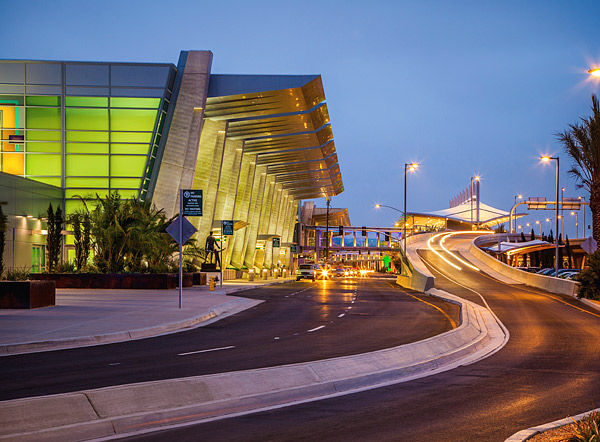
Expanding Terminal 2 at the San Diego International Airport was the largest improvement project in the airport’s 81-year history. The expansion — dubbed “The Green Build” because of the airport authority’s commitment to sustainability and environmentally friendly materials and methods — cost $907 million and at peak construction created 1,000 jobs.
All told, 7,000 workers had a role in the project, which was completed on time and under budget. And some of those workers produced architectural and decorative concrete, which was utilized throughout the expanded terminal.
Two major contracts were awarded for the massive undertaking:
- A design-build joint venture between Turner Construction Co., PCL Construction Services Inc. and Flatiron Corp. oversaw the addition of the three-story Terminal 2 building. It featured 10 massive architectural concrete columns, 10 new gates, and improvements to the runway side of the new terminal in the way of 1.5 million square feet of new taxiway and aircraft parking.
- The Kiewit/Sundt design-build team was responsible for the land-side improvements for the Terminal 2 expansion. These included decorative concrete walkways, accessories and landscaping, a new dual-level roadway across from the terminal that separates arriving from departing traffic, two curbside pavilions in front of the terminal for passenger check-in, enhanced vehicle parking, two pedestrian bridges, six roadway bridges and the nation’s largest USO Center, among other improvements.
Work began in July 2009 and the terminal officially opened August 13, 2013. The results have received national attention. The San Diego airport placed second in the Architectural Concrete, Over 5,000 square foot category in the sixth annual Decorative Concrete Awards competition sponsored in 2014 by the American Society of Concrete Contractors Decorative Concrete Council.
Architectural concrete provides support
Architects and general contractors involved with the expansion project used the term “architectural concrete” to describe the exposed columns that adorn the front of the terminal and also serve as structural elements, as well as the stained, integrally colored and saw-cut flatwork in front of the building. The curved walls, benches, planters, bollards and trash receptacles also were considered both architectural and decorative concrete. For many, the terms are interchangeable.
According to the American Institute of Architects, cast-in-place architectural concrete is “formed concrete that is exposed to view on surfaces of (the) completed structure or building and that requires special concrete materials, formwork, placement or finishes to obtain (the) specified architectural appearance.”
Architectural concrete’s key attribute is that it is an exposed concrete surface with some kind of aesthetic consideration. It can be gray, white or colored and still fit the definition used by many in the construction field.
The massive inclined columns, a significant feature of the expanded terminal building, duplicate those found on Terminal 2 East that opened to passengers in 1998.
Although it may not be obvious at first glance, “The 54-foot-tall columns were designed to look like airplane wings,” says Ron Vollmond, formwork operations manager for Anaheim, California-based Bomel Construction Co., who was tasked with coordinating and designing the formwork using EFCO steel forms. The columns were poured in three lifts and on a seven-day cycle.
“Because of the sheer mass of these columns, there were many challenges,” and consequently extensive mock-ups and trials, says PCL’s Jeff McDonald, who oversaw the terminal project from preconstruction through turnover as the general superintendent for the Turner/PCL/Flatiron joint venture.
The hardest part of the job involving the columns, Vollmond says, was “getting the mix design, slump and vibration just right for aesthetics and constructability purposes.”
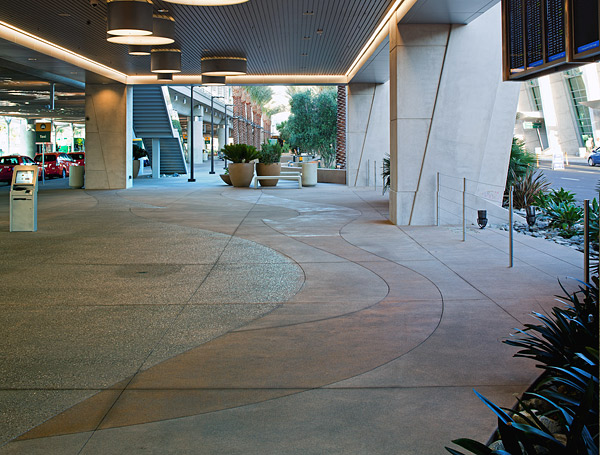
In short, the job required a high level of quality concrete with a complicated consistency because the new columns had to match what was already done years ago.
