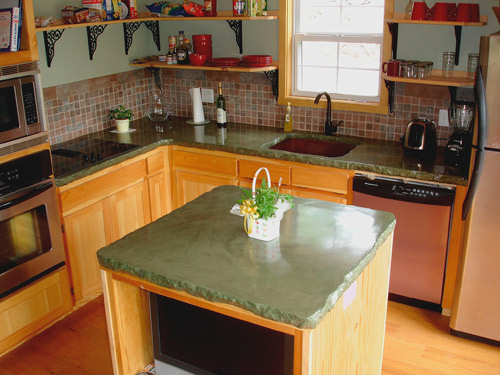
Concrete tables and countertops are held to a higher standard of appearance, feel and performance than floors and walls. And the final element of the finished piece — the interface between the concrete and the customer — is the coating.
There is much debate about the benefits and drawbacks of various coatings used to color and seal countertops. Most people feel there is a trade-off between good chemical resistance and appearance. A high-performance protective coating is often too shiny for many tastes. And to add insult to injury, any coating is vulnerable to contamination from particles that settle into it before cure is complete, so that when the customer runs a hand over the piece, he or she feels tiny imperfections and rough spots. While this is particularly common on countertops installed on a busy job site, it can happen even under controlled studio conditions.
But there is a way to improve the look and feel of high-performance coatings while making them more scratch-resistant. With some extra time and elbow grease, epoxies, polyaspartics and polyureas can be sanded and buffed to a rich, satiny sheen with a glass-smooth finish.
Here is how some concrete artisans are doing it.
Coating prep and application
The first step is to keep as many impurities out of the coating as possible. “Clean the piece again and again before coating it,” instructs Rick Ogden, Rick Ogden Construction, Pryor, Okla. “The fewer impurities, the easier the sanding and buffing process.” Then apply two coats of the selected coating, following manufacturers’ directions for how quickly the second coat can be applied. The coating should be completely cured for 72 hours before sanding. Ogden recommends at least 12 mils. Polyaspartics cure more quickly and can be sanded the day after application, but they are thin-film, so contractors should avoid oversanding.
Sanding
This is where the elbow grease comes in. To eliminate the nubs and bumps, the piece is wet-sanded by hand. Frank Wise, Custom Design USA Inc., Oklahoma City, compares this step to wet-sanding the paint on a car. He starts with 200-grit sandpaper and works up to 1,000 grit. Ogden starts with 1,000 grit if the surface has quite a few impurities and finishes up with as fine as 2,500 grit. Wetting the surface makes the process easier and the surface smoother.
Buffing
Once the surface has been sanded smooth, the coating is buffed using a commercial variable-speed buffer. Start buffing with a more-aggressive buffing compound and a higher-grit buffing pad, and work down through medium and fine-grit polishing pads. Ogden recommends using wool pads over foam and using the compound liberally.
While the process feels similar to buffing paint, there is little risk of going too far and buffing all the way through the coating, as can happen with paint. Also, more pressure must be applied than when buffing paint, in order to remove all the sanding marks.
After buffing with each grit, wipe the piece clean with a damp cotton cloth. Repeat the process until this cleaning step reveals that the desired finish has been accomplished.
Challenges
The biggest downside to sanding and buffing is the extra time it adds to the process and the cost to the customer that results. There is no way to sugarcoat this, but clear communication from the beginning will set a cost expectation and demonstrate the benefits.
The best way to communicate is with samples that the customer can see and touch. “One selling point is the feel of the product,” Ogden says. “It has the feel of old marble. Customers who really want something unique and are already convinced of the worth of a one-of-a-kind concrete table or counter are most likely to appreciate the value added by sanding and buffing.”
Why do it?
The main reason is appearance. “It’s gorgeous,” says Doug Bannister, owner of The Stamp Store, Oklahoma City. “What you’re doing is taking the shine away and then putting a degree of shine back. It has a wonderful glow.” For the customer this is a better-looking result. For the contractor, it is a competitive advantage. “I just wanted to make my work look different — and nicer — than everybody else’s,” says Frank Wise.
Performance coatings such as epoxies and polyaspartics tend to have a high sheen. Some people don’t like the shiny look. And any scratches in the high-gloss coating are immediately visible. Sanding and buffing give a piece a softer-looking finish and keep scratches from showing. Bannister suggests that the heat generated during buffing actually improves the scratch resistance of the coatings.
Another reason is the feel. Sanding and buffing give the surface a nice “hand-feel” comparable to natural stone. Bannister recalls taking two tabletops to an art show. Visitors repeatedly ran their fingers over the buffed and sanded piece, but not the other.
Finally, the look of concrete surfaces that have been sanded and buffed can be restored by repeating the process after years of wear. If the coating gets scratched or dull, wet-sanding and buffing it again restores the soft luster.
The story Rick Ogden tells about how he got started sanding and buffing illustrates both the process and the end result. He says: “I made a coffee table for a man, and even though it was a very beautiful table, it had one little impurity in it that you felt every time you passed your hand over the table. I just could not sell it like that. So I decided to sand it out and see if I could buff the table back to some sort of luster that would be acceptable. Not only was I able to do it, the overall feeling and look of the table was improved immensely. Now I sand and buff everything I do and the results are always worth it.”