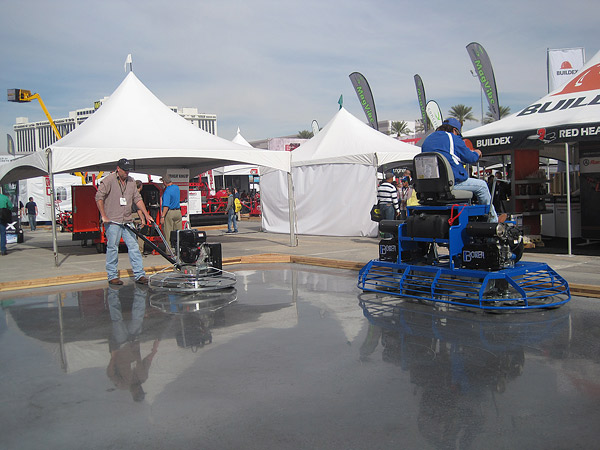
As a consultant, I am asked questions regarding all facets of concrete construction. I freely admit I don’t know everything there is to know. However, I try to learn something new every day about concrete, in particular about issues that affect finished concrete flooring.
As a result, I have a wide variety of knowledge about the concrete industry in general. This knowledge sometimes allows me to put pieces together from different sections or trades to get a clearer picture of what needs to be constructed so my customers get the best possible outcome. With that in mind, I want to address the topic of concrete placement.
There is too much information to completely cover in one article, but with a three-part series I’ll address three key issues related to concrete placement and discuss how these items can affect finished floors. I believe a better understanding of these specific components of concrete finishing can help decorative contractors better manage their projects’ outcomes.
In this sequential series, I’ll address three specific areas in the order they can affect the outcome of your project. First is the actual finishing level of a new concrete placement. The second issue is concrete curing and its effects. The third issue will relate to mix designs.
Trowel first
Today, most slabs are finished using mechanical trowels for the body of the slab and hand trowels for the edges. There are two basic types of mechanical trowels: walk-behinds and ride-ons.
Walk-behind trowels are the most common. Positioned flat on the slab, these basically look like a fan protected by a wrap-around cage. Like a ceiling fan, the blades are tilted slightly. The blades spin in a clockwise motion.
Ride-on trowels have two counter-rotating heads with a cage, motor and a seat for the driver. The counter-rotating force allows the driver to control the direction. As one head speeds up it turns the trowel in that direction. Skilled trowel drivers can use this rotational force to get close to pipes, slab edges or walls.
The tilted blade, along with the rotational action, depresses the sand aggregates at the top of the slab and pulls up portland paste. This paste is carried from between the slab’s filler aggregates to the surface. When a slab is complete, the surface paste is generally about 1/8 inch thick. When the paste is initially drawn out, the surface is open and porous. Additional troweling as the concrete starts to stiffen compacts this paste into a dense surface layer.
When the concrete is open and porous, people in the placement industry generally refer to it as “fuzzy.” This type of finish is not conducive to polishing or most other decorative finishes. The large number of open pores allows the concrete to be easily penetrated by moisture, which can create issues for any type of color application. The open pores allow the pores’ edges to break during the grinding process. Without additional filler, these types of slabs are unpolishable.
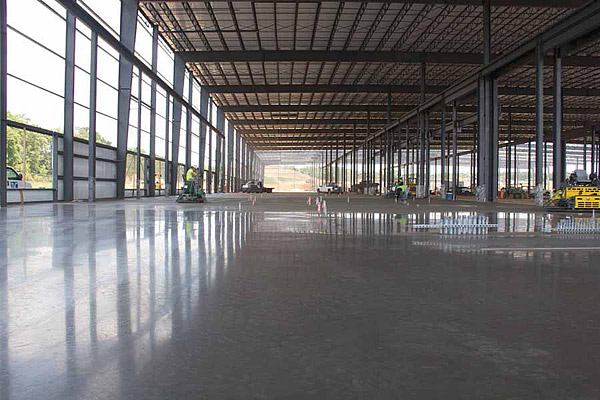
When concrete has been compacted and has stiffened, additional troweling creates excess friction, with heat as a byproduct. The heat melts small particulates of sand on the surface and turns them into a type of glass. Additionally, the heat buildup scorches the portland particles, turning the slab dark gray to black. This process is called “burning” the finish. The floor is very tight here, but don’t be fooled by the glassy finish. This floor won’t hold up to traffic for very long before the tight finish and paste surface start to wear away.
Finding the sweet spot
An ideal finish for polished or decorative concrete is the sweet spot between fuzzy and burned. At this point, the concrete is about as tight as you can get it without having a glass-like buildup on the surface. The only time concrete slabs get compacted and tight are when they are troweled. A tight slab is better to polish.
As an analogy, consider rocks. It’s much easier to polish dense, tight granite than it is to polish porous or rough limestone or pumice rock. The tighter the slab, the better and stronger the polished surface will inevitably be.
With that said, burning a slab is extremely counterproductive when you’re doing a polished concrete finish. The glass finish is not a great surface to grind. The smooth texture doesn’t allow the cutting process to grab the concrete. Generally, additional steps of lower-grit grinding pads are necessary to break through the burnt surface. This results in extra time and expense in tooling costs for the polishing contractor with no discernable long-term benefit.
When I talk to concrete placement contractors, I tell them, “In a perfect world the slab would be finished as tight as possible and the troweling would stop right before the slab started to burn. I understand we don’t live in a perfect world, so I would rather have the finish be tighter than too open or porous.”
By discussing this issue with the concrete placement contractor, you’ll get a much more suitable finish for whatever decorative process you’re installing on the interior floor. Without having these discussions, you’re leaving your project open to the concrete contractor’s idea of what is the correct finish.
As a word of advice, addressing these issues as early as possible is the best plan. If you wait until shortly before concrete is placed, the contractor will already have developed a plan based on whatever requirements are covered in the specifications.