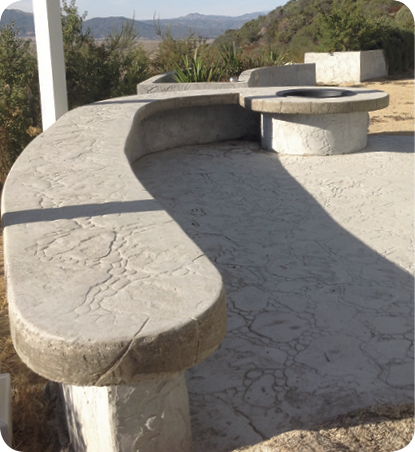
As a child, who wasn’t thrilled to see the wood forms come out indicating a new sidewalk, driveway or even basement was about to be poured?
Today, we know concrete can do so much more, and certainly the forms that helped shape it have changed, too. While steel forms are pretty much reserved for larger industrial and commercial projects, plastic is providing a very durable alternative to lumber these days.
A real advantage to plastic is its ability to be curved and otherwise manipulated. Need a tight radius or maybe a set of cantilevered steps? There are ways of easily achieving them with the right form.
And, while plastic can create a much smoother surface than wood forms, the addition of urethane liners can also add the sorts of textures that in the past could only be stamped, giving decorative concrete experts yet another option to offer clients.
Say it with plastic
Even if your forte is patios and driveways, it may be time to think beyond simple wood forms.
People may automatically think wood when they think about building forms for pouring concrete, but Dan Block, vice president of sales for Milwaukee-based Metal Forms Corp., says his company began manufacturing steel forms in 1909 and launched its Poly Meta Forms — made of high-density polyethylene (HDPE) — at the start of the 21st century.
“Their main market is for a contractor who wouldn’t use a steel form because of its weight, and he’s probably used to using wood,” says Block. “These are very lightweight, and they come in similar lengths and sizes to lumber, so the concrete contractor is familiar with using this type of product.”
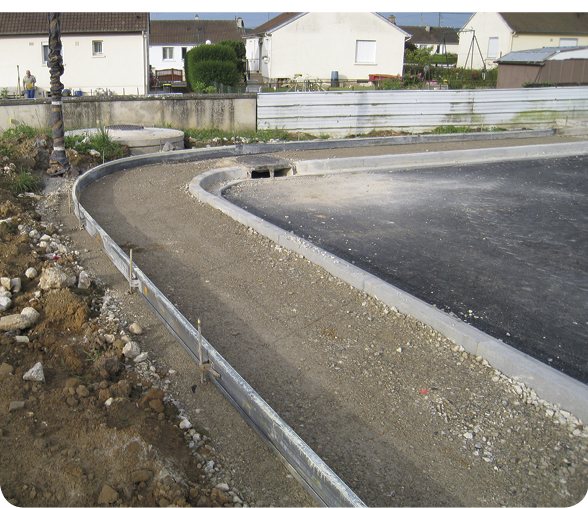
Mary Ann Dorman of Santa Ysabel, California-based Plastiform Concrete Forming Systems LLC says there are other advantages to using plastic forming systems. One is their ability to make tight radiuses quickly and easily. For instance, using a 1-by-4 bender board from her company, it’s possible to create an 18-inch radius.
Perhaps one of the biggest advantages to plastic, however, is its durability.
“I have people who have had them for 30 years and more, and we’ve been in business for 33,” says Dorman. “With wood, you have to shop for something without knotholes, and then you can use it maybe three times if you’re really careful and really lucky.”
Block agrees that durability is a key feature of his product, as well. He also highlights the ease of cleaning, which can be done easily with a broom, a brush or a spray of water. And both Poly Meta Forms and Plastiform are designed to not only snap together easily, but their staking systems allow users to quickly and accurately set elevations.
Their other advantage: fasten a urethane mold inside the form before you pour, and you’ve got a wood- or rock-face without stamping.
“You can screw a urethane liner into the plastic form if you want to give it some accent,” says Block. “It’s an easy upsell.”
