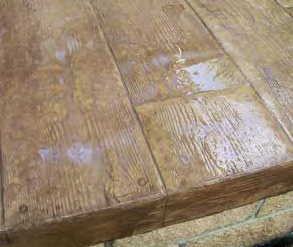
CCI Flooring Inc. in Crest Hill, Ill. installs and distributes sealing products. The company is involved in more than 500 decorative concrete jobs per year. CCI President Bob Bauer worked with solvent-based sealers from 15 different top suppliers before settling on a product he likes.
Bauer offers specific steps and precautions to make sure solvent-based sealing is successful:
“If the surface was recently power-washed — or it has rained — make sure the felt expansion is not wet. If it is damp, you will probably get white foggy areas along expansion after sealing.
“Make sure you tell your customer to turn off automatic sprinklers. Water mixed with solvent sealer will give you days of cleaning enjoyment.
“If you are resealing a job done by someone else, verify the prior sealer. If this is not possible, do a test area. If you have not tested and don’t know what was applied previously, you could end up with serious issues. If the previous sealer was latex, you’ll get bubbling. I once saw a driveway that looked and sounded like bubble wrap.
“Watch your temperatures. I have installed sealer down to 35 degrees with my current manufacturer. We keep the sealer warehoused at 65 degrees in the fall and early spring. It’s transported and kept at 85 to 90 degrees until the moment it’s applied. We pour it into warm plastic pails, place them on a warm truck hood instead of cold concrete when applying.
“If you have an issue with your sealer — whether through installer error or bad product — get it corrected as soon as possible. Usually the fix is not as bad as you think.”
Who’s to blame when a sealing job goes bad? According to Bauer, most of the time it’s the contractor. “If I had to give a percentage … it would be 90 percent contractor problems and 10 percent product problems,” he says. “Most manufacturers restrict installations very tightly and offer clear directions to prevent call-backs.”