Here it is – a bright and shiny new year! And just like at the start of every other new year, I spent some time developing resolutions and reflecting on previous years and what I’m thankful for. Of course, there are resolutions that look quite familiar, like “Try to slow down and be a bit more thoughtful” and “Don’t gossip” and “Just don’t be so nasty!” And the list of what I’m thankful for also appears familiar: my wife and kids, my extended family and friends, my partners and associates, even my adversaries you see, I have the greatest “adversaries” that any guy could ever ask for! And I’m thankful that for the most part, we all are still here and have each other, have our health, and have enough to eat and a roof over our heads. Wait a minute, Miller! What kind of a column is this? Enough of your personal meandering! This is a decorative concrete trade magazine, right? Ah, thanks for helping me focus…
Practically speaking, I’m thankful for the infrastructure of this great country, and the efficiency and economy it affords us.
I’ve recently returned from a themed concrete hardscape project in Singapore. I was working as an art director on Far Far Away (inspired by the Shrek movies), part of a new Universal Studios theme park on Sentosa Island. Singapore was great, a really wonderful country, with fascinating people and a rich collage of cultures. And a wealthy country as well!
There were even unbelievable benefits from a concrete contractor’s standpoint. As Singapore is near the equator, temperatures are very stable and don’t typically swing much or swing quickly. It’s also quite humid. What this meant, from a concreter’s standpoint, was great latitude as to contraction joints. I’m sure most engineers would disagree with me (even those local engineers in Singapore), but the anecdotal evidence that I witnessed suggests that virtually no concrete out of the 135,000 square feet that we placed showed evidence of any shrinkage cracking of substance. And, believe it or not, I don’t know that a single bit of it was jointed, properly or at all. Amazing!
However, what was not so amazing was my lack of access to proper materials and equipment to complete our project. You see, in Singapore, there are no Home Depots or Lowe’s stores. There are no Ace or True Value hardware stores. There are no White Cap stores. And even something as seemingly simple as purchasing dry bagged silica sand required our initiating a smuggling operation over the causeway between Johor Bahru, Malaysia, and Woodlands, Singapore. I don’t know that it was ever necessary, but I do know that in Southeast Asia, bribes to customs officials are referred to as “coffee money.” I had a staff of three great young Malaysian civil engineers (really smart and talented), who were responsible for procurement, and even so, even with substantial time available for sourcing, we would often come up short-handed.
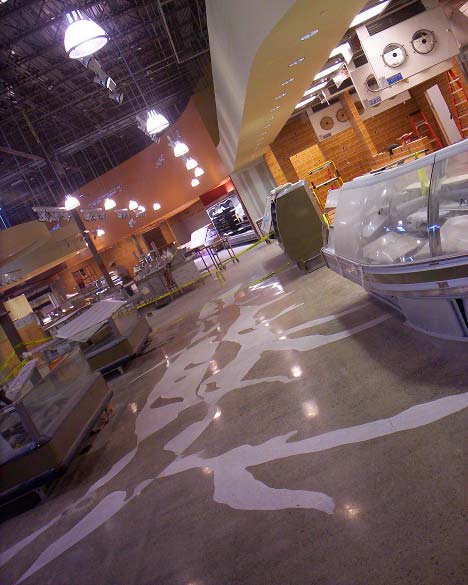
Sometimes this was fun and challenging. I felt a bit like the MacGyver of sensory concrete. An example of this was my first day on the project. The project schedule was continually being modified and shortened. This started from day one. We were asked to place stamped concrete that wasn’t to have been placed for another couple of weeks. In fact, the stamps were still in a container on a ship on the South China Sea. But never mind – we were ordered to pour. I spent the morning with my engineers, young Albert and Chan, scouring the neighborhood shops for rubber from which to dummy up stamps. We finally succeeded and were able to make the pour. Color hardener was hand-batched, with a digital scale and plaster mixer, and cast. Mineral spirits were applied with a garden sprayer to act as a release agent. Dirt, stones, twigs, leaves and other forest debris from under the on-ramp at Opal Crescent were collected and cast, too. We cut Flintstone-style random stone shapes from the rubber with a razor knife and proceeded to stamp away. Even the tamper was homemade – a 4-inch-thick composite of plywood “Makitaed” together with deck screws and an axe handle attached. My mainland Chinese finishers had never done anything quite like this before. In fact, I’d never done or even seen anything quite like this. Not only my part of it, but their part, too. They didn’t use screeds. They used 3-foot homemade wooden darbies. Their longest trowel was 12 inches and was out of plastic. They had no kneeboards, so they concocted what looked like giant rebar chairs out of – rebar. They used these in kneeboard fashion to walk over and then squat above the concrete to do their finishing.
