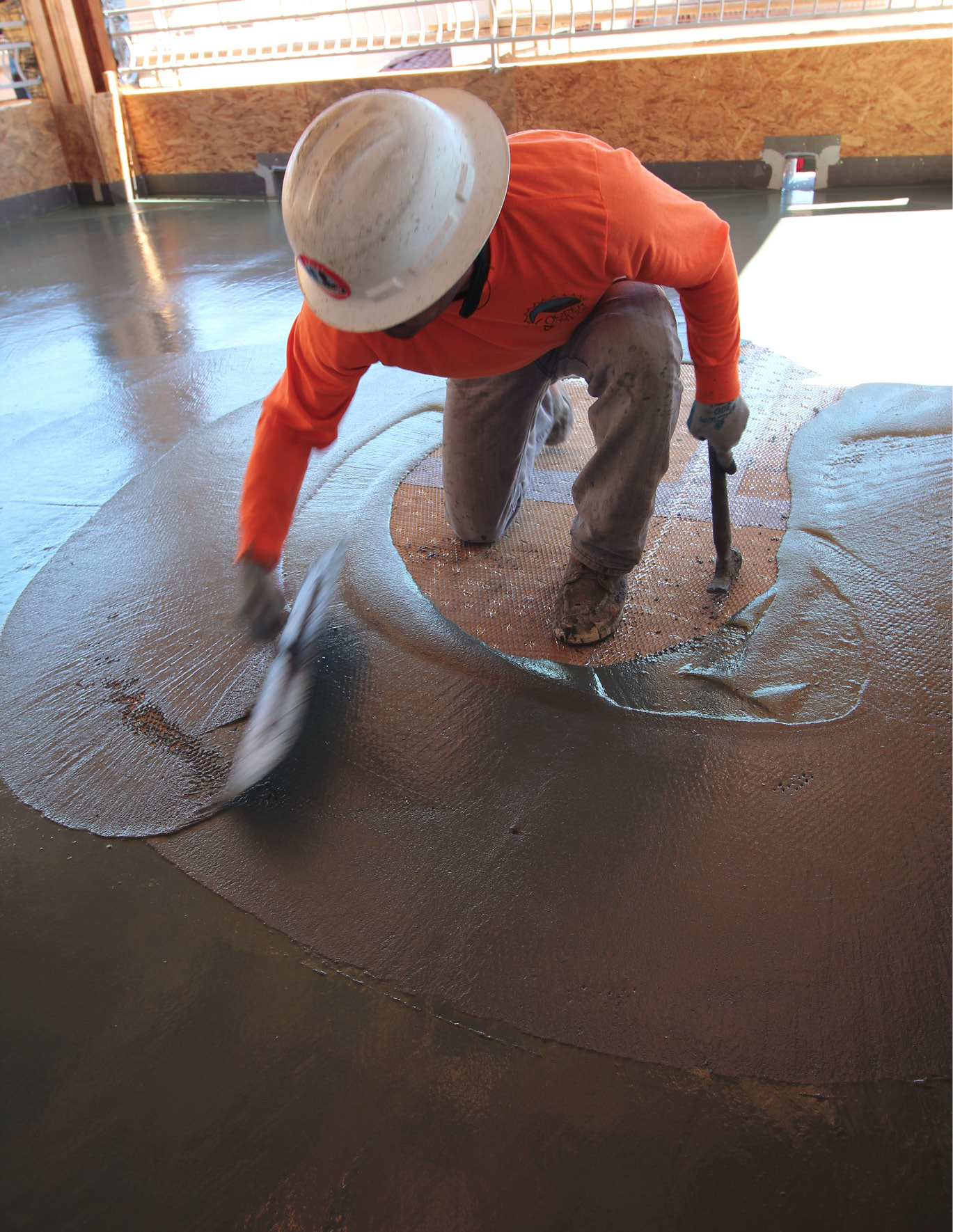
Whether the objective is keeping water in — like a pond, tank, pool or reservoir — or keeping it out — such as a foundation or entire building — waterproofing looms large in concrete installations.
For concrete contractors, designers and specifiers, the waterproofing facet of the project begins with deciding what’s best for the task. Making that call, of course, hinges on a working knowledge of the technologies and systems on the market — including the latest advances and newest arrivals to the marketplace. Concrete Decor looks at some of these systems in this two-part report.