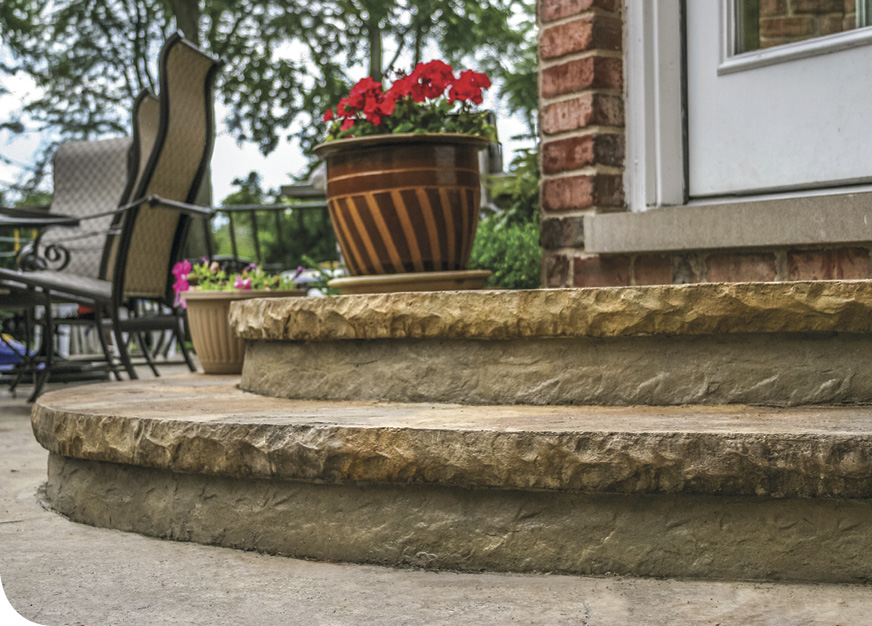
The upsell
“Upsell” is a word Keith Boudart, sales manager for Aurora, Illinois-based Butterfield Color, uses a lot when talking about that company’s one-piece form for steps.
“The advantage is it allows a contractor to have a decorative feature on steps — mainly a cantilever step, a textured step — without having to strip the form the same day to finish it,” he says.
The cantilevered steps are certainly one piece of the upsell equation. Butterfield is the only company to offer the one-piece form, Boudart says. Previously, the company offered the cantilevered step and the riser separately.
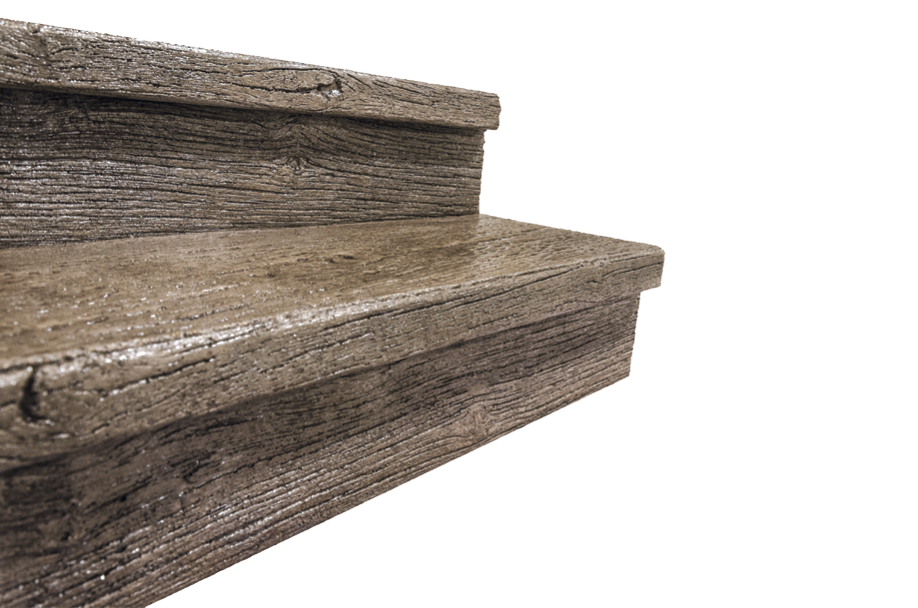
Butterfield has also developed its own form liners specifically for steps that allow a contractor to put a texture or decorative feature on the front or riser. The same form liner works on the outside of a patio or other vertical surface.
