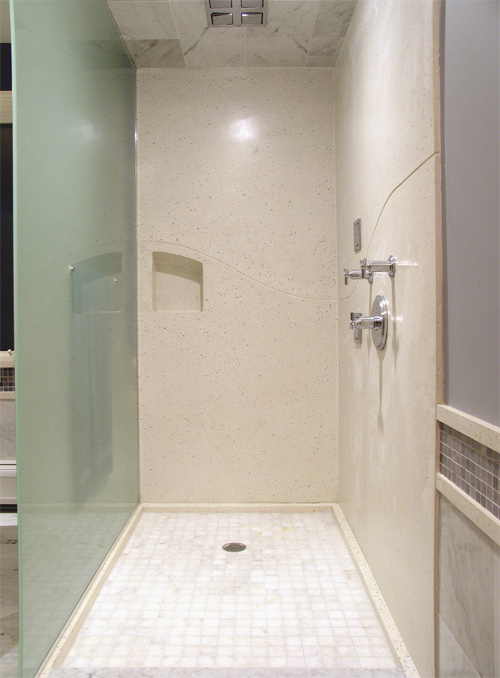
Imagine homeowners having the choice of covering their walls with paint, wallpaper, tile – or concrete panels 1/4 inch thin. Or new homes built with precast modular exterior walls up to 20 feet high that can be manufactured off-site and snapped in place in a few hours.
Concrete wall panels can be thin enough to be applied to an inside wall with epoxy or durable enough to clad a building’s exterior and withstand hurricane-strength Florida winds. The common denominator is their lightweight, modular design and ease of installation, finishing and maintenance.
“They’re a lot like traditional concrete, but (made from) a much stronger mix,” says Raymond Iacobacci of Form Function Concrete, a contracting company located in Rowley, Mass. “You need more tensile strength with concrete wall panels because they’re only an inch thick.” Or even thinner.
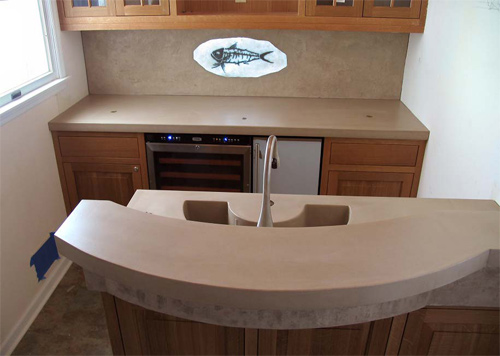
Ryan Brayak of the fabrication and design studio Rock Elements, in Escanaba, Mich., uses wall panels for walk-in showers and other stylish interior flourishes. “Two people can handle them,” he says of the 3/4-inch thick concrete panels formed and installed by his company.
Brayak’s product offerings include an attractive and easily installed alternative to tile. “All I have to do is make four panels (for a shower enclosure). A couple of people can take them into a home and I can install them in an hour,” says Brayak. “There’s no time spent setting individual tiles in grout.”
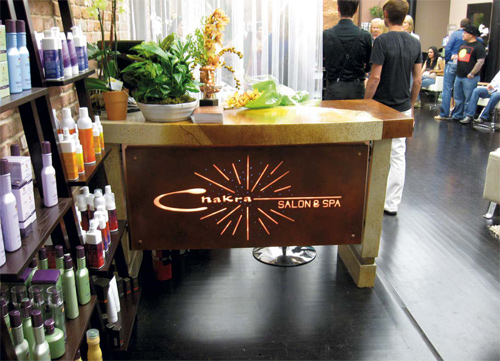
That absence of grout also means less opportunity for water penetration, points out Iacobacci, who values both the style and pragmatic advantages of concrete’s “monolithic surface.” His concrete panels are mostly featured in sinks, shower enclosures, fireplaces, floors and other decorative elements for customers he characterizes as “homeowners who are tired of granite and want something different in the mid-range prices.”
While he observes that most of his clients prefer the natural appearance of gray concrete, he can offer the same range of finishes that are available through traditional decorative concrete – including sealing, painting, acid staining and polishing. He can also add exposed aggregate, though he says that’s a less popular option these days.
For maintenance, Iacobacci recommends simple waxing.
Bold molds
Cindy Russell, marketing director for Nawkaw Corp., promotes the durability of the rubber forms manufactured by her company for producing wall panels. Some of them are sold for reuse up to a hundred times. “They’re very pliable, so you get multiple pours out of a single mold,” she says.
