right time and it will take the bend without showing any ill effects.
As concrete enters its initial set, it begins to move from a plastic state into a hardened state. The window for bending normal non-accelerated portland cement-based concrete will last about 15 minutes on a 90-degree Fahrenheit day and longer on a 60-degree day. The problem is the “bendable window” may take an hour or more to occur on a 90-degree day, up to perhaps three hours on a 60-degree day.
In order to speed things along we replace a portion of the portland cement with CSA cement. CSA cement, or calcium sulphoaluminate cement, sets much faster than the ordinary portland variety. How much you replace depends on batch and ambient temperatures. A 20 percent replacement in an 80-degree shop will have you warping about 15 minutes after casting. A 40 percent replacement may be required for the same performance in a 50-degree shop. Make small samples to evaluate set times or you may find yourself with a batch that goes hot and begins to set while you’re mixing it.
To see if your concrete is ready to bend, lift the edge of your form slightly and watch for slumping. I like to bend as soon as the concrete will hold rather than risking cracks. Cover your concrete with plastic once you’ve got it warped to prevent moisture loss during curing. You may be able to strip your piece on the same day it was cast when using a portland-CSA blend.
Mix Design For Bendable Concrete
The following mix makes about 1 cubic foot — enough to cast 16 square feet at 3/4-inch thick.
62 pounds cementitious ingredients
You can mix portland cement with CSA cement.
Start with 80 percent portland, 20 percent CSA and work in more CSA as needed.
62 pounds sand
I like sand in the 30 to 50 mesh range.
40-50 blend works very well.
18 pounds water
This will give you a water-to-cementitious ratio of .29.
Don’t sweat it if you use a little more or a little less.
1.86 pounds Trinic GFRC Admix (3 percent of cementitious weight)
62 pounds cementitious multiplied by 3 percent = 1.86 pounds
0.31 to 0.62 pounds Trinic Plasticizer (0.5 percent to 1.0 percent of cementitious weight)
Start with 0.5 percent.
The finer the sand the more required to maintain fluidity. 3.72 pounds A R Glass Fiber (total dry weight of batch [124 pounds] multiplied by 3 percent)
200 bundle 1/2-inch or 3/4-inch will work fine.
Purchase pre-made molds for warping concrete:
www.ej3inc.com