“We have a vertical wall system that can be used for creating knee walls called the country ledge form liner,” Boudart says. “We have 2- and 3-foot-high sections, and we also have column forms that match the type of stone.”
Basically, the one-piece steps and the form liners give contractors an opportunity to offer more than just a stamped patio, for instance.
“They might also sell them a knee wall, along with the stamped patio, or they can add decorative steps,” Boudart says. “They’re not only upselling, but they’re raising the level of their expertise and offering a higher-end job.”
Ed Baldoni, owner of the Scott Township, Pennsylvania-based Concrete Countertop Solutions, isn’t so much about upselling as he is offering a better look and an easier pouring experience with his company’s PVC (polyvinyl chloride) forms for countertops and pool forms.
Baldoni’s competitors offer Styrofoam forms, which he notes aren’t nearly as stable or as easy to work with. One secret to the PVC forms’ success is they mount much more securely. They also don’t have to be removed while the concrete is still workable.
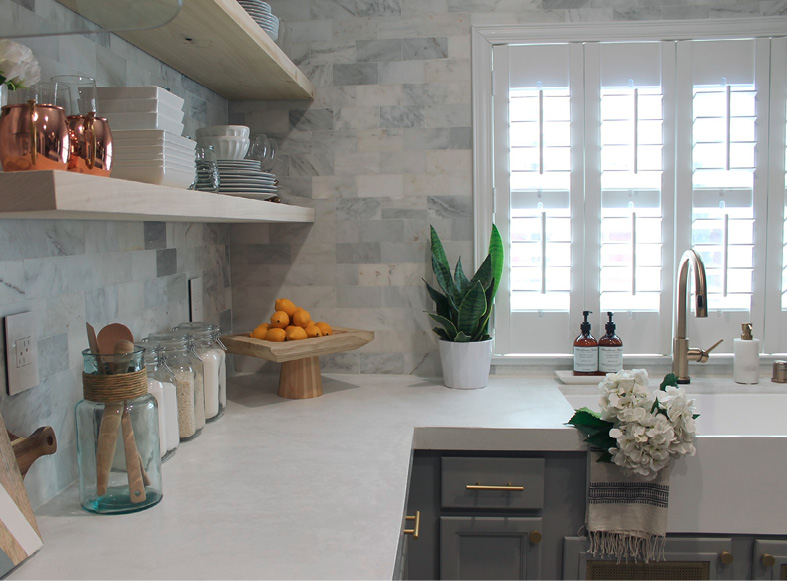
He explains that in both environments, the preferred method for mounting Styrofoam is two-way tape.
“The way our countertop forms mount, we put a half-inch cement board on top of the cabinet and the forms mount from the top into the cement board, so there’s nothing stuck to the cabinet,” he says. “Once the concrete is dry, you pull the form forward and it snaps off.”
Because part of the form is left under the concrete, it isn’t reusable. However, the company’s system does offer seven different edge profiles. And, since the concrete has been poured against smooth plastic, “You’re going to have what looks like a perfectly polished piece of concrete,” he says.
Concrete Countertop Solutions’ pool forms are another story. They snap into the track holding the vinyl pool liner and can be reused. And both they and the countertop forms have reusable liners available to match a stamped pool deck or if a client wants a rock-face or travertine edge on a countertop.
The company’s newest offerings are bringing a touch of Europe to the concrete countertop market as well.
“Our Euro Edge lets users pour a countertop that’s only 7/8 inch thick,” says Baldoni. “They also want white countertops, and you need a special concrete to pour countertops that thin, so we’re replacing our regular mix with the white mix.”
