Miracote got involved in a large rehabilitation project in the Broadway Lofts Parking Garage project in San Antonio, Texas, after 240,000+ square feet of concrete on all five levels of a newly constructed parking garage failed immediately after it was built in 2012. To make matters more complicated, the parking garage project was for a fully occupied 308-unit residential complex. The property, once called Villaje del Rio, spans three city blocks and is part of a 350-acre master plan to reinvigorate the downtown and river area of the city. Miracote shared details and photos of this extensive repair project with us.
The failure, caused by fiber being used in lieu of rebar, was catastrophic and extensive. Thousands of lineal feet of cracking had occurred throughout the garage. When examined after opening, it was determined that the cracks extended the entire depth of the slab.
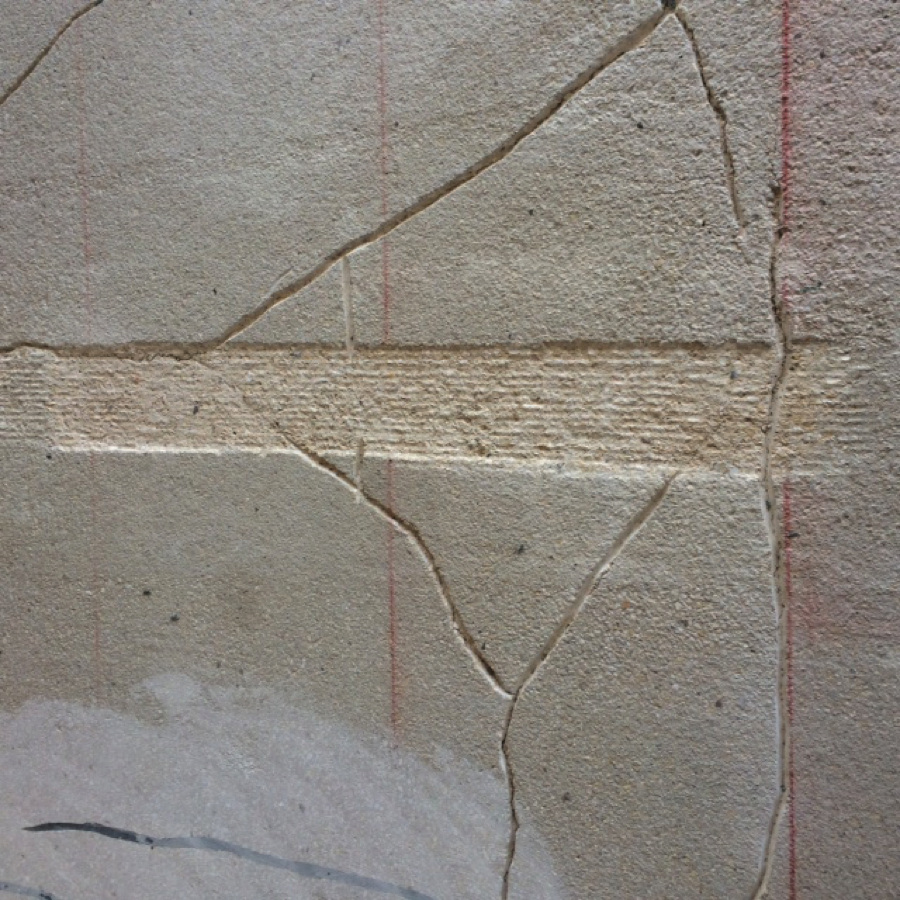
The top 1/4-inch of the deck surface was extremely carbonated due to overwatering during the original pour. Severe dusting was occurring, causing numerous tenant complaints. During rainstorms vehicles became stained and costly removal of staining was required. Surface removal was performed by shot blast and diamond grind methods.
The vehicles driving over the failing concrete created a disturbing cracking sound. The damage was so extreme and safety concerns so pressing that the owner removed and replaced an entire drive ramp. Unfortunately, the tenants experienced a month of noisy demolition and extreme inconvenience during the time of that repair attempt.
