Once upon a time, there was a polished concrete job that was easy. It started out with a new, flawless install, a clean, even slab ready to grind. The client closed the building for a few days, providing ample, uninterrupted time to do the job. There were no hurdles. There were no surprises. Everything went according to plan.
The polish applied last March at the Empyrean Coffeebar in Nashville, Tenn., was not that job.
The Empyrean Coffeebar is part of Rocketown, a multipurpose youth center that comprises classrooms, a skatepark and a live music venue. During the 2011 Concrete Decor Show & Spring Training, the Rocketown facility received a decorative concrete overhaul, courtesy of dozens of artisans, manufacturers and suppliers. (For more details on the renovation in its entirety, see “Remaking Rocketown” in the April 2011 issue.) Although there were challenges involved in every aspect of the Rocketown project, arguably the gnarliest was the restoration of the floor at the Empyrean.
Originally poured back in the ’60s, the Empyrean’s floor was home, for decades, to an engine rebuild shop. Years of deterioration had been compounded by untold gallons of motor oil and engine fluids that had seeped into the surface, causing it to soften severely. “The floor was in the worst possible condition for a polished concrete job,” says Roy Bowman, president of Tulsa, Okla.-based Concrete Visions Inc. “I’ve been polishing since 2002, and I have never cut a floor that soft.”
Bowman was one of four trainers with the Concrete Polishing Association of America who came to the event to run two back-to-back polishing workshops. The restoration of the Empyrean’s floor was the hands-on portion of the class. So when Bowman, along with Concrete Visions vice president George Gooch, Derek Mackenzie of Toronto-based Floorlab Inc., and CPAA president Brad Burns, arrived to find a slab you could pretty much cut with a butter knife, they had no choice but to roll with it. Luckily, both Bowman and Burns feel that rolling with it is a big part of what the CPAA teaches.
“The hardest thing about polished concrete are all the unknown variables,” says Burns. “We have the flexibility and the knowledge to adapt to that, and that’s exactly what we did.”
Bowman agrees. Dealing with the unforeseen is “really what the CPAA is about,” he says. “Part of being a craftsman is that when someone hands you a sow’s ear, you have to give them a silk purse.”
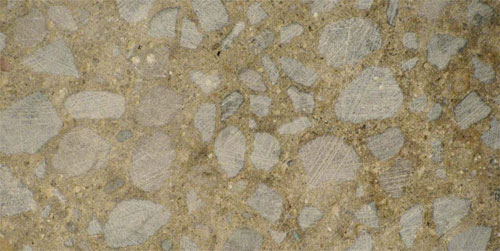
Getting the floor into polishable condition took not only several steps of grinding and cleaning – “We’d wash it and oil would leach up, and we’d wash it again and more oil would leach up,” Bowman says – but also an epic amount of densifier. A few steps into the grinding process, the team applied Husqvarna’s GM 3000 grout coat, which combines with the grinding dust to make a slurry that fills in pits in the surface. They followed that up with multiple rounds of densifier as they went through the polishing process, until the surface wouldn’t absorb any more. In addition to several applications of Prosoco’s Consolideck LS, Bowman used 7 gallons of L&M Construction Chemicals Inc.’s Lion Hard on about 700 square feet of the floor. Under normal circumstances, Bowman says, that would’ve been a good amount for 6,000 square feet.
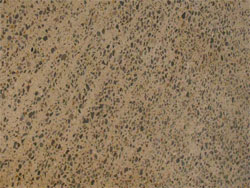
On hand to help demonstrate the polishing process to attendees were several manufacturer reps, armed with polishing machines and years of experience. Burns says this support from the manufacturers is a strength of the polishing field. “Polishing manufacturers can all pull together for the benefit of the industry,” he says. “They’re not trying to trump each other. It’s not a competition. It’s for the good of the industry.”