And that, says McDonald, was a big part of the challenge. “The quality of the existing columns was less than desirable. So it was a bit of a struggle to bring up the quality of the new ones without making them look totally different.”
The crew went through dozens of small mock-ups, everything from 4-foot-square flats to 2-by-2 columns 16 feet tall, as well as two large mock-ups of 6-by-8 15-foot columns, before landing on the right consolidation and vibration procedure to produce the desired color and texture.
“The placing and consolidation (of the mix) are critical to the exterior finish because different methodologies, procedures and materials affect the color,” says McDonald. If the mix was not consolidated adequately, there would be voids in the concrete. If it was vibrated too much, there were dark stains from excessive water. Too little and there was material separation.
“We ended up using a reputable outside expert for our mix design,” McDonald says, “which helped us to determine the best aggregate sizes with the Type III portland cement and color additives. Originally we were trying to make a structural mix work (for the architectural concrete) and it wasn’t cutting it.”
These columns presented a challenge that stands out over the 40 years McDonald has been involved with concrete “We did everything exactly the same as much as possible (when making the columns),” he says. Besides strictly controlling the mix and blending concrete truckloads, they used the same people, equipment and schedule. In addition to the mix, the vibration sequence, as well as its timing and force, was critical to maintain uniformity in color, consistency and consolidation.
The inclined columns at the airport were colored as cast, as is the case for most architectural concrete on today’s buildings. Once the metal forms were removed there was no dry sacking or painting. Except for a little touch-up to minor imperfections, the columns were finished. “The finish is a little industrial-looking,” says McDonald.
On the land side: Decorative concrete
As a member of the Kiewit/Sundt design-build team, Patricia Trauth, principal landscape architect for the Southern California region for URS, helped design the landscape improvements throughout Terminal 2 West. The exterior area for arrivals and departures features waves of seeded Lithocrete, stained concrete, walkways finished to look like quarried stone and meandering concrete seat walls.
Rich Robertson, senior general superintendent for T.B. Penick & Sons Inc., San Diego, another member of the Kiewit/Sundt design-build team, was in charge of installing and finishing all the flatwork on the terminal’s land side, as well as the walls, stairwell and pedestrian bridges. He says he used a house-made reactive stain to further distinguish the saw-cut “kite tail” or “ribbon” design. The whole project, he adds, was integrally colored with Davis Colors’ Palomino.
“Concrete is a creative fluid substance that’s fun to add different materials to,” says Trauth, adding that T.B. Penick mocked up extensive samples using different aggregates for the airport project before the team decided on glass beads, pyrite and granite aggregate. Team members also decided they wanted to incorporate curved saw cuts into the overall design. “When you start doing this type of detailing to concrete, you need to have a good process and seasoned professionals to do the work.”
Seeded with the glass beads and pyrite, the curves not only look good but also serve a wayfinding purpose. “The seeded curves guide people to the right location by getting them from point A to B,” Trauth says. “People at the airport are in a hurry and many visitors are not familiar with the environment, so the seeded paths make it easy for them to understand where to go.”
For instance, one of the crosswalks has an aggregate wave going through it that swirls around and ends near the escalator that takes you upstairs to the departure area. Another area upstairs has a curve that leads to the pedestrian bridge that takes travelers into the terminal.
“When the sun hits the pyrite, it looks like waves of gold,” Trauth says. “The whole indoor/outdoor setting is designed to celebrate San Diego’s climate and proximity to the ocean.”
“This project has definitely changed people’s arrival and departure experiences from San Diego,” says Chris Klemaske, project developer with T.B. Penick, whose job was to work with architects and airport representatives about the concrete aspects of The Green Build. “I especially like the way it all comes together. The concrete is a piece of the design rather than the focus of it.”
Trauth praises the people involved with The Green Build as being among the best she’s ever worked with. “This project is definitely the highlight of my professional career.”