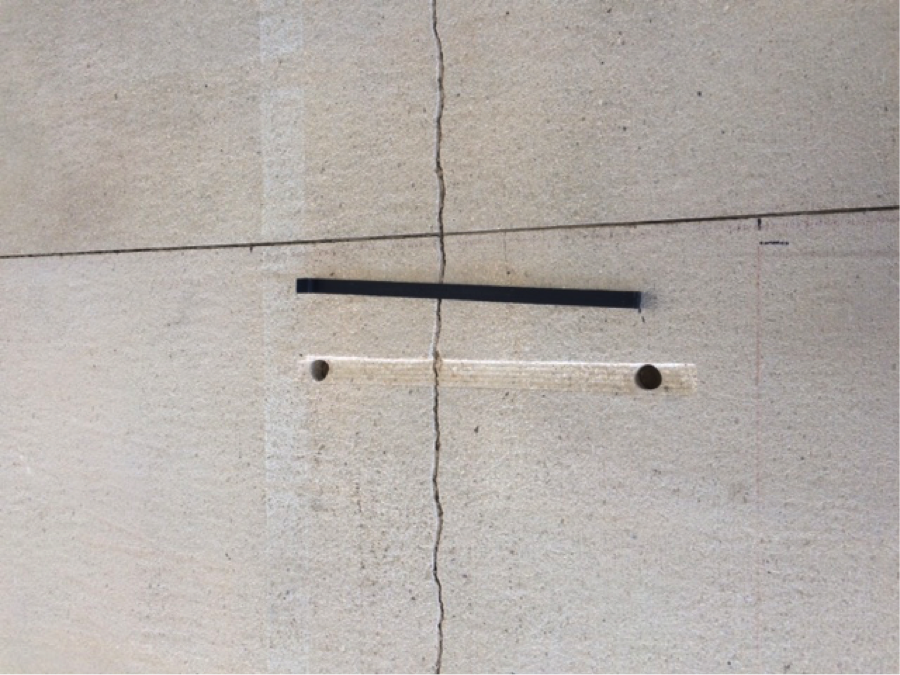
The parking garage owner began to think that he had no choice but to demolish and dispose of all of the concrete decking and undertake a complete re-pour. That came with a hefty price tag of more than $5 million, and there was no alternative parking available for the tenants. They began to investigate other options.
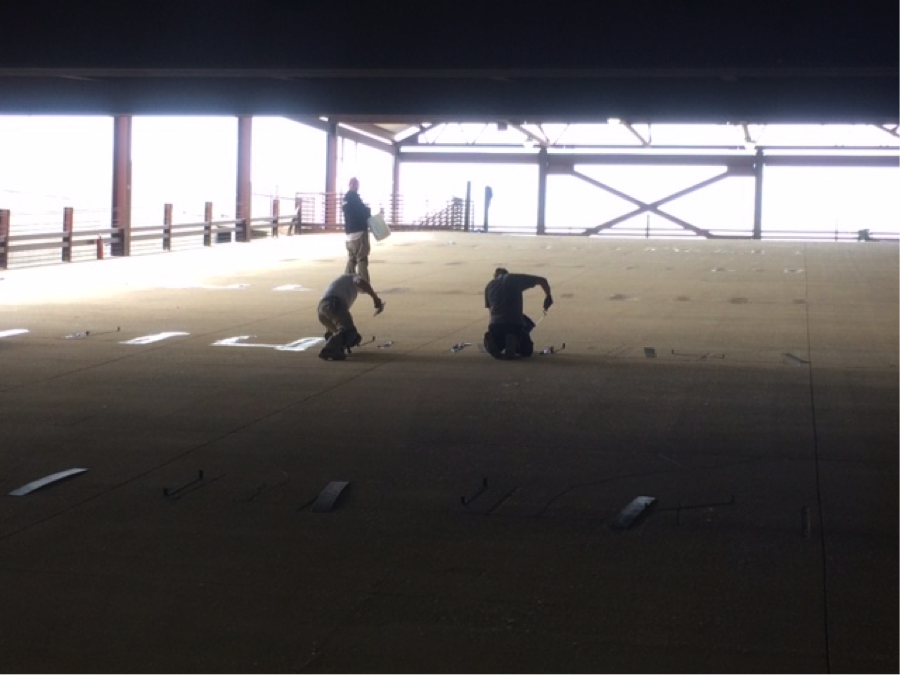
Rick Watson with Surmac Inc., a Texas-based nationwide specialty contracting company, approached the owner with a proposal to design and test a repair protocol. The repair contractor was not involved in the construction of the parking garage, but it was aware of the failure because of other work done on-site. Through the years the repair contractor has performed other work for the owner on other projects, including the successful repair of a 156,000-square-foot multi-use concrete floor for a distribution warehouse that had been scheduled for a costly demolition and re-pour. The fact that the warehouse floor, once slated for demolition and re-pour, is still functioning with no issues reported after 10 years of heavy use provided credibility to the repair contractor’s contention that this parking deck might be similarly spared, and the owner allowed the repair contractor to begin on-site testing of a proposed repair protocol.
