On of the advantages of landing a contract for several polishing jobs is that the later ones can improve on the minor missteps of the earlier ones. A recent pair of jobs for the Yakima, Wash., School District is a classic case in point.
In 2009, voters in Yakima approved a $218 million facilities improvement bond for their school district. In addition to upgrades and repairs throughout the district, the bond funded three major construction projects — replacement of Stanton Academy for the 2012-2013 school year, replacement of Eisenhower High School, known as “Ike,” for the 2013-2014 school year and a major remodel of A.C. Davis High School for the 2015-2016 school year.
For all three projects, the school district chose polished concrete for floors in the high-traffic areas of the buildings. Lundeen Simonson Inc., of Spokane, Wash., did the polishing on both the Eisenhower and Davis projects.
After dealing with scheduling problems and a damaged slab at Eisenhower, Lundeen Simonson staff approached the A.C. Davis job determined to make use of what they’d learned. Applying the lessons of Eisenhower — and some ideas that had worked well at Stanton Academy — has made A.C. Davis a much better polishing project for everyone involved.
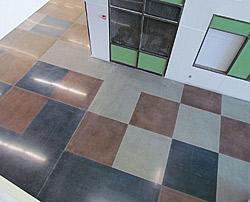
An acre and a half of challenges
Eisenhower, Washington’s biggest high school, was a 70,000-square-foot job that posed challenges because of the size of the project, problems with the new slab, and elements of the design.
“When we get into the 60,000-to-80,000-square-foot range, you get into a whole other level of challenges,” says Skyler Owen, Lundeen Simonson’s project and sales manager.
And so it was with this new pour. “The placement wasn’t so great,” Owen says. “It wasn’t very flat, and there’s a lot of cracking and damage to the floor.”
Architect Ryan Monson of KDF Architecture (Yakima, Wash.) originally envisioned dyed rectangles in the floor accented by a grid of saw cuts filled with grout. But when it became apparent that the grout lines would increase maintenance work, Monson modified his plan.
The original design also incorporated crushed glass broadcast over the surface after the pour. But when Lundeen Simonson did a mock-up slab on the site, workers discovered that it was hard to get the glass to feed consistently over the surface, so that feature was dropped from the design.
Eisenhower’s construction schedule allotted 10 weeks for concrete polishing which were slotted late in the project. “We ended up working around finished walls,” Owen says. “All the other trades were in our way.”
When they started polishing in April 2013 — more than a year after the pour — Lundeen Simonson’s crew discovered that the slab was unusually hard. It also had sustained damage from previous construction operations. “You want a hard slab,” Owen says. “But it was hard and not flat.”
“We tried dry grinding. We tried different combinations of tooling and super-soft diamonds,” Owen says. Eventually, Owen’s team decided that wet grinding, using HTC 800 HDX planetary grinders with that company’s EZchange tooling, was the only way to achieve a satisfactory finish. “If you switch over to wet grinding, nine times out of 10, that solves all your problems,” he says. “It keeps your diamonds cool, softens the concrete a little, and allows the tools to stay open and work. And it provides protection (from silica dust) for the people.”
Slurry disposal on a 70,000-square-foot job was a significant task. Lundeen Simonson worked out an agreement with the contractor to dispose of the slurry in its washout pit. An estimated 20,000 to 25,000 gallons of slurry was collected in barrels, which were emptied into the pit.
When it was time to stain the concrete, Lundeen Simonson’s foreman, Monte Plough, drew on his experience pouring foundations and footings to do the layout. “He used string lines, reference points and a lot of patience to get everything set,” Owen says. “It was pretty unbelievable how fast and efficient he was at getting everything laid out. There were thousands and thousands of feet of layout, squares and dimensions and pullout points.”
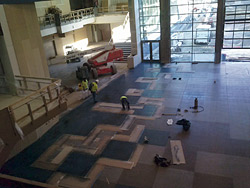
Educated choices at Davis
Lundeen Simonson staff approached the A.C. Davis job with the Eisenhower problems in mind. “We had a prepour conference,” Owen says. “We sat down with the concrete contractor and the architect, and we discussed expectations and mix designs and submittals.”
The principal architect on the A.C. Davis project was Gary Wetch, of Yakima-based Loofburrow Wetch Architects. He had been involved with the Eisenhower job, and he also had been the principal architect on the school district’s first polished concrete project — Stanton Academy, a new 49,500-square-foot facility polished by Meidling Concrete Inc., of Spokane Valley, Wash. Stanton, which opened for the 2012 school year, had gotten good reactions from the community and students. In fact, Wetch says, Stanton’s success gave the school district confidence to specify polished concrete at Eisenhower and Davis.
Wetch designed the A.C. Davis remodel using polished concrete in the corridors and a commons area. The concrete floors in the older parts of the building would be polished and dyed to match the new construction, with a pattern of colored rectangles unifying the old and new sections.
