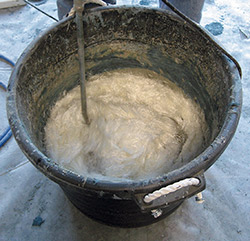
The popularity of glass-fiber reinforced concrete (GFRC) has grown in the past few years as more and more people discover its versatility, strength and relative ease of manufacture. GFRC makes it possible to create stronger and lighter elements and complex 3-D pieces easily.
GFRC is strong and flexible, and because of this, concrete pieces made with it can be thinner, which makes them much lighter than thicker conventional reinforced concrete. Also, because GFRC has its reinforcing mixed in, it makes it easier for more people to make strong, durable pieces.
However, being successful with any material requires some understanding of how it works and what its limitations are. GFRC is fairly tolerant when it comes to variations in mix design or manufacture, but it does require some care during design and fabrication. Compaction and fiber orientation are particularly important to realizing the full benefits that GFRC offers.
This article examines the reinforcing and strengthening elements of GFRC. GFRC derives its strength and flexibility from a high load of alkaline-resistant (AR) glass fibers that are the concrete’s only reinforcement. There is no steel rebar or any other secondary reinforcement material.
The principal factors affecting strength properties of GFRC are fiber content, composite density, fiber orientation, fiber length and type of cure. All of these are impacted by the fiber reinforcement. Low density lessens strength because in less-dense GFRC, entrapped air reduces the bond between the fibers and concrete. Therefore, proper compaction of the composite is very important. Poor curing also affects strength, as an undercured cement matrix is weak and does not form strong bonds with the fibers.
While compressive strength of GFRC can be quite high (due to low water-to-cement ratios and high cement content) it is the material’s very high flexural (bending) and tensile strengths that make it superior to ordinary concrete. Essentially the high dose of fibers carries the tensile loads and helps to make the concrete flexible without cracking.
On average, GFRC has two to four times more flexural strength than does conventional unreinforced concrete. This means that GFRC is stronger and more flexible, while ordinary unreinforced concrete is weaker and more brittle.
AR glass fibers
Let’s take a closer look at the alkaline-resistant (AR) glass fibers inside your GFRC concrete. The AR glass fibers used by concrete countertop makers come in two lengths: 1/2-inch and 3/4-inch. Either will produce similar strengths when used at the same dose, but the 1/2-inch fibers are easier to work with and spread, while the 3/4-inch fibers are more easily sprayed by a machine.
Fiber content in GFRC varies, but the amount used ranges from 3 to 5 percent of the total mix weight. Increased fiber content adds strength but decreases workability.
Besides fibers, AR glass can be incorporated into a piece as scrim. Scrim is a woven mesh made from continuous strands of AR glass. It’s used to enhance flexural properties in locations where additional flexural capacity is needed. Scrim is an efficient form of flexural strength enhancement when its closely spaced continuous strands are placed at discrete locations within the GFRC profile.
Note: Steel reinforcement is NEVER used in GFRC because it can cause warping and curling.
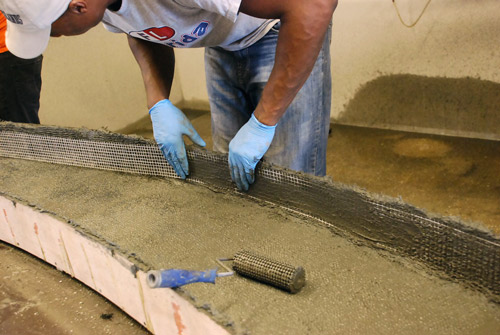
Now, let’s discuss how and why the fibers work.
GFRC uses high doses of alkali-resistant glass fibers as its principal tensile load-carrying member. The concrete matrix serves to bind the fibers together and transfer loads from one fiber to another via shear stresses through the matrix.
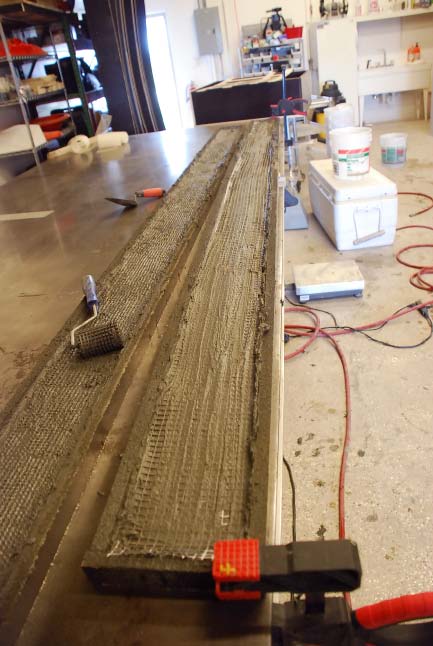
In order to resist tensile loads and prevent the GFRC piece from breaking or cracking, the fiber must be present in a sufficient amount. Additionally, the orientation of the fiber determines how effectively that fiber resists the load. Finally, the fiber needs to be stiff and strong enough to provide the necessary tensile strength. Glass fibers have long been the fiber of choice due to their physical properties and their relatively low cost. High zirconia content makes these specialized glass fibers resistant to concrete’s alkalinity.
