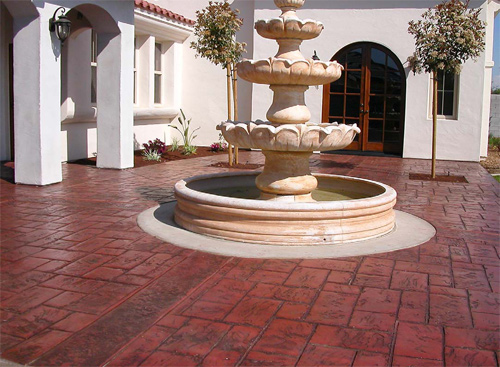
You asked for it, here and here it is. I am going to talk about troubleshooting concrete sealers.
I had a dream the other night that I was driving down Highway 101 on the coast of California in a red Corvette convertible. This is no doubt a car I could have purchased new with all the money I have invested in sealer callbacks. It was as if I was looking down on myself from Google Earth. But upon zooming in I saw that, although it was a pleasant experience of a scenic drive, this wasn’t the case. Taking a closer look, I noticed a red pump-up sprayer in the back storage area of the car with its hose and wand dangling in the air behind. I obviously was in a hurry to fix a sealer problem. Weird.
We have been hitting this sealer problem head on in this column because this is what your feedback has asked for. I recently had the chance to visit with Bert Adams of Glaze ‘N Seal to get his input on what is happening with this industry. Having an opportunity to see the sealing part of our business from a manufacturer’s point of view is priceless. This guy has years of experience and no doubt has red, white, and VOC blood cells coursing through his veins. Thanks, Bert.
Troubleshooting
I asked Bert what the heck is going on with these concrete sealers most of our industry is using today. Bert broke it down to me something like this: A certain percent of the jobs sealed will fail. The idea is to stack the deck in your favor, but the fact is that some jobs will need more work than others. Bert reminded me that the reason for sealer failure is not always obvious.
A film-forming sealer that “turns white” could be the result of moisture trapped underneath or hard-water deposits on top of the sealer. The remedy for each cause is completely different, but Bert recommends starting with the lesser of the two evils first. The easiest, in most cases, is mineral or hard-water deposits sitting on the sealer surface. This will usually be around the perimeter or edges of decorative work as it transitions into landscaped areas.
Bert recommends using a product like Lime-A-Way or a mild acid solution to break down the white buildup. This may take several applications but will not hurt the sealer. The next step will be to neutralize the surface, let it dry, and then reseal your job. Recommend to your customer to adjust the sprinklers or install a water softener.
Moisture problem
If your sealer problem is from moisture trapped underneath, then you will need to take one or more of the following steps to remove the dead sealer. I say dead because that is exactly what it is. If you try to reseal over the damaged sealer, you will find yourself dealing with the same problem again, but with a much harder fix.
The old sealer must go. The most effective ways for this to happen are chemically, with hot pressurized water, or with sandblasting. Not fun.
Be sure to test an area to see what works best for your project. Check out Concrete Decor’s last couple of issues for more on removing old sealer. Once the removal of the old sealer is complete, you’re good to go with a couple of light coats of new sealer.
Application advice
I have to admit that I like to cut my sealer. When I told Bert from Glaze ‘N Seal this, the silence was long and calculated. His response was nothing short of polite, but confident, supported by the fact that most sealers come ready to use.
He warned that many states are closely watching VOCs and diluting may be illegal if it increases the VOCs. Now this may or may not be a big deal to you or your client. But the fact that dilution can compromise the film formation, affecting the life of the sealer, might be a big deal too.
You may be asking yourself if the compromise is worth the trade-off of how well the sealers lay down with a shot or two of xylene or acetone. This is your call, but the fact is, most manufacturers will be hard-pressed to help troubleshoot a product that has been compromised. Nevertheless, apply the sealer with thin coats and be sure to add “nonskid” to your sealer on exterior work.
Life expectancy
One of the most common questions my office receives is how long will the sealer last before resealing is necessary. Bert recommends resealing every two to three years to maintain a fresh look.
If a glossy look isn’t important, know that the concrete will be stain-resistant for five to eight years with most film-forming sealers.
Bert had some recommendations for preventative steps when applying sealer. One, make sure to use a quality sealer and know what it’s capable of doing (or not doing). Two, follow the product guidelines, especially with respect to condition of the substrate, surface temperature, and method of application. Three, make sure the concrete surface and edges are completely dry before, during and after application. Remember, stack the deck in your favor.
Personal note: I have used most of Glaze ‘N Seal’s sealers over the years and have found Bert’s company nothing but top-notch to deal with. You can reach Glaze ‘N Seal at www.glaze-n-seal.com for more information. Thanks again, Bert.
Questions from readers
Question
We just finished an interior grind-and-stain floor. It turned out beautiful with three light applications of sealer. However, the owners are having problems mopping it clean. Do you have any suggestions?
Answer from Concrete Decor
Are your customers wet or dry mopping the floor? You may also consider applying a wax to the floor as that can assist with cleaning while creating a sacrificial coating on your floor. Following a wax application and buffing they should be able to run a microfiber pad over the surface regularly to keep the floor looking great.
Let me know if you have any other questions.