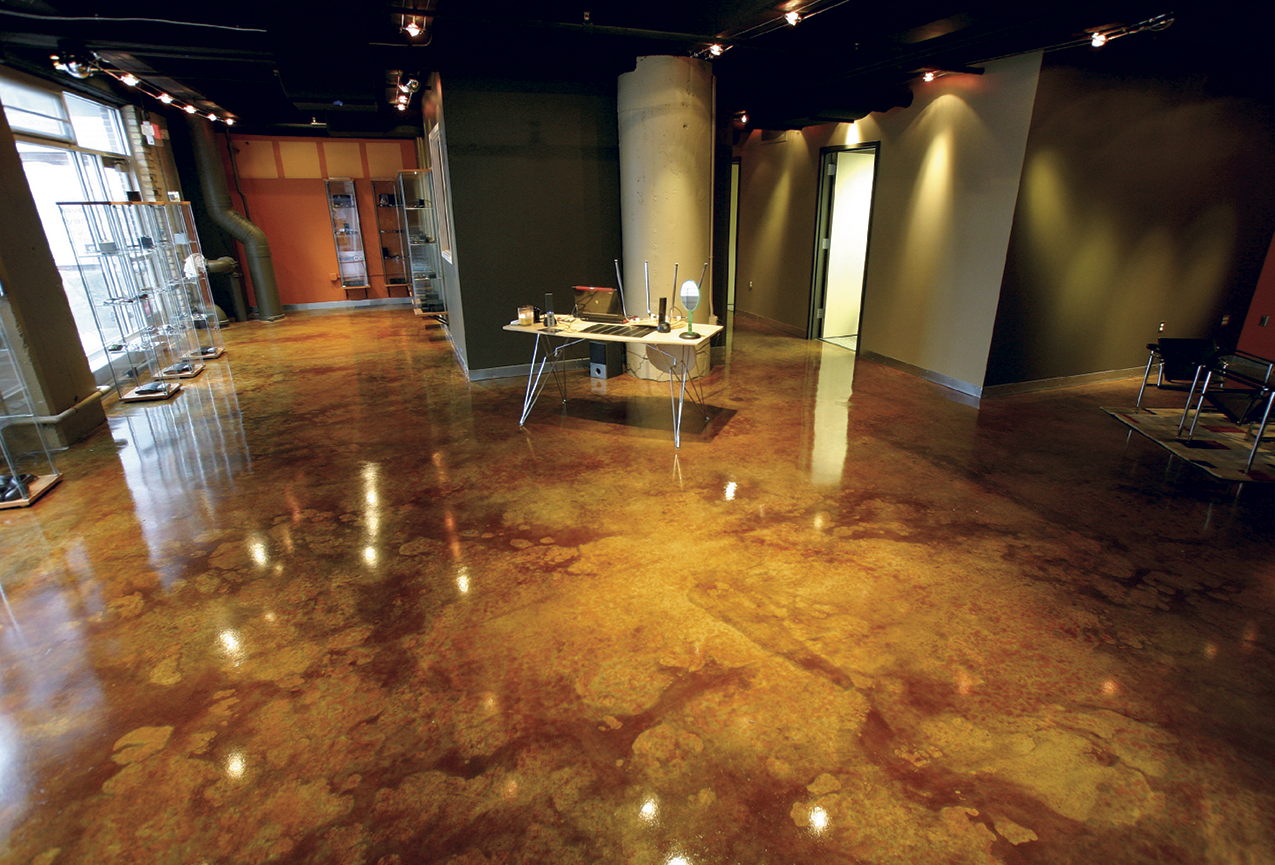
The 28-day curing time is standard in the concrete industry and comes into play on almost every project. “Wait 28 days before application” or “Concrete requires a 28-day cure before this or that can take place” — including the application of most decorative sealers, coatings, stains and toppings — is a common tag line. Is that because the concrete needs to have a certain strength, or is there something else going on?
The 28-day standard comes from decades of testing that’s determined concrete achieves 99% of its strength in 28 days. The American Concrete Institute, ASTM International and Portland Cement Association all reference the 28-day time frame as the accepted standard for measuring compressive strength. Really, it’s an arbitrary number based on concrete cylinder tests.
It’s also important because it sets a standard and establishes consistency in testing. Mix design and curing conditions have more to do with strength than a set number of days. According to “The 28-Day Myth” published by the National Precast Concrete Association, it’s estimated that concrete reaches 75% of this 28-day compressive strength in seven days, and its strength will remain stable or even increase over time.
Use a Type III-high early cement in your mix and you can achieve 3,000 psi concrete in 24 hours. Most ASTM testing lists a 24-hour, 7-day and 28-day time frame. All three are important milestones and provide information on how materials are performing compared to a standard. So why does the decorative concrete industry focus on 28 days?
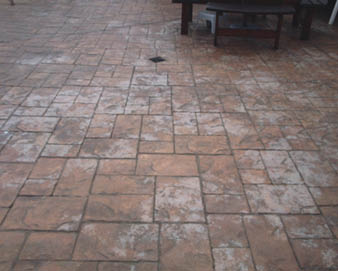
Moisture content matters
The answer is simple. Dry time! In decorative, as well other concrete industries, when applying a material to new concrete dry is more important than strong.
A great example is a liquid-applied curing compound or cure-and-seal. These materials are applied to green concrete as soon as finishing is complete. The concrete is only hours old and has very little strength. It is, however, loaded with water. The reason these curing materials can be applied while other products require 28 days is chemistry. They are designed to work in a wet environment, while sealers, coatings and most post-applied colorants are not.
It comes down to moisture content and occupying space. In the case of sealers and coatings, moisture can affect a product’s chemistry. In some cases a reaction with water takes place resulting in unwanted byproducts.
Polyurethane coatings are a great example. The isocyanate portion of a polyurethane will react with water and produce CO2 gas. These tiny gas bubbles can become trapped in the coating resulting in permanent white spots. Other coatings and sealers, like acrylics and epoxies, don’t react with water, but instead will trap moisture in and under the coating creating what is known as blush or haze.
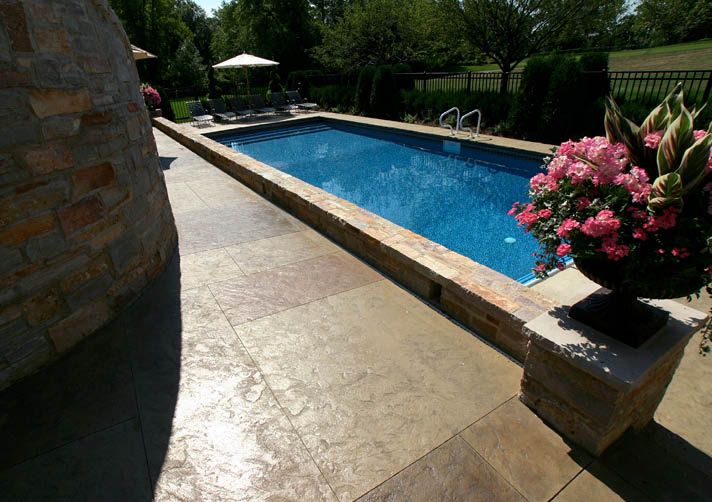
No vacancy
The other issue with excess moisture has to do with occupying space. Most post-applied colorants such as stains, dyes and color washes occupy space. They fill microscopic voids and pores in the concrete’s paste layer. If these spaces are occupied by water, there’s no place for the color to go, resulting in lowered color intensity.
The other factor to consider is hydrostatic pressure and equilibrium. As concrete cures, mix water evaporates. If a colorant is applied to concrete that’s still drying, not only will the color intensity be reduced because water is occupying those voids, but ongoing evaporation will carry color out of the slab.
This is the same process that occurs when dye is applied to polished concrete that’s been ground wet in a room with little air movement. The air above the concrete becomes saturated with moisture from all the water used in the polish process.
The floor and the air find equilibrium regarding humidity, which slows or stops the process of drying. Dye is applied to what appears to be dry concrete, but it’s actually a wet slab. Everything looks good until the HVAC is turned on. Then the dye suddenly fades or ends up as a dry dusty powder as the evaporating water carried it to the surface.
Visual inspection is not always a good indication. Surface-saturated dry is a phenomenon where the concrete is saturated with water, but the surface appears dry. Other methods for moisture evaluation may be needed.
Test to be sure
Dry time is not black and white. Environmental conditions have a significant impact on how fast concrete dries. This holds true for both newly placed concrete and an old slab being power washed for resealing.
Following the weather, especially humidity and dew point, can help determine moisture levels in concrete. This is especially true during spring and fall where large swings in temperature can take place. On larger-scale projects inside, I always recommend running some type of moisture test.
Next time you see a reference to waiting 28 days, it probably has more to do with allowing concrete to dry than strength. Understanding this can provide insight into how products work and when you may be able to push the hot dry conditions to allow for faster turnaround when drying comes into play.
Cooler temperatures with higher humidity can slow the process, even past the 28-day mark. It’s always better to spend a little time and run a test then rush into a project hoping for the best.