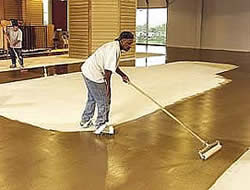
Due to its unique set of performance and installation benefits, the use of gypsum underlayment is growing rapidly in all facets of commercial and industrial construction.
U.S. Gypsum introduced its Levelrock Brand product line in 2000. The new line offers the highest compressive strength range in the industry (2,500 to 8,000 psi). A recent addition to the line, Levelrock Brand Proflow, is the first gypsum underlayment that can be used with a high-performance coating to serve as a decorative wear surface system.
Gypsum concrete underlayment was introduced more than 50 years ago to serve as an alternative to cellular concrete in multifamily construction. It consists of gypsum cement mixed with sand and water. The resulting slurry mix is pumped and poured in place and then “screeded” to a level surface. Depending on the floor layout and the thickness of the pour, up to 30,000 sq. ft. of gypsum underlayment can be applied in a single day.
The product is now the dominant choice in multifamily construction, and its use is growing rapidly in commercial and retail markets. The commercial and retail growth stems directly from recent increases in product compressive strength and “flowability.” Gypsum floors are now able to withstand heavy construction traffic as well as high-volume retail traffic, without powdering, chipping or cracking. The improved flowability offered by newer gypsum underlayments makes the product almost completely self-leveling, further reducing application time and costs and minimizing finished floor preparation time.
Gypsum underlayments accept virtually any type of floor covering, including vinyl composition tile, ceramic tile, wood laminate, glued-down hardwood and carpeting.
In new commercial construction, gypsum underlayment is typically applied over structural concrete or precast concrete planks to create a smooth, monolithic floor surface that delivers superior strength, sound control and fire resistance. The product sets quickly, allowing foot traffic within two hours and continued construction activities the next day.
Gypsum underlayment assemblies offer UL-certified fire ratings of up to four hours. The fire resistance of the floor results from the fact that gypsum is a naturally fire-resistant product. When exposed to flame, it releases moisture in the form of steam, thereby slowing flame spread.
Sound control is another key benefit. The excellent acoustical properties of a poured gypsum floor result from the product’s mass combined with the fact that the underlayment does not shrink as it sets. Unlike portland cement products, which do shrink, gypsum underlayments seek and fill cracks and joints, a major source of sound leakage between floors.
Gypsum underlayment floor assemblies deliver STC (Sound Transmission Class) ratings in the high 60s and IIC (Impact Insulation Class) ratings of 55 and higher, even with hard-surface floor coverings. Gypsum underlayment requires minimal surface preparation. No time-consuming shot-blasting of existing concrete is required. In most applications, the only preparation work required is cleaning, sealing off any through-holes in the existing surface (to prevent the material from running down to the floor beneath) and priming. This makes the product the quickest and most cost-efficient option for transforming worn, cracked and uneven floors into level, high-strength surfaces ready for the application of finish materials.
According to Don Brandt, marketing manager for U.S. Gypsum’s Industrial Products Division, developers and storeowners should specify a minimum strength of 3,500 psi for retail applications that will have a floor covering, and 6,000 psi for underlayments used with a high-performance wear surface coating.