Polished concrete is a young industry. Surveying the processes and technological advancements over the last 15-20 years, it’s apparent the industry has continued to grow and discover new, faster — and not always better — ways of achieving unique, shiny floors. But not all these shiny floors are refined polished concrete floors, and therein lies the problem.
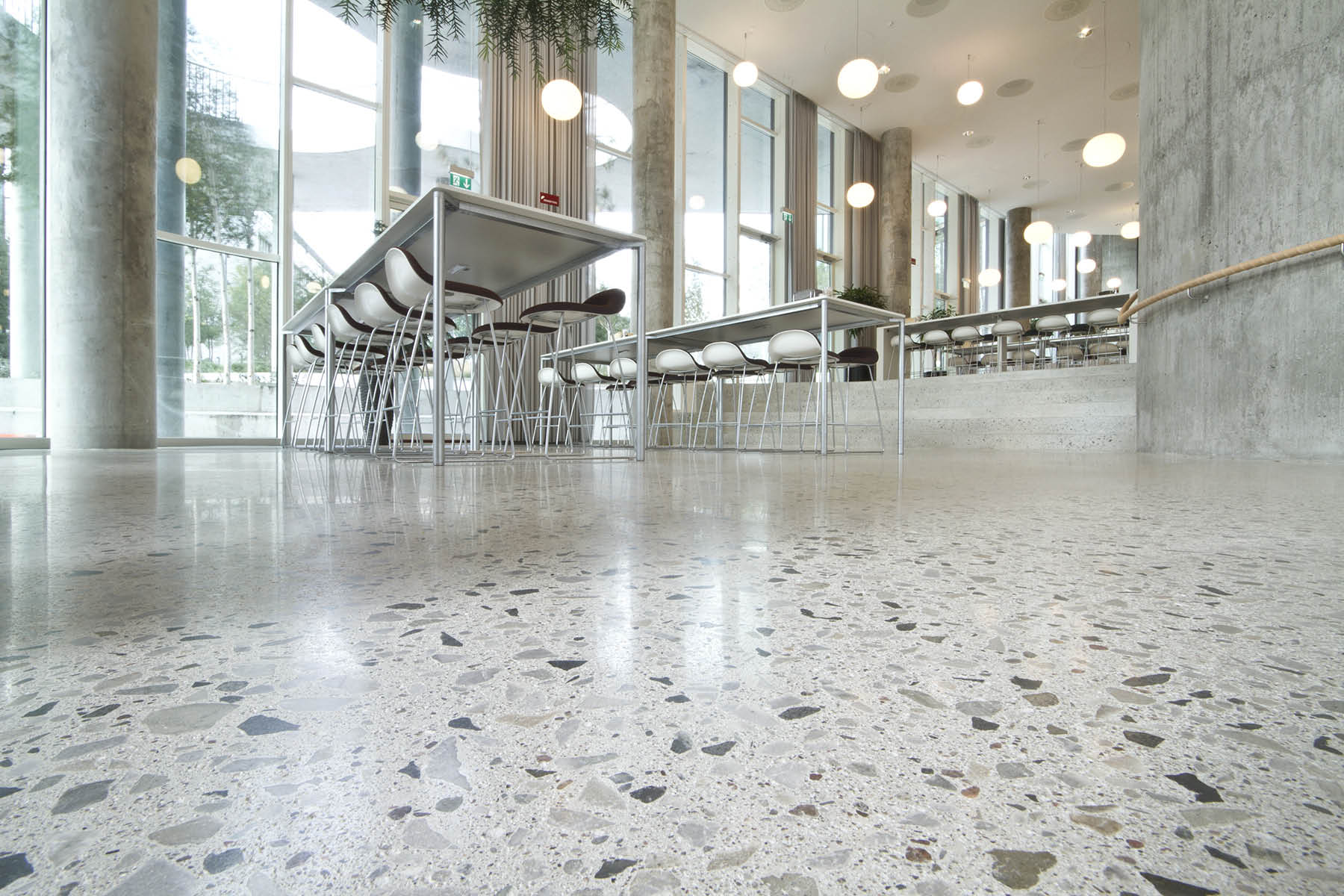
A look at evaluation and testing history
In the early days of our industry, for every new process introduced, accountability seemed to lag a few years behind. For example, when polished concrete floors became popular within the architectural community, architects specified the “look” or process according to grit or finish level. Specifying based on these parameters was extremely hard, not only for the contractor to bid, but also for the owner, general contractor or architect to hold the contractor accountable if the finished floor wasn’t what was originally envisioned.