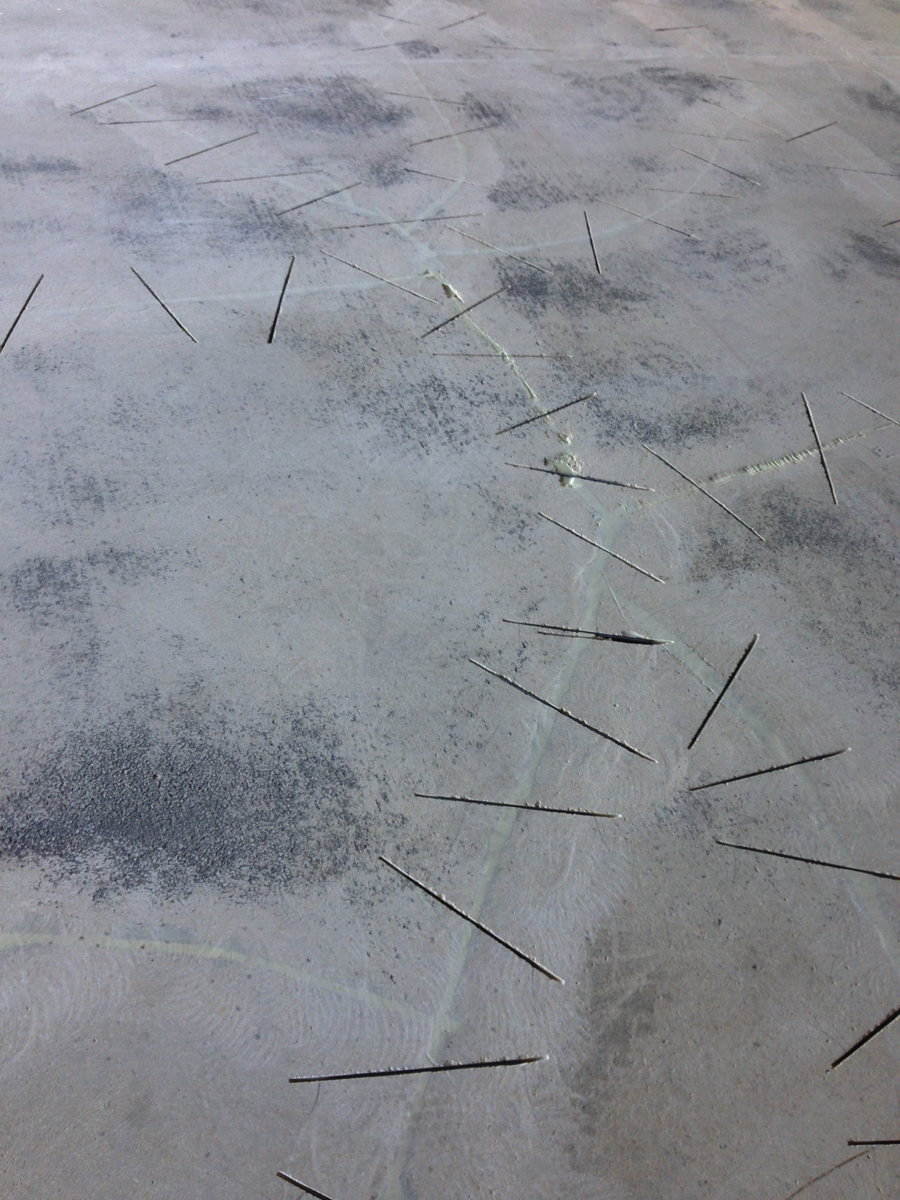
The owner took a lot of convincing that the project was salvageable. Plus, financially it was a mess because the failed deck is the subject of arbitration proceedings to ascertain liability and apportion damages, so the owner would be fronting the cost of any solution—whether repair or demolition and re-pour. Needless to say, everyone wanted the repair to work out.
