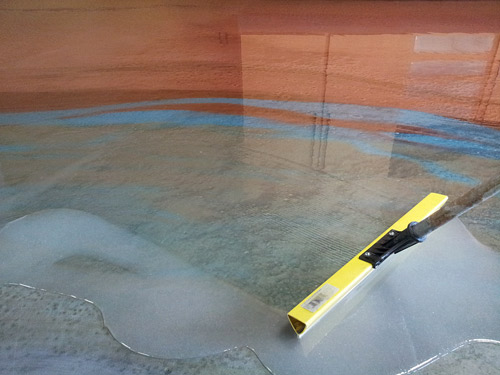
When a client calls me with a concrete flooring project, they are usually looking for a long-term solution. I usually hear, “Hey, its concrete. It will last forever!” While they are right that concrete will last a long time, the surface finish, color, and maintenance requirements all depend on the sealer of the finished concrete surface.
As an installer of finished flooring, you must become an expert on the floor sealing systems you offer. The client trusts you to offer the solution that works best for their unique application.
The market for concrete sealers is vast and it seems that there is almost every imaginable way to protect and enhance concrete floors. For the purpose of this article we are going to discuss two options that involve a clear sealer.
A clear sealer is used to enhance and protect integrally colored or stained concrete floors. You may use a thin-build (less than 10 mils total thickness) or thick-build system (greater than 10 mils total thickness). For the record, 1 mil is a thickness of one thousandth of an inch. For easy reference, 1 gallon of a product applied at 10 mils thick would cover 160 square feet.
Thin and thick-build coatings each have their respective parts in creating long-lasting and good-looking projects.
Thick-Build Concrete Sealers & Thin-Build Concrete Sealers
|
||
---|---|---|
S |
THIN-BUILD |
THICK-BUILD |
THICKNESS OF SEALER: | Less than 10 mils | Greater than 10 mils |
TYPICAL SEALER TYPES: | Acrylics, wax finishes, water-based products | 100-percent solids epoxys, polyaspartics, polyureas |
BEST USES: | Residential floors, light-traffic floors | Restaurants, hight-traffic floors, garages |
HOW IT CURES: | The sealers carrier, such as water or a solvent, evaporates | You get a catalyzed reaction by mixing separate parts together |
MAINTENANCE: | Reapplication of sealer | Mopping and rinsing, reapplication if necessary |
COST: | Lower initial cost, higher cost to maintain | Higher initial cost, lower cost to maintain |
Thinking thin
Thin-build coatings usually provide a more natural concrete look to the surface. For residential projects where floor traffic is going to be light or for commercial projects with a proper maintenance program, thin-mil systems are a great fit. The most popular thin-build systems include acrylics and wax-type finishes.
Cory Hanneman, owner of Element 7 Concrete Design, Marble Falls, Texas, has developed a thin-mil sealing process that imparts a natural look to the concrete floor. His process is a good fit for people who embrace concrete as something that will take on a great patina, he says. This sealing system’s final finish is an Italian beeswax that is worked into the concrete with a slow-speed floor machine. This type of finish ages well and can be maintained by an additional beeswax application five to 10 years later.
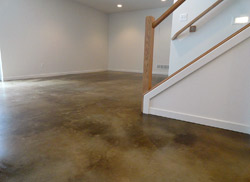
A thin-build system my company, Dancer Concrete Design, regularly uses is an application of a water-based epoxy followed by a water-based urethane. This system enhances the color of the underlying concrete while providing a soft satin finish.
Thin-build coatings are typically more affordable and easier to install than thick-build systems.
The majority of thin-build systems are also considered breathable sealers. This means they will allow substrate moisture to pass through the surface without peeling or delaminating the sealer.
Many applicators will put down an epoxy as a primer, then lay a urethane topcoat. A water-based urethane offers excellent abrasion resistance and UV stability but does not adhere well to concrete and will not offer color enhancement of the surface. A water-based epoxy will offer color enhancement when applied to a concrete surface but has low UV stability and can scratch very easily. By using a water-based epoxy as a clear primer with a water-based urethane topcoat you get the best of both worlds: A durable thin-mil system. This may be one of the fastest-growing indoor sealer applications, as it is a no-wax, easy-to-maintain floor.
Thinking thick
In commercial or industrial applications where there will be heavy traffic on the floor, thick-build floor systems offer the best protection and durability. An example of this would be a restaurant floor with a finished concrete surface in its dining area. This type of floor will be heavily trafficked, and what’s more, spills of food and drink will be a common occurrence. The best solution for this type of environment would be to apply a thicker-build sealer to protect the underlying concrete from stains and from wear patterns being developed in the finished concrete surface.
A recommended thick-mil system could incorporate a 100-percent solids epoxy base coat and be topcoated with a polyaspartic or urethane. Thick-build coatings are also chosen for their ability to impart a durable and deep gloss to a concrete surface.
Fernando Franco, owner of New Jersey-based Bodenkraft (formerly asssociated with Garage and Beyond) uses a thick-build system on his garage floor projects for maximum durability. He suggests using a thicker epoxy coating rather than an acrylic sealer or a water-based epoxy-and-urethane system, as thin-build sealers tend to wear down much faster than a 100-percent epoxy, especially in areas of the country where vehicles track in road salt.
The best thing to do when determining the proper sealer for the job is to understand the client’s needs and expectations for the finished concrete surface. It is our job as professionals to make sure we install the right type of sealer, set the expectations as to how the sealer will perform, and explain how to care for the surface long-term.