This problem developed because there was no standard way to determine what that “look” was and if it was achieved. Due to this, our industry tried to create guidelines and a measurable way to ensure everyone had the same expectation.
One of the first attempts at regulation was the gloss meter. We adapted a meter used for detecting the gloss level of a painted finish to the polish level on our floors. Architects were then able to take that information and specify the finished gloss value (noted as Gu for gloss unit) transcribed to the “look” of a particular floor finish.
Many contractors found the “look” far easier to bid and far easier to fake by applying a coat or two of acrylic or other sealer. This made the concrete floor “shiny” and registered the correct Gu, but the floor wasn’t necessarily polished or really what the owner or architect wanted.
Now our industry is ready to grow, and many companies are jointly compiling years of testing and evaluation to help polished concrete evolve. As an individual who has strived to create great polished concrete floors for years, nothing has been more frustrating than to see floor owners’ expectations not met by a system that may have met the specified “look” but lacked the full process we commonly refer to as “refinement.” Without refinement, the true glory of a polished concrete floor is typically not achieved.
With that said, what can we do? One solution begins by looking at our eyes. Sounds weird, right? But our eyes are a remarkable meter. We can look at two reflections and tell which “look” we like better. Putting that “look” into vocabulary or creating a label for it has been the challenge.
A mentor of mine often says, “Ryan, words are important. You have to say the right words or have the right labels to be able to intentionally interact with the process.” If we, as an industry, can define and use the most accurate and consistent labels, we can help others understand what they see and like, and then we will be able to repeat the process again.
Many advanced polishing contractors have adopted this concept and have begun to use more sophisticated methods for creating great-looking floors by perfecting their measuring/testing of end results. It has taken years to learn and thousands of test samples measured to label what data is important and what data is inconsequential.
Testing for refinement
This brings us to the heart of the challenge. As an industry, we have two mountains we must label correctly so we can resolve and move forward intentionally: testing devices and testing procedures.
Testing devices— The first thing we need to determine is what testing devices are working well or could work well (what can we adapt from other industries, other resources) to help us monitor, detect, specify, measure and ultimately use to improve our industry and satisfy floor owners.
Testing procedures — The second item we need to figure out as an industry is how to create testing procedures or best practices for uniformity and linear data collection that are acceptable to our constituents. After all, that which can be measured can be improved!
Let’s start with testing and evaluating the “look” with quality control equipment. A little story, if you will:
“I want a shiny floor, but not too shiny. Too shiny looks slippery,” said the floor owner to his contractor.
The contractor thought to himself: “I know how to do that. I do it all the time. My client is going to be so happy when I finish!”
Unfortunately, this story is probably closer to real life than we want to admit. Neither the floor owner nor the contractor knows exactly what the expectation should be. There’s no measure in place. The floor owner’s definition of a “not-too-shiny” floor is probably way different than the contractor’s definition.
