Glass-fiber reinforced concrete (GFRC) is a highly specialized form of concrete distinguished by a cement-rich mortar containing a very high load of alkali-resistant glass fibers. The fibers are the main ingredient responsible for producing high flexural (or bending) strengths in GFRC. High flexural strength is essential to making large, thin concrete slabs and other shapes that are strong, durable and long-lasting.
GFRC also contains another specialized ingredient that performs a vital, but not so obvious, role. It is a prime contributor to achieving the performance, aesthetic characteristics and quality levels that we and our customers demand. That ingredient is polymer, and it commonly misused and misunderstood.
This article presents a lot of calculations, but please read through to the end. They show how some popular GFRC mixes don’t actually contain enough polymer, and how the “recipe” or “formula” format helps conceal that.
Most people don’t understand percentages, but instead work off small batches that make 1/2 cubic foot or so. It’s not obvious from simply looking at a batch formula that calls for X pounds of cement and Y pounds of fibers that the dose of polymer — or fiber — is too low to be effective. I have found that it’s easy to illustrate my point if I show some batch formulas people are using and then back-calculate the proportions from those to show that these popular mix designs actually contain too little polymer and fiber.
Decades of research show that certain levels of polymer are necessary for GFRC to have its expected high compressive, flexural and tensile strengths. The manufacture of GFRC building panels is a massive industry with large research and development budgets, and by using the same practices as this industry, GFRC countertop manufacturers can be confident that their creations will have the same high quality, strength and longevity.
Polymer’s importance in curing GFRC
GFRC is often cast in very thin sections, typically around 1/2 inch (13 millimeters) to 3/4 inch (19 millimeters) thick. Large, thin panels of concrete have very large surface areas, so they lose moisture rapidly, and thin sections of concrete reach lower internal moisture levels much more rapidly than thicker sections of concrete do. This means that good curing practices are more critically important and must be given more time so the full thickness of concrete can reach acceptable strength levels. Concrete that dries out too soon never reaches its full potential, resulting in concrete that is weaker, more brittle, more porous, and often lighter in color than is expected.
Inadequate curing has less of a negative effect on thicker, steel-reinforced concrete, since this type of concrete often spends more time curing in the mold and its greater thickness retains more internal moisture longer. Undercuring thick steel-reinforced concrete usually doesn’t affect its structural performance nearly as much as undercuring GFRC does. Often the compressive strength of the concrete is more than adequate even when it’s only partially cured, and the tensile strength of the reinforced concrete slab (or shape) comes entirely from the steel reinforcing. A properly designed steel-reinforced slab has very high flexural strength thanks to the steel. This is why polymer is not used, nor is it necessary, in conventional steel-reinforced precast concrete.
GFRC, on the other hand, is more sensitive to poor curing practices, and its strength properties (flexural, compressive and tensile) are directly dependent upon the strength development of the cement matrix, as this is what binds the fibers together and creates a solid, reinforced composite. Inadequately cured GFRC is brittle and weak in flexure because of premature fiber pullout from a low-strength, undercured cement matrix.
Polymer in the mix promotes wet curing during the first seven days after casting and also helps the concrete achieve its desired 28-day strength. Typically GFRC is cast, cured under plastic sheeting overnight, and then demolded. Using polymer, and more importantly using the right amount of polymer, permits this rapid turnaround time. The polymer acts both internally and on the surface, decreasing the porosity of the concrete so the evaporation rate is reduced. This allows the concrete to be stored in the open air and yet continue to gain strength as the concrete cures from its own internal moisture.