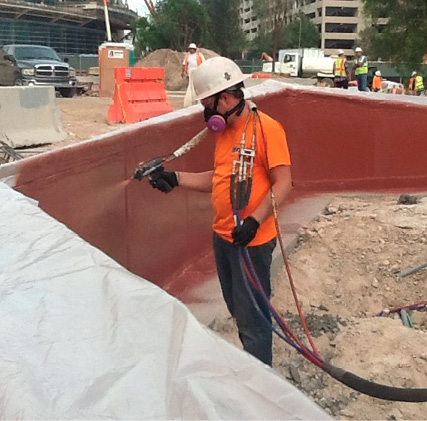
Shoring up a sieve
So, let’s say the objective is the former — keeping the water in. Such was the case for Redstone Arsenal, a sizeable U.S. Army base in Huntsville, Alabama.
The brass at Redstone had a decision to make: repair or scrap a working, 5-million-gallon water tank built in 1941. Though still structurally sound, the aging concrete tank had developed hundreds of cracks and leaks, and was losing water at a significant rate. The tank’s storage of treated water for potable use added to the expense hit the Army was taking.
Contracting and Materials, a specialty coatings contractor in Decatur, Alabama, was enlisted to shore up the tank. Redstone Arsenal had attempted a fix on several occasions, C&M notes, using a liner of one type or another.
The effectiveness of a polyurea waterproofing material on a smaller water-storage pond adjacent to the Redstone reservoir led to the decision to go with a similar approach — applying a polyurea coating. The product, VersaFlex 405, is approved for potable water in water temperatures up to 140 degrees F.
According to VersaFlex, the two-component, 100-percent solids, spray-applied waterproof coating creates a seamless, durable lining that prevents leaks and actually strengthens the integrity of the storage structure. The coating also can withstand freeze-thaw cycling and wide temperature variations for the long term, is very flexible and is capable of bridging cracks.
The company’s aromatic polyurea products are formulated for the heavy-duty, industrial segment of the market such as water tanks, secondary containment, transportation/infrastructure, water and power, and other demanding environments.
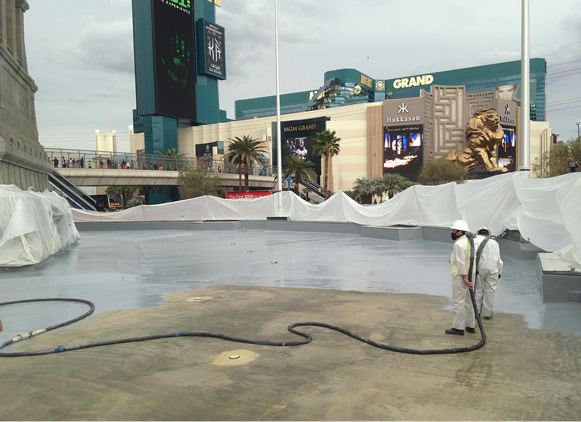
Reflecting pools in Vegas
GelFlex, another polyurea waterproofing product in VersaFlex’s portfolio, is geared more toward decorative concrete projects such as reflecting pools and others with water features. Based on aliphatic polyurea chemistry, the material has strong color-retention properties.
It was the polyurea system of choice for a reflecting pool at the New York-New York hotel/casino on the Las Vegas Strip. WaterFX, a builder and renovator of dramatic pools, spas, water features and thematic props, tackled the job.
The VersaFlex polyurea system beat out plaster, epoxy, tile and fiberglass as it proved to be a faster-turnaround alternative for reflecting-pool installations — one that delivers a spray-on waterproof, protective, seamless surface. A plaster-type material is typically used to line pools but applying it is time consuming and color consistency can be difficult.
Visually, the project’s dark topcoat makes the pool look much deeper than its safety-regulated 18 inches. Tim Singleton, WaterFX project manager, says the VersaFlex polyurea system offers a wide range of UV-stable topcoat colors that deliver “the look of multiple epoxy coatings in a single, seamless, durable waterproof topcoat without all the work and hassle.”
The GelFlex topcoat is an aliphatic, UV color-stable, 100 percent solids, chemical-resistant polyurea, typically applied over an aromatic polyurea basecoat that serves as the main waterproof membrane. The seamless basecoat creates a waterproof, durable protective liner that strengthens the integrity of the entire structure.
The polyurea materials’ physical properties include high elongation, crack bridging, hardness, tensile strength, and resistance to wide fluctuations in temperature and humidity. Thanks to quick setting and curing, the polyurea surface can be walked on in minutes, allowing projects to be returned to service a few hours after the topcoat is applied. The topcoat delivers color stability, gloss and distinctness of image.