A series of samples of the proposed repair protocol were performed in the garage and carefully monitored by all parties over a three-year period. The first test sample to measure and evaluate results involved a 250-square-foot area of decking where crack repair was performed,( but no overlay installed) so that the integrity of the crack repair could be monitored over time. Three years later, despite daily vehicular traffic, that repair is holding up well, with no signs of failure.
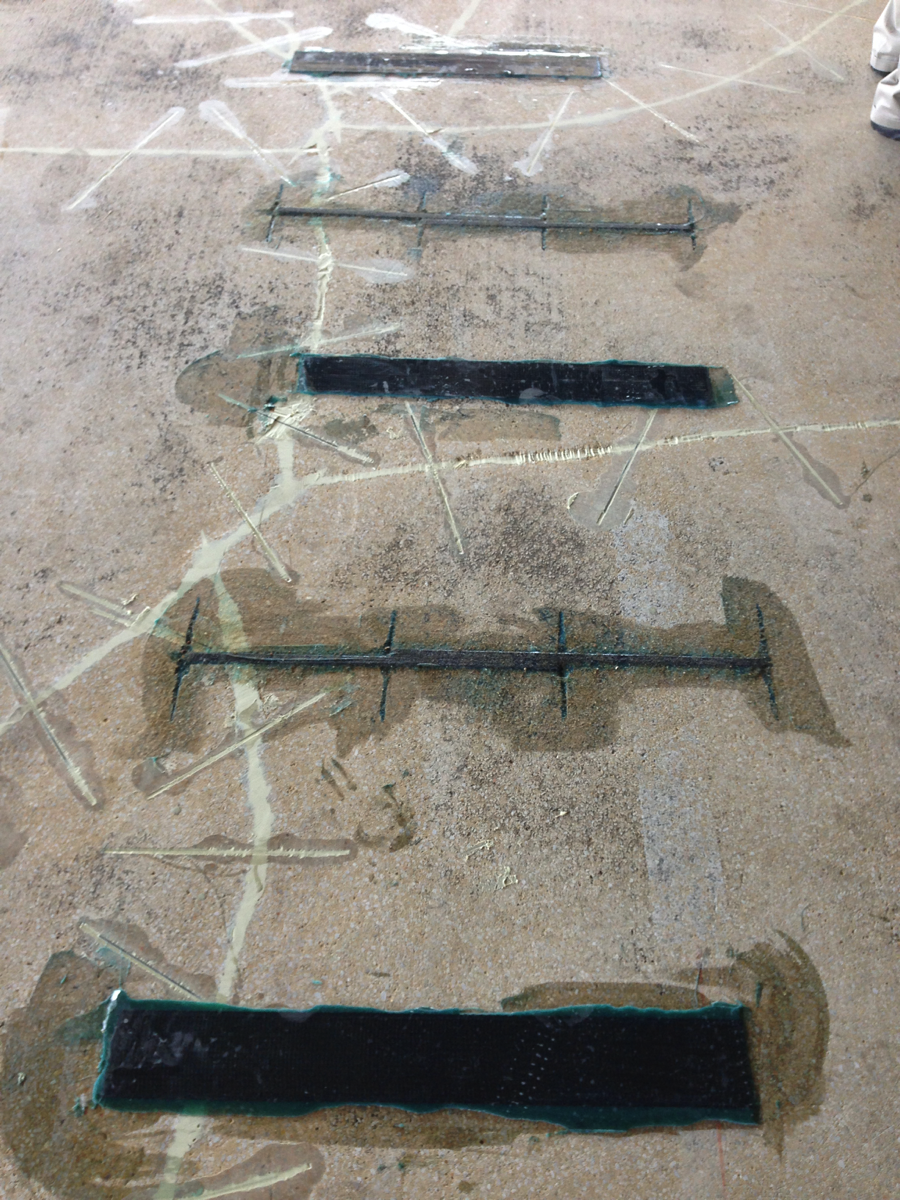
A second test sample involved subsurface flexural strengthening, crack repair and installation of various wear surfaces. That sample also performed well after another year of monitoring.
A third test sample was undertaken at the most challenging area of the garage. A 500-square-foot sample of the final proposed repair protocol was completed and monitored for performance for one year. This sample, which was performed on a turning radius in the driving lane receiving heavy daily use, showed no sign of deterioration or other issues. Based on the success of these samples, the repair process was undertaken.