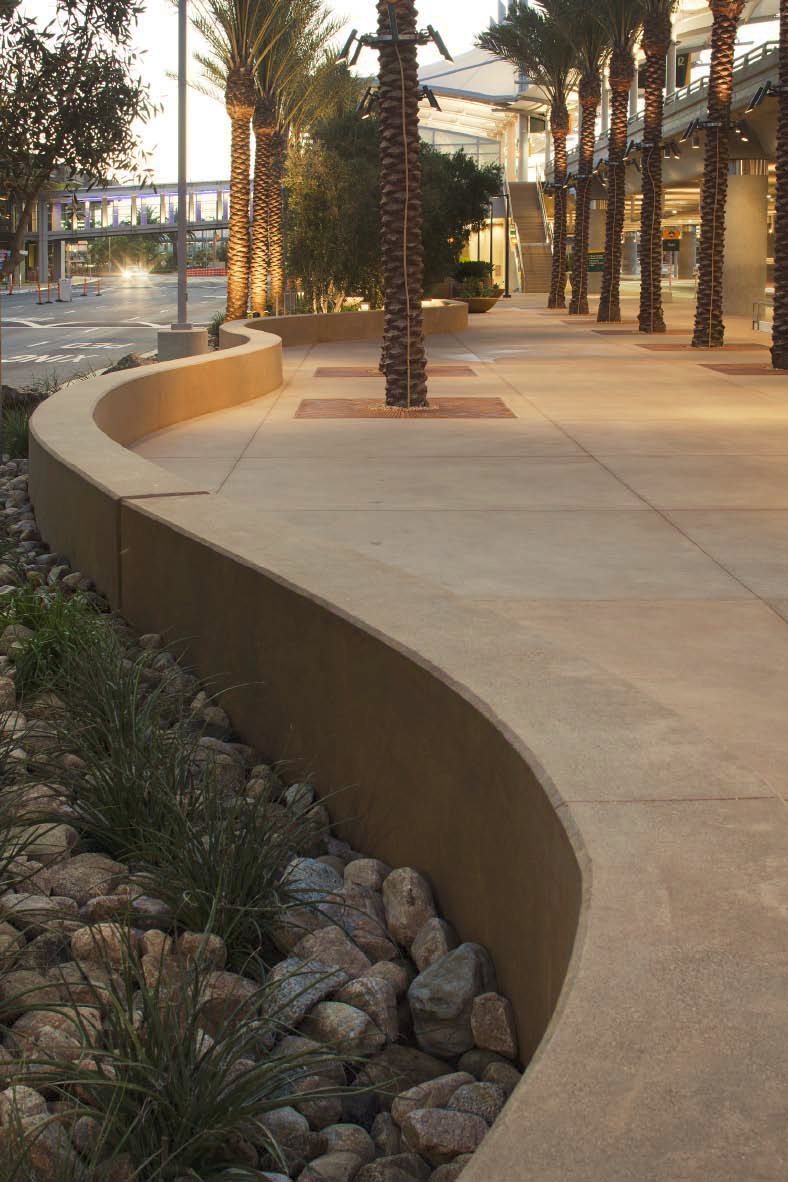
Terminal and perimeter
HNTB Corp., as part of the Turner/PCL/Flatiron joint venture, provided architectural and engineering services for the airport’s Terminal 2 West and air-side expansion, which consists of 460,000 square feet of new public and nonpublic areas. Thanks to extensive sustainable features, this part of the expansion recently qualified for the Leadership in Energy and Environmental Design (LEED) Platinum certification from the U.S. Green Building Council, making San Diego the first LEED Platinum-certified commercial airport terminal in the world.
Jennie Santoro, an HNTB architect who was part of the on-site design team, says, “Matching the existing building’s details (like the inclined columns) while at the same time bringing in new design to give the owners a better product than what they had before was a challenge.” That, she adds, and keeping the building operational during the construction process.
It was always in the plan to expand the existing L-shaped building with a mirrored L-shaped addition that would transform its shape into a T, she explains. “And it was part of our job to make sure that to a layperson the (expanded) building looked like it was built all at once.”
In addition to the building, Santoro’s design jurisdiction included the sidewalk area in front of the terminal, in which Trauth with URS also was involved. They were tasked with improving the terminal’s curbside appeal and selected decorative concrete flatwork and precast concrete accessories as the new design elements for the job.
“The airport authority wanted a design that promoted safety yet was warm and welcoming to visitors,” Santoro says. “So we came up with a creative solution that involved a variety of precast types of concrete furnishings as part of the terminal’s security and blast protection. Instead of just rows of bollards, we used (steel-reinforced) concrete benches and planters to break things up.” The bollards, she adds, were custom-made and lit at the base. And the planters allowed for some greenery to soften the hard lines.
The sidewalk was colored and saw-cut to break up its expanse and add another decorative element. “The bands of Lithocrete align with the inclined columns and follow the rhythm of the facade,” Santoro says.
Teamwork
The Green Build project was a huge success in many ways. Small and local businesses got a fair share of the pie thanks to the airport authority’s hiring policy. It was a win-win for the county and environment as the project’s sustainable practices involved building materials and methods. And Green Build’s design-build concept was backed by bona fide teamwork all the way around.
“The more knowledge everyone on the team had, the better the project went,” says T.B. Penick’s Klemaske. “Everyone involved felt part of the team. There was no finger-pointing. We all came to the table before it was built so we knew the challenges beforehand.”
That’s the trend for big projects nowadays, Klemaske says. Architects and contractors develop a relationship and agree on designs by sharing drawings, mock-ups and samples. “They meet regularly so they can build as a team and go in as a team,” she says. “It’s a smarter way to work and a money-saving way to work.”
Concrete facts about The Green Build
110,802 cubic yards of concrete were used to make improvements on both the land and air sides of the San Diego International Airport.
The terminal contains 20,000 cubic yards of concrete. The Green Build’s new airfield apron contains enough concrete to build a 5-foot-wide sidewalk from San Diego to San Francisco. That’s almost 500 miles!
54,000 tons of construction material waste from The Green Build was diverted from landfills, much of it recycled or used on site, including concrete that was recovered, crushed and used to make subfoundations.