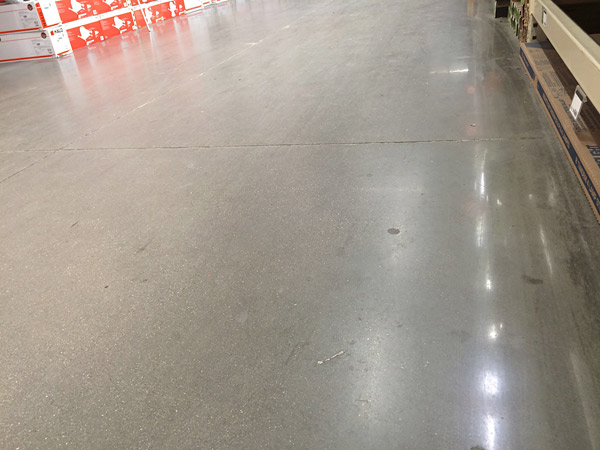
From huge industrial manufacturing plants and nationwide retail stores to restaurants and residences across the country, polished concrete has become a very popular flooring option over the last decade. Some say it’s grown too fast and now we’re beginning to experience growing pains as we learn more about this flooring alternative.
Polished concrete is very young in comparison to other popular mainstream flooring options such as carpet, engineered wood flooring, vinyl composition tiles and quarried stone. Whereas polished concrete has been used in the mainstream as a viable flooring system for only about 15 years, it’s still in the infancy stage as we discover what works and doesn’t work in different environments.
With concrete being the No. 1 building material in the world, it makes sense why polished concrete has taken off. Let’s not forget that polished concrete naturally and inherently contributes toward achieving certification for most types of construction projects under the LEED green building rating system developed by the U.S. Green Building Council.
Guarding against stains
By now most people are aware of the advantages of polished concrete compared to other flooring options. Some of the pros are high durability, low maintenance, cost effectiveness, long life span and endless design options. The biggest con would be that it can stain or chemically etch fairly easily if spills are not cleaned up in a timely manner.
To correct staining issues, one of the most popular options is to apply a coating. But a high-solids coating won’t adhere well to a polished concrete surface. Plus, a topical coating defeats the purpose of going to all the trouble of grinding, densifying, honing and polishing the concrete to achieve a highly durable and abrasive-resistant surface.
And then there’s moisture drive to consider. Since topical coatings are known to fail when there is moisture drive in a concrete slab, a semi-topical coating was developed for the polished concrete industry. Often referred to as a “guard,” this type of product is usually made of some combination of diluted densifier and acrylic/co-polymer in a water-based formula.
Guards or semi-topical coatings do a fairly good job at protecting the polished concrete slab from easily staining or etching. They also do a nice job of slightly filling in some of the micro pores and fissures in the surface. As a result, they give the already shiny polished concrete floor an additional bump in gloss after burnishing as well as enhance any dye or integral color if used. For these reasons semi-topical stain protection products took off rather quickly and became the norm for polished concrete surfaces.
Semi-topicals and the need to reapply
After about five years of using semi-topical stain protection products in high-traffic retail stores and industrial manufacturing plants, it became obvious this may not have been the best option for all environments with polished concrete floors. Foot and wheel traffic has proven over the years to be equivalent to about a 200- to 400-grit abrasive. Semi-topical coatings are nowhere near as abrasion resistant as the polished and densified concrete they are applied to, so they wear off rather quickly.
Because of this the frequency of the reapplication of the product is much more often than what floor owners were expecting. In some of the main aisles and entryways they are having to reapply the semi-topical protection products as often as every three months. In the lower traffic aisles and areas, they must reapply about every five months.
Many chemical manufacturers even developed specific cleaners that contained trace amounts of the co-polymers to help reapply the semi-topical sealer in an effort to prolong the inevitable reapplication of the guard products. Unfortunately, all the efforts were to no avail. Some national retailers have even considered going back to VCTs as the reapplication of the semi-topical sealer is not that far off from the old “strip and wax” game they used to play with them. Storeowners started asking for other ways to protect their polished concrete floors.
Advantages of penetrating sealers
Now comes the introduction — actually more like a re-introduction — of penetrating sealers. In the early stages of concrete polishing, companies used penetrating sealers borrowed from the natural stone industry. They provided decent stain repellency but the technology was designed more for granite, marble and travertine than concrete.
Although concrete has similar properties found in some reactive metamorphic natural stones such as marble, or sedimentary rocks like limestone and travertine, its crystalline structure and percentages of reactive properties can be very different.
With the advancement in technologies, there are now penetrating sealers that have the same hydrophobic and oil-phobic repellency properties as silane/siloxane sealers but without the airborne dangers that normally come with them. Silane/siloxane sealers are considered a carcinogen when they become airborne when atomized with a pump sprayer or from high-speed burnishing. Some of the new penetrating sealers are safe to atomize and burnish and they come in solvent- or water-based carriers.
When using a penetrating sealer, nothing like a “guard” or semi-topical sealer remains on the concrete surface. So foot and wheel traffic make contact with the polished, densified and hardened concrete surface rather than a softer acrylic, semi-penetrating guard product. Not only will the concrete wear better and longer than an acrylic guard, but now polishing abrasive maintenance pads can come in contact with the actual surface of the polished concrete. This allows the pads to do their job and keep the visual aesthetics, which are the specular gloss and DOI (Distinctness of Image) of the floor at an acceptable level within a given time frame.