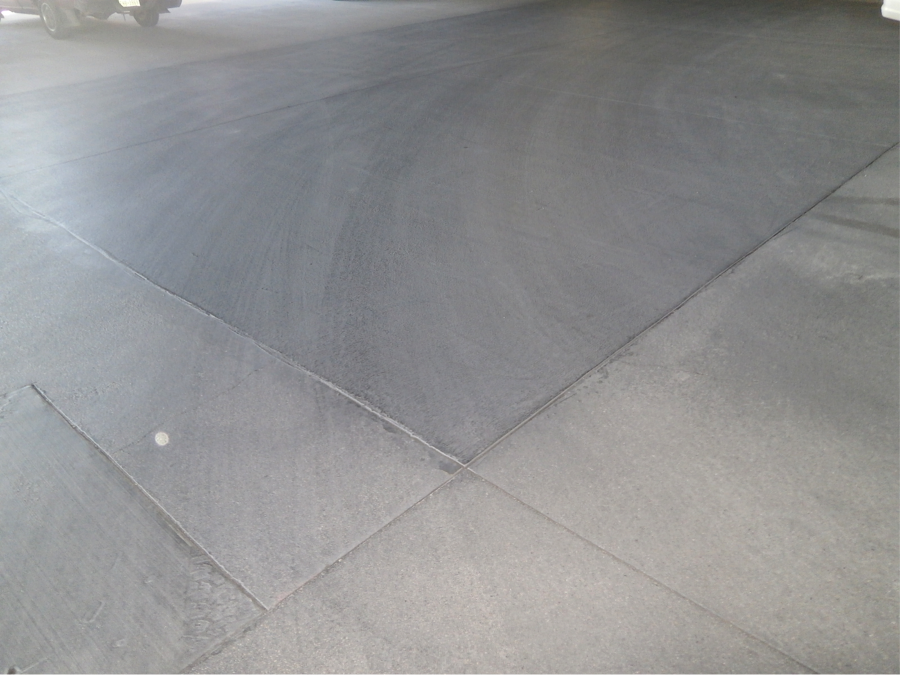
To repair the cracks, a low-viscosity, hybrid polyurethane-polyurea mender called Fast Patch LV was applied, seeping the full depth of the crack and welding the broken concrete deck sections into a monolithic deck member.
Custom-designed, open-weave carbon fiber strapping was cut to 4-foot lengths and epoxied into a precut 1/4-inch-deep pre-routed bed. Specially designed 1.5-inch-wide by 24-inch-long solid carbon fiber staples manufactured by Fortress Stabilization were fitted into the pre-drilled and routed troughs. Both systems were used side-by-side at 3-foot spacings placed over the main girder beams to ensure increased rigidity and protect against excessive flexing. A total of 3,000 staples and 4,000 lineal feet of carbon fiber strapping were used on the project. Additional joints were cut to provide relief in areas of extreme cracking; taking care not to cut through the carbon fiber.
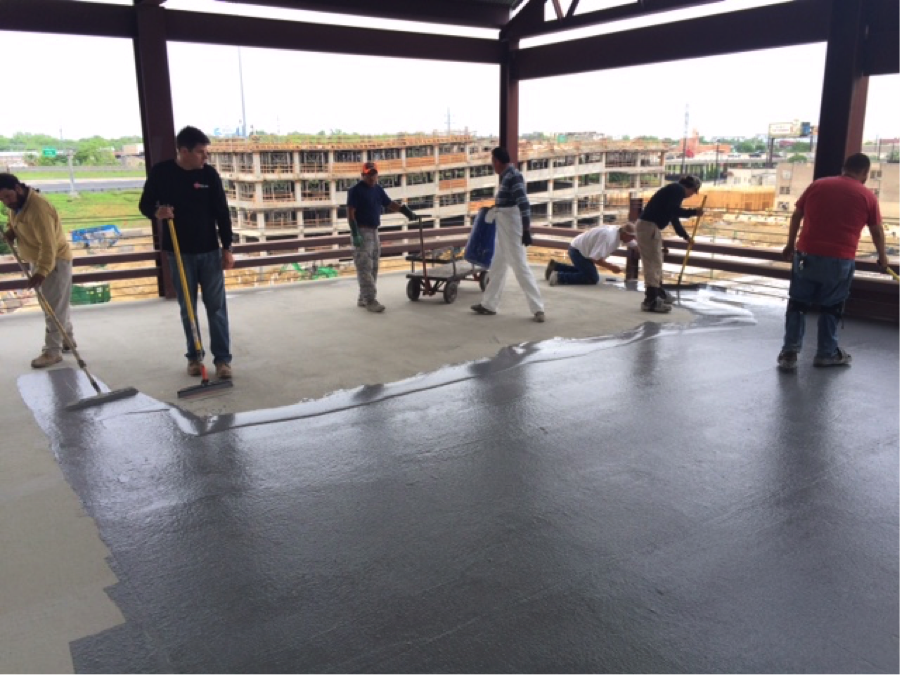
Because of the unusually large capillary structure and very high porosity of the deck, it was decided that a deep-penetrating alkali-reactive internal hardener called Miracote MiraPrime Aqua-Blok would be used to both stabilize the low (6.8) pH and strengthen the concrete. An alkaline catalyst also was used to make sure that there was enough alkali in the concrete for the concrete to react. The chemical reaction creates a dense crystalline network of insoluble calcium silicate hydrate gel within the pore structure. During this process any subsurface contaminants would also be purged. The net result is that this process increases concrete density. The final pH tested at 11.8.