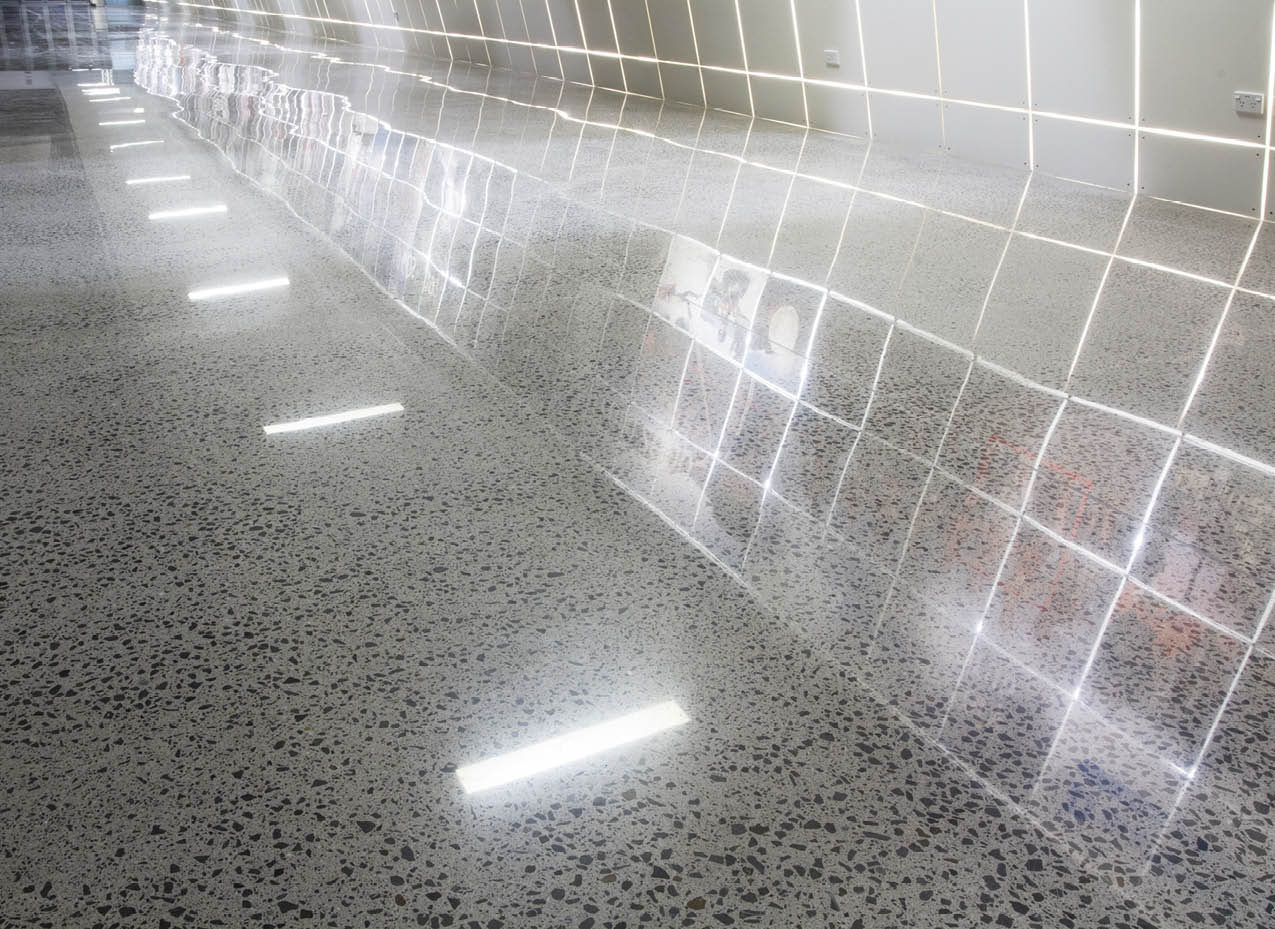
This is why more advanced tests besides gloss value need to be developed to evaluate the finished appearance of a refined floor. In addition to gloss, there are other values to test to ensure a floor is polished concrete and not just “shiny.”
The top three visual values we have evolved to evaluate polished concrete are:
- Gloss: Amount of light reflected by the surface.
- Distinction of image (DOI): The sharpness of light reflections or reflected images.
- Haze or the halo factor: Reflections appear to have rings around images. This is caused by the dispersion of light at the surface, which is normally due to resin left behind from tooling used in the polishing process or a guard/sealer that may be present on the surface.
Testing these three values can be accomplished by multiple devices or by one simple handheld device. I have found the Concrete Clarity Meter will accomplish most of my day-to-day evaluation with ease.
As an industry, guiding groups like the Concrete Polishing Council, a specialty council of the American Society of Concrete Contractors, have moved toward DOI as their primary value for describing the look of a polished floor. ACI Committee 310-OJ has created a taskforce and is evaluating data collection to help develop specification guidelines to fully embrace DOI and its value to our industry. (Stay tuned for an update on testing processes with DOI values.) Another member group, the Concrete Sawing & Drilling Association (Committee ST-118), is currently evaluating testing procedures and equipment for best practices pertaining to surface refinement.
All this testing and measuring will lead us to more consistent, high-quality floors and to clear, concise specifications. This leads to more consistent bidding, higher accountability to the contractor and owner. This sets the expectations from floor owner, to architect, to contractor and means a better understanding of the whole process for all involved.