Clif Rawlings, product manager and training coordinator for HTC Inc., and Sam Lewis, SASE Co. regional sales representative, were the manufacturer reps in charge of the polishing demonstrations for the workshops at the Empyrean. While both Rawlings and Lewis say the collaboration worked really well, they did hit a small speed bump when they started the floor. Each of them had a different idea about what abrasives to use on a surface that soft, and they started their sections out at different grits. Fortunately, the floor was easy to even out to the same grit, and the students got to discuss the merits of the different approaches. “Once we got past that,” Lewis says, “everything smoothed right out and moved on as planned.”
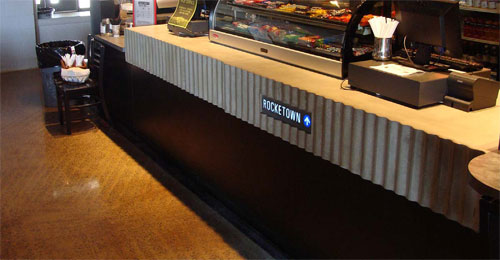
Well, almost as planned. After the initial grind on the floor, the team discovered that the Empyrean had another surprise in store – a phenomenon known as jitterbug lines. A jitterbug is an old tool used for consolidation, sort of an early version of a vibratory screed. The trouble is that it consolidates the concrete unevenly, and when you grind the surface down, you expose “tiger stripes,” as Burns calls them. The entire floor of the coffee bar had lines across it, at about 2-inch intervals, of alternating aggregate and mud.
While the tiger stripes were not entirely off-putting – “It gives the floor a neat effect,” Rawlings says – they did interfere somewhat with the original plan, which was to place a logo on the polished gray floor. (Bowman says that some of the lingering oil stains also made the logo a tricky prospect.)
So they needed a backup. Fortunately, in the next room, Bobby Watson of American Decorative Concrete Supply Co. was using his company’s AmeriPolish Surelock Dyes. Bowman, seeing the caramel color they were using, had an epiphany. He realized that the dye looked almost exactly like the oil stains on the Empyrean floor. After a long couple of days with not a lot of lucky breaks, the dye discovery had given them the right hue at the right time.
ReGina Newkirk, executive director of Rocketown, was particularly happy with the solution because the caramel dye toned down the shiny silvery surface of the plain polished floor. “The diamond polishing looked really beautiful,” she says, “but it started to look like you had walked into a bank.” The dye disguised the oil stains, worked well with the tiger stripes, and really brought the floor together. Newkirk says that ultimately, the floor’s imperfections were really what made it special. “Things that are odd and quirky and not perfect really work for us.”
Newkirk says that the process of the renovation was fairly hectic. (Did we mention that Rocketown was not only open for business during the project, but also hosting a series of all-day programs for spring break?) She attributes a lot of the project’s success to the fact that the artisans were careful to communicate with them throughout.
“One thing that was really nice was that the guys would take the time to explain what they were doing and what was happening and what they were finding,” Newkirk says. “They were able to put it in layman’s terms, and that was really appreciated.”
Project at a Glance
Client: Rocketown, a youth center, complete with skatepark and concert venue, in Nashville, Tenn.
Trainers: Brad Burns, president, Concrete Polishing Association of America; Derek Mackenzie, CPAA executive board chairman and owner, Floorlabs Inc.; Roy Bowman, CPAA executive board secretary and president, Concrete Visions Inc.; and George Gooch, CPAA trainer and Concrete Visions vice president
Machine Operators: Sam Lewis, regional sales manager, SASE Co., and Clif Rawlings, product manager and training coordinator, HTC Inc.
Scope of project: 2,500-square-foot concrete floor, to which the years had not been kind
Duration of project: Two days, March 14-15, 2011, as part of workshops at the Concrete Decor Show & Spring Training.
Tools/Equipment Used: HTC 950RX, HTC 650RX, HTC 270EG, SASE PDG 8000, Substrate Technology STI-2417 Prep/Master Propane
Materials Used: Prosoco Consolideck LS, L&M Construction Chemicals Lion Hard, Husqvarna GM 3000, AmeriPolish Surelock Dye: Caramel Empyrean Coffeebar Floor at Rocketown Nashville, Tenn.