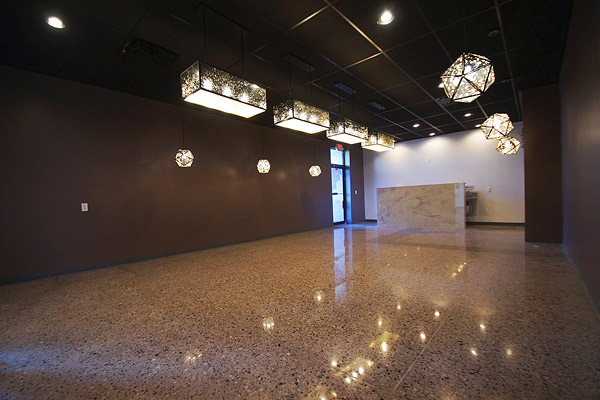
How can you tell if you have achieved a quality polished concrete floor? Perhaps more importantly, how can the owner tell? Up to now, judgments have been fairly subjective. They are based on a contractor’s experience and aided by a gloss meter or distinctness-of-image (DOI) meter. All of these things help contractors with measuring gloss on polished concrete. But as Clif Rawlings, vice president of key accounts for AmeriPolish Inc., explains, “A gloss meter can be fooled.”
To measure how light scatters, use a gloss meter. However, an angle, ambient lighting or even a high-gloss coating can impact the number. A DOI meter addresses this problem by “seeing” through a coating to determine the consistency of the surface underneath. Still, it cannot measure the porosity of the floor. So these readings may reveal little about the condition of the actual concrete or the floor’s expected life.
As a result, the industry has been searching for a better way to quantify the refinement of polished concrete. They want this to reassure customers they’re getting the floor they expect. Now, Rawlings says, the CSDA ST-115 standard is “a step in the right direction.”
What is the CSDA ST-115 standard?
In fall 2013, the Concrete Sawing & Drilling Association (CSDA) working with ASME, ASTM and ACI, issued a specification titled “Measuring Concrete Micro Surface Texture.” (See the January 2014 issue of Concrete Decor for more details.) Briefly, the standard, commonly called ST-115 details methods and sets parameters for measuring the average roughness of a concrete surface.
This measurement, the Ra, describes the surface refinement. It measures the average difference between the profile peaks and valleys — the scratches — in micro-inches. The Ra is key to achieving the desired appearance, performance and sustainability of the finished polished floor.
One can measure the microtexture by running a texture meter with a stylus probe over the surface. A reading of the variations measured in micro-inches or microns can be expressed as a surface texture grade. These grades are not ratings of “good” or “bad.” They are objective, measurable levels that roughly correspond to traditionally subjective descriptions. These include “heavy texture,” “ground,” “honed” and “polished.”
Why owners and architects care — and why you should too
For years, the variation and unpredictability of the finished appearance and wearability of polished concrete floors has frustrated architects, specifiers and building owners. Even specifying polishing to a certain grit or gloss number could produce different results from one floor to another. And floors that looked good and met the required gloss level in the beginning often turned out to wear more quickly. They also required more maintenance than anticipated. This soured some design professionals on the whole idea of polished concrete floors.
The ST-115 standard allows the customer to specify a Ra number that contractors must reach. They no longer have to specify a grit or a gloss number. If they want a matte finish, for example, they specify a “B-2 low polish” finish from the Surface Texture Finishes Chart in ST-115. Contractors will know they have to hit an Ra of 32 micro-inches.
Consultant Chris Swanson, of Sacramento, California-based Colour, explains it like this. “If a contractor is handed a specification based on ST-115, there’s no way around it. The specification will list the steps you must follow. The finished floor must be at this number.” This means a national account with dozens or hundreds of floors nationwide can get the same floor finish every time, even with different contractors. “Better refinement means higher level gloss, better consistency, easier maintenance and longer life,” Swanson adds.
Implications for contractors
Measuring Ra with a texture meter takes the guesswork out of selecting tooling and eliminates the issue of operator variation. “It used to be that a very experienced guy would have to come look at the floor and diagnose the level of the scratches,” explains decorative polishing contractor Robert Fruland, of Color Surface Inc., Las Vegas. “The problem with that system was, if you didn’t refine the floor enough to get the deepest scratches out, you might not see what you missed. So at step six you’re highlighting the deepest scratches and suddenly you have to go back to step two. It makes you just want to pull your hair out!”
Now Fruland has his crews use a meter as required by ST-115, and they don’t miss spots like they used to. They take a reading at the beginning of the pass to gauge the operator’s walking speed. If the number generated is lower than expected, for example, he’s walking too fast. So they adjust the walking speed, test again after about 8 feet and adjust again if necessary.
After another 10 to 15 feet they test again. Finally, after finishing the pass, they test one more time to be sure they’re still getting the same number they got in the beginning. Then they move on to the next tool and the next target Ra number. This is usually half the number of the previous pass.
Lenny Sniegowski, president of Prep and Polish Consultants LLC, Richardson, Texas, recommends this process. “Once you’re hitting the optimum refinement number for a given tooling step, then you know you’re walking with the right speed and sufficient down pressure. Stick with that.” He recommends taking readings every 500 square feet.
Texture meters are helpful
One caution — if the probe is set on a joint or piece of aggregate, it might give false readings. Fruland typically checks the floor in about 10 different spots to be sure he is getting an accurate average.
Using a texture meter as described in ST-115 actually helps contractors complete jobs more efficiently. This is because they can run the tooling just as much as they need to — no less and no more.
Andy Bowman, president of Adaptive Concrete Innovations, one of several companies making tools that take Ra measurements, relates the example of a contractor who starts every job at 30 grit. “If you had a meter that showed you didn’t need to start at that level, which creates a heavy scratch that’s so hard to recover from, you would save labor and be more competitive.”
“I can have my guys run this system and they can’t mess it up,” says contractor Gene Ferrant, of Sydco Inc., Covington, Louisiana. “You hit the number and move on to the next step. It’s a good system. I like it. It’s quick. I may pay more for tooling, but labor-wise it’s a whole lot faster.”
Equipment considerations
Besides setting a measurable standard for floors, ST-115 helps set a de facto standard for tooling as well. Currently, different tools identified as the same grit can vary widely, depending on the range of grit size, density and quality.
“There are no unifying quantifiable standards for diamond tools,” says Christopher Bennett. Bennett is responsible for architectural specifications for Husqvarna Construction Products. “So the next best thing is to measure how the tooling affects the surface of the slab, what it does to concrete. That you can measure.”
The standard is driving momentum to get tooling certified to produce specific Ra numbers. For example, Husqvarna had all its tooling audited by a third party. The did this to determine the scratch pattern and maximum refinement level produced by each tool. Once the industry adopts this type of testing, it will make it simple for contractors to compare tools. Thus, they will select the right equipment to meet any given customer specification.
Is the best yet to come?
The CSDA ST-115 standard certainly has the potential to bring greater accountability to the polished concrete industry. Clif Rawlings believes its greatest strength lies in using it in combination with gloss and DOI measurements. “This will help the floor owner know what they’re getting in terms of the quality of floor and workmanship,” he says.
“What we’re doing now is otherworldly compared to what we used to do,” Robert Fruland says. “The best polished floors are yet to come. Floors we’ve done to this point are going to be pretty substandard compared to those going forward with a tool like this. I can’t wait to show off these floors when they’re years old.”