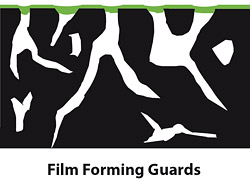
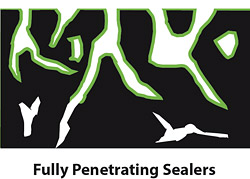
With the help of engineered cleaners chemically linked to penetrating sealers, you can now prolong reapplying the sealer to once a year in high-traffic environments. This is a substantial labor and material savings when compared to semi-topical products that must be reapplied every three months.
A winning combination
Contractors are a very valuable and necessary part of the evolution of our industry’s products because they love to play around with products and come up with their own systems. Thanks to some of them, we now have a combination or a “hybrid system.” Some of our customers discovered you can apply one coat of our semi-topical sealer (3D SP Stain Protector) then high-speed burnish, followed by a coat of our penetrating sealer (SR2) and high-speed burnish.
What happens is the first application of the water-based 3D SP is mostly penetrating. With only one coat, 3D SP mostly penetrates and fills the concrete’s small pores and fissures, enhancing the color and slightly bumping up the gloss and DOI. You really don’t get the topical aspect of a guard-type product until after a second application where it builds on top of the first application.
Next the SR2 penetrating sealer migrates in and around where the 3D SP semi-topical product is still breathable. Now the SR2 is protecting where a stain would have gotten in, yet remains breathable. With this combo you get the best of both worlds — color enhancing with gloss and an increased DOI from the semi-topical product, along with extreme hydrophobic and oil-phobic stain repellency that a penetrating sealer provides — all in one system.
With this system there is very little, if anything at all, to wear off the surface of the concrete so it can be used in medium to some higher-traffic environments. Maintenance on this system is similar to the penetrating sealer-only floor, typically involving an auto scrubber with the respective abrasive pad and the cleaner linked to the penetrating sealer.
A simple water absorption test will tell you when it’s time to reapply the two products again. If water penetrates easily, then it’s time to reapply this hybrid system. Once a year in medium-traffic environments should be sufficient.
It’s important to note the type of products and the order in which they go down. For example, Ameripolish’s water-based guard must go down before the solvent-based penetrating product. If you do it the other way around, the water-based guard will be repelled and you’ll wind up with a streaky and fisheye mess on the surface. Check with the manufacturer of each product to assure compatibility.
Maintenance weighs in
I feel it’s equally important to note that the abrasive pad used to maintain a polished concrete floor is just as crucial as the sealer used. For example, let’s take a polished concrete floor left at a 3,000-grit dry polish. If you maintain this floor with a 3,000-grit diamond-impregnated pad wet under an auto scrubber, you’ll take down the gloss and DOI in a couple of months.
Every diamond abrasive cuts more aggressively when used low-speed “wet” (like under an auto scrubber) compared to when it is used high-speed “dry” (like under a high-speed burnisher or a planetary grinder). So on this 3,000-grit level floor, it’s best to use a 6,000-grit or higher diamond-impregnated pad or a DOI pad under the auto scrubber.
You have to evaluate the volume of traffic in a given environment and recommend the proper sealer and maintenance program based off those parameters. For example:
High-wheeled traffic manufacturing plant or large distribution center (typically large square footage): These facilities usually involve a gray (non-colored) polished concrete floor up to 800 grit. This floor is best suited for a penetrating sealer and maintained with the respective abrasive pad using the proper supportive cleaner in the auto scrubber. Reapply sealer once a year, preferably late fall right before winter (mostly beneficial for Northern states).
Low foot-traffic retail store (typically small to medium square footage): This type of customer usually wants a highly polished, vibrant and multicolored decorative floor polished up to 3,000 grit. This floor and environment is best suited for a semi-penetrating sealer like a guard-type product that enhances the color and provides additional gloss and DOI after each reapplication. Maintenance involves periodic auto scrubbing with the respective abrasive pad using the proper supportive cleaner and occasional high-speed burnishing. Customers are usually OK with more frequent reapplications as they are more concerned with the floor’s aesthetics. With the low traffic, the reapplication in this environment should only be once a year.
Medium foot traffic and some wheeled cart traffic in a retail store (typically medium square footage): This customer is looking for that compromise between function and fashion and usually goes with a highly polished up to 1,500-grit, one-color floor. This might be a good candidate for the hybrid system mentioned earlier. With one application of the semi-topical sealer, you’ll enhance the color and slightly increase the gloss and DOI. Follow that with an application of the penetrating sealer and you’ll get the extreme hydrophobic and oil-phobic stain repellency. Maintenance will be with the respective abrasive pad and the proper supportive cleaner in the auto scrubber. Again, a once-a-year reapplication should be good but may require more if traffic is higher. Do a water absorption test to determine when.
Concrete polishing contractors who continually educate themselves are doing a much better job today at not only controlling the expectations of floor owners but also evaluating the environment to be polished. By suggesting the most logical level of gloss or DOI to stop at and the proper sealer and maintenance system for that specific floor, we’re starting to see much happier facility owners and will continue to grow the polished concrete industry.