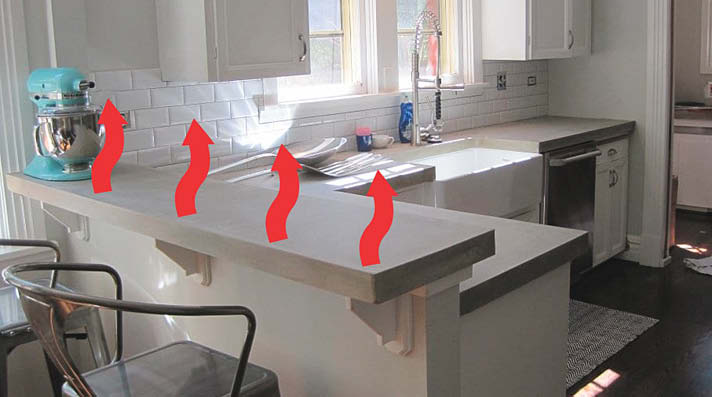
In the past five years, heated concrete countertops have become more popular and remodelers, contractors and renovators are faced with the task of how best to install them.
Historically, remodelers had to expend a great deal of preplanning, research, design and engineering to meet the requests of clients who wanted heated countertops. This subsequently made the feature expensive and limited to high-end homeowners and business owners.
But thanks to technology, installing temperature-controlled concrete countertops is no longer such a challenge.
Heating countertops history
Originally, contractors placed floor heating coils onto the countertop’s substrate, which was typically ¾-inch plywood. They had to predetermine the coils’ layout so they could be placed to uniformly warm the concrete. Using a router, contractors created channels in the substrate to accommodate connection wires for the buss system so that the thicker wires could rest below the surface of the plywood and not get compressed by the concrete.
Since the floor heating systems operate using a closed-loop thermal-control method, a temperature sensor was also mounted in the substrate and wired to a controller. Floor heating mats commonly draw a significant amount of power so a dedicated 120-volt 15/20-amp line from the breaker box was also required. This was especially challenging when renovating an existing home.
Complicating matters was that this process placed the responsibility of the heating solution onto the contractor. If the heating was installed in a way that resulted in the pad overheating or the approach introduced thermal stress points, the contractor often was liable to replace the concrete if it cracked or was damaged in some way.
Preparing and designing this heating solution commonly took four to eight hours.
Specially designed heating mats
In recent years, the solution has transitioned from floor heating coils to ultra-thin heating mats that were developed specifically for countertops. This completely changed the level of effort for renovators and installers.
These new heating mats, available from companies such as FeelsWarm and WarmlyYours, greatly reduce the contractor’s level of work. Installers just need to provide a sketch or print of the concrete countertop and identify the area of the surface where the heat is desired.
Technical breakthrough
The new generation of heating mats mainly provides a breakthrough in four ways:
1. The resistive coil is made with thin highly-ductile foil instead of thick round wire. With a foil thickness of 1.5 thousandths of an inch, the overall heating mat, including the encapsulated high-performance plastic films, is less than 25 thousandths of an inch.
Foil-based heaters with thin foil and resistive patterns as close as .100” widths and spacing provide very uniform and consistent thermal results.
This technology provides a very compliant material that can be compressed by hundreds of pounds. This thinness also enables the pads to be attached directly to the concrete under an overhang without the substrate extending to its edge. The thinness also makes the pad unnoticeable.
2. The mats can be custom produced to any shape or size to match the countertop and cabinet design. They are usually not sized for the entire counter. Rather, they are placed in specific selected areas — typically where people rest their arms.
The heating mats are produced in about a week.
3. The new style of heating pads operates on low voltage (12-24-volt DC), using household power transformers that plug into standard outlets.
For contractors, this means there’s no need for a dedicated power line. The heater can plug into an outlet that already exists in the island or countertop area. The maximum current draw for a large mat is 2 amps. Smaller mats draw less current.
4. The heating mats’ thermal control differs from floor heating. The heaters, when plugged into the outlet, deliver thermal output to raise the concrete to a peak temperature of skin temperature, about 95 degrees F — which translates into the surface no longer feeling cold.
The thermal rise amount is fixed and is designed into the heater at the factory. This eliminates the need for a sensor in a closed-loop control scheme. Rather, manufacturers provide a simple electronic controller that enables homeowners to decrease the temperature if they want a cooler surface.
