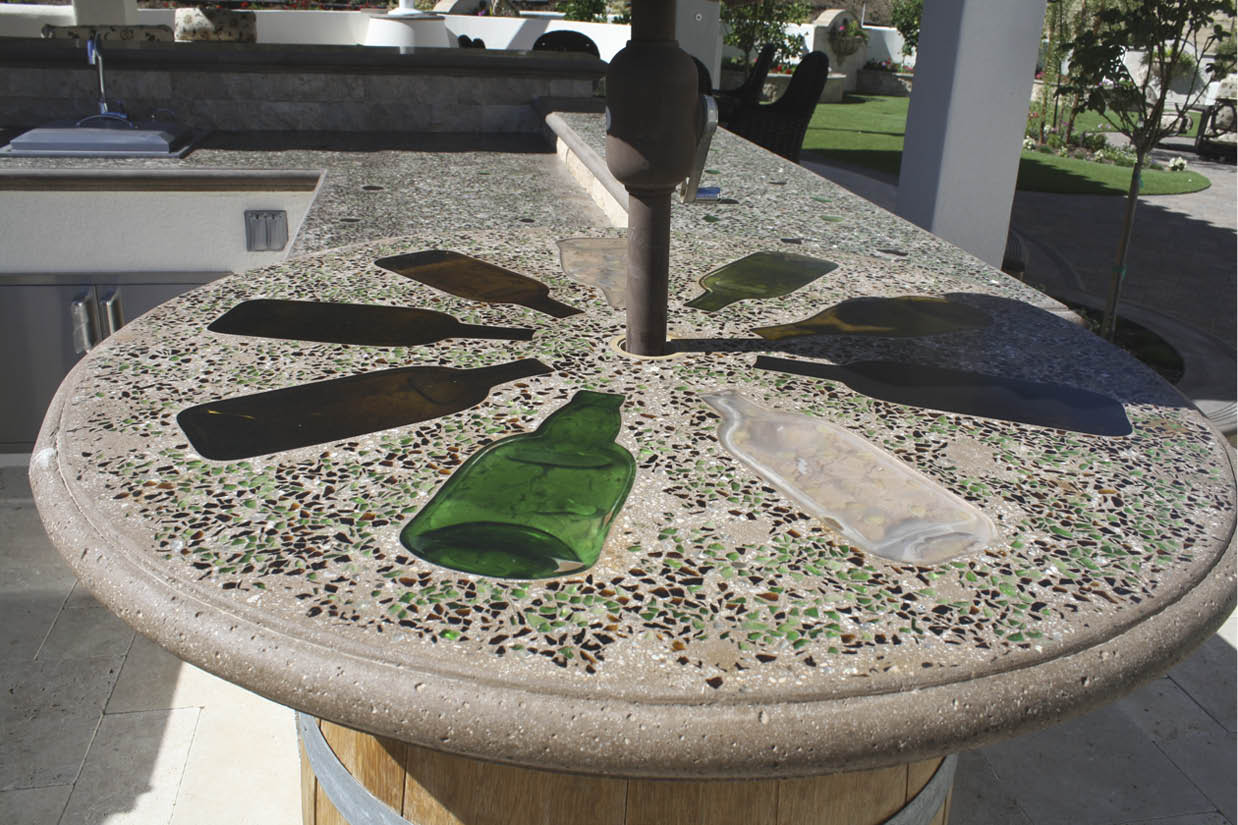
Scott Cohen, owner of Green Scene Landscaping & Pools in the Los Angeles area, has been designing and building concrete countertops for more than 20 years. He is one of the early innovators in the cast concrete counter arena and has experimented with hundreds of different embeds, with glass being one of his favorites.
“At Green Scene we like to incorporate recycled materials in the hardscape projects we build and using glass is an easy way to do that,” says the award-winning outdoor room designer and author of several landscape design and construction books. “It’s also a great way to create something special for the client.”
Glass is a fabulous way to introduce various colors, textures and even fiber-optic lighting, he says. Sometimes he even uses glass to incorporate a client’s hobby or interest.
Hitting the bottle
“I’ve done quite a few projects with melted bottles,” Cohen says, joking that it lets him write off his wine and scotch consumption as a legitimate business expense.
Cohen has a ceramic studio at his home where he can slump bottles and fuse glass in an electric kiln for specialty projects. “Slumping bottles correctly is the key. They get soft at about 1,400 degrees. At 1,500 degrees, they’ll melt flat,” he says. Bottles only need to “soak” in the 1,400-1,500 degree range for about five to 10 minutes or they’ll turn into “soup,” he cautions.
“If you try this at home, the cooling, or annealing, process is really important,” Cohen continues. “If glass cools too quickly, it gets brittle. It needs to be annealed properly, which means cooled slowly to relieve the stress.”
Over the years, Cohen has also tried many different types of recycled glass aggregates, including crushed beer bottles. “The amber glass really pops,” he says.
He often uses special order crushed pieces of recycled glass that have been flash-dipped in silver to get a reflective quality like an all-sided mirror. This way, he kids, he avoids the bad luck of breaking an actual mirror. The all-sided silver-coated pieces are about 10 times the cost of regular glass, so he just uses a smattering of it to bring a shimmer to outdoor projects when the sunlight hits it just so.
“I love an opportunity to be creative.”
Glass selections
Cohen typically uses glass aggregates sizes 1, 2 and 3 that he buys mostly from Heritage Glass and American Specialty Glass and often mixes in larger chunks of glass for emphasis. He slumps his own bottles.
He also uses the rounded jelly bean glass beads size 1 or smaller for tables, polished concrete, pool furniture and plastered swimming pool liners. “Everything we set we cast in place and hand seed. We build the forms on-site and vibrate the mold to consolidate the mix and then seed with the glass chunks,” Cohen says, adding he hasn’t had any issues with the smaller-sized jelly beans.
He or his crew then tamps in the glass with a wood float and goes over them with a steel trowel. After that step, Cohen lets the concrete cure for a week or so before grinding, honing and polishing the top with three-head polished and diamond-tipped heads.
Experience gets it right
But Cohen has had some issues with alkali-silica reaction when he’s used larger chunks of clear glass. “In my experience, clear glass is the most susceptible (to ASR),” Cohen says. “Large chunks have popped out a few times and have left an unsightly goo behind.” He gets around this problem by just avoiding them in his designs.
For contractors just getting into using glass in their projects, Cohen advises practicing on smaller stepping stone-size pieces about a foot square before taking on large projects. “It’s easy to push glass too deeply in some areas and when you go to polish there’s nothing there because it’s buried below the surface. The glass disappears on you,” he says.
“Be careful with your edging tools,” Cohen continues. “Work them gently and don’t worry so much about (protruding) glass because you’re going to hit it with a polisher later. Don’t overwork the concrete. Grinding will take care of the imperfections.”
As for color combinations, some clients want an approach that is clean and contemporary. Others want a more whimsical tactic. It’s pretty much a personal choice. “That’s why there are 31 flavors at the ice cream store,” Cohen says. “People like different things.”
Editor’s note: Scott Cohen has also written several books to help contractors with their project designs. These include “The Big Book on BBQ Plans” that illustrates 65 designs and also includes an outdoor kitchen design workbook that shows contractors how to cast countertops with glass embeds and fiber optics.
Looking for glass aggregate?
Offered by Concrete Decor StoreJewel Mix Landscape Glass
by American Specialty GlassEarthtone Mix Terrazzo Glass
by American Specialty Glass