Perhaps surprisingly, Baldoni says that the new mix, which is 50 percent white marble, is less expensive than the regular mix. And, he adds, it’s also ideal for other specialized uses, such as table tops and concrete furniture.
Art and science
If it sounds these days as if the sky’s the limit in terms of concrete forms, that may be a bit optimistic. However, as the heart of any concrete project, it’s important to make the right choices, says Jeff Girard of the Concrete Countertop Institute in Raleigh, North Carolina.
“The fit, the finish, the aesthetic of the finished piece are dictated largely by the form,” he says. “The choice of materials and the techniques to assemble them, as well as its design, are critical.”
Based on years of teaching techniques for working with concrete, he says while beginners focus on getting a good concrete mix, those with some experience know the greatest challenge is building forms efficiently and profitably.
Or, as he puts it, “You can lose a lot of money by spending a lot of time making a complex form that isn’t necessarily required for the project.”
An important thing to consider when choosing the right form for a job is whether the job is one of a kind — say, a custom bathtub — or more of a production item, such as a tabletop. And, for Girard, materials for making forms extend well beyond wood or plastic.
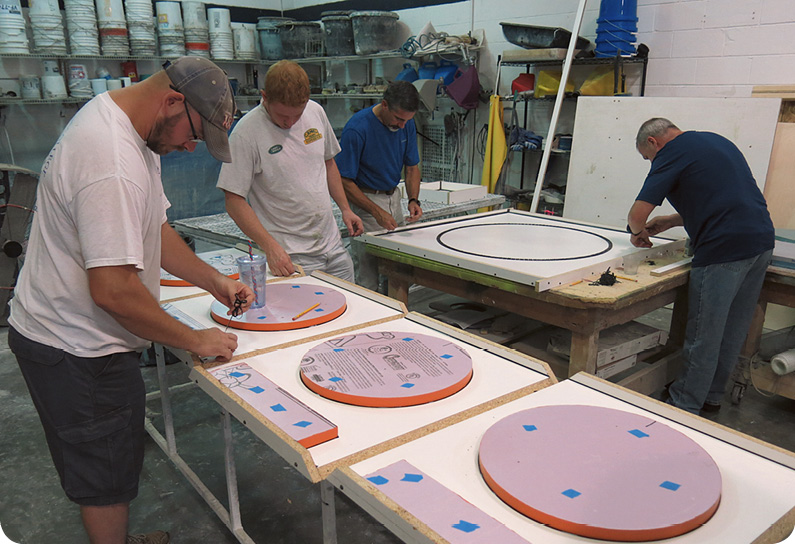
“Because the material that makes up the form is in intimate contact with the concrete, understanding how it interacts with the concrete as it is cast and cures is an important consideration,” he says.
His list includes steel, such as angle iron, various plastics from polystyrene to PVC, melamine, urethanes and silicone rubbers.
“What we do is special,” Girard says. “It’s high value, and it appeals to the person who wants something that’s unique, which means custom. Our skill set should include making forms and molds, and it should involve creativity. We have to get to what the customer is asking for.”
And, what might that be? In the kitchen and bath, Girard says it’s often something that’s tactile — and not granite. He also sees a growing demand for concrete furniture, a demand he compares to “a fast-growing tree.”
“The biggest detriment to concrete furniture is the weight,” he says. “It used to be the only way to make something strong enough was to make it thick enough. Now, the material itself and the technology of the material has opened up the design possibilities to where we can make analogs of conventional furniture.”
It’s those changes in the material itself that Girard believes will dictate what can be done in concrete in the next five years. While the form will continue to accommodate the characteristics of the concrete, he feels many new projects will incorporate systems where a veneer or face coat will be applied to the form first, followed by a backer with fiberglass reinforcement. The concrete will be poured later.
“It’s kind of like making a cake by first putting the frosting inside the pan and then putting the cake inside the frosting,” he says. “There’s an art and a science to knowing how to build forms and then also knowing how to cast with concrete and work with it.”
www.butterfieldcolor.com
www.concretecountertopinstitute.com
www.concretecountertopsolutions.com
www.metalforms.com
www.plastiformcfs.com