Colour, a decorative concrete company in California that specializes in elegantly colored and polished concrete surfaces, seemed to get lucky when it parlayed a small staining job into a major floor overhaul.
Then the carpet was peeled off and the horrendous condition of the 4,500-square-foot concrete floor was revealed. Some might have questioned their luck at that point. But Colour forged on, and it was rewarded with a wonderful surprise: The floor polished astonishingly well.
“It was a horribly ugly floor that everybody was worried about, and it turned out to be one of the most beautiful floors we’ve ever found,” says Chris Swanson, who, along with his father, Jim Swanson, and their partner, Jamie Schneider, run the Placerville-based company.
The project was part of the renovation of a nearly century-old building in downtown Redding, Calif. The structure was being transformed into The Atrium Building, a shopping arcade in the new Market Street Promenade development, and the owner hired Colour to acid stain the walls around the elevator. The ground floor of the building, which sits near the Sacramento River, is well below street level and suffers from moisture vapor problems. Despite that fact, the owner wanted to replace the old carpeting on the floor with tiles, keeping his fingers crossed that the moisture wouldn’t cause the tiles to pop up.
When the Swansons pointed out that refurbishing the existing concrete would avert a tile-popping moisture vapor nightmare, the owner was skeptical but curious. When the Swansons pulled out photographs of some of the exquisite refurbished floors they’ve done in the past, the idea of laying tiles flew out the window. “He went berserk when they saw what we can do,” says Chris Swanson.
At that point nobody had any idea what kind of condition the concrete was actually in. It wasn’t until the carpet was pulled up and three layers of glue were painstakingly removed that the horror beneath was revealed. “We expected some plumbing cutouts, electrical cutouts and cracks,” Swanson says. “But it was much worse than we expected.”
The cracks were extensive, long, and often gaping. The cutouts were many, and in some cases mysterious, made for no obvious reason. The pourbacks were loose and chunky or dusty. The floor was uneven, with lots of high and low points. And to top it off, the original pour was littered with embedded foreign objects, including nails, electrical boxes and pieces of wood.
Leveling the peaks and valleys was one of the first steps toward transforming the eyesore of a floor into something beautiful. That took several days of aggressive grinding with 25-grit metal-bond diamond tooling. Next came crack repair and the stabilizing of problem pourbacks. For hairline cracks Colour used VersaFlex Quick Mender in its low-viscosity form, where it penetrates deeply into the substrate and acts like a repair mortar. For the wider cracks and the problem repours, the Quick Mender was made into a parging compound by loading it with 30-mesh sand and dust left over from the grinding stage.
Then the diamond grinding resumed, proceeding in this order: 40-grit metal bond, 40-grit resin blocks, 80-grit resin blocks. With the floor’s pores still wide open after the 80 grit, Colour applied a lithium-based densifier, which hardens and expands over the course of several months, slowly increasing stain resistance. After the densifier was applied, the floor was honed using 100-grit, then 200-grit mixed resin blocks. Then it was polished using 400-grit resin diamonds. Next, all the design and coloring took place, and the floor was polished with 800-grit resin diamonds.
It wasn’t until the grinding got underway that what Swanson thought was a “horribly ugly floor” began to reveal its true colors. Those colors included rich reds, greens, blues, yellows and pinks – rock that a concrete artisan might have selected, but which was actually the locally available aggregate when the floor was poured at the beginning of the 20th century.
“We weren’t able to see how pretty the rock was until we were done with the 40 grit,” Swanson says. “By the time we got done with the 400 grit, you could really see how much rock was showing and the color of the rock.” For the edges Colour used a stand-up edging machine and plenty of hand grinding. The budget didn’t allow for the monumental task of polishing the edges, so Colour used an edge tint to create dark brown borders that complement the color of the baseboards.
The owner gave the Swansons more or less free rein to come up with the floor’s design, which features three sections of tortoise-shell colored concrete set against long gray stretches of naturally colored concrete. “By leaving some natural gray, all the other colors we used get a really nice contrast,” Swanson says.
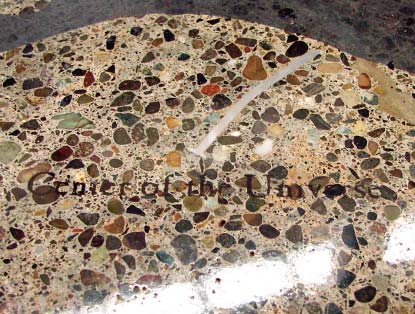
The main section of the floor is defined by intricate borders and contains a compass rose, along with the Redding city seal. After diamond-scoring the borders and compass rose, the Swansons scored crisscrossing diagonal lines across the floor’s colored sections. The lines create the illusion that the floor is composed of 6-by-6 diamond-shaped slabs. The technique is one of Colour’s hallmarks. “We like to make it look believable, as if there’s inlaid stone there rather than just a big strip of colored concrete,” Swanson says. All of the scored lines were later mortared to complete the effect.
The incorporation of the city seal was inspired by a manhole cover the Swansons noticed on the street. Redding’s manhole covers are embossed with the seal, and the Swansons took a photo of one and sent it to Colledi Signs in Fresno, which used it to fashion a set of vinyl sandblast stencils. The seal was then sandblasted into the center of the compass rose, and the recessed areas were dyed black. The seal offers a roughly-textured contrast to the gleam on the rest of the floor, as if the seal had been engraved into the polished surface.
Of the 15 colors of acetone dye used on the floor, the black in the seal is the only one that came straight from the dye can. The other 14 were custom mixed by the contractor. On the central part of the floor, four earth tones – a main color and three highlights – blend into each other, creating a variegated look. Exactly how Colour achieved that look is something you’ll have to guess at. “We have techniques we don’t share with other contractors,” Swanson says.
Once all of the coloring was done, Colour densified the floor and polished it with 800-grit resin diamonds. Then the floor was burnished with diamond-impregnated twister pads and an application of stain guard went down. It was burnished again with 1,500-grit twister pads and a second application of stain guard, then burnished once more with 3,000-grit twister pads. The burnishing and stain guard were woven into a five-step process that went like this: 800-grit diamond twister, stain guard, 1,500-grit twister, a second application of stain guard, 3,000-grit twister.
In a whimsical finishing touch, the Swansons stenciled the words “Center of the Universe” beneath one of the tiny nails embedded in the floor. The nail, which is so small you practically have to get down on your hands and knees to see it, lies at almost the exact geographic center of the room – right in the middle of the compass rose. The building’s owner frequently pointed to the nail and joked that it was the center of the universe, which prompted the Swansons to ask if he wouldn’t like to make that official. What the heck, he said. So the Swansons stenciled the tiny letters into the floor.
“Now every time he brings people in to see his building, he points it out and says, See, I told you it was the center of the universe,'” Swanson says.
Shelly Shively, the interior redesigner who worked on the project, says the one-of-a-kind nature of the floor gives the building’s owner a lot of satisfaction. “He likes being exclusive,” she says. “And now he has a floor that nobody else could buy.”
(530) 409-9232 (Colour)
Project at a Glance
The challenge: Transform an aged floor in atrocious condition into a beautifully polished and colored surface.
Polishing machines used: HTC 800 HDX, HTC 500, HTC 400, HTC 130
Acetone dyes: Ameripolish
Coloring decisions made: At the last minute.
Local supplier who got acetone dyes ordered and shipped in record time so project could proceed without any delay whatsoever: Spec West, Sacramento, Calif.