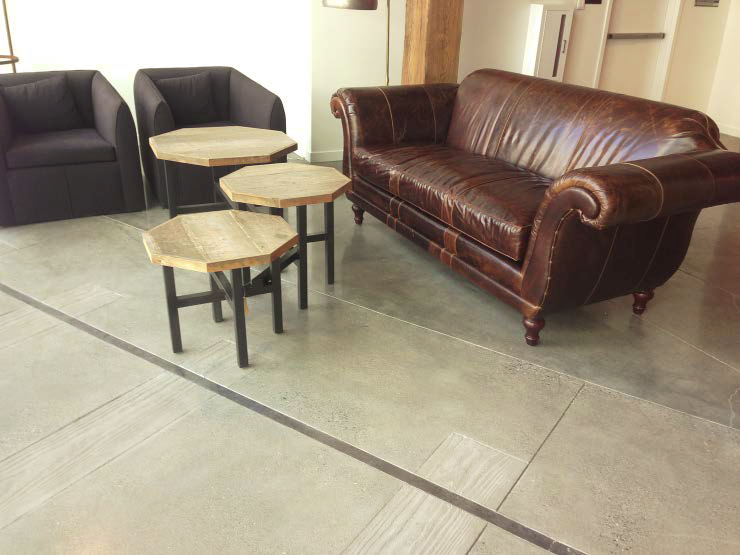
Concrete Decor asked Bay Area Concrete’s president, Mike Price, a number of questions about the phenomenon of polished concrete in the high-tech area of California’s Silicon Valley. That discussion follows.
What is driving the growth of polished concrete in the high-tech customer segment?
No. 1, they love it. It’s architectural and also “green.” No. 2, the price point is good. No. 3 is life cycle — the long-term service life or cost of the floor over a 30-year time span. Polished concrete beats all other floor surfaces over this span.
The architectural possibilities are endless and the maintenance is much less with polished concrete. We can add dye effects in any color, graphic enhancements or architectural saw-cuts, not to mention that a heavier grind and polish can produce beautiful colors in nature’s own rocks and sand tips — just like polished rocks.
Are these companies doing creative things with polished concrete?
Yes, of course they are! BAC installed a recent project in a high-tech software/code firm’s offices in a 100-year-old train station converted to office space. The existing floor surface was part asphalt, some old, dirty concrete and hardwood, among other remnant surfaces.
We installed a concrete topping slab, 1- to 4-inches thick, and inlaid some metal railroad-track sections into the topping. We poured concrete over different elevations and materials. This was a cost-effective solution, because we eliminated the need for a large scope of demolition. We then diamond-polished and even used heavier aggregates near the track, hand-seeded into the surface. We used 3/4-inch rock around the track sections when we poured, then we polished using hand grinders to reveal the larger aggregate. This simulated the gravel beds that train tracks are laid upon, in an abstract, artistic format. This was in their employee lobby, gathering/game area and general quad/cafeteria locations.
The highly durable and artistic surface served their needs well, as this is a highly creative firm with creative folks. We even produced a railroad spike with the founders’ names engraved on it, and it was placed in the new concrete surface. It’s real-world creativity coming to life in polished concrete.
What are the key attributes of polished concrete in this case?
It’s green-building, the maintenance is low-cost and concrete as a surface medium took care of different height elevations resulting from the irregular surface and varying existing flooring materials. In most cases of polished concrete, we are using the existing concrete and no hazardous materials are involved. Clients like the idea of taking an existing concrete slab, honing it and making a natural kind of surface. We are not raping Mother Earth to create surfaces like other chemically based or tree-based mediums of flooring. We are simply reusing the existing concrete foundation to create a beautiful and allergen-free floor finish.
In the future, the clients can do whatever they want with the floor, with regard to design changes. They can put carpet, tile or hardwood over it, or simply regrind and polish adding a dye color or saw-cut pattern. Long-term design possibilities are endless.
What did you do in a similar project?
