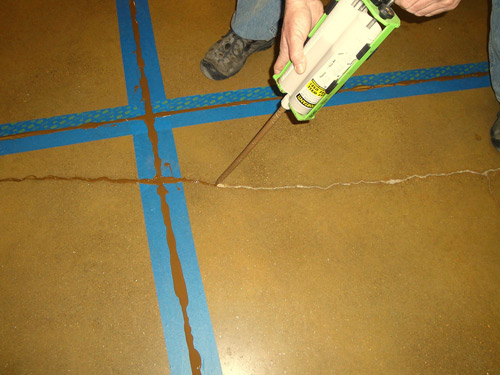
A concrete floor polished up to 3,000 grit, stained, guarded and burnished can be a sight of sheer beauty. For many customers, a polished concrete floor is the perfect fit. The only problem is, many concrete floors are far from perfect slabs. There are pinholes, cracks, pop-outs, gouges, and spalling joints, just to name a few flaws.
Defects not only detract from the aesthetics of the floor, but can also compromise a facility’s functionality. They create problems such as trip hazards or can act as bacteria collection points in locations with sanitation concerns, such as hospitals and food processing plants.
When it comes to high-end floors, these types of imperfections are simply unacceptable. Fortunately our industry has progressed to the point where it seems every disfigurement can be addressed.
Small hole and defect repairs
When it comes to everyday holes and small cracks (those less than 1/8 inch wide) your best bet is to use a polyurethane/polyurea polymer.
The process for addressing a chip in the concrete surface is relatively easy. Begin by removing all debris from the defect, and leave it in its structural concrete form. Next, slightly overfill the problem area using your selected polymer. If the floor repair is being done in conjunction with grinding and polishing, the repair material should be applied after the initial coarse grind.
The product must then be given time to harden. Depending on the polymer used, the wait time will vary. Metzger/McGuire’s Rapid Refloor sets up in about 25 minutes.
Then the overfill material can be removed. If the polymer is used during the course of grinding, simply move on to your next grit.
It is important to note that stronger polymers require aggressive tooling of 100 grit or more. If the repair is not done in conjunction with grinding, the excess can be removed using a cup-wheel grinder and a medium-grit pad. Using this process the floor could be ready for traffic again in as little as 30 minutes. Repair of minor defects is simple and can turn a potential safety hazard or unsightly blemish into something barely noticeable.
Joint separation
We have all seen it before — previously filled joints that have opened up and left tears or voids in the installed joint filler. The simple fact of the matter is that concrete shrinks. A typical concrete slaib contains more water than is needed to activate the cement. Over time the moisture begins to exit the slab via evaporation, reducing the overall size of the concrete slab. The typical rate of shrinkage in a 6-inch slab is 1/8 inch per every 20 feet. This means that if you have 15-foot panels, each 1/8-inch saw-cut joint will eventually open to almost 1/4 inch, an expansion of nearly 100 percent.
This leads to a common question: If separation is going to occur, when do I need to be concerned? Charles Serrano, Florida sales representative of Niagara Machine Inc., explains that 1/32 inch, or approximately the width of a credit card, is the magic number. “Hairline voids are bound to occur, but will rarely be cause for concern. What is important is separation between the filler and slab. The main concerns here are if the separation will cause joint edge deterioration over time (especially with seasonal changes affecting the level of separation) or if sanitation is a concern.” If either of these are issues, then the joint should be addressed.
There are two main options for repairing filler separation. The first is cleaning out the separation voids by removing loose debris mechanically or with compressed air and then refilling with a fast-setting semirigid polyurea or slower-setting epoxy joint filler. The second option is to cut out or “mill out” the top 1/2 inch of filler using a saw, then utilizing an epoxy or polyurea polymer to refill. Each of these methods has its own pros and cons, but both will get the job done.
Color-matched joint filler
Nothing can put a bigger damper on a beautifully polished or colored concrete floor than having a mismatched joint filler color. As options for concrete colorants have become nearly limitless, the ability to match joint and repair material to the substrate has followed.
Metzger/McGuire has color options in many of its product lines that are designed to match the colors of industry leaders in stains and dyes such as L. M. Scofield Co. and Prosoco Inc.