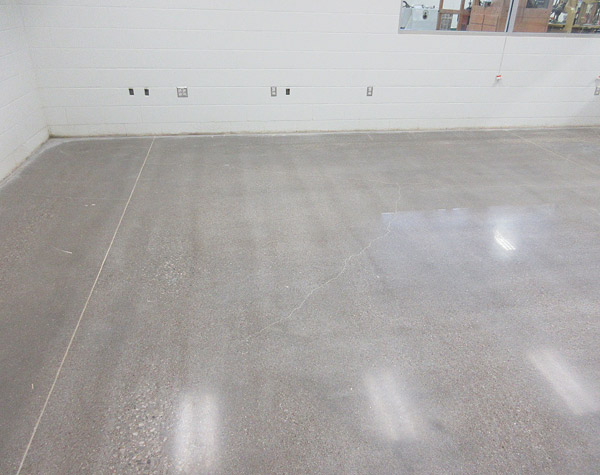
Repairs are always tricky. The idea is to get them done as quickly as possible with a remedy the customer will buy. By selecting the correct process and products, you can control how long the repairs will take to complete. Customers’ willingness to accept repairs is determined by understanding their expectations and letting them know early on if their goals are achievable.
All damages or problems generally fall into a few categories. They can be caused by the decorative contractor, by other trades during construction or, in the case of remodels, by existing conditions that need to be addressed.
Self-inflicted problems
Damages caused by the polishing subcontractor are generally the easiest ones to fix, but they can be painful because there’s no one to charge back the time and materials spent on repairs. The most common mistakes are scratches from the grinding process, streaks or overspray from the application of colors, or issues related to edge grinding.
The only way to repair scratches is to physically remove them by regrinding. Color issues can be corrected by using bleach to kill the color, which will take the concrete back to gray. Dye can then be reapplied. To make it easier, reapply the dye from joint to joint as it’s sometimes hard to blend it in an area with no joints. Edge grinding issues are usually repaired by starting the grinding process over and working out the scratches.
One thing that seems to bite contractors every time when it comes to these types of repairs involves the application of stain protection. When stain protection is applied, it makes performing any repairs much harder. You should review the floor in phases to note potential repair areas prior to installing stain protection. Repairs done prior to stain protection generally take about half the time to correct.
If stain protection has already been applied, don’t make the mistake of attempting to grind it off. You will almost certainly have to drop to 100-grit resin or lower to get below the stain protection. First, attempt to chemically remove the product without affecting your mechanical polish. Most major chemical manufacturers offer a “stain protection stripper” that works with their product. If you chemically remove the stain protection, you’ll find the repair much easier to do.
Generally, customers aren’t very forgiving when it comes to contractor-caused mistakes. If something you do is going to change the repaired area’s overall look, review this with the customer first. For example, if you’re trying to remove deep scratches you might expose more aggregate and cause the corrected area to stand out. Discuss this possibility with the customer and offer ways you could limit the degree of variance, such as grinding joint to joint to create an intentional color shift. This way, the area looks like it was architecturally designed to be different.
The culprit: Other trades
On most new construction projects, I see polished concrete damaged by other trades. Painters, carpet installers or men on lifts are the usual culprits. The ensuing repairs are normally charged as change orders to the GC, who back-charges the subcontractor responsible.
Generally, paint can be corrected by first scraping it off and then lightly regrinding the surface to bring back the shine. Smeared carpet glue can usually be corrected easily by removing the transition strip separating the carpet and concrete, scraping off the glue and then lightly polishing the area. Chips are the hardest to repair but I’ve had success installing color-matched grout fill products and then repolishing the area.
All three of these types of repairs are best made before applying stain protection. It’s in your best interest to hold off on the application as long as you can and when polishing is 100 percent complete.
After stain protection is applied, I ask contractors we work with to take copious photos of each phase of the project. If damage is done later, pictures will help get customers or contractors to approve change orders for repair. When damage is caused by someone other than the decorative contractor, the GC will work with you to manage the customer’s expectations. I always recommend doing a sample of your repair so the owner has a very clear understanding of what you are proposing to install.
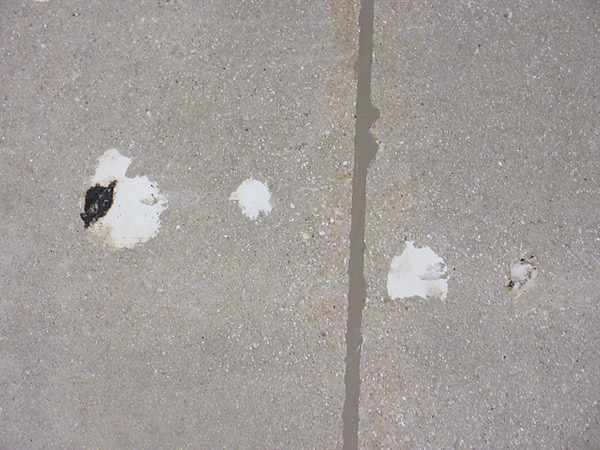
Dealing with remodels
When dealing with remodels, there are almost always existing conditions that weren’t visible until the grinding work occurs. The most common issues are existing fill-in spalls or low areas, trenches that were poured using concrete that’s unpolishable and cracks that need to be filled. These are generally covered by another flooring type that’s removed for polishing.
Remember, underlayments are designed to be covered by another flooring type and are unstable when exposed to traffic or cleaning. Generally, they will turn chalky and soft, creating safety and maintenance issues if they’re left in place. In the projects we manage, we require all underlayments or existing fill be removed.
For small holes, there are many good spall repair products that can be colored to closely match the existing concrete. For larger areas, use a polishable overlay, which generally requires prep work to ensure a 3/8- to 1/2-inch depth prior to installation. Trenches that need to be addressed can either be polished after installing a grout repair product or after the floor is prepped and a polishable overlay installed. Overlays can be pricey so provide your customer with a separate estimate for approval before you start.
Cracks can either be cleaned and filled as they are or chased with a saw and filled. I determine the method based on the traffic. For light retail traffic, I usually just clean and fill the existing crack with a matching colored material. For heavier industrial traffic, I require the cracks to be chased and filled to ensure they don’t spread or get wider with the heavy loads.
In conclusion
To recap, there are many different methods to perform repairs. One thing that’s true with all repairs is they’re easier to complete prior to applying stain protection. If stain protection has been applied, it is easier to chemically remove it than it is to mechanically grind through it.
Go over the consequences of your repairs with your customers so they understand what to expect. It is always easier to under-promise than to recover from an unrealistic over-promise. When managed correctly, repairs are easier, quicker and much more acceptable by your customer.