Having used polished concrete on five previous projects, Wetch knew that cosmetic cracks might become an issue at A.C. Davis. “When you have a steel building with a metal pan deck (on the second story), you will get more cosmetic cracking,” he says. “If you use steel I-beams, it’s more expensive, but it’s a little more rigid, and you would get a little less cracking.”
To minimize cracks, Wetch specified a concrete mix that included 3 pounds of fiber reinforcement per yard. He also specified a 5-inch slab instead of the 4-inch slab used at Eisenhower.
In a thicker slab, “you can use bigger aggregate, which allows for less cement and less cracking and more durability and strength,” he says. “My opinion is that with a thinner slab, you have more potential for curling. With a thicker slab, the weight of the concrete helps prevent some of the curling. You have more expense with additive mud but can use bigger aggregate, which keeps the costs down.”
When a slab will be polished, Wetch also likes to seed the surface with aggregate and trowel it in. He used that technique at Stanton.
“It gives you a terrazzo-like finish, and the eye is not drawn to any cosmetic cracks,” he explains. “But the sheer volume and size of the Davis and Eisenhower projects didn’t allow that, and on Davis we also had to try to match the existing concrete.”
On the A.C. Davis project, where old concrete floors would be polished along with new, Lundeen Simonson’s Owen worked closely with Wetch to develop the spec for polishing the existing floors, spelling out the costs of repair work that might be needed.
Wetch and Owen also made sure school district decision-makers understood the appearance issues that might arise. Chuck Doan, the district’s director of maintenance and operations, went to a remodeled Lep-re-kon Foods supermarket where Lundeen Simonson had polished the floors, and took video showing polished floors that bore shadowy marks from stripped-off tiles and former walls. The evidence helped school district representatives form realistic expectations of how the old slab might turn out.
“The owner was well aware of that going into it and still sees the benefit and payoff of polished concrete,” Wetch says.
“You can actually take existing buildings and enhance and incorporate them, and the blemishes add to some of the character, some of the nostalgia and some of the history,” Wetch says. “As long as the owners go into it with their eyes wide open, polished concrete will do what it’s supposed to do — rate of return.”
As a result of these measures and the close communication between Lundeen Simonson and Wetch, the A.C. Davis polishing job has gone smoothly for Lundeen Simonson. “That job is about the same size as Eisenhower, but it’s broken up into six different buildings,” Owen says. “Everything is a more manageable and controllable size. And the placement and the concrete was 10 times better.”
High-profile projects
Eisenhower High School will hold its grand opening celebration in October, and A.C. Davis is scheduled to open in fall 2015. Owen says Yakima’s investment in polished concrete is a powerful endorsement of the technology. “Seeing the whole school district do polished concrete because they believe in it is really exciting,” he says. “We have 130,000-140,000 square feet in this one city. These are two major schools for which they decided to go in that one direction.”
Owen likened Yakima’s choice to that of JC Penney, whose wave of store renovations last year raised polished concrete’s profile.
“These larger projects showcase the design capabilities and the function capabilities” of polished concrete, he says. “This is almost like a living, breathing flooring.”
Project at a Glance: Eisenhower High School
Client: Yakima, Wash., School District
Decorative concrete contractor: Lundeen Simonson Inc., Spokane, Wash. | www.lundeensimonson.com
Lead architect: KDF Architecture, Yakima, Wash. | www.kdfarchitecture.com
General contractor: Graham Construction, Spokane, Wash. | www.grahambuilds.com
Scope of project: New construction of high school for 2013-2014 school year, with 70,000 square feet of ground, polished, and stained concrete
Most challenging aspect: Precise dye layout, fast-tracked schedule (10 weeks from start to finish), huge building footprint to coordinate work force in
Equipment and materials used: HTC 800 HDX and 800 RX grinders, HTC EZchange diamond tooling, L. M. Scofield Co.’s Scofield Formula One Lithium Densifier MP, Scofield Formula One Liquid Dye in Leather and Bahama Blue, Scofield Formula One Guard-W water-based finish.
Project at a Glance: A.C. Davis High School
Client: Yakima, Wash., School District
Decorative concrete contractor: Lundeen Simonson Inc., Spokane, Wash. | www.lundeensimonson.com
Lead architect: Loofburrow Wetch Architects, Yakima, Wash. | www.loofburrow.com
General contractor: Absher Construction Co., Puyallup, Wash. | www.absherco.com
Scope of project: New construction and renovation of high school for 2015-2016 school year, with 66,000 square feet of ground, stained and polished concrete
Most challenging aspects: Precise dye layout, fast-tracked schedule and multiple trades working in the space.
Equipment and materials used: HTC 800 HDX and 800 RX grinders, HTC EZchange diamond tooling, L. M. Scofield Co.’s Scofield Formula One Lithium Densifier MP, AmeriPolish Surelock Concrete Dye in Burnt Sienna and Midnight Black, and L. M. Scofield’s Scofield Formula One Guard-W water-based finish