A plural-component spray gun connected to a long, heated hose and pump machine is used to spray the polyurea basecoat and topcoat. The polyurea components are mixed in the spray-gun nozzle during application, with no pre-mixing needed and no waste produced in the process.
“The polyurea topcoat can customize the design and color of swimming and decorative pools, ponds, fountains, water walls, waterfalls and water features,” Singleton says. “It is fun, for instance, to match the bright colors of kids’ water-toy structures with complementary designs and colors in pools.”
Singleton says WaterFX initially checked out polyurea materials about six years ago, but back then designers and owners were largely unfamiliar with these products in waterproofing applications and were hesitant to try them out. That has changed as polyureas have been used in other infrastructure and building applications.

In a decorative project such as the New York-New York reflecting pool, Singleton says installation began with thoroughly cleaning and inspecting the concrete substrate, and patching cracks 1/8 inch or wider with a polyurethane repair material — Sikaflex 1a in this case. Then the system primer — VersaFlex VF 20 modified urethane — was spray applied in a thin mist coat and rolled with a short-nap roller to enhance penetration. The surface was covered to prevent any moisture, debris or other contamination prior to applying the waterproofing basecoat the following day.
The basecoat — the primary waterproofing membrane — was spray applied at approximately 60 mils, using VersaFlex FSS 45 aromatic polyurea. Due to rapid cure of the polyurea basecoat, the decorative polyurea topcoat was immediately applied. The topcoat — in this case VersaFlex GelFlex 115 aliphatic polyurea — was applied at 20 mils dry film thickness.
To ensure proper adhesion, the primer shouldn’t cure more than 24 hours before recoating with the basecoat, Singleton says.
Compared to waterproofing systems that combine a rubberized coating and fabric membrane, the polyurea system is “harder to get wrong” because of the seamless membrane that’s created, Singleton says. He adds, however, the substrate surface must be completely dry and free from all dirt, debris and moisture or imperfections can form in the membrane. During application, any moisture on the surface will convert to vapor due to the applied polyurea’s heat. It will be trapped under the coating, causing blisters or bubbles.
Singleton says use of the polyurea waterproofing is beginning to draw broader appeal as designers and specifiers gain familiarity with its use in other facets of construction, such as infrastructure and wall reinforcement.
Big-game assignment for cold-applied material
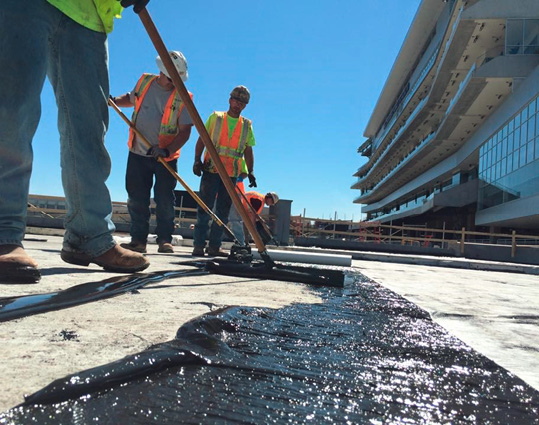
Turning to the matter of keeping water out, W.R. Meadows is looking to drum up interest in its Hyrdralastic 836, a cold-applied, solvent-free, one-component, low-VOC material that stands up to temperature extremes. Uses include interior and exterior concrete surfaces in horizontal and vertical applications such as plaza decks, planter boxes and parapets, and for positive-side waterproofing for foundations and between slabs.
A big-game test for this new player in the waterproofing arena came at the new Vanier Family Football Complex at Kansas State University’s Bill Snyder Family Stadium in Manhattan, Kansas.
Topeka, Kansas-based Restoration & Waterproofing Contractors Inc., the waterproofing subcontractor for the Vanier complex, looked for an equivalent alternative to the hot-applied sealant in the architect’s specifications, citing safety concerns.
The subcontractor’s job primarily focused on 50,000 square feet of split-slab waterproofing for the concourse area. The process involved applying a 90-mil coat of the Hydralastic 836, followed by placing reinforcing fabric and another 90-mil coat of the cold-applied waterproofing.
Also used in the project were W.R. Meadows’ Mel-Rol waterproofing membrane for below-grade applications such as elevator pits and the hydrotherapy pool area, Sealmastic solvent to reduce dampness and moisture infiltration, and BEM one-component waterproofing membrane for sealing around conduits, rebar and brackets.
Russ Snow, W.R. Meadows product group manager for building envelopes, says Hydralastic’s key features, besides its cold-applied characteristic, is that it can be applied to green concrete and asphalt, and it doesn’t require any special application equipment.