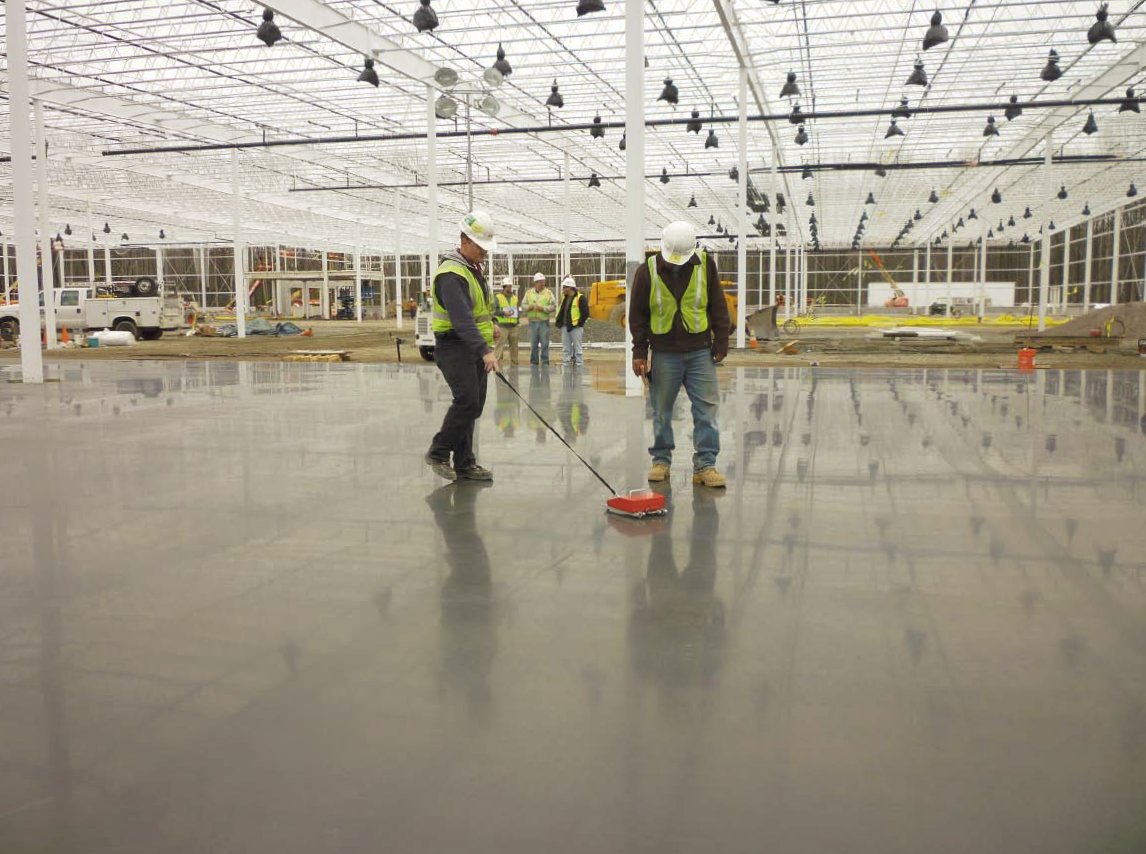
In the world of concrete contractors and finishers, there are at least three factors that really matter when pouring and placing concrete to achieve a flat slab.
First, there is the foundation, which must be graded, leveled, and compacted accurately. When concrete is poured and placed on an unevenly compacted foundation, these areas often develop troublesome low spots (birdbaths) and cracks in the finished floor. What’s more, just because a laser hits both side of the form does not mean that the entirety of the foundation has been compacted evenly.
Second, there is the finishing of the concrete. Often, finishing depends on the size of the pour. Larger concrete contractors usually bid and place larger concrete slabs (10,000-plus square feet). Larger contractors own power trowels and laser screeds and have more experienced crews. Just as with polishing, the right equipment and expertise can make a significant difference with the finished result.
Third, the flatness and levelness of the slab must be measured and documented once a slab is bull-floated, vibrated, pan-troweled and steel troweled.
This is where F-numbers come into play. There are two types of F-numbers, which measure floor flatness and levelness respectively. Industry expert Allen Face is the creator of the F-number system, as well as the inventor of several measurement instruments and a principal inventor of superflat floor technology.
According to the Faceco.com website, “The F-number system is the American Concrete Institute (ACI 117) and Canadian Standards Association (CSA A23.1) standard for the specification and measurement of concrete floor flatness and levelness. F-numbers replaced older ‘1/8 inch in 10 feet’ type specs that had proven unreliable, unmeasurable and unrealistic.”