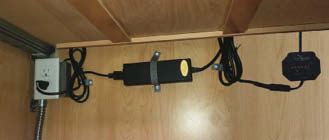
Because these new generation heaters are designed for aftermarket homeowner installation, as well as contractor installation, the approach is simple. Contractors just connect two cables and the unit is immediately operational. The cables are designed so that they can’t be connected incorrectly.
Three basic installation types
Despite a wide variety of custom countertop and cabinet designs, there are generally two basic approaches that concrete countertop heating pad manufacturers consider when designing the pad. There’s a third option for concrete counter fabricators who want to integrate the heater into the wet concrete.
1. No overhangs/full substrate: Contractors will find installing heating mats on concrete countertops with no overhangs, such as islands, to be extremely easy. In these applications, prefabricated concrete countertops rest on a substrate that covers the entire area where the concrete is placed. Heaters will be installed in a minute or two.
The only prep work for the installer is to drill a ¾-inch hole through the substrate into the cupboard where the outlet is located. A thin tail from the heater curls down into the hole so a bump or raised area isn’t created. The cord from this tail then plugs into the controller or transformer inside the cabinet.
The heater is then simply rolled out onto the substrate and its tail is fed down into the hole.
Next, the concrete can be placed directly on top of the heater. The heater’s material construction can handle the weight of the concrete without damage.
|
|
|
2. Overhangs and cabinets without substrates: For applications with overhangs, heating mats are manufactured with an additional protective layer and a pressure-sensitive adhesive tape on the back.
The heater is mounted onto the underside of the concrete and will remain permanently attached. These heater designs also provide a tight seal to prevent leaking into the body of the heater if something is spilled onto the countertop.
For heater installations with a countertop overhang, there are a few extra steps for the contractor.
The first step is to determine if the heater can be installed after the concrete is placed onto the cabinet or if the heater should be mounted onto the concrete prior to it being placed. Either way works.
A preparatory coating must be applied to the underside of the concrete countertop to enhance bonding. This coating seals the molecular surface and provides excellent adhesion for the heater. This coating is a two-part epoxy that’s brushed or rolled on and cures to a hard finish in 30-45 minutes.
The release liner is peeled off and the heater is attached to the concrete overhang about ½ inch away from the outer edges. To avoid wrinkles or large bubbles throughout the heater body, this area needs to be wiped. This can take between 30 seconds and five minutes depending upon the heater’s size and shape.
If the heater is attached after the concrete is on the cabinet or is an aftermarket installation, the heater may have cut-outs or unique shapes that accommodate corbels, supports or other cabinet features.
After the heater is installed, a ¾-inch hole is drilled into the cupboard under the overhang. The cord is fed into the hole and a small plug is attached around the wire for a professional look.
|
|
|
3. Embedding the heater into the concrete during the pour: A third option is to integrate the heating pad within the concrete as the top is being formed. The heating pads are made with materials that can withstand the acids, water content and other chemicals present in wet concrete. Some contractors elect to submerge the heating pad when the concrete is partially poured into the form, then cover the heater with additional wet concrete.
This approach requires a slightly modified heater that has the electrical cord well protected from the rigors of handling and chemistries.
Hookup and controller
The final steps to complete the heater installation for both an overhang and non-overhang application is to connect the electronics. This is a simple process. While the heater may be plugged directly into the low-voltage power supply, most customers prefer a controller so they can adjust the temperature.
Installers mount the controller onto the cupboard’s side wall in a preferred location using two screws. The transformer is then mounted alongside the controller using the straps and screws provided.
Finally, the heater is plugged into the controller, the controller into the transformer and the transformer into the outlet.
Final touches
Contractors should be aware that because these new-generation heaters specifically engineered for countertops are low voltage, they don’t aggressively accelerate the heating of concrete.
After installation and power-up, the surface may take 60-90 minutes to reach its stabilized temperature of around 95 degrees F. This slow warm-up process ensures that no thermal shock is introduced into the concrete, addressing the risk of cracking.
The heaters are sold in custom-designed configurations as well as in standard rectangular shapes. They are priced primarily on a square-foot basis and start as low as $250 for smaller standard heaters, including the thermal control unit.