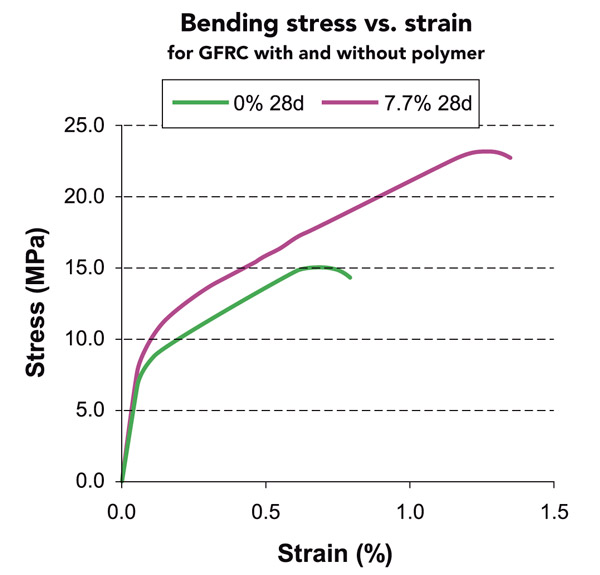
A 20-year durability study by Hiram Ball, Ball Consulting Ltd., found that the minimum acceptable polymer solids content that will confer composite strengths equal to or greater than those achieved with a seven-day wet cure is 6 percent polymer solids by weight. In addition, the long-term properties of GFRC with polymer are superior to GFRC that does not contain polymer. In fact, naturally aged nonpolymer GFRC tends to be weaker and more brittle than it was when it first was made, whereas GFRC with polymer retains its early strength and flexibility.
In addition to its role as a curing aid, polymer offers a host of other benefits too:
- It reduces permeability and water absorption rates.
- It reduces shrinkage cracking and curling tendencies.
- It gives GFRC excellent freeze-thaw resistance.
- It reduces the brittleness of GFRC, letting thin sections flex more without cracking.
- It helps disperse integral pigments better for more uniform and often more intense coloration.
- It makes spraying and hand-layup of vertical surfaces easier.
- It gives concrete with a low water-cement ratio better workability.
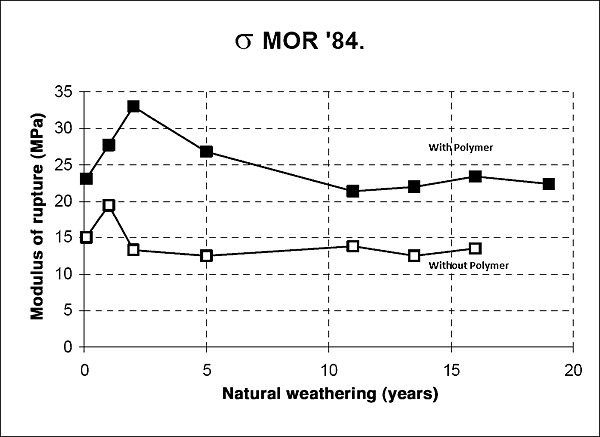
Calculating the right amount of polymer
As I’ve just stated, the effective minimum dose of polymer solids in GFRC is 6 percent by weight. Polymer is most often in a liquid form, so the calculations to figure the right amount of liquid polymer require knowledge about the solids content of the liquid polymer. Most commercial GFRC polymer is about 50 percent solids. (Two widely used brands have 51 percent solids and 47 percent solids, respectively.) If we use an example of polymer with 50 percent solids, half of the weight of the liquid is polymer solids, and the other half is water. And this water counts as part of the mix water used in the GFRC.
I will step through the calculations since this gets a bit complicated. Let’s start with a typical commercial GFRC mix design that will make 10 square feet of 3/4-inch-thick backer for GFRC:
- Sand: 33.4 pounds
- 6 percent liquid polymer with 51 percent solids: 3.9 pounds
- Water (assuming a water/cement ratio of 0.32): 8.8 pounds
- Portland cement (80 percent): 26.7 pounds
- Pozzolan (20 percent): 6.7 pounds
- 3 percent AR glass fibers: 2.5 pounds (3 percent of total weight of all ingredients, including the fibers)
- Total weight per batch: 82.0 pounds
This mix design has 33.4 pounds of sand and 33.4 pounds (portland cement plus pozzolan) of total cementitious material. All admixtures (polymer solids, pigments, superplasticizer, etc.) are dosed based on the total cementitious material weight.
A 6-percent polymer solids dose means we need 33.4 pounds times 6 percent, or 2.0 pounds, of polymer solids (not liquid polymer). To calculate how much liquid polymer (what is poured out of the bucket) is needed, perform this calculation:
2.0? pounds polymer solids
+ 0.51(or 51 percent solids content)
= 3.9? pounds of liquid polymer
If you think about it, about half of the liquid polymer is water and the other half is solids, so about 2 pounds of solids is contained in about 4 pounds of liquid polymer.