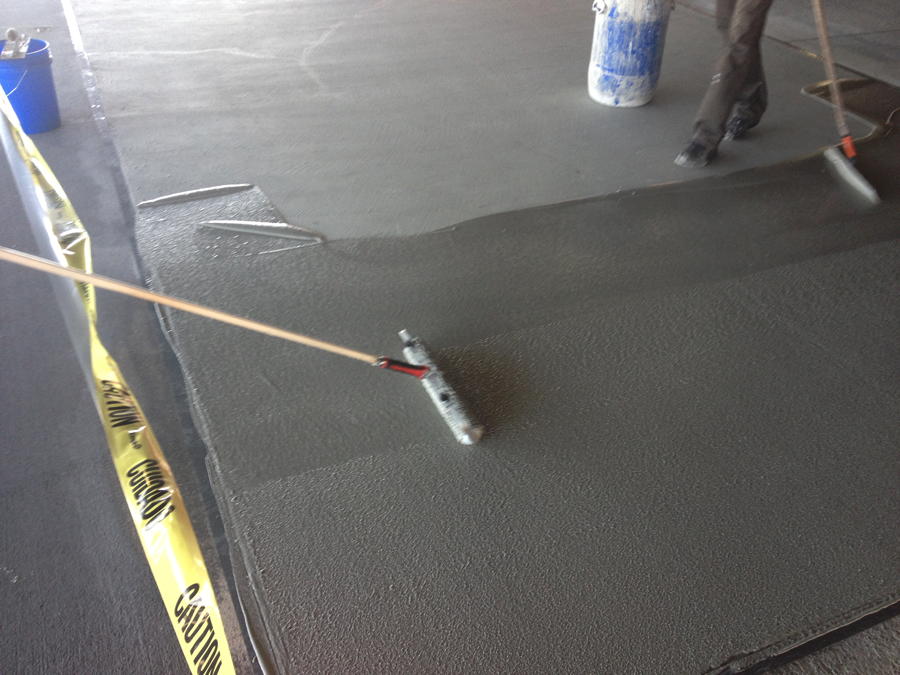
Because the wear surface was very delicate, a three-coat heavy-duty overlay system called Miracote MPC Park Deck was installed as the new driving surface. The 10-year warranty on the system issued by the manufacturer helped allay the owner’s understandable concerns, given the unfortunate history of the garage. Application consisted of two squeegeed coats of a polymer-based cementitious waterproof overlay, MPC (Multi-Purpose Protective Coating) in natural regular, was followed by a polymer-based wear coat called MPC natural hard impregnated with aluminum oxide that was back-rolled for a stippled effect to enhance traction. A penetrating clear sealer called Miracote MiraGard Dry Look was then applied as an added water- and stain-repellent layer and to facilitate future cleaning of the surface. The deck also was restriped in a new layout that added an additional 20 parking spaces in a part of the city where parking is at a premium.