We did saw-cuts and waves of color in a 4,000-square-foot business space. There’s a band of blue dye, a band of red dye, then gray installed in both the lobby and common area. The adjoining rooms were done in different colors. Every project takes a different timeframe to complete based on the intricate nature or simplicity of design, volume of area to address, and of course, the all-important construction schedule. We have completed 1,000-square-foot projects in two weeks and massive largest-in-class 500,000-square-foot projects in eight weeks. We always remain flexible and open to design and schedule challenges.
What kinds of customers are driving this growing market for polished concrete in this geographic area?
In the Silicon Valley and San Francisco marketplace — and the situation is similar in other cities — the dynamic is that an increasing share of the office space market is owned by large developers or property-management firms. Sometimes these owners will polish the floors, and these can be customized, if a long-term lease is signed. Then the new tenant can add other floor coverings as desired. Again, cost is a big factor along with surface durability and natural beauty of this green-build(ing) material. Architecturally speaking, the polished concrete floor surface is timeless.
Do the tenants hire their own contractor and customize this surface?
Yes, it’s up to the tenants to do what they want, as far as altering the surface as needed. It’s a win-win. Polished concrete is a popular, cost-effective medium, not only for the tenant but also for the people who own the buildings.
We also see projects where the owner is doing the common areas, and tenants are doing their own thing with different colors or polish levels. The tenant can remove the polish “cap” off of the concrete, patch and repair and polish to a higher level, and install decorative saw-cuts and dye colors. Corporate logos or sayings can be placed in the floor, too.
You say you have another creative project in the works in Silicon Valley?
Yes, I can’t identify the company, but we are doing research and slab development concepts for a topping slab that will produce a jelly-bean, blue-glass-aggregate look in a lobby. This design may change over time, but this is where we excel. We work with owners, interior designers, architects, general contractors and artists every day, in the early stages of their projects, to create the road map for their polished concrete success. We want this industry to continue on its path of growth because it is a wonderful product for our clients and the planet. Polished concrete will eventually come to every corner of the Earth. It has arrived.
Where is growth occurring for polished concrete, and how is the market evolving in other ways
With the high-tech companies, the market is driven by designers and budgets. But you also see it in condos and common areas of apartment complexes, in some cases due to young environmentally conscious professionals who work at Google or Apple and want it in their homes, too. Loft owners in San Francisco have loved polished concrete forever, since around (the year) 2000 when we first started mass polishing concrete surfaces with our PolishedCrete brand name.
When polished concrete first came in vogue, it was mostly in schools and lofts, due to low cost and low maintenance. Now we get entire homes or apartments in the San Francisco Bay area where (residents) want all their floors polished. That’s where the more decorative part of the business really comes into play. Homeowners love the unique and artistic design possibilities. Each floor is artistic and difficult to duplicate, thus these diamond-polished surfaces become an extension of the homeowner’s creativity and individuality.
Do you see continued growth as likely?
Yes, it’s only going to continue to grow. The market has huge growth potential. We’re seeing commercial flooring contractors going into it as well as companies that do carpet, tile and so on. This market is just beginning and has a long way to go before reaching saturation. It is a shooting star in flooring.
How has polished concrete figured into your portfolio mix? Have these market dynamics changed your business?
Yes, polished is now about 50 percent of our business. In 2000 it was 5 percent of our business, and in 2010 it was about 20 percent. I can foresee that in the future it will be 75 percent plus. For a company like ours, we live and thrive on the cutting edge of new concrete technology and diamond-polished concrete is here to stay.
What did your portfolio look like before the dawning of the age of polished concrete?
We were architectural concrete guys — toppings, Bomanite, stamped, textured, decorative concrete. We are the longest-surviving stamped-concrete contractor and the second in the nation to start stamping concrete back in 1966. This gives you an idea of our pedigree.
It took 18 years for stamped concrete to take off and thrive. As a concrete-polishing company, we are on year 16 and we are taking off and thriving once again, (this time) in polished surfaces.
What kinds of innovative, creative concepts are you seeing with high-tech customers?
You see everything, from taking an existing warehouse floor and polishing it to a nice shine, to cases like a project we did in an existing office space overlooking the (San Francisco) Bay, where we used a blue dye that reflects the hue of the bay. New concrete toppings integrate the use of recycled glass and when revealed, ground and polished, they become fantastic mediums of light-giving surfaces for employees to be inspired by every day at the office.