Nawkaw primarily works with precast plants and concrete contractors to produce vertical surfaces with decorative textures. “Everything we do is custom,” Russell says. “We can offer a full range of textures, including rock, brick and geometric patterns.”
Photoengraving is another dramatic aesthetic possibility. “Give us any photo and we’ll scan it and make a mold from it,” Russell promises. Nawkaw is currently seeing interest from a museum of flight history and from several counties in Florida. For each, the company would create concrete design elements modeled after thematic photos in the client’s collection.
J&M Lifestyles LLC, of Randolph, N.J., purposes concrete panels for residential countertops, vanities, fireplace, tub surrounds and exterior architectural features, according to partner Michelle Radley. For commercial customers, their product offerings include bar walls, as well as backlit signs that have been used for hair salons, a gym and a kitchen showroom.
By using glass-fiber reinforced concrete (GFRC), Radley says that her company has been able to get the panels down to 3/8-inch thicknesses while still offering more flex strength than poured concrete in comparable or greater thicknesses. “You can screw into them without any concerns about cracking,” she says.
“The GFRC also makes them good for outdoor use. They won’t crack with temperature extremes. We can do overlays, textures, whatever you want. Your largest cost is the first mold.”
Ruggedly attractive
For Art Porcella, a designer for Everlast Wall Systems LLC, concrete wall panels are less a fashion statement and more a factor of time, cost and rugged durability in new home and light commercial construction. The Florida-based company specializes in the manufacture and installation of precast concrete bearing and nonbearing walls, columns and beams. The company’s tilt-up structural concrete construction work features 5-inch-thick, solid lightweight concrete with 1/2-inch rebar, patented reinforcement and a connection system and scree surface.
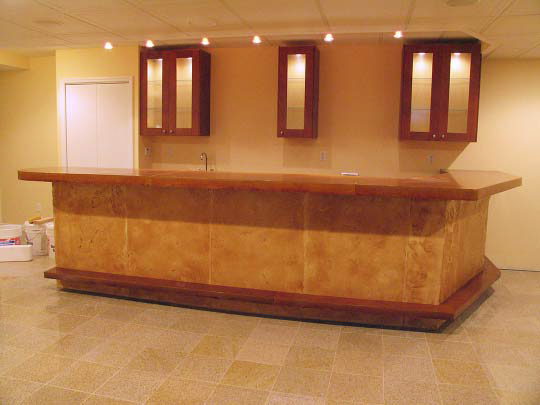
“Ninety percent of our projects in Florida have stucco applied to it,” he says. “Or you can paint it.”
The technology has certainly withstood the test of time.
“We’ve built 1,200 units like this in north-central Florida since ’97. In 2006, we were limited only by our transportation,” says Porcella, who admits that the economy has slowed their pace significantly.
Porcella illustrates the time savings of wall panels this way: “We’ve assembled many 3,000-square-foot structures in three hours or less. There’s no way conventional block masons can lay the blocks to buildings of that size in less than several days. During 2006, our best year, we assembled eight houses a week, sometimes three a day.”
The process has advantages over traditional concrete construction, too.
“Some concrete manufacturers install wall forms and pour the walls on site,” he says. “This is very labor-intensive and time-consuming. We schedule our manufacturing to coincide with site preparations so that when the slab is ready, we can assemble immediately, allowing the site work to proceed rapidly.”
With a panel thickness that’s 3 inches less than traditional concrete block construction, the wall panels allow additional living space to be built into a residence.
But don’t think that quality is sacrificed for speed, cost and material savings. The Everlast system exceeds 180 mph wind load, a prime advantage in hurricane season.
It’s a snap
Nolan Mayrhofer, owner and president of Szolyd Development Corp., a Canadian company that designs hard-surface architectural features from advanced concrete-fiber pastes, also prefers panels over traditional concrete construction. “Water infiltration is lessened, and with the embedded fasteners and threads, the speed of construction is amazing,” says Mayrhofer. “The modular panels just click together like Legos.”
When it comes to panels, he is just getting started. He incorporated concrete panels when provided consulting services and a full-scale mock-up for The Atrium, a major new commercial building project in Victoria, B.C. He predicts similar jobs are on the horizon for him.
www.everlastwallsystems.com
www.nawkaw.com