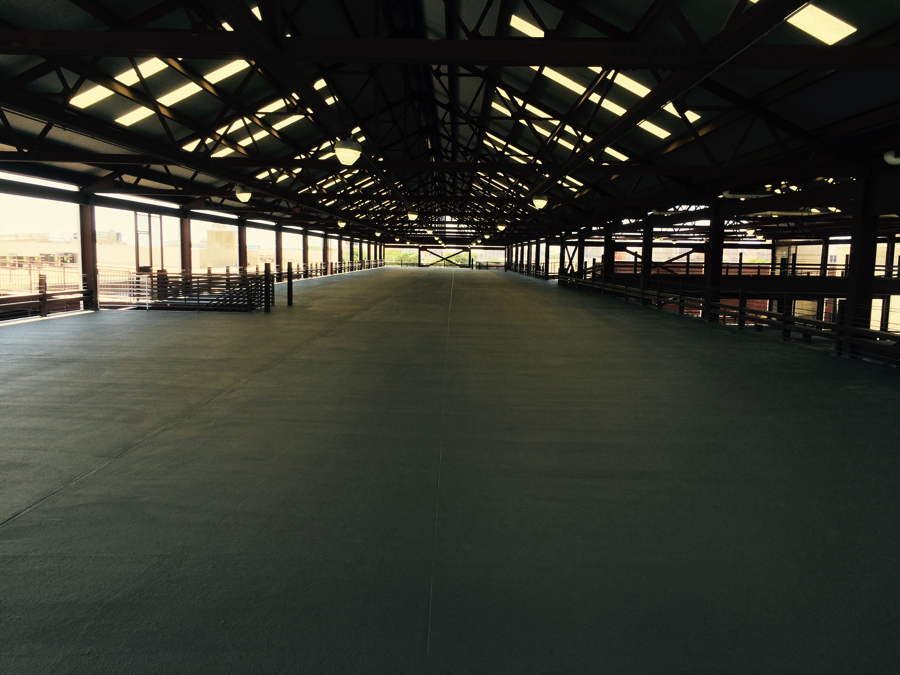
The garage remained open for tenant use throughout the repair. When the present owner bought the property out of bankruptcy in 2012, it was challenged to find the best use for 19 concrete superstructures that had been abandoned during construction some 17 years ago. The property was described as an “eyesore” by San Antonio’s mayor and “a symbol of deterioration and disinvestment” by its deputy city manager. With the help of a $23.4 million government-backed loan, the present owner converted the dystopian-looking building shells into an award-winning standalone destination for urban living that is now fully leased. Now that the parking garage has been repaired, it continues San Antonio’s mission to revitalize downtown.
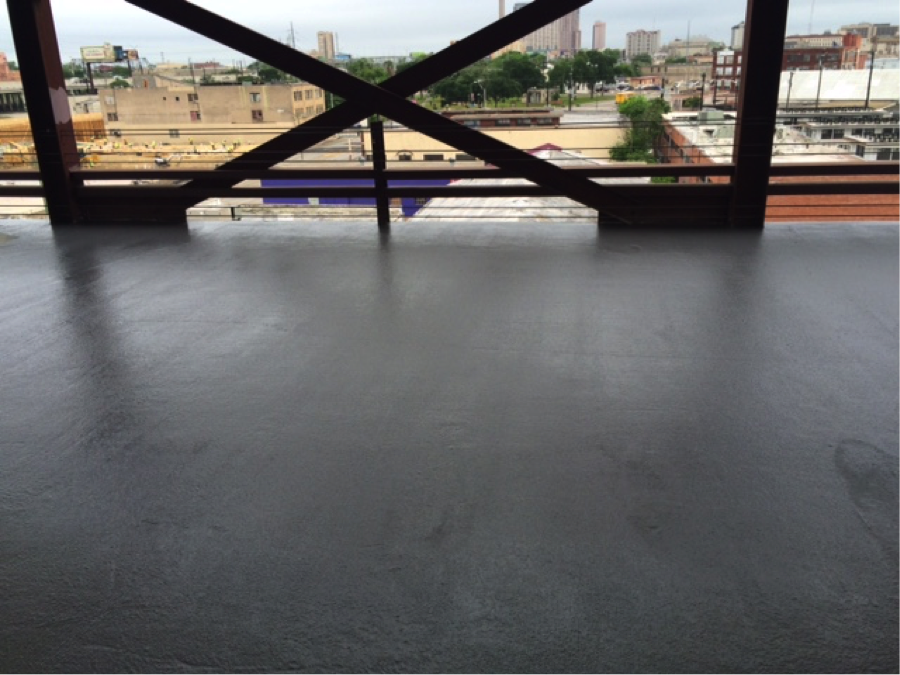