Fibers are dosed differently from other admixtures in concrete. Pigments and superplasticizers are dosed by weight against the total cementitious content in the concrete. In contrast, fibers are dosed by weight of total concrete material, which includes the fibers.
A typical GFRC mix uses a high load of glass fibers to resist anticipated tensile loads. Often a volume fraction loading of 3 percent fiber is used. This means that for every 97 pounds of material in the GFRC mix, 3 pounds of glass fibers are added to make 100 pounds of GFRC.
Most concrete countertop GFRC uses the premix method, where glass fibers are mixed into the concrete before application. With this method effective fiber doses ranges from 3 to 5 percent. Commercial GFRC often uses the spray-up method, where longer fibers are simultaneously chopped and sprayed onto the forms, enabling higher fiber loading than can be achieved with the premix method.
Premixed GFRC with fiber doses higher than 5 percent will yield a stiff, unworkable mix that is difficult to place and compact. Ironically, this results in weaker concrete. It contradicts common sense that more fibers should yield lower strengths, but adding too much fiber to the mix will significantly reduce workability. This makes it difficult to properly compact the fibers and to remove entrapped air.
GFRC is all about achieving a high flexural strength. And that is only achieved by using the right amounts of fibers and casting and compacting using proper techniques. Fiber contents lower than 3 percent will not yield strong GFRC. In fact reducing the fiber content to 2 percent can cut the flexural strength by up to 33 percent! The lower the fiber content, the more GFRC acts like a brittle and weak unreinforced mortar.
![]() |
![]() |
Fiber orientation
Finally, the orientation of the fibers is important. The more random the orientation, the more fibers are needed to resist the load. That’s because on average, only a small fraction of randomly oriented fibers are oriented in the right direction.
There are three styles of reinforcement that are used in GFRC. The first is random three-dimensional reinforcing. This occurs when fibers are mixed into the concrete and the concrete is simply poured into forms. The fibers are distributed evenly throughout the concrete and point in all different directions.
This first level of reinforcement describes vibration wet-cast and self-consolidating GFRC. Generally the full profile thickness of the concrete is cast in one pour. Because of their random and 3-D orientation, very few of the fibers are actually able to resist tensile loads that develop in a specific direction, so the concrete has less strength than the high fiber content would suggest. Typically only about 5 to 10 percent of the fibers are effective in resisting tensile loads. This type of fiber reinforcing is inefficient, since only a fraction of the fibers enhance strength.
The second style of fiber reinforcement is random two-dimensional reinforcing. The fibers are oriented randomly within a thin horizontal plane. GFRC is either hand-placed or sprayed into the forms and then compacted. This process forces the fibers to lay flat so they conform to the shape of the form.
GFRC must be built up in thin layers in order to achieve the full flexural strength offered by GFRC. Generally, the layer thickness is about half a fiber’s length. This ensures the fibers will lay flat during compaction. Most GFRC is made to be 3/4-inch thick, built up in two or three layers.
While it is more efficient than 3-D, 2-D reinforcing is still relatively inefficient because of the highly variable fiber orientation within a horizontal plane. Typically only about 33 to 45 percent of the fibers are effective and able to provide real tensile strength. Additionally, most of the fibers lie outside the zone where the tensile loads are the greatest.
The third type of reinforcement is discrete one-dimensional reinforcing. This is how structural beams are designed using steel reinforcing. It is the most efficient form of reinforcing because it uses the least amount of material to resist the tensile loads. The reinforcing is placed entirely within the tensile zone, maximizing effectiveness.
Discrete 1-D reinforcing is added to GFRC, increasing bending strength, when you use scrim in key areas. Scrim is laminated into the backer to add more flexural strength to the piece. It’s used in areas such as the narrow sections in front of and behind sink openings, long, thin backsplashes and bar-top overhangs.