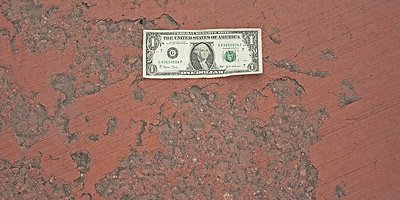
Watch out for water, especially in climates where you get cold winters. Water is by far the biggest challenge you will face as a decorative concrete professional.
Words like “spalling,” “flaking,” “pitting” or “chipping” are not what people making a living in concrete want to hear. Rarely do these words accompany a satisfied customer, and rarely do they lead to a profitable month.
Too much surface water will break down a film-type sealer, turning colored concrete white and unappealing. And water emission trapped beneath some sealer types will lead to an unattractive project.
So to fight water and freeze-thaw, you have to have a battle plan that involves proper sealers.
No battle plan
The picture with the dollar bill shows a commercial project without a plan to battle freezing water. For the record, this project did not live up to the owner’s expectations. The concrete pictured is only a few years old, and not long ago the integrally red-colored flatwork looked nearly flawless. It’s obvious the contractor took great pains to consistently place several truckloads of colored concrete and equal pains to consistently finish the surface too. Let’s break down what went wrong and then chalk it up as a learning experience.
First, let me disclose that the only concrete failing on this commercial project is along areas with high foot traffic. The concrete is spalling, or flaking, along these areas because this is the only area exposed to heavy wintertime usage of de-icers. I visited this project and quickly noticed no concrete disruption in the outdoor seating area. No one uses this area in winter so there is no need to seed salt or de-icers here.
A simple penetrating sealer would have eliminated, or greatly reduced, the problems pictured. A penetrating sealer would not affect the color, not affect the slip-resistance, and barely affect the project’s budget.
A penetrating sealer would also simplify the snow removal process, making it less necessary to use a de-icer.
No one made a plan to control freeze-thaw or the ill effects of de-icing and the results are catastrophic and expensive to remedy. This flatwork will only deteriorate further, eventually leaving the owner liable and at risk.
Your exterior plan
Relying on the ready-mix company is not enough. Most suppliers will provide air-entrained concrete, which resists freeze-thaw damage, but this alone will not always be enough protection. Your exterior decorative concrete plan must include a short-term and long-term protective plan.
Let’s take the short-term plan first. Concrete sealers work best when applied in temperatures 50 degrees and rising. So it’s very possible that late-season flatwork will be left unsealed through the winter. If so, we must formulate a protection plan which includes not using de-icers until the concrete is properly protected. DO NOT let your customer use de-icers the first winter if concrete is left unsealed.
Your long-term plan hinges on a few steps taken during concrete placement. Keep the ready-mix just wet enough to provide a workable material for placement. Maintain a slope of 1/4 inch per foot, especially if the surface is imprinted. Water will puddle in low-lying areas, even with adequate slope, which creates even more justification for sealing. Let the concrete cure for at least 30 days before sealing. Thoroughly clean the surface with pressurized water and then let the surface dry overnight before applying the sealer.
Make sure all irrigation sprinklers spray away from the sealed surface. Make sure all roof drains discharge unwanted water into a drain and not across the flatwork surface.
One last thing to remember — topical sealers require a nonskid additive but penetrating sealers don’t.
Differences between sealer types
Few will argue that decorative flatwork looks best with a film-type topical sealer, but I personally will do everything possible to talk my customers out of this type of sealing. You can do everything textbook, topically speaking, and still find yourself with a customer call-back.
If you’re uncomfortable with applying topical sealer, learn how to sell your customer on the natural beauty of penetratingly sealed concrete. The paver industry has done this for years with great success.
Below are differences between the two sealer types, to help you out.
- Topical sealers cost more than penetrating sealers.
- Penetrating sealers generally last longer and provide protection longer.
- Topical sealers can be slippery, while penetrating sealers don’t affect slip resistance.
- Penetrating sealers don’t enhance color but topical sealers do.
- Topical sealers protect against the sun’s UV rays but a penetrating sealer won’t.
- Penetrating sealers will not protect against wear patterns from foot traffic, but topical sealers do.
- Topical sealers are notorious for “adverse reactions” while penetrating sealers aren’t.
- Topical sealers can potentially provide a profitable maintenance side for your company, while penetrating sealers rarely offer resealing opportunities.
- Penetrating sealers are more user-friendly, while film-style sealers are the most dangerous ingredient of decorative concrete. Most are made of solvent and very combustible. Solvent sealer is extremely dangerous when under pressure and warm, especially in 55-gallon metal drums. Also, skin and eye burns are very common with topical sealers and very rare with penetrating sealers.