What FF means
The FF (floor flatness) measurement reads the “bumps” (highs and lows) in the slab, and higher numbers are better. The more bumps there are, the lower the FF number will be and the more difficult it will be for a polished concrete floor to have a uniform appearance. Think of these bumps and high areas like the knuckles on your hand. When your fingers are bent, the knuckles stick up higher than the rest of your fingers. If something rough rubs against your hand, the skin will tear and expose blood (sand) or bone (aggregate) at the knuckle, while the other parts of your fingers remain intact.
This is one reason why it is problematic to promise a certain amount of cream, sand or aggregate exposure without reading the specifications beforehand. If the specification contains low numbers, the installer does not read that, and they shoot off their mouth and say they can make any floor shine without showing aggregate, they will fail. Knowledge is power!
When concrete is ground, honed and polished, the high areas are exposed and the sand or aggregate is revealed. To what level the sand, aggregate or cream will be revealed depends on a multitude of items: machine weight and size, speed of the rotating heads, how well the heads flex, operator pace, grit and aggressiveness of the diamonds, diamond bond, the amount of tooling per plate, whether the machine is being used wet, damp or dry, the amount of pass overlap, whether each pass is crosshatched and so on. Some variables can be controlled, but you are at the mercy of others due to concrete mix design, concrete placement, finishing techniques, curing methods and the age of the concrete. When it comes to polishing concrete, each and every slab will be different, and that is one thing that you can count on.
When bidding a new construction project, reading the 03 30 00 Cast-In-Place section (which is using the Construction Specifications Institute format) in the specification is extremely important. Remember, the higher the FF numbers, the less you will need to worry about uneven exposure. My experience is that the flatter the floor, the more predictable the grind, the lower the risk of cost overruns, the higher the profitability, and the more predictable the production schedule will be.
Within the last five years or so, as concrete has become a go-to choice for finished flooring, reported FF numbers have been steadily rising. Previously, FF numbers were specified in the 20-30 range, which resulted in undulations and unpredictable appearances. Over the last few years, the numbers specified have been rising and are now typically FF 35-50.
Note that F-numbers are linear, so an FF 20 is twice as flat as an FF 10, but only half as flat as an FF 40. This means that the higher the FF number, the flatter the slab will be, and the easier it will be to achieve a more uniform polished appearance. Whether you realized it or not, the jobs where you had the easiest time getting a uniform appearance, with very few issues, were the slabs with higher FF numbers. Most likely these are also the floors that you are the most proud of and that were more profitable.
When an owner requires a flat slab, the numbers should range from FF 40-70. The beauty and benefit of this trend is that once a concrete finisher has to meet these stringent numbers, they almost always err on the high side!
The importance of FL
Also consider the FL (floor levelness) measurement, which tells you the amount of “slope” or elevation of the slab from one side to the other. A sloped slab can make the approach to a project a bit trickier. For example, when a concrete polisher works on an auditorium, he or she must keep the slope in mind. We cannot simply push uphill and cut the “hill” down. Instead, we grind across the hill and maintain that slope.
Generally speaking, you will only see FL numbers called out for the slab-on-grade (SOG) part of the specification, but all floors should have an FF number. If an FF number is not called out, it would be a smart idea to make the general contractor or architect aware. Planning well is essential when the outcome of your polishing job depends on it.
Getting the numbers
Now that you have some basic understanding of FF and FL numbers, just how do you get these numbers, and who is responsible for measuring and reporting results? For large box-store work and building multiples, it has become common to hire a concrete testing agency to monitor the pour and do the testing. Testing should be performed as soon as each day’s placement will bear foot traffic and definitely within 72 hours of slab installation. In most cases, the F-numbers for that slab can be determined within a few hours and the report can be generated before the next slab is placed. For smaller or single-pour projects, contractors can take measurements themselves. Companies such as The Allen Face Cos. teach professional slab measurement seminars. Contractors can purchase or rent the instruments and may be able to arrange loaners with the manufacturer.
F-numbers offer significant benefits and were not simply invented as a way to find someone to blame. Properly used, F-numbers can identify potential problem areas and help the concrete polisher predict probable appearance inconsistencies and outcomes. The hard numbers can help to clearly explain this to the project owner.
How flatness minimizes slips
As a final thought, polished concrete floors may not have the same degree of traction in all areas. An unintended or unexpected change in the contact between the feet and the walking surface can cause a slip. The flatter the floor, the more contact the sole of the shoe will have with the concrete, and this can be critical for preventing slip-and-fall accidents. So when the owner of your next project mentions slip coefficients, think “flat floor” and you will be headed in the right direction.