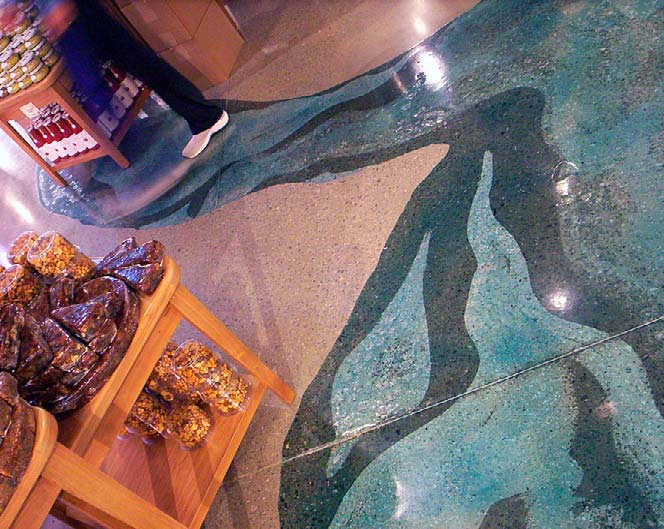
And you know what? They pulled it off. That first pour was perhaps the best concrete we placed over the course of that job. The loose leaves and debris were later washed off, the surface was screened (finding screens and a floor machine was another adventure) and the color-hardened surface was then patina-stained. (Of course, the container was in port, but had not yet cleared customs, so we had to compound the stain ourselves, too, with muriatic acid, iron salts and a little sodium dichromate, which somehow Albert was able to find.) This was fun and challenging, but certainly not something you’d want to have to deal with on a regular basis.
Now, back to the States, and an example of a contrast in efficiency and economy. A few years back, Kelley and I were fortunate enough to art-direct Bob Harris and Mike Speech as decorative concrete artisans on a new Whole Foods Market in Duluth, Ga. Our mission was to design, sculpt and color a stylized map of the Chattahoochee River into an existing ground, polished, sealed, natural gray concrete floor. Our art piece was an afterthought, albeit a really cool afterthought, and was the brainchild of the Whole Foods regional president. God bless him! Anyway, Duluth is just outside of Atlanta, so we had plenty of Home Depots and Lowe’s stores and Ace and True Value hardware stores and, I think, a White Cap. And if there wasn’t a White Cap, there were 10 other well-stocked decorative concrete accessory houses, not to mention the resources of Bob’s Decorative Concrete Institute, FedEx Kinko’s, OfficeMax, Starbucks and NPR. Kelley and I were really comfortable and in good hands. When Bob and Mike showed up on the site that first day, they were driving something similar to a semi, fully loaded with every tool that a sensory concrete gal and guy could ever want. And, if it wasn’t there, they knew where to get it, and fast.
We put in really long days, because the style of work required it. We did have some unskilled labor issues, but they were minimal, and they were more than made up for by Bob and Mike’s preparedness, knowledge, general support and personal extra effort. I’m thankful for guys like this and for all of the hard work of past generations who developed the infrastructure of this country (roads, communications, retail, technical knowledge, the whole lot of it). It’s this infrastructure that allows us the efficiencies and economies of today.