To calculate the water:
- Calculate the total amount of water needed:
33.4? pounds cementitious
× 0.32 w/c
= 10.7? pounds of water
Some of that water comes from the liquid polymer. So now we need to calculate how much water will come from the polymer we’re adding. We’ve already calculated that 3.9 pounds of liquid polymer is needed, and that contains 2.0 pounds of polymer solids, leaving 1.9 pounds of water being contributed by the liquid polymer.
Now subtract that water from the total amount needed:
10.7 pounds
– 1.9 pounds
= 8.8 pounds water to add
Changing the w/c ratio alters only how much water we must batch out (more or less than 8.8 pounds). It does not change the amount of liquid polymer needed.
Calculating the right amount of fiber
For completeness, I’ll calculate the weight of fibers called for, too. Unlike other admixtures, fibers are not dosed based on dry cementitious weight. A 3-percent fiber load means 3 pounds of fiber have been added to 97 pounds of nonfiber material to make 100 pounds of GFRC backer.
We first have to determine how much nonfiber material we have. Adding up our ingredients (everything but the fiber), we have:
33.4 pounds sand
+ 26.7 pounds cement
+ 6.7 pounds pozzolan
+ 3.9 pounds liquid polymer
+ 8.8 pounds water
= 79.5 pounds of nonfiber material
So rather than having 97 pounds of material, we have 79.5 pounds of material. We can use ratios to find the amount of fibers to add.
In English: 79.5 pounds is to 97 pounds as (unknown fiber quantity) is to 3 pounds.
In mathematical terms: 79.5 &pide; 97 = x &pide; 3. Do the algebra:
(79.5 × 3) &pide; 97 = 2.458 pounds of fibers needed, rounded up to 2.5 pounds.
The total amount of backer would be:
79.5 pounds
+ 2.5 pounds
= 82.0 pounds
These calculations are complex but essential for correct GFRC mix design. I’ve included them to give you a full understanding of GFRC mix calculations. It is easier to present GFRC mixes in 10-square-foot batches, which you can then multiply by the number of 10-square-foot units you have. For example, if you need to make 52 square feet of GFRC, you can simply multiply your 10-square-foot batch by 5.2. Alternatively, I have a GFRC mix calculator that asks you to enter only the square footage (or meters), after which it produces a batch report.
Examples of poor GFRC mix design
As GFRC has become more popular over the last five or six years as the go-to concrete mix design for concrete countertops, I have gotten more calls about cracking, curling and other issues that I believe are directly related to a disturbing trend: mix designs that use too little polymer and too little fiber. These mix designs run counter to decades of well-studied commercial GFRC mix design and would fail to meet the quality levels required by certified commercial GFRC plants.
Instead of producing a high-flexural-strength concrete that is strong and resists cracks and shrinking, users of these mix designs are instead making brittle, underreinforced concrete that has low flexural strength, higher porosity and greater shrinkage and crack tendencies.
For example, this mix design seems to be quite popular judging by the amount of problems I’m seeing, and it clearly uses too little polymer and fiber to produce the quality and strength of GFRC that the users of this mix are expecting:
- Cement: 23.5 pounds
- Pozzolan: 2.6 pounds
- Sand: 21.5 pounds
- Water: 7 pounds
- Liquid polymer (50 percent solids): 1.5 pounds
- Glass fiber: 1 pounds
Using the calculation methods previously mentioned, the above mix design has only 2.9 percent polymer solids content and only 1.8 percent fiber content! (I’m using 50 percent solids as a middle ground between the commercial polymers that are 47 percent and 51 percent solids.)
Another mix design I’ve seen using powdered all-in-one additives is:
- Cement: 30 pounds
- Sand: 30 pounds
- Water: 9 pounds
- Dry polymer blend: 0.45 pounds
- Glass fiber: 1.8 pounds
This mix design has insignificantly low 1.5 percent polymer solids content and 2.5 percent fiber content!
Concrete has rules that must be followed if it is to produce the kind of performance that is being expected from it. GFRC is a well-studied material purposefully developed to create large, thin structural shells, panels and other high-quality architectural products. It’s an internationally used and recognized material that has certification requirements and standards for quality and strength. The mix designs and ingredients are widely used and tested for performance and consistency.
It’s true that using the required amount of polymer and fibers does increase the cost of the material, but that’s what it takes to make a high-performance material like GFRC. Extraordinary performance demands extraordinary care and attention to detail, and paying attention to what the world has done for the last few decades is a good way to ensure your GFRC will perform to your expectations.