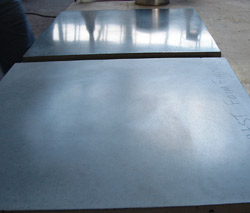
While doing some consulting for a cement company a few years back, I made concrete samples with portland cement and their cement, then strength-tested and polished the samples. In the process, I had the opportunity to correlate concrete strength with polishability and look at the effects of different densifiers on different concretes at different ages.
My first question was: How strong (in compression or psi) does concrete have to be to take a polish without densifier? Getting an answer for this one was pretty straightforward — 5,000 psi to 6,000 psi, depending on the aggregate. Concrete that was weaker (density is directly proportional to strength) would not take a polish as well because very small particles of aggregate would pull out of the matrix rather than being held firm and shaved flush with the surface during polishing. The problem was exacerbated in mixes containing glass (as concrete countertop makers would have guessed). The effects can be seen by viewing the surface through a small microscope.
I found that after a time I could actually work backwards and estimate psi based on polishability. My educated estimates reminded me of a story my father told about working as a spark tester for a steel company. He was trained to differentiate different scrap metals by the spark they threw when touched with a grinder. I’m sure that experienced polishers can evaluate a floor very quickly once they start polishing. I think they can do it before estimating the job.
Matching densifier to concrete
The next question was harder to answer: Very few projects are going to specify a minimum compressive strength of 5,500 psi just so the floor can be polished without using a densifier, so densifier will likely be needed, but what type of densifier works better on what concrete?
Some overlay products do not contain portland cement. With the use of pozzolans in concrete, there is less reactive free lime for conventional densifiers to work with. There are also very weak floors (some almost like hard sand in their density) being rescued by floor polishing.
The answer is that all densifiers work, but some work better than others in different situations.
Pozzolans and densifiers do some similar things. The majority of products added to mixes or used as densifiers are silica-based. Pozzolans have a silica component, slag is about 40 percent silica depending on the source, and silica fume is about 95 percent silica. The smaller the particles are, the faster they react — in many cases they‘re small enough to actually act as accelerators rather than retarding the set.
Many polished concrete products are also silica-based. It started with sodium silicates, then came potassium silicates, and now we’re on to lithium silicates and colloidal silica. Sodium and potassium silicates have a metallic salt component, which is why they can cause efflorescence if overapplied either as an admixture or topically as a densifier. (Lithium silicates also have a metallic salt component, obviously, but are less likely to white out.)
Why does one floor white out when another did not, even though I applied the densifier the same way? The answer may have been differing porosity and amounts of free lime in the floors.
If your floor is dense and has enough free lime to work with, lithium silicates or colloidal silicas generally work fine. If your floor contains very little free lime (was cast with a very high pozzolan dosage), is weak psi-wise or very young, you may need to look for alternatives or in many cases a combination of alternatives.
Colloidal silica is pure silica with a particle 100 times finer than silicates and 1,000 times finer than silica fume (which is finer than tobacco smoke). Silica fume is 100 times finer than portland cement — you get the point. This is why colloidal silica reacts quickly when used internally — as an admixture it becomes a pozzolan and an accelerator — or externally, because as a surface densifier it begins to gel almost upon contact. It will also form bonds with silica, which is important on floors with little free lime to work with or overlays with no portland cement.
If your floor or overlay contains no portland cement, if your floor was cast with a high percentage of pozzolans, if your floor is young (calcium hydroxide needs time to develop internally), or if you have a decently hard floor in good shape and you don’t want to use diamonds, colloidal silica would be a good choice.
I prefer a colloidal silica engineered to contain a range of particle sizes (from 1 nanometer to 100 nanometers) at a specific pH to prevent molding. Our research has found this to be more effective and efficient than typical colloidal silica densifiers, which contain a narrow range of particle sizes. It’s particle packing on a “nano” scale. The range of particles fit the pores in a floor like locks in a key, allowing the contractor to densify a broad range of floor types. The problem is when the key is too small to fit the lock — the colloidal silica can disappear into the concrete without affecting the surface.
Many of our customers are using a 50-50 blend of our lithium silicate product and our colloidal silica product. I look at this as covering all bases. You end up with particle sizes with chemistry to cover most situations. We will preblend this for you or you can blend on-site.
Dealing with porous floors
Compared to problem floors, dense, high-strength concrete requires little help from surface densifiers before polishing. However, when concrete is cast with high degrees of excess water, the water leaves channels behind when it evaporates out of the concrete. The more excess water in the mix, the larger and more frequent the channels and the weaker the mix (meaning less ability to hold the aggregate so the polishing machine can shave it rather than pulling it out). This is the main reason most polishing concrete contractors stay away from the residential market — less quality control with the concrete. You don’t know what you’re walking into or how much it will cost to get it polished if it will polish at all.
You will need to start with the largest particle required to fill the pores and work your way smaller to fill the voids, densify, and provide a uniform plan for polishing. Sometimes this can be accomplished in one step, sometimes not.
Very weak, porous concrete may require a very large particle in the form of cementitious slurry prior to any attempt at densification. The concrete may be so porous that any densifier will simply absorb into the matrix without benefiting the surface. A “neat” reactive slurry (with no sand or aggregate in the mix) will close the very large voids. This may need to be ground off before going to the next step, which would be larger particles (lithium silicate) mixed with smaller particles (colloidal silica). A final step (if needed) would be colloidal silica — this would bond to any silica particles present and fill any microscopic low spots, readying the concrete for final polishing. Obviously you’ll use more products and spend more time on machines than when polishing dense concrete, which often makes this option more expensive than coating the floor with a film-type product.