There are new profit opportunities in polished concrete for the decorative concrete contractor. This is a fact, and every decorative concrete contractor should look into polished concrete. However, nothing ever caused more people to go broke than too much optimism and too little planning.
You are probably getting very tired of hearing that everything is green. The sustainability movement today seems ubiquitous. There’s even a term for this: greenwashing, which Greenpeace defines on its anti-greenwashing Web site (www.stopgreenwash.org) as “the act of misleading consumers regarding the environmental practices of a company or the environmental benefits of a product or service.”
I tried to think of the least green thing I could to see if it too was being touted as green — how about gasoline? You’d think there wouldn’t be a way to portray gasoline as green. From oil production to transport to emissions from burning the stuff, there doesn’t seem to be much room for being green. So I did a Web search and, lo and behold, found an online article devoted to, you guessed it, green gasoline. It’s almost like the recent barrage of political talk: If you say something enough times people begin to believe it whether it’s true or not.
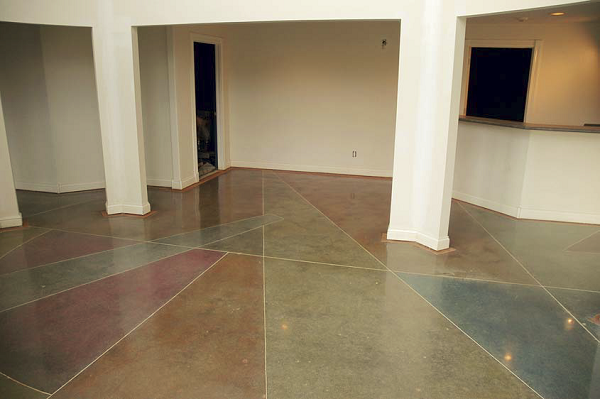
All that should make it pretty easy for us to declare concrete green. If everyone else is greenwashing their products, why not us? The real bottom line is that many products and construction materials can be considered green if used in the right way, to contribute to durable and efficient use of the world’s resources. The danger, though, is that as manufacturers greenwash their products, architects and owners have become cynical about any claims of environmental benefits. So when they ask for proof, be ready.
The good news is that we don’t have to greenwash concrete, because there are many ways that concrete as a construction material honestly contributes to green — sustainable — construction. Although we can’t and shouldn’t try to gloss over the fact that the production of portland cement and the mining of aggregate are not gentle, environmentally friendly processes, we can show those looking for ways to make their buildings greener that the benefits of building with concrete outweigh the impacts. To do that, though, it’s not enough to try to make concrete less bad. We have to look at the life cycle of the material in a way that is more organic and less industrial.
Architect William McDonough calls this evolution, this new paradigm, “cradle to cradle,” since we are talking about recycling rather than disposing. In his book, “Cradle to Cradle: Remaking the Way We Make Things,” he points out that “when designers employ the intelligence of natural systems — the effectiveness of nutrient cycling, the abundance of the sun’s energy — they can create products, industrial systems, buildings, even regional plans that allow nature and commerce to fruitfully coexist.”
Concrete is a perfect material for this philosophy of green construction, since it is basically man-made sedimentary rock. Concrete is eminently recyclable as road base or fill or even as aggregate for new concrete. In building interiors, once hardened, it is basically inert — no need to worry about toxic off-gassing. Concrete’s ability to store heat and thereby dampen temperature swings in a building can reduce the size of heating systems when creating comfortable homes. But concrete’s greatest contribution to sustainability is its durability. With smart design, a concrete building will provide safe shelter for its residents from any natural or man-made disasters for at least 100 years — the Pantheon’s concrete dome still stands in Rome nearly 2,000 years later.
So that’s my standard concrete greenwashing pitch.
Tell all this to an architect or building owner and their eyes will begin darting around as they look for a way to escape another green sales spiel. What they should do is ask a simple question: How can you prove it?
The way to prove it is with numbers. We live in a world where everything has to be quantified — how big, how fast, how strong, how green. And that leads us to LEED.
You have undoubtedly heard of LEED, which stands for Leadership in Energy and Environmental Design, a program of the U.S. Green Building Council (USGBC). This is one — not the only, but the most referenced — rating system for quantifying just how green a building is. Under LEED, you do this and you get a point. Do that and you get another point. Get enough points and you can call your building green.
If you haven’t yet been involved in green building, you will be. Cities, states and countries around the world are mandating green attributes for new and retrofit construction. According to the USGBC, as of Oct. 1, 2008, LEED initiatives have been adopted by 163 localities (107 cities, 29 counties and 27 towns), 31 state governments, 12 federal agencies or departments, 15 public school jurisdictions and 39 institutions of higher education across the United States. And that’s just the beginning.
Let’s look briefly at how concrete helps a building gain points under the LEED program. In subsequent “Green Matters” columns we will explore some of these factors in detail and also look at the other rating systems.
An introduction to LEED
Today there are nine approved LEED programs, for projects such as new construction, homes, schools, healthcare facilities, and even neighborhood development. Each of these has slightly different requirements, all with the goal of reducing a building’s (or an entire development’s) environmental footprint.
Each LEED program includes categories for such things as site selection, water efficiency, energy usage and indoor air quality. Points, up to a total of 136 possible, are awarded for attributes of the construction within each category — sometimes very specific attributes.
Take, for example, water efficiency in LEED for Homes. You can earn a maximum of 15 points for water efficiency. Within the water efficiency category, Section 1 is Water Reuse, which can earn a building up to 5 points. To get all 5 points, the building would need to have a rainwater harvesting system and a gray-water reuse system. For rainwater harvesting, you would need to design and install a system to collect and store all the water from a 1-inch rainfall — equivalent to 0.62 gallons per square foot of roof.
As a decorative concrete contractor, your most likely contribution would come from improving indoor air quality. Unlike carpeting, concrete floors emit no volatile organic chemicals. Concrete can’t get moldy and it also seals out radon (when there is a good vapor barrier). But finding where you get credit for this in LEED isn’t simple. First you look in the Indoor Environmental Quality category. That refers you to the Environmental Protection Agency’s Energy Star Indoor Air Package. There you find, in Section 6.7, Building Materials, this requirement: “Install water-resistant hard-surface flooring in kitchens, entryways, laundry areas, and utility rooms.”
Is that convoluted enough for you? Does it make you want to just give up? LEED isn’t perfect, and it doesn’t completely incorporate the cradle-to-cradle philosophy. But it is what most designers are using today to prove that their buildings are green. So you need to be ready to show them how concrete can help them with LEED points. In the next issue we’ll get more specific on how to do that.