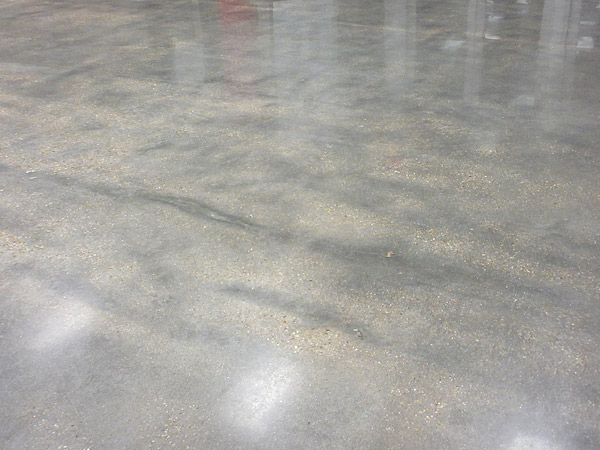
Floor flatness (FF) and floor levelness (FL) are measurements by which architects can hold concrete placement contractors accountable and provide a quality control level during the initial placement of concrete slabs. There is a difference between the two.
When explaining this to my customers, I often use a pool table as an example. A flat surface will provide a smooth roll but if the surface isn’t flat, the balls will bump along at seams, tears or debris. If the table is flat but not level, the balls will roll smoothly but curve naturally to the lower side. This can apply to concrete slab placements as well.
You can have a very flat slab that’s not level or you can have a level slab with elevation variances so the surface isn’t flat. The FF/FL requirements for the project are called out in The Construction Specifications Institute’s 03300 specification section on concrete placement. Almost all commercial slabs placed today have FF/FL requirements. Generally, there is a testing service that performs FF/FL testing right after placement but before saw cuts are made. This is mandated by ACI standards and the specifications for the project. I recommend you review these specifications for concrete placement on any new construction project that you work on.
Higher and more consistent FF means better profit
As a polished concrete contractor, you should be much more concerned with the FF number than you are with the FL number. The better the FF readings are the more consistent finish you can provide your customer. The FL numbers are less important to polished concrete contractors because you can evenly grind the surface whether the slab as a whole is level or not. The FL reading is much more important for other trades like framers and roofing contractors who have to deal with the building envelope.
I work on a lot of projects each year as the owner’s rep. In some cases, the building is being built by a developer or some entity where I, as the owner’s consultant, do not control the specifications. When this occurs I have seen FF numbers all over the board, with the lowest an FF 25. This extremely low number generally results in many random high and low spots highlighted by the concrete polishing process.
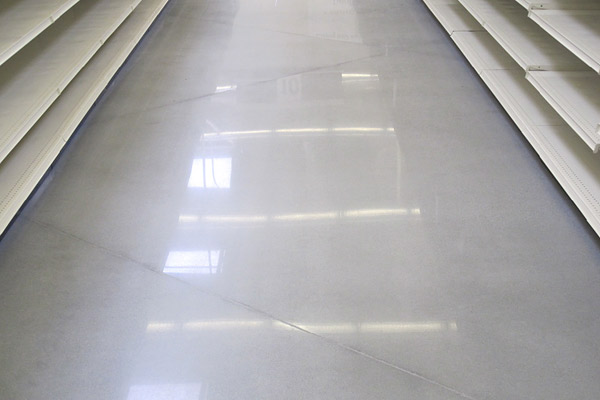
The highest number I generally see is an FF 70, which is considered a “super-flat” floor by ACI. These slabs generally are very uniform in the depth of grind and have a very even aggregate exposure. If you have input on the specifications, I recommend a 45 FF average or better. This generally requires the placement contractor to use a laser screed machine during the concrete placement.
If the specified or test results show the FF readings are below the 40 range, you must assume you’ll use about 20 percent more diamonds during your metal bond steps. This is a result of the grinders attempting to cut off the high areas.
You also must assume you’ll need to use a grout fill in some areas where larger aggregates are exposed. These aggregates trap air during the placement process, resulting in air voids when you expose the concrete to that level. You also should plan for some extra hand grinder and machine time to grind into the lower areas. Sometimes these are impossible to get to with regular grinding procedures. I also find a lot of scratches that need to be worked out as well as resin burns caused by the elevation changes during the grinding process. I routinely see change orders for low FF floors.
When you have a high FF floor you can count on reduced tooling costs and reduced labor costs because the machines will grind the floor evenly and quickly. On large “super flat” floors, contractors generally have great results and are able to make better margins even at a lower price per foot.
Be prepared
Once the concrete is placed, it’s extremely important that the polishing contractor ask for the FF/FL report as it can be an early warning sign of issues to come. If the FF/FL readings don’t meet specification requirements, you can prepare for this ahead of time. That could include budgeting extra time and materials, providing the GC with a change order for the additional work and preparing the customer for the results in the finished product.
The placement contractor is responsible for providing a foundation slab. The polished concrete contractor is responsible for taking that slab and turning it into the finished floor. If customers are expecting an even aggregate monolithic finish and the end result is a randomly textured surface with light and dark areas and larger rock exposed in sections, the first person they contact to discuss their displeasure is the polishing contractor. If the customer is warned of this potential ahead of time it relieves a lot of stress, places the responsibility on the contractor that is underperforming and ensures all parties are compensated and satisfied with the results provided.
It’s important to remember there are specific guidelines for performing these tests. You are unable to count results that are along the edges of a pour (so address the edge finishing separately) and you are unable to count readings taken around stub ups for electrical or plumbing (preplaced conduit below or in the slab for electrical wiring or plumbing to be installed later, such as plumbing for a toilet). The testing equipment needs to be calibrated properly and operated by a professional.
Recently we had a customer’s pour that was extremely well placed by the concrete contractor. A laser screed was used and the requirement for the floor was FF 50. The testing showed that the floor averaged out to an FF 37, which didn’t meet specification requirements. During this project’s investigation phase, we figured out the testing contractors had not properly calibrated their machine. When we retested the floor the average was in the 60s. I share this story to relay, “sometimes even testers make mistakes, so use your judgment.”
If you are on a large remodel it may be worth the few hundred dollars it costs to have the floor tested for FF/FL prior to starting work. The FF/FL levels can severely affect your pricing. I see a lot of contractor paperwork where minimum tolerances are called out as part of the bid. For example, “This bid is based on a minimum FF average of 50. An average below 50 may increase the cost of polishing the floor.” This inclusion protects the contractor and ensures the owner is aware of the issue.