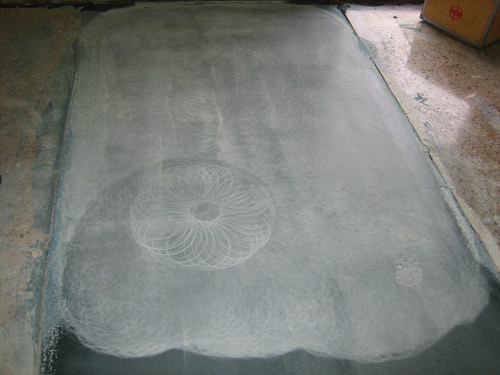
Self-leveling overlays that are polishable have been around for about years now, but only in recent years have they really gained traction in the retail and residential markets. Over the last seven years I have been fortunate enough to work with eight different self-leveling manufacturers, successfully using almost the same grinding-polishing system on all of them.
Let’s cover what I know is a proven system for polishing self-leveling overlays. Then I’ll talk about issues that I have seen over the years on these floors when things go wrong.
First: the cream
The basic idea of the first step with most overlays is to make sure you get the skin/cream off the top surface. The reason for this is that the highest concentrate of polymers will be in this top layer. When you are using resin-bonded diamond tools, toward the end of the process you will get a burning or discoloration as a result of basically plastic-to-plastic contact creating excessive heat. So by going aggressive on the first step you will remove this polymer layer and get down to the body of the material that will give you a more uniform and monolithic look.
This aggressive first step is also necessary if you need to expose aggregates that are either in the mix or seeded while it’s still wet.
It may be necessary to start with a 40-grit metal bond if there are aggregates in the mix, while in most cases starting with an 80-grit metal bond will be enough if you are seeding aggregates or simply removing the skin for floors without aggregates.
Normally it’s necessary to make a double pass (north to south, then east to west) with your first grit. It’s imperative that you do not leave the metal-bond stage until the skin and all low spots have been removed.
Also, the sooner you start grinding after the overlay was installed, the harder the bond of metal tools you need to use. So for example, if you are grinding 24 hours after the floor was installed, use a C or CA series tool that is normally for softer concrete. The longer you wait the harder these overlays get. If you wait a week or two before you do the initial grind, you might need to use an SF or CX metal-bond tool for harder concrete. You can also perform a surface hardness test based on the Mohs hardness scale to help you select the proper tooling.
In order to make a profit when grinding overlays you have to choose the correct metal-bond tool that will cut efficiently yet give you good tooling life also. Overlays are full of silica sand that is very abrasive on your tools, causing them to wear very fast. So keep a watchful eye on tooling life and be prepared to move to a harder bond or combo if necessary.
Next: the hybrids
After your 80-grit metal bond step is complete, it’s best to use a transitional or hybrid type tool of 100 grit to make the jump from metal to resin-bond tools. This tool can be copper, ceramic, or even diamonds coated in a metal bond and placed into a resin bond. Either way these work best to remove the metal-bond scratches and prep the floor for the resin-bond stages.
This step can normally be done with a single pass in a direction opposite the one you took with the previous metal-bond step. However, be prepared to do a double pass if you do not remove all the deep metal-bond scratches with a single pass.
I want to give a heads-up to all the concrete polishers who are considering trying their hand at polishing self-leveling overlays: Trying to read the scratch patterns on the first few steps is much more difficult on overlays than concrete. Don’t get frustrated. Just continue on with the system and you will start to see the pattern as you go to the resin stages in the third step.
Also, make sure you always relieve head pressure when you start and stop the grinder. Overlays are more susceptible than concrete to difficult “start” and “stop” scratches.
The honing stage
Now it’s time to start the honing stage. Here at HTC Inc., we use our 200-grit Fenix pads to make the jump from hybrid to resin steps to remove the scratches from the hybrid-type tools. The HTC Fenix pads were specifically made for polishing overlays. Other manufacturers have made similar products, so ask your tooling supplier for more details. Fenix pads are available from 40 grit to 3,000 grit. If you try to use standard resin tooling designed for concrete polishing you will experience a burning or discoloration from the polymers, even if you properly remove the skin with metal bonds. This step will show all the sins you committed with the metal or hybrid tools.
If you still have these deep metal-bond scratches after the 200 grit, you need to go back to your 100-grit hybrid-type tool and make another pass.
Densifying and polishing
If not, it’s time to densify and move on to the 800-grit pads. (Check with the manufacturer of your overlay to make sure it’s even beneficial to use a densifier and at what stage it’s recommended to apply it.) One hour is normally the absolute minimum that is required to let the densifier cure before you move to the next step. At this point we are exiting the honing stage and entering the polishing stages.
After the 800 grit we move to the 3,000-grit pads for the final polish.
This standard five-step system will normally yield gloss readings in the high 50s to low 60s (roughly, the minimum for a reflective floor) before the stain-protection guard product is applied at the end.
Most specifications for retail chains only ask for an overall minimum in the low 40s and overall sustained average in the low 50s. (All gloss readings are based off a 60-degree gloss meter.) If you are trying to get higher gloss readings, like at a high-end residential job, then simply do not skip any of the pad grits. Your standard five-step system turns into a seven- or eight-step system.
Fixing problems
Let’s discuss some of the problem floors, when things went wrong. Most if not all problems caused by the polishing contractor can be removed or fixed by grinding deeper on the first step, backing up to the previous grit that caused the problem, or spending more time with each grit to achieve maximum refinement.
Those problems are normally random scratches left from the metal bonds, low spots from not spending enough time with the first-step metal bonds, start and stop marks from not relieving head pressure, or lines in the floor from moving either too slow or too fast on the first cut. A recommended forward walking pace would be around 8-10 linear feet per minute.
Problems caused by the overlay installer are as follows: leaving spike roller marks, using football- or soccer-style cleats rather than proper spike shoes, and line marks from a smoother trowel.
If you are the polisher and are the recipient of roller marks, cleat marks or smoother lines, you have a very limited number of things to try. Simply grinding deeper might get rid of these issues in some cases, but not in others. I have also seen contractors use dyes to try and mask the spike roller marks or smoother lines. This can work, but it really depends on how bad the marks and lines are and how skilled the sprayer is.
There is a very fine line when trying to grind deeper to remedy one of these problems. At 3/8-inch thickness you obviously are at risk of grinding through to expose the substrate below. When this happens, cutting out a section and repouring will be necessary. If the bad area is near a control joint, you could just remove the entire section and repour, or saw-cut out the bad area and repour.
Make sure to call the manufacturer of the overlay that you will be polishing and have them recommend a qualified installer of their products. The installer of the overlay sets the stage or creates the canvas for you as a polisher to work from. They can